1. Introduction
Cementitious composites are the most used and widespread materials in the world due to their physical and mechanical properties, which includes questions about durability. Factors such as these stimulate interest in the discovery of new technologies and new compounds as proposals for the improvement of some properties (Mechtcherine et al., 2020; Nguyen; Castel, 2020).
The durability of concrete is an essential issue, as it allows understanding the performance of the material during the entire life of a structure (Kashani et al., 2017). In addition, it can be affected by the action of external aggressive agents, such as chloride ions and (CO2) - carbon dioxide (Nascimento et al., 2021).
According to Azevedo et al., (2020) civil construction, despite having great importance in the economy, is the largest consumer in the world of natural raw materials among industrial sectors. This consumption is estimated at 40% to 75% of the raw material produced on the planet. Oliveira et al., (2020), emphasize that the impact of the industry on the environment involves, from the exploitation of raw material, to its use, which can generate solid waste.
As a way of reducing the negative impact on the environment generated by this disposal and the use of natural raw material in the manufacture of cement composites, granitic crushed stone and marble dust have been materials with great potential to be reinserted as aggregates in the cycle. production in the construction industry.
Despite the large generation of solid waste, civil construction is the industry that can most absorb this waste in the form of aggregates in cementitious composites. Both in Brazil and in other countries, most of the aggregates market is used in concrete and mortar. These residues can be recycled and reused in the construction itself, or they can also be sent to recycling plants and, later, be acquired as aggregates, in different granulometries, for a reduced cost (Brandão et al., 2021).
Despite research demonstrating the feasibility of using these residues, achieving quite significant results for physical and mechanical properties, national standards allow the use of recycled aggregates only in low-strength composites, that is, in non-structural cement-based materials (Mohajerani et al., 2020).
Generally, concrete residues are used in cement composites as a material, partially or totally replacing natural aggregates. After being discarded, the material goes through the beneficiation process, consisting of reducing the size of the material in granulometries similar to those of natural aggregates, which are used as substitute materials for the production of cement composites (Klepa et al., 2019).
The replacement percentage used in research is quite heterogeneous, ranging from 10% to 100%. The water/cement ratio used by the researchers varies according to the percentage of replacement adopted. The highest ratio (w/c) observed was 1.2 and the lowest was 0.35 (Andrade et al., 2018).
According to Cipriano et al., (2021) and Silva et al., (2021) the increase in the ratio (w/c) is due to the need to maintain the workability of the material, and this fact may be attributed to the greater absorption of water from the recycled aggregates, which implies the migration of water to the aggregates, reducing the amount of water that contributes to the workability of the concrete. One way to give concrete with recycled aggregate greater workability, keeping the ratio (w/c) constant and equal to that of conventional concrete, is through the use of superplasticizing additives.
Varadharajan, Jaiswal and Verma (2020) analyzed the durability and strength of concrete with 5%, 10%, 15% of marble powder in place of fine aggregate, in addition to a water/cement (w/c) ratio of 0.43. The study revealed an improvement in compressive strength of approximately 35 MPa at 28 days, that is, 15% greater when compared to reference composites.
Zhen and Liu (2021) analyzed the behavior of cementitious composites using percentages of 10%, 20% and 30% of granitic crushed stone in partial replacement of the fine aggregate. The researchers observed that mixtures containing 30% crushed stone powder had an improvement in axial compressive strength at 28 days of 20%, resulting in 50 MPa when compared to the reference composites.
Research carried out by Thapa and Waldmann (2021) showed the effectiveness of cement composites using 10%, 20% and 30% of granitic crushed stone. The authors noticed that the use of 30% of the recycled material made it possible to improve the axial compressive strength in the concrete mixtures, being observed at 90 days, 58.1 MPa.
Aliabdo, Elmoaty and Auda (2014) performed mechanical tests on concrete using 0%, 5%, 7.5%, 10% and 15% of marble powder in cement-based composites at different curing times. For a water/cement (w/c) ratio of 0.50, an increase in flexural tensile strength in the mixture containing marble powder of approximately 10% compared to the reference mixture was reported. For all curing times, maximum flexural tensile strength was reached at 7.5% and minimum at 15% replacement.The data obtained in this study did not corroborate those obtained by Rodrigues, Brito and Sardinha (2015), where they report a decrease in the results of axial compressive strength due to the increase in the percentage of marble dust residues. The authors reported a maximum loss of 31% at 28 days of healing.
Aiming at mitigating the environmental impacts resulting from the generation of waste, there is currently a great search for alternative materials that can be used as partial or total substitutes for natural aggregates. According to Meena et al., (2021), the amount of solid waste generated by the construction industries will increase from 12.7 billion tons to 27 billion tons by 2050. With this, it confirms that the generation and disorderly disposal of waste solids in civil construction need to be mitigated, reintroducing these wastes into the production cycle of the generating industry itself (Meena et al., 2021; Paiva et al., 2021).
In view of this problem, the objective of this work is to study the feasibility of using marble powder and granitic crushed stone, replacing the natural fine aggregate in the production of cement composites, aiming at the search and definition of an alternative for a correct disposition. of these residues and the reduction of the use of the natural fine aggregate, aiming at mitigating the environmental impacts caused by the extraction process.
2. Experimental procedure
This topic aims to present the experimental schedule performed and the respective methodologies carried out to achieve the objectives of this work, being divided into 8 subtopics, considering from the initial characterization tests of the fine aggregates to the final tests of workability and resistance to axial compression. The tests were carried out in the Civil Engineering laboratories of the Faculty of Integration of the Sertao - FIS, located in the municipality of Serra Talhada - PE. The marble dust was collected in a company (Pedra Bonita Mármores e Granitos) and the others (granitic gravel dust and natural fine aggregate) were acquired through a local enterprise, and later, they were transported to the Engineering Laboratory Complex. Institution's Civil Service.
2.1 Materials
The cement used was type CP-II-F-32 RS (Sulphate Resistant). This type of binder was chosen due to its rapid strength gain and absence of additives. The content of mineral additions contained in other types of cement could contribute to the refining and filling of the pores inside the concrete, which makes it difficult for aggressive agents to enter and improves durability.
Marble powder and granitic gravel powder were used, where the fractions of the materials can be seen in (Figure 1 (a) and (b)). Natural fine aggregate (sand), of quartz origin, used in the region was used (Figure 1 (c)). The sand was acquired by a company taking into account its physical characteristics. The material was in a wet state and therefore it was necessary to correct its water content by natural drying.
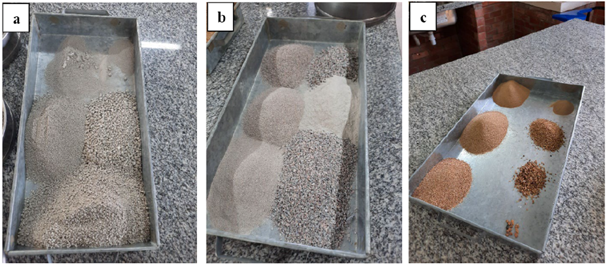
Figure 1 Fractions of marble dust particles (a) granitic crushed stone dust (b) natural fine aggregate (c).
The additive used was Techniflow 520, by MC Baushemie. This plasticizing additive was used in the matrix dosage of concrete with a mass density of 1.08 kg/L.
The coarse natural aggregates used had a maximum diameter of 19 mm and a fineness modulus of 6.48 mm. The granulometric curve of the material was not exposed in this research, but the type of aggregate used was classified as gravel 1.
2.2 Methods
2.2.1 Correction of fine aggregate moisture (sand)
To ensure the moisture content, 600 g of material were placed in an oven for about 24 hours at a temperature of 100°C ± 2°C and, after this procedure, 300 g were used for the granulometric characterization test taking into account the granulometry of the fine aggregate according to the NBR NM 248 standard (ABNT, 2003), using the set of sieves in a normal series and the sieve shaker at a frequency of 8 hertz, for 2 minutes. The sieves used were #6.3mm, #4.8mm, #2.4mm, #1.2mm, #0.60mm, #0.30mm and #0.15mm. In view of the mass retained in each sieve, the Maximum Characteristic Dimension - (DMC) was obtained, which corresponds to the nominal opening, in mm (millimeters), of the sieve as to the normal or intermediate series in which the aggregate has an accumulated retained percentage equal to or less than 5% by mass - of the fine natural aggregates. In addition, the fineness modulus, which according to NBR NM 248 (ABNT, 2003) is the “sum of the retained percentages accumulated in the mass of an aggregate, in the normal series sieves, divided by 100” - of the fine aggregates were obtained with the use of (Equation 1).
where:
2.2.2 Characterization of the natural fine aggregate
For crystallographic analysis, the fine aggregate was dried to mass consistency in an oven at a temperature of 105 ºC and in the appropriate minimum granulometry passing through #200/0.075 mm. The X-ray diffraction technique used for the characterization of the aggregates was performed using a D8 Advance diffuser, Bruker, which contains a Kα tube of copper radiation with a wavelength (λ) of 1,541 Å, a current of 10 mA and 30 kV voltage. The tests were performed with the scanning range (STEP) (2θ) ranging from 10º to 60º, time of 1 second and increment of 1º (degree), speed (Scan-Speed) angular step of 0.02º/second and divergent slit. of 1st degree. The phases present in the samples were later identified with the computer program X'Pert HighScore, through the PDF system (Powder Diffraction).
2.2.3 Specific mass
Due to the lack of the type of flask required to perform the test according to NBR NM 52 (ABNT, 2009), as an alternative means to analyze the specific masses of fine aggregates, the Chapman flask was used, according to NBR 9776 (ABNT, 1987), with the specific mass: “the ratio between the mass of the oven-dried aggregate (100 °C to 110 °C) until mass constancy and the equal volume of the solid, including impermeable pores”. The materials were submitted to the test after 24 hours in the oven at 110 ºC. After reading the results, the formula (Equation 2) that the standard governs was applied to obtain the specific masses.
where:
y = density of the fine aggregate in g/cm3;
L = bottle reading (volume occupied by the water-fine aggregate set.
2.2.4 Unit mass in loose state
The unit mass tests in the loose state of the fine aggregates were carried out according to the parameters established by NBR 7251 (ABNT, 1982). According to NBR 7251 (ABNT, 1982): “the unit mass of loose aggregate is the average of the individual results obtained in at least three determinations, dividing the aggregate mass by the volume of the container used”. Therefore, the test was performed 3 times for each type of fine aggregate. The test consisted of weighing the dry container first, then filling it up to its top with fine aggregate and smoothing the surface with a rod and weighing it, then the necessary calculations were performed using (Equation 3).
where:
2.2.5 Dosage of mixtures of cementitious composites (concrete)
Taking into account that the municipality of Serra Talhada - PE falls into the environmental aggressiveness class (CAA) II of NBR 6118 (ABNT, 2014), the strength established for the concrete traces of the present work was 25MPA at 28 days of age. (curing), with a water/cement factor of 0.55. In addition, for the execution of the different types of mixtures, a mass volume ratio (TMV) of 1 : 2 : 3 ratio (mix/weight), M% = 55% (mortar content) and A% = 10.5% was established. (ratio of water-dry material. For the preparation of the different types of concrete mix, National cement CP II-F-32 RS, crushed stone 1 and the plasticizer additive MC-TechniFlow 520 from MC-Bauchemie (also used by local concrete plant) in 0.65% of the cement mass.
After the granulometry, specific mass and unit mass tests were carried out, the data obtained were used to establish the defined amount of each type of material to be incorporated into the concrete, to make different types of mix. Obtaining, for example, the amount of materials for the production of 1m³ of concrete from the reference trace, being: 352.36 kg of cement/binder; 740.66 kg of fine aggregate; 1133.89 kg of coarse aggregate; and 193.79 liters of water (w/c = 0.55). The same process was carried out with the other traces using the values obtained for the unit mass in the loose state and the specific mass.
To carry out the research, 3 different types of concrete mixtures were performed, as shown in (Table 1), where: mixture 1, being the conventional mix using 100% natural sand as fine aggregate; mixture 2, with the mix replacing 50% of the sand volume with marble powder (10%) and granitic crushed stone powder (40%); and mixture 3, being the line with the total replacement (100%) of the sand by solid industrial residues, marble dust (15%) and granitic gravel dust (85%).
The percentages of marble dust and granitic gravel dust used in the research were defined in order to understand the mechanical behavior of a cementitious compound (concrete) when using 100% industrial recycled aggregates. The main focus of the study was not to analyze the optimal percentage to be used in composites with different cementitious matrices, but the properties of these materials that are not defined by national regulations.
Table 1 Mixtures and amounts of specimens analyzed at different curing times.
MIXTURES | Total specimens that were produced to be ruptured by curing time | |||
---|---|---|---|---|
7 days | 14 days | 21 days | 28 days | |
Mixture 1: reference trace, using completely (100%) natural sand as fine aggregate. | 10 SP | 10 SP | 10 SP | 10 SP |
Mixture 2: partially replacing (50%) the natural sand with granitic crushed stone powder (40%) and marble powder (10%). | 10 SP | 10 SP | 10 SP | 10 SP |
Mixture 3: completely replacing (100%) the natural sand with granitic crushed stone powder (85%) and marble powder (15%). | 10 SP | 10 SP | 10 SP | 10 SP |
Total of 120 specimens |
2.2.6 Procedure for execution of concrete specimens
The production of specimens was developed according to the procedures and parameters established by NBR 5738 (ABNT, 2015). The cylindrical molds used had dimensions of (10 cm x 20 cm) of diameter and height respectively. All the (SP's) produced were used to carry out the analyzes through complementary tests which, in turn, were of paramount importance to understand the physical-mechanical behavior of the material studied. Before starting the separation of the percussive materials for the production of different types of concrete, it was necessary to use a type of liquid release agent in all the forms, where it was left to rest for 15 minutes, to facilitate the removal of the hydrated material. After that, it was necessary to carry out the moisture correction of the fine aggregate (sand), as it directly influences the quality and fluidity of the material under study. This correction implies a reduction in the amount of water used in the production process of the specimens. For this purpose, the matrix materials such as: cement, fine aggregate (sand), coarse aggregate (gravel) and solvent (water), were duly weighed and directed to the mixer according to the corresponding order: the coarse aggregate was taken to the mixer and, after that, approximately 2/3 of the water was used, where the mixing process took about 1 minute. Then, the binder (cement), the fine aggregate (sand) and 1/3 of the remaining water were added. All materials underwent a homogenization process for approximately 5 minutes and, after this process, the consistency test (Slump test) was performed, also known as truncated cone slump according to the procedures established by NBR NM 67 (ABNT, 1998).
After these procedures, the specimens were molded according to the parameters established by NBR 5738 (ABNT, 2015). Firstly, the concretes were introduced in two layers in the molds, each one being densified from the application of 15 blows evenly distributed with a metal rod, without affecting the base. In addition, the external face of the molds was lightly tapped in order to minimize the voids caused by densification. Finally, the last layer was molded with a certain amount of material, in order to exceed the volume of the mold, to facilitate flattening with a metal ruler, without adding material after consolidation. After completing the molding of the concrete, the specimens were taken to a room with an ambient temperature of 25 ºC ± 2 ºC, where they remained for 24 hours for the hydration process to be successfully completed and, after this period, were demolded, identified and subjected to wet curing in a container with the presence of water in a static state with relative humidity above 95% until the time of the tests.
2.2.7 Consistency test (slump test)
The consistency test (slump test) was performed for each trait, characterized as slump of the trunk of a cone according to the procedures established by NBR NM 67 (ABNT, 1998). The purpose of this test was to evaluate the workability of the concrete, with regard to the mobility of the binder against the cohesion of the constituent materials in its matrix. The slump test is composed of a metal plate with dimensions (50 cm x 50 cm) and thickness of 3 mm, a truncated cone with a maximum height of 300 mm, a metal rod with dimensions of 600 mm and a diameter equivalent to 16 mm
To carry out the procedures, first the plate and the trunk of the cone were moistened and placed in a flat region free from vibrations. After that, a sample of the concrete to be analyzed was collected and directed to the trunk of the cone in three layers. The material was compacted with the rod, exerting 25 blows evenly distributed over each layer. This procedure was repeated two more times until the top of the mold.
At the end of the procedure, it was necessary to even out the surface using the compaction rod, and to clean the base. After that, the mold was carefully removed vertically, where the standard informs that this time varies between 5 to 10 seconds. After removal, it is necessary to measure the slump of the material given by the difference in height between the top of the mold (inverted) and the axis of the demolded material.
2.2.8 Axial compressive strength test
The axial compressive strength test was performed according to the established parameters prescribed by NBR 7239 (ABNT, 2018) which comprises the determination of the mechanical behavior of the material. After molding the specimens and after 7, 14, 21 and 28 days of wet curing, the materials were submitted to analysis. All specimens were rectified and taken to a SOLOTEST model DL 200 hydraulic press with load application speed of 0.50 ± 0.15 MPa/second, maximum load of 1000 kN, which is related to 30% applied at end of charge. The equipment used was a hydraulic press with a capacity of 200 tons, which provides the results of the axial compressive strength (Fck) in MegaPascals (MPa) and their respective rupture curves.
3. Results
3.1 Particle size analysis of aggregates
From the granulometric analysis of the aggregates, it was verified that the fine natural aggregate (sand) presented a fineness modulus of 2.15 and a maximum diameter of 4.8 mm, being classified as an aggregate of medium granulometry. The recycled aggregates called crushed stone and marble powder showed, respectively, a fineness modulus of 2.73 and 3.88, both higher when compared to the fine natural aggregate. The maximum diameter of the particles of the recycled aggregate was 4.8 mm, which can be classified as a medium granulometry material. Each sieve used presented a retained fraction of aggregates, where they were weighed and served to project the granulometric curve. In the #6.3 mm sieve, no material was retained; #4.8 mm, 0.29 g; #2.4 mm, 3.03 g; #1.2 mm, 10.88 g; #0.60 mm, 32.26 g; #0.30 mm, 71.38 g; #0.15 mm, 97.32 g.
As for marble powder, the quantity of particles retained on each sieve was: #4.8 mm, 0.42 g; #2.4 mm, 22.35 g; #1.2 mm, 70.83 g; #0.60 mm, 95.05 g; #0.30 mm, 99.51 g; #0.15 mm, 99.96 g. Regarding the granitic crushed stone powder, the quantity of particles retained on each sieve was: #4.8 mm, 0.16 g; #2.4 mm, 15.77 g; #1.2 mm, 42.70 g; #0.60 mm, 58.78 g; #0.30 mm, 72.17 g; #0.15mm, 99.96 83.35g. For both, the total amount tested was 300 g. Figure 2 shows the granulometric distribution curves of natural fine aggregate, marble dust and granitic crushed stone. It is possible to observe that the curves of the natural fine aggregate and of the granitic crushed stone behave in a similar way, both being able to be used within the limits established by the Brazilian standard NBR 7211 (ABNT, 2019), as also observed by Barros e Fucale (2016), who used recycled aggregates in the concrete production. However, the curve referring to marble dust does not fit within the limits established by the standard, presenting particles with dimensions of 1.18; 0.6 and 0.3 mm in excess.
The powdery material content test was carried out. Natural sand presented a fine material content of 7%, while marble powder and granitic crushed stone powder presented a rate of 12.5% and 10.3%, respectively, showing an increase of more than 50% compared to the natural aggregate. However, despite the fact that recycled aggregates have a high content of powdery material, this result allows this increase to remain within the limit established by the standard for recycled aggregates of solid waste according to NBR 15116 (ABNT, 2004), not exceeding 20%.
According to Souza (2019), continuous granulometry aggregates, which do not present excess or deficiencies of particles of any dimension, produce the most workable and economical concrete mixtures, however, the other characteristics of the aggregates, such as the dimension maximum characteristic and the fineness modulus. In (Table 2), the results of the other characterization tests of the fine aggregates are presented.
Table 2 Fineness modulus, maximum characteristic dimension, specific mass and unitary mass in loose state of the fine aggregates used in the work.
Feature | natural sand | Granite crushed stone dust | marble dust |
---|---|---|---|
Fineness module: | 2.15 | 2.73 | 3.88 |
Maximum characteristic dimension (DMC): | 4.8 | 4.8 | 4.8 |
Specific mass (g/cm3): | 2.63 | 2.65 | 2.74 |
Unit mass in loose state (g/cm3): | 1.46 | 1.62 | 0.94 |
The aggregate fineness modulus limit values according to NBR 7211 (ABNT, 2009) are: | |||
NOTE 1: The fineness modulus of the optimal zone varies from 2.20 to 2.90. | |||
NOTE 2: The fineness modulus of the lower usable zone ranges from 1.55 to 2.20. | |||
NOTE 3: The fineness modulus of the upper usable zone ranges from 2.90 to 3.50. |
According to the data presented in (Table 2), comparing the values of fineness modulus of the aggregates with the limits established by NBR 7211 (ABNT, 2009), both natural sand and granitic gravel powder present fineness modulus within the usable zones, mainly the granitic stone dust that fits in the optimal zone. However, marble dust does not fall within the usable zone.
The granulometric curves of the recycled aggregates were evaluated separately in order to understand how their particles behave, which helps for a better distribution of the percentages used. Even used together, an individual analysis is necessary as proposed in the research, because the characteristics of these materials are different. A similar feature is the specific area, as both have high levels of fine materials which, in turn, require a higher percentage of water or a higher water/cement ratio (w/c).
According to Souza (2019), the higher the fineness modulus, the larger the dimensions of the aggregate (which was the case with marble powder), in addition, aggregates with similar fineness modulus tend to produce cementitious composites with similar characteristics, but this depends of other factors such as the maximum size of each aggregate and the presence of powdery materials. Also according to the same author, the greater the maximum characteristic dimension, the smaller the surface area to be covered by the cement paste, which can influence the reduction of costs in the manufacture of concrete, but this depends on other factors, such as the presence of powdery materials.
3.2 Analysis of consistency (slump test)
All mixtures were evaluated according to their physical characteristics, which cover the behavior of cementitious materials in terms of workability. In (Figure 3), the mixtures were analyzed separately and the results of the slump of the “trunk cone” were obtained in cm. It can be seen that the mixtures containing 50% of industrial solid waste, have similar behavior to the reference composites. The mixtures containing 100% had a “trunk cone” slump of 4 cm, which indicates that the material has a greater specific surface, which consumes a greater amount of water.

Figure 3 Representation of the workability (obtained through the Slump Test) of the different types of strokes.
Although the natural fine aggregate and crushed stone powder present their granulometric ranges within the limits established by the standard, none of the 3 (three) mixtures presented slumps between 10 cm and 16 cm, which, according to NBR 8953 (ABNT, 2015) would be ideal. for the execution of the structural elements.
Observing (Figure 3), it can be seen that the mixtures containing 50% of industrial solid waste showed a workability around 11.11% lower when compared to the reference mixtures, which demonstrates their feasibility for the development of new cementitious composites for structural purposes. However, the mixtures containing 100% of industrial solid aggregates showed a 55.56% lower slump when compared to the reference mixtures.
The marble powder showed unfavorable characteristics when mixed with water, where its grains were deposited, forming a powdery material. In addition, the material had a viscous characteristic when saturated, which negatively influenced the workability of cementitious composites (concrete).
3.3 Analysis of axial compressive strength
The use of industrial solid waste in the matrix structure of cementitious materials (concrete) provides a better physical-mechanical behavior which, in turn, fills the voids/interstices due to the specific surface area of these materials, according to the results obtained through the granulometric classification. All analyzes were performed at 7, 14, 21 and 28 days and the results were expressed in the graph shown in (Figure 4).
The mixtures containing 50% of industrial solid waste in their composition provided the material with greater mechanical efficiency when compared to the reference (SP’s), which were greater than 20 MPa at 7 days. However, the results of the reference mixtures and with 100% recycled aggregates have similar behavior at the 28 days of analysis, where the values obtained were 27.94 MPa and 27.47 MPa, respectively. It is possible to notice that all mixtures have a significant sample correlation, that is, the (R²) vary around 0.900 and 0.920.
Considering the analyzes carried out, it was observed that the mixtures containing 50% of industrial solid waste provided an increase in the compressive strength at 28 days of approximately 4% when compared to mixtures of (REF), which is considered an adequate value in the face of the presentation of the physical characteristics of the materials under study. These composites gave more significant values, however, at 7 days, they resulted in a slightly higher behavior when compared to the reference mixtures.
As for the mixtures containing 100% of industrial solid waste, it was noticed that at 28 days of analysis, it obtained axial compressive strength values of 27.47 MPa, that is, 2% lower when compared to the reference mixtures. This behavior will be due to the percentage of fine materials present in the material and the water/cement ratio (w/c). The higher the content of powdery materials, the greater the absorption of water, making it difficult for all particles to become wet. This process implies the absence of better cohesion and, above all, the formation of voids inside the cement matrix, leading to the loss of mechanical properties.
The growth of the compressive strength occurs linearly, as the increase in the content of particles of residual materials dispersed in the cement matrix of the mixtures with 100% does not coincide with the good mechanical behavior of the material. Furthermore, it is known that the increase in the void ratio can cause pressures inside the hydrated compound, forming microcracks that, when a force is applied, contract in the regions close to the transition zone of the aggregate/binder.
In order to better represent the data obtained, and from the values of the axial compressive strength at 7, 14, 21 and 28 days, a statistical analysis was performed using histogram and ANOVA (single factor method). It can be seen, therefore, that the analyzed mixtures have statistically different results according to the representative P-value less than 5%, the F > Fcritical and by the dispersion of the data circled in red (Figure 5). When there is this behavior, it is verified that the data are significant at a confidence level of 95%, as can be seen in (Table 3).
Table 3 Analysis of variance of the axial compressive strength of cementitious composites at 7, 14, 21 and 28 days of curing.
Analysis time | source of variation | SQ | gl | MQ | F | p-value | F-critical |
---|---|---|---|---|---|---|---|
7 days | between groups | 82.079557 | 5 | 16.41591 | 2.6582498 | 3.00E-02 | 2.353809 |
14 days | 340.73302 | 68.1466 | 7.1096072 | 2.26E-05 | 2.5891899 | ||
21 days | 159.02956 | 31.80591 | 5.770562 | 1.77E-04 | 2.8481088 | ||
28 days | 380.53679 | 76.10736 | 39.387462 | 1.54E-18 | 3.1329197 |
SQ: Sum of squares;
gl: Degree of freedom;
MQ: Mean of squares;
F: Test F, calculated value;
P: Significance level associated with the calculated value F.
Some analyzes were carried out corresponding to the data obtained in the result of simple compressive strength, which, in turn, made it possible to understand the behavior of each mixture. The evaluated samples went through a quantitative statistical process (Table 4), where it was noticed that the reference composites had an average standard deviation of 1.699 and a coefficient of variation of 6.081 compared to the other mixtures. Mixtures with 50% of industrial waste had a standard deviation of 0.804 and a coefficient of variation of 2.765, that is, 11% and 15% lower compared to the reference composites, respectively.
Table 4 Statistical analysis of axial compressive strength data at 28 days of curing.
Data | REF | 50% industrial waste | 100% industrial waste |
---|---|---|---|
No. of samples | 30 | 30 | 30 |
Average | 27.94 | 29.09 | 27.47 |
Standard deviation (mean) | 0.906 | 0.804 | 0.768 |
Standard deviation (sample) | 1,156 | 1.073 | 1.019 |
Standard deviation (population) | 1,156 | 1,027 | 0.975 |
Coefficient of variation (%) | 3,243 | 2,765 | 2,794 |
standard error | 0.143 | 0.127 | 0.121 |
95% confidence interval | 28.3 | 29.41 | 27.77 |
27.58 | 28.77 | 27.17 | |
0.358 | 0.318 | 0.302 |
3.5 Microstructural analysis
To understand the microstructural behavior of cementitious composites, using different percentages of industrial waste, it was necessary to perform diffractometric analyses. All samples were analyzed after 28 days using the X-ray diffraction test, in order to identify the crystalline phases present in the material in the hydration process, as well as to understand the portlandite reactions in the hydration states. XRD patterns can be seen in (Figure 6 (a) and (b)).
Regarding the behavior of the percussive materials, it can be seen that the fine aggregate and Portland cement have a crystalline structure with well-defined intensity peaks, as can be seen in ((Figure 6) (a)). The detection of the fine aggregate peaks is indicated in the 2θ positions: 21.2º, 26.8º, 36.7º, 40.4º, 50.3, 60.0 and 68.6º, where they refer to the crystalline phases of quartz.
As for the Portland cement aliquot, one can see the formation of diffraction spectra peaks, where some phases were identified. Positions 2θ = 29.5º and 32.2º are formed by the decomposition of alite (3CaO.SiO2) and at position 2θ = 62.3º there is the presence of tricalcium silicate - (C3S). Furthermore, at positions 2θ = 27.6º and 32.8º, the crystalline phase composed of belite (2CaO.SiO2) is observed and in the regions 2θ = 30.2º and 31.1º, the formation of dicalcium silicate can be seen - (C2S).
The formation of tricalcium aluminate - (C3A) defined by the chemical correlation (3CaO.Al2O3), can be seen at positions 2θ = 23.2º and 33.4º. Note that tetracalcium ferric aluminate defined by the chemical correlation (4CaO.Al2O3.Fe2O3) abbreviated as (C4AF), can be seen at position 2θ = 14.7º and gypsum, in turn, can be seen at position 2θ = 11.8º.
In this context, it is noticeable that the content of (C3S), (C2S), (C3A), (C4AF) and gypsum in Portland cement aliquots is well defined. All the crystalline phases identified in the material, as well as the chemical composition present in the hydration phase of the binder, are correlated with the studies carried out by Geng et al., (2018).
All results, in turn, directly influence the behavior of the hydrated cementitious compound. As they are very thin materials with a high specific area, some particles are often agglomerated, which directly influence the physical-mechanical behavior of the material under study (concrete).
4. Discussions
Current research aims to evaluate the use of marble powder and granitic crushed stone as an alternative material that aims to reduce environmental impacts. In terms of the mechanical performance of cementitious composites modified with marble powder, Arshad et al., (2014) concluded that the replacement of 15% of fine aggregate by marble powder residues in the presence of plasticizing additives, evidenced a maximum compressive strength. similar to the reference mixture, after 28 days of curing.
Shukla, Gupta and Gupta (2020) when producing cementitious composites containing marble powder in the proportion of 100%, it was observed values of average axial compressive strength at 28 days of approximately 40 MPa, which was 6.5% higher when compared to the reference mixtures. Likewise, Barros and Fucale (2016) verified the possibility of using the total replacement of natural aggregate by recycled and concluded that the concrete was able to withstand 22% higher compressive forces when compared to the reference mixture.
Studies carried out by Aliabdo et al., (2014) showed that the use of a water/cement ratio (w/c) of 0.40 enabled a significant increase in the axial compressive strength of cementitious composites containing industrial waste in their matrix. In addition, they observed that the mechanical compaction of concrete affects the filling of voids.
Ali and Hashmi (2014) evaluated the mechanical behavior of cementitious composites using different percentages of marble dust and stone dust individually. The authors found that the use of 20% stone powder improves the mechanical properties of cement-based materials by approximately 17% at 7 days and 16% at 28 days of analysis.
Studies by Hebhoub et al. (2011) reported an increase in axial compressive strength using 75% recycled aggregates. In addition, the authors performed a comparative behavioral analysis, where they realized that the use of 100% recycled aggregates affects the loss of axial compressive strength determined by the filling of micropores in the cement matrix, improving the properties in the transition zone. All analyzes corroborated the results obtained in this study.
Rodrigues, Brito and Sardinha (2015), evaluated the behavior of cement composites containing industrial solid materials, where they realized that the use of plasticizers improves the axial compression strength and workability. In addition, it is necessary to use industrial waste properly, because when used incorrectly, it can lead to the decomposition of dicalcium silicate (C2S) and tricalcium silicate (C3S), constituents that are responsible for the increase in compressive strength. of cement-based composites.
5. Conclusions
In this article, the behavior of cement composites, more specifically concrete, was analyzed in terms of the use of industrial aggregates composed of marble dust and granitic crushed stone as a partial replacement for natural fine aggregate, as an alternative to minimize environmental impacts. The main conclusions are described below:
Cementitious composites (concrete) containing 50% of industrial waste resulted in an increase in axial compressive strength of 29.09 MPa, that is, 4% higher when compared to the reference mixtures;
The use of plasticizers improves the behavior of cementitious materials, especially with low water/cement ratios. In addition, the mixtures containing 100% recycled aggregates had a lower truncated cone slump, even though they contained plasticizer in their composition;
The results of the reference mixtures and with 100% recycled aggregates have similar behavior when analyzed at 28 days, where the values obtained were 27.94 MPa and 27.47 MPa, respectively.
The use of components with higher contents of powdery materials can affect the workability due to the high specific surface. On the other hand, the proper use of percentages can promote the filling of voids inside the cement matrix, as well as contributing to the cohesion process and improvement of the mechanical properties of cement-based materials;
It was possible to notice that all mixtures have a significant sample correlation, that is, they vary between 0.900 and 0.920.