1. INTRODUCTION
The problem of corrosion consumes directly or indirectly about 5% of GDP of an industrialized nation and involves major disasters when not properly treated (Cunha et al., 2013). The main corrosion problems are associated with the lack of suitable coverings of concrete. Since concrete gives the steel a double protection: first a physical protection, separating the steel direct contact with the external environment, and second, a chemical protection conferred by the high pH of the concrete, which promotes the formation of a passivating film that covers the steel (Figueiredo and Meira, 2012). Corrosion may be defined as the deterioration of a metal or alloy, from its surface, by the environment into which it is inserted. The process involves oxidation and reduction reactions (redox) that convert the metal or the metal component into oxide, hydroxide or salt (Silva et al., 2015).
There are several factors influencing the corrosion parameters of concrete immersed metal: the diffusion coefficient, the water/cement ratio, the thickness of the coating, the presence and amount of additions, the humidity, the pH of the concrete and the temperature of exposure (Andrade, 2001; Gu and Beaudoin, 1998). In addition, the type of protection system applied to the metallic material are relevant, because the concrete or steel bars can receive surface protection (Figueiredo and Meira, 2012).
When the strategy is to protect the steel bar, the protection technique can be applied in the construction of new structures or in limited repair areas when there is a concern for the reinforcement bars corrosion (Araujo, Panossian and Lourenco, 2013).
Intending to offer safety and durability for structures, the chemical and the civil construction industry sell products for corrosion protection in different forms (Vieira et al., 2010). In the case of repairs, some authors describe the main protection methods used in Brazil (Figueiredo and Meira, 2012), as shown in Figure 1.

Source: Adapted from Figueiredo and Meira (2012)
Figure 1 Protection methods most used in steel bars for structural repairs
It is noteworthy that in the area of diagnosis of pathological manifestations is inherent in reconciling research, testing, interpretation of results and mastery of the latest developments regarding the prognosis of structure deterioration mechanisms and its influential (Medeiros et al. 2012). Thus, this study aims to assess how the type of steel, the pH of the environment and the presence of surface protection used in the steel bar can alter the electrochemical characteristics of the corrosion mechanism. This type of study is essential to understanding the influencing factors of corrosion and how effective repair products are. As well as forecast the life of reinforced concrete structures.
2. LINEAR POLARIZATION RESISTANCE (LPR)
There are several types of measure for corrosion controlling, but the current density and corrosion potential are most commonly used in the diagnosis of reinforced concrete (Tavares, 2006). Table 1 and Table 2 show the corrosion level in terms of current density values and corrosion potential.
Among various techniques used to study corrosion and used for the determination of the current density, corrosion potential and corrosion rate, the linear polarization resistance technique (LPR) is the most applied (Alves et al., 2012). Its wide application is due to the speed and ease with which can determined the variables measured. The purpose of this technique is to measure the resistance that a material, exposed to particular environment, offers to oxidation during the application of an external potential.
To perform the technique is common to use a potentiostat for applying different potentials (voltages) in the reference electrode (Flores et al., 2013). Thus, if the potential is different than the corrosion potential, the equipment registers the applied current (Fofano, 1999). Thus, is is obtained the variation of the current as a function of the applied potential (E vs I) as shown in Figure 2. Another control parameter obtained is the polarization resistance, which can be considered as the ratio between the potential difference and the applied current (Liu, 1993).
From these data it can be made quantitative measurements of various parameters of electrochemical corrosion, based on the equations presented by the ASTM G 59 (1997) and by Wolynec (2003). The current density, for example, can be calculated as shown in Equation 1 and Equation 2.
Which: icorr is the corrosion current density (A/cm²), βa is the Tafel anodic slope and βc is the Tafel cathodic slope (V/decade), e Rp is the polarization resistance (ohm/cm²).
The corrosion rate - CR (mm/year), on the other hand, can be determined from Equation 3, where Eq is the electrochemical equivalent of the corroded species (g), and ρ is the density of the corroded material (g/cm³).
The corrosion rate CR (µm/ano) can also be considered equivalent to 11.6 times icorr (µA/cm²) for a steel bar (RILEM, 2000).
3. MATERIALS AND METHODS
In the ollowing, the materials used in this research and the test methods adopted will be presented. The steel types were chosen from the NBR 7480 (1996) which deals with the steel destined for reinforcement of concrete structures and the NBR 7482 (2008) which deals with steels for prestressed concrete structures. Another criteria for the selection of steel types was the proximity of the diameters between classes, to reduce variability in the results. The selected types are displayed in Table 3.
For each steel from Table 3, there were four specimens of 15 cm in length, wiped with a hydrochloric acid solution according to ASTM G 1 (2011).
Tests were performed with bars immersed in solutions of different pH, altered by the addition of sodium hydroxide and controlled by a benchtop pHmeter at 25° C. The solutions had the values of 7, 9 and 11 initial alkalinity, and there were no pH adjustment after start of the tests. Measurements were taken at 7 and 30 days. It should be noted that the steel bars were in containers, sealed, and immersed in an aggressive solution, thus, there was no entrainment material contamination or addition of substances and gases.
Before the tests, part of the bars were subjected to a surface protection method. The protection system used was a rust converter applied in two coats with a 60 minute interval, with subsequent application by an acrylic painting. The protection product used had density of 1.03g/cm³, solids content of 10 to 15%, pH of 2.6 and chemical composition of organic extract of Acacia Mearnsi (3-15%), citric acid (2-10 %), acrylic co-polymer (5-20%) and 2-butoxy ethanol additive (3-15%).
The linear polarization resistance tests (LPR) were performed as prescribed by the ASTM G 59 (1997) with a SP-200 BioLogic potentiostat - Figure 3 - which used an electrode of copper/copper sulphate (Cu/CuSO4) by applying voltages ranging from -2V to + 2V.
For each test condition (pH and protection) four measurements were performed, and the electrode was placed as close as possible to the steel bar during the tests. After the test, the polarization curves were analyzed and thereby it was possible to obtain the corrosion potential (Ew), corrosion current density (Icorr), the corrosion rate (CR) and polarization resistance (Rp) for each of the steel bars - with and without protection - at different pHs.
To validate the results, the Tukey statistical test for multiple comparison of results was applied. Thus demonstrating the differences between the results obtained with a confidence level of 95%. We emphasize that the statistical analysis were performed only for the results of the current density and corrosion rate.
4. RESULTS AND DISCUSSION
The table below shows the results of corrosion measurements of steel bars under different pH levels with and without surface protection in the bar. Figure 4 and 5 show the results of potential corrosion to the steel bars after 7 and 30 days, respectively. Data were ranked based on the probability of corrosion as is shown in Table 2.
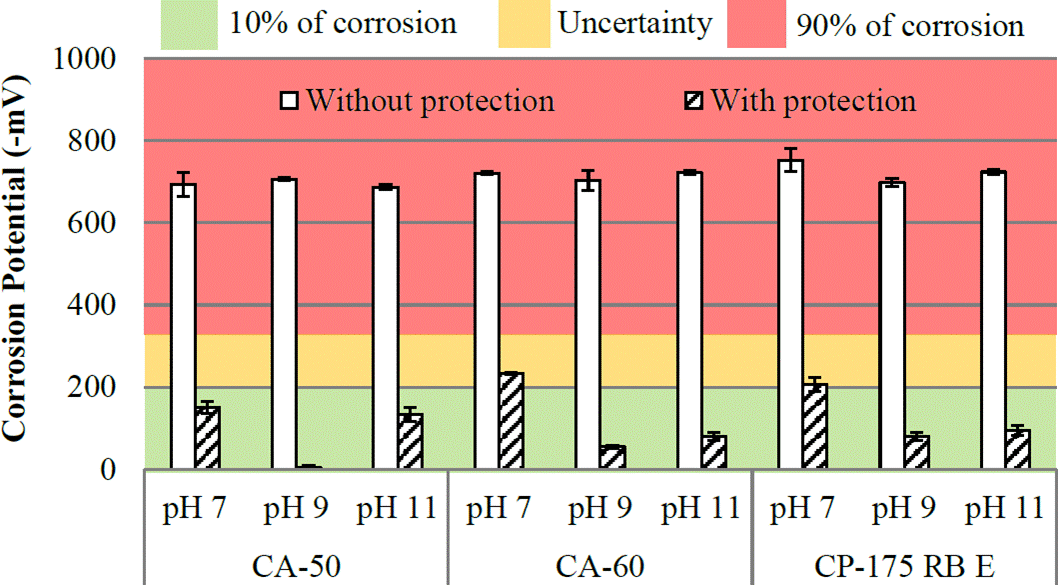
Figure 4 Potential corrosion of the bars at 7 days (Reference electrode: copper/copper sulphate Cu/CuSO4).
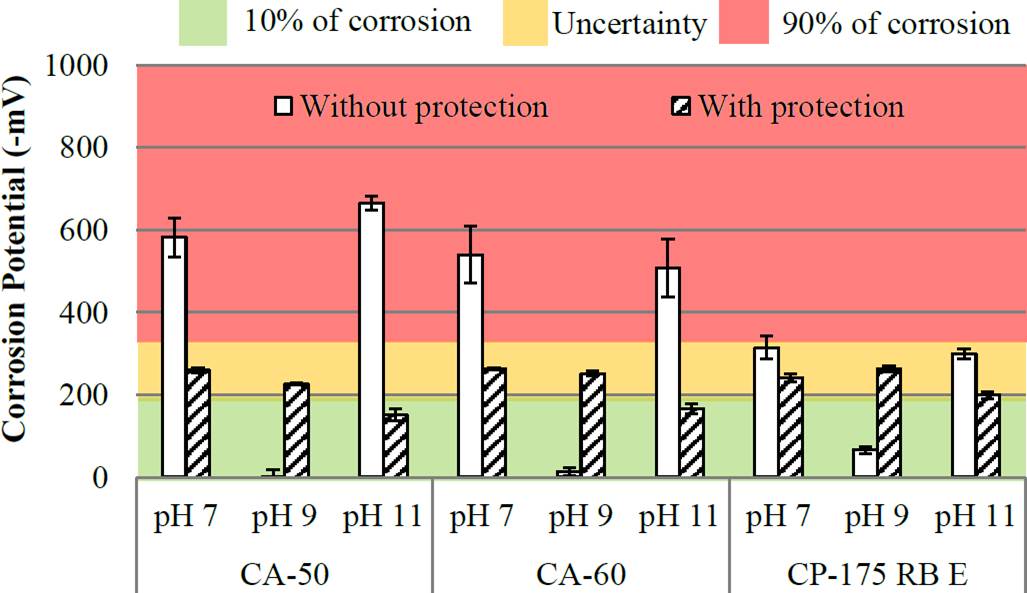
Figure 5 Potential corrosion of the bars at 30 days (Reference electrode: copper/copper sulphate-Cu/CuSO4).
It is observed in Figure 4 that, at 7 days, all unprotected steel bars have probability of 90% of corrosion, averaging -711mV. While 78% of the bars are protected with a low probability of corrosion (10% occurrence), with data ranging from -3mV and -205mV. The results in Figure 4 show the rust converter action in corrosion potential application in early ages.
In 30 days (Figure 5), the surface without protection had increased corrosion potential, presenting results from -6mV and -582mV. Even after 30 days, the bars with protection have undergone an increase in corrosion potential, with a reduction to 33% of the samples in the low likelihood of corrosion area (with -224mV reading average). Also, we evaluated the results of the current density and corrosion rate depending on the level of corrosion shown as in Figures 6 and 7.

Figure 6 Current density and corrosion rate of the bars at 7 days (Reference electrode: copper/copper sulphate- Cu/CuSO4).
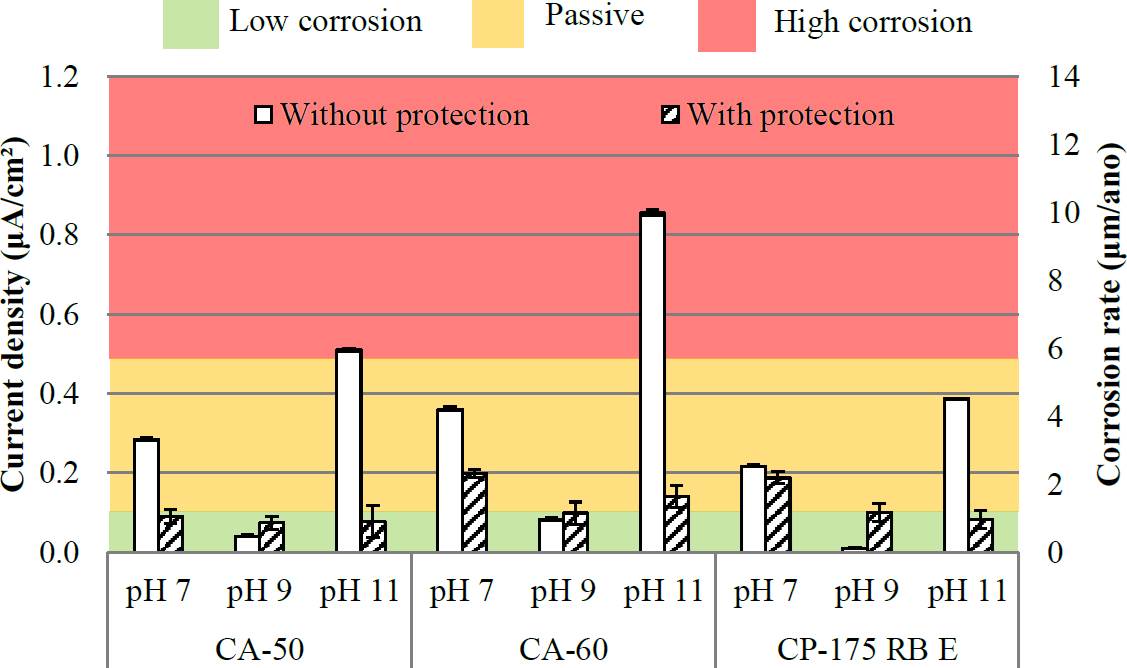
Figure 7 Current density and corrosion rate of the bars at 30 days (Reference electrode: copper/copper sulphate- Cu/CuSO4).
With the data presented in Figure 6, it can be seen that for analysis at 7 days occurring high corrosion rate value in bars without protection, or a state of general corrosion (with all the results classified as moderate corrosion to high, and current densities greater than 0.77 uA / cm²). It should be noted in Figure 6 that in all cases, the corrosion rate was larger in the bars without protection, if compared with steel bars that have reached their protected surface current densities lower than 0.23 uA / cm², with 78% of the results in the passivity zone. Note that the CA-60 steel with protection showed the highest corrosion rate values when compared with the other results of steel protected surface.
As for the analysis carried out after 30 days, (Figure 7) has a reduction of corrosion rate in all cases. Being the most part included in the first two groups of corrosion status classification: passive and low to moderate state of corrosion, with the exception of the CA-50 and CA-60 steel in the environment for pH = 11.
It is known that during the initial periods of exposure to the atmosphere, the corrosion rate of carbon steel is usually high. This is due to the high porosity of the rust initially formed, consisting mainly of iron oxides. After this initial period, the improved protective properties and the corrosion rate decreases (Panonni et al., 1993). Because of this behavior, exponential models are used to represent the corrosion rate over time (Hakkarainen, 1982; Barton, 1980; Pannoni and Marcondes, 1991). Thus, the results obtained are consistent with the results observed by other authors.
Therefore, the decrease in corrosion rate could have been caused by severe initial corrosion in the equipment, which resulted in the formation of a layer of corrosion products on the exposed surface of the armor which, in other words, may have limited contact between steel samples and solutions. Another possibility not covered by others is the variation of oxygen present in the solution, that is, with the iron rust was a decrease in the concentration of oxygen present; ie, the corrosion product itself tended to reduce the speed of progress of corrosion of reinforcement, as it presents as a physical barrier to the electrolyte access.
Note also that the steel bar CA 60, generally had higher values than the others, indicating a greater susceptibility to corrosion, but without statistical significance. It should also be noted that the protection capacity of the steel surface treatment system does not have to be more effective after 30 days of exposure to the corrosion conditions. To allow a better analysis of the influence of solution pH, Figures 8 and 9 were prepared according to the pH of the solutions.
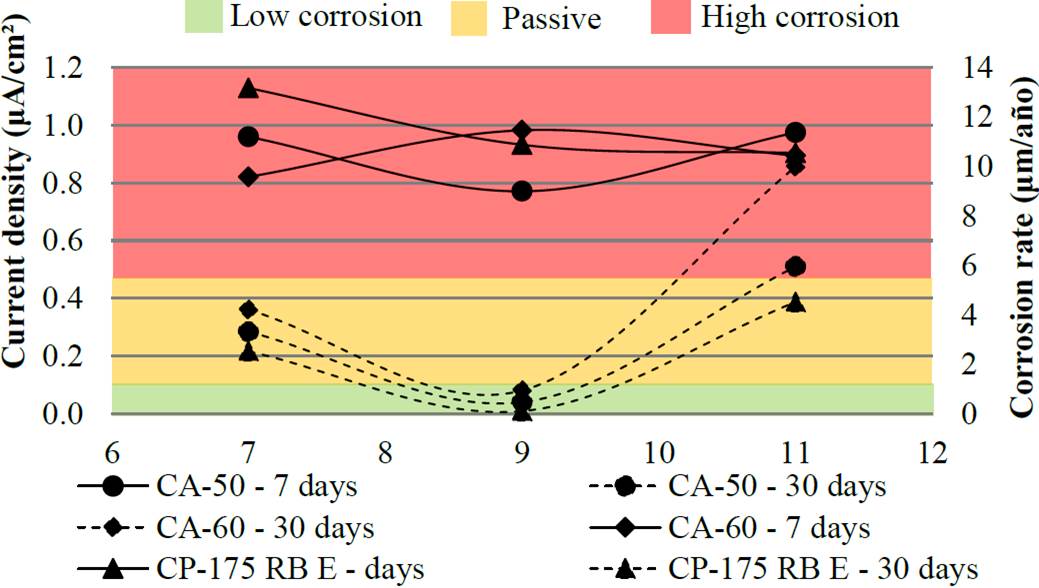
Figure 8 Current density and corrosion rate of the bars without protection (Reference elect rode: copper/copper sulphate- Cu/CuSO4).
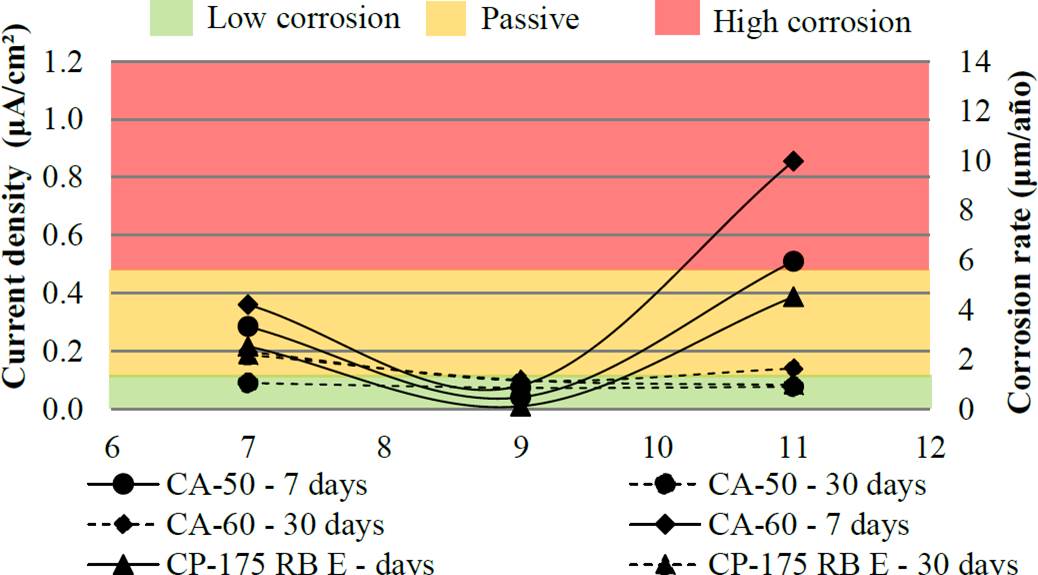
Figure 9 Current density and corrosion rate of the bars with protection (Reference electrode: coppercopper sulphate- Cu/CuSO4).
From the results shown in Figure 8, it could be observed that the pH had little influence on the results of unprotected bars, exposed for a period of 7 days, and the samples achieved a current density value in the range of 0.8 to 1.1 uA / cm², being classified as a corrosion state of moderate to high. During the 30 days, unprotected bars showed mixed results of corrosion rate, especially the reduction of corrosion to those who were in the pH = 9 solution - reaching passivity.
By analyzing the bars with surface protection (Figure 9), it is noted that at 7 days was a variation in current density with increasing rates including protected bars, when pH = 11 with values up to 0.85 uA / cm². At 30 days the pH of the solutions was not influential on the results of the current density with near passivity results. However, it is possible to highlight the pH = 9 inhibited the corrosion process in all protected bars.
As the results of pH, the variation in the type of steel used is CP, CA 50 and CA 60, had little influence on the variability of results. However, it is observed that in both scenarios (30 days without protection and 7 days with protection) CP-175 was the least damaged by steel corrosion effect, followed by steel AC 50 and AC 60. This behavior can be explained by the fact that from 0.15 to 0.40% carbon steels in CA 50 and CA 60, while CP-175 presents content from 0.70 to 1.20% carbon (ARCELORMITTAL, 2016). Thus, by having a lower iron content in its chemical composition, the prestressing steel tends to have a lower rate of iron oxide formation.
Figure 10 shows a correlation between the results of corrosion potential and current density. It is found that there is a correlation between the two quantities corrosion monitoring, with R2 equal to 0.83.

Figure 10 Correlation between measurements taken (Reference electrode: copper-copper sulphate-Cu/CuSO4).
This result is expected since the increase in the corrosion potential induces an increase of the Tafel slope and hence the current density. The existence of a good correlation proves the effectiveness of the techniques applied.
With the objective to prove the difference between the results, was performed statistical analysis, by Tukey test, shown in Figure 11. In the test, the confidence intervals represent the interaction between two samples if there is the intersection between the end of the range top and bottom of the samples with zero vertical axis, it can be said that the differences between them are not significant.
As results show in Figure 11, differences occurred - with higher significance than 95% - of the results obtained after 7 and 30 days and between the bars with and without surface protection. Thus, protection was able to improve the electrochemical properties of the steel at different pHs, thus reducing the corrosion rate and current density.
Still according to Figure 11, it was observed that the type of steel used and the pH of the solutions did not exert statistically significant influence on the results. This behavior is explained by the observed deviation in the values of current density with different behaviors in each of the conditions studied.
However, although not statistically significant when analyzed, deviations in Tukey test caused by type of steel, it is noted that the steel that showed no difference in the results were the CP-175 and CA-50 steel. The pH of the solutions, it is noted that the pH = 9 was which generated a greater difference in the results (when observing the deviation of the pH analysis 9 - pH 11 and pH 9 - pH 7).
This type of analysis is essential to prove that the durability studies increasingly need to evaluate other variables that can influence the tests and environmental interactions in which materials are with steel and concrete.
5. CONCLUSION
In general, it confirmed the influence of variables on the corrosion process of steel bars: time and surface protection system. In this study we observed high corrosion rate values at early ages, with a reduction 30 days after the medium change - caused by the material resulting from the etching process (possible deposition surface on the bar and change of oxygen concentration in the solution). It was observed that bars subjected to surface protection demonstrated ability to maintain the corrosion rate even with low values ages.
The analysis of the classes of the steels found that there was a small difference between the values without influence statistically significant in the results of current density and each rate. The pH values, in turn, also did not statistically influence the results obtained.
Note that the linear polarization method for corrosion rate measurements proved to be efficient and accurate in its determinations, with good correlation between the measurements of corrosion potential and current density. Moreover, it can be stated the importance of conducting more studies focused on understanding the variables that influence the corrosion processes, thus enabling better prediction of service life of reinforced concrete structures.