Introduction
With the aim to produce heat, fossil fuels (gas, oil products, coal) can be replaced by local biomass resources (plant or other organic matter, for example, wood chips and agricultural residues), in order to reduce the pollution of atmosphere caused by greenhouse gas emissions.
Agricultural residues are carbon -based materials generated as a by-product during the harvesting and processing of agricultural crops, according to Directive EN 14588 of the European Committee [1]. Agricultural wastes can be classified due to their provenance in to four main classes: wastes from soil plantations, waste from food industry, breeding, and slaughter wastes [2]. At the national level, out of the total of 238.397 thousand hectares, the sum of Romania’s surface, 61.4 % is represented by the agricultural area and 28.3 % of the area covered by forests and other lands with forest vegetation, in 2015, about 3.7 million toe from biomass and renewable waste, in this context we can see that Romania held 2.8 % of the total biomass and renewable waste obtained at European level, being on the 11th place, with the smallest amount of biomass and renewable waste being Malta, with only 3000 tons of oil equivalent. Romania’s agricultural sector is one of the largest in Europe. This sector can make large quantities available of residues and other unused or underutilised material to feed a national bio-based industry. Romanian agriculture has long been characterised by a fragmented landscape (92.2 % of the holdings by numbers are under 5 ha). The farms under 5 ha use only around 30 % of the total utilised agricultural area while large farms of 50 ha or more cover 52 % of the agricultural area [3]. Biomass represents 51.61 % of the global potential in Romania; biomass energy potential being approximately 7.6 tonnes of equivalent oil per year, out of which: 7.7 % biogas; 15.5 % lumber and firewood waste, 6.4 % wood waste, 63.2 % agricultural waste from cereals, corn stalk, vineyard; 7.2 % urban household waste [4]. According to the Romanian Strategy for the Valorization of Renewable Energy Resources (2003), which was approved by a Government Decision (GD 1535/2003), the Romanian potential of agricultural biomass is about 12.6 mio. tones x year-1which corresponds to approximately 201 PJ. More recent studies indicated that the amount of agricultural biomass would be about 154 PJ, with significant annual variations [5]. In the literature is reported the biomass energetic potential of our country of about 7594 tap/year (318x109 MJ/year) representing almost 19 % from the total primary energy resources in the past years. Agricultural wastes, resulting from cereals, corn, vine residues, are evaluated at 4799 x 103 tap (200.9 PJ/year) [6-7]. Largest quantities of biomass obtained from agriculture are reported in the South Plain Region of Romania. The richest counties from the point of view of the agricultural resource used as biomass in energy production are Timis (1432 thousand tons/98.6 %), Calarasi (934 thousand tons/ 98.9 %) and Braila (917 thousand tons, 99.15 %). According to the National Institute of Research and Development for Energy (ICEMENERG Bucharest), the plant biomass obtained from the forestry and agricultural sector will produce a thermal/ electric energy of 11249 thousand toe/year equivalent to 471000 TJ/year [8].
A challenge regarding the energetic use of agricultural residues refers to the plain zones having reduced forest resources and increased demands for firewood and reduction of available fossil energy resources [9].
In Poland and Latvia is presumed that the major biomass manufacturer for energy purposes will be agricultural industry [10-11]. In Latvia, straw is used in heating either by being transformed into pellets or pressed into bales or coils. In Poland, biomass undertake distinct significance, which is outlined in the currently mandatory legislation [12]. Biomass is processed into solid biofuels as briquettes and pellets, in order to facilitate the energetic utilization of biomass (transport, storage and combustion). Co-firing biomass with coal is a subject of great interest worldwide. The use of pure biomass firing in some industrial processes is unattractive due to its low bulk density, high moisture content and low calorific value.
Co-combustion is the burning of more than one fuel to produce power. The process is also known as co-firing or co-utilisation. Co-firing coal with biomass has been considered as an opportunity to decrease the dependence on coal and its associated impacts. Co-firing biomass with coal reduces fuel costs, emission of NOx, SOx levels and fossil CO2, reduce soil and water pollution. Burning biomass with fossil fuels has a positive impact, both on the climate and the economics of power generation [13-14]. Blending biomass with higher quality coal will reduce the corrosion effects. Biomass co-firing can be considered as a transition option towards a completely carbon-free power sector.
High- and low-energy biomass components can be mixed in convenient amounts. Components that produce a high amount of ash can be combined with components that produce a low amount of ash to create a good-quality pellet. Choosing the suitable ingredients and mixing them in adequate ratio adjusts the calorific value and moisture content as well as the ash content [15].
Sugarcane is one of the world’s most important crops, representing 21.1 % of the total global crop production, Brazil being the largest producer (632.127 million tons in 2014/2015) [16].
In the literature, sugarcanes by product, called bagasse, have been intensely studied, due to its high potential for bioenergy production [17]. It is known that sugarcane bagasse has a low heating value, between 17 and 20 MJ/kg, due to its high O2 composition, which is typical of biomass materials [18]. Mortari et al. [19] investigated the interaction between sugarcane bagasse and coal during co-firing, using different ratios of blend. The interaction between both materials occurs and improves the burnout of the blend in relation to the pure coal firing due to the contribution of sugarcane bagasse volatile matter. Similar studies were performed in many developing countries like Pakistan, India, Ghana and Nigeria, where co-combustion of agricultural residues in energy recovery schemes could significantly increase the income of the people in these countries. Combustion behaviour of the blends of shea-meal, cotton stalk, wood chips and bagasse with Russian coal were investigated and it was found that co-combustion of agricultural residues with coal has a positive impact on NOx, SO2 reduction and carbon burnout. The reported results demonstrated that co-combustion of agricultural residues with coal seems more practicable than pure agricultural residues firing due to the potential risk of slagging and fouling [20]. In Vietnam studies on the economic feasibility of co-firing rice straw were also performed [21]. Studying the blends of coal and olive residues, Riaza et al. [22] observed that the decreasing ignition temperature is proportional to the amount of the biomass in the blend, this effect being more pronounced in high rank coals.
According to IEA Bioenergy Task 32, 2009b [23] the procedure of co-firing more than 20 % of biomass in terms of energy content is technically reasonable and applicable. Also, the literature states that depending on the plant set-up and the chosen co-firing technology, substitution of more than 50 % of coal can also be achieved [24]. The co-firing mix also depends on the type of boiler available. In general, fluidised bed boilers can substitute higher levels of coal with biomass than pulverised coal-fired or grate-fired boilers [25]. Some technical impediments to co-firing refer to the local availability of large volume of quality biomass, as well as the charge of selection, handling, preparation, and transportation, in contrast with the approximately low cost of coal. By electing adequate co-firing techniques and feedstock, the hazard of slagging, fouling, erosion, and corrosion due to biomass operation can be prevented [25].
Biomass perennial herbaceous species present agroecological benefits not present in annual row crops such as a high content of organic carbon and reduced soil erosion. The species studied in the present work are from the Poaceae family, which are the most commonly used biomass species [26].
Taking into account the great Romanian potential of these species, makes biomass co-firing more economically attractive in the ratio 80 % biomass: 20 % coal.
Sorghum (Sorghum bicolor (L). Moench), is a very promising plant for energy application, being a multipurpose plant from the genus of about 25 species of flowering plants in the grass family (Poaceae) [27]. Sorghum crops are more valuable than cotton and corn considering lower energy intake and higher energy production yield [28-29], being used as a natural and cost-effective fuel source [30]. There is an increased interest of farmers to extend the cultivated surface and produce more sorghum in Romania, due to its potential use in the manufacturing industry as biomass for producing renewable energy, electricity, and heat, as a resource for achieving biofuels. In the period 2010-2019, the cultivated area with Sorghum registered a general ascending trend. In 2019, 15.712 ha were cultivated compared 10.283 ha in 2010, reflecting an increase by 52.79 % [31]. In Romania, sorghum is mainly cultivated in the West, Southwest Oltenia, Southeast, South Muntenia and Northwest, these five regions together accounting for 94 % of the whole cultivated area with this crop. In 2019, Romania produced 60.010 tons sorghum compared to 18.677 tons in 2010. If in 2010, our country produced 1.816 kg/ha, in 2019 the yield was 2.1 times higher, 3.819 kg/ha [31].
In literature, the largest areas of planted sunflower, rapeseed and soybean crops were reported to be in the regions of South, Southeast and Northeast of Romania [32].
Rapeseed is an important food and energy crop for European agriculture, increasing its potential during the last years. In the European Union the rapeseed cultivation concerning the oilseed production plays a crucial role [33]. Rapeseed crop represents a special case at present in Romania. A significant increase area sown with rapeseed in the range of 2002-2013 showed a decision of Romanian farmers caused by the demand on the market rape [34]. In 2020/2021, Romania’s rapeseed production reached 725 000 MT. The strong export demand resulted in 46 % higher exports, mostly to other EU markets with large crushing capacities, including the Netherlands (202 000 MT), the Czech Republic (94 000 MT), Germany (93 000 MT) and Belgium (71 000 MT) [35].
Among Romania’s area for oilseeds, sunflower accounts for the largest share, followed by rapeseed and soybeans. In fact, Romania is the largest sunflower producer in the European Union [35].
Sunflower (Helianthus annuus) is widely cultivated worldwide due to its relatively short growth cycle, high resistance to drought and adaptation to different soil conditions. Statistical data show that in 2019 Romania ranked first in the EU in sunflower both in production and area, with a harvest totalling 3.569 thousand tones. In 2019, the area cultivated with sunflower in Romania reached 1,282.7 thousand hectares representing almost one quarter of EU’s sunflower cultivated area [36]. Sunflower grist is a by-product of the sunflower oil industry.
Soybean is considered among the important agricultural plants. In our country soybean was introduced late in 1909. A growing interest of the farmers is to increase the soybeans area in the Danube region. Romania has a soybean cropping potential of 0.8-1.0 million Ha. This potential may generate more than 2 million tons representing about 5 % of the EU annual consumption [37]. Soybean grist is the main product in the processing of soybeans, obtained after pressing and extraction.
The agricultural by-products from the above presented species were studied in the form of pellets, in order to standardize the grist, improve the usefulness for energy purposes and facilitate their manipulation. Pellets from agricultural biomass residues are known as agripellets, being a popular biofuel on the energy market. There are no specific standards for quality requirements of agripellets. The calorific value of agripellets oscillates between 12 and 18 MJ/kg, and the ash content is relatively high (over 1 %) [38]. For heating purposes, a high-quality biomass needs: high yield; low ash content; low humidity level; high heating value; high bulk density.
In this paper the secondary residues from agricultural industry are characterised in order to evidence their suitability as renewable sources to substitute the fossil fuels.
The purpose of the study was to evaluate the suitability of the presented agricultural residues for energetic use, taking into account their heating values and physicochemical parameters. Higher heating value (HHV), higher heating value of ash free sample (HHVf), volatiles, fixed carbon, energy density, fuel value index (FVI), nitrogen and sulphur content were determined after combustion experiments. The following physical characteristics were determined: the bulk densities of the samples, moisture, and ash content.
Production of such biofuels may solve the problem of a bio-waste disposal and places a new environmentally friendly product on the energy market.
Experimental
Materials
In the present study, the agricultural by-products (coarse ground grist) of sorghum seeds, rape seeds, soyabean and sunflower seeds and their mixture with 20 % coal are used. These grists were obtained from S.C Expur Slobozia, a Romanian company having the main activity oil seeds processing for the purpose of obtaining crude and refined oil, meal and biodiesel.
The coal used in powder form was provided by the company S.C Explocom GK SRL, Lupeni, Romania.
Method and equipments
The four agricultural by-products of seeds were dried naturally for four weeks before procedure taken place. The measurements were performed in the Laboratory of Chemical Thermodynamics of Institute of Physical Chemistry “Ilie Murgulescu” of the Romanian Academy in accordance with European Union Standards for solid biofuel. Biomass samples were milled with the coal and then transformed in pellets. Through this type of processing, it was obtained a homogenous and solid product with high density, thus having an improvement in terms of biomass quality [39]. The Parr 2811 Pellet Press was used to produce the pellets. It provides a convenient means for compressing powdered materials into pellet or tablet form, being a compact, hand-operated press producing uniform pellets in a polished stainless-steel die and ejecting them smoothly into a stainless receiver without danger of contamination. The obtained pellets are cylindrical in shape with flat ends and have ½ inch diameter [40]. The samples pressed into pellets of about 0.6-0.8 g were weighed with a Mettler-Toledo analytical balance, model XP6 with an accuracy of ±2·10-6 g. The pellets were dried at 105±20C in a ventilated oven until constant mass. Three times determination for each sample were performed. The prepared raw materials were placed in plastic container and stored in a desiccator at room temperature until the analyses were carried out.
The determination of calorific value of agricultural grists and coal was performed in accordance with the ASTM D5865 Standard Test Method for Gross Calorific Value of Coal and Coke [41] and standard operating procedure Parr 6000 Calorimeter [42]. The experiments were carried out in a bomb calorimeter at oxygen pressure of 35 atmospheres and high purity (99.995 %). For each material there were made three determinations, in order to verify if the difference in calorific value between them is lower than 120 J/g, according to literature protocols [43]. The method was detailed in previous papers [44-45]. The identification of the parameters affecting the calorific value (moisture, ash content) was performed. The amount of nitric acid formed is determined by titration of the final bomb solution. The content of nitrogen of the product is calculated from the quantity of nitric acid formed [44]. Determination of sulphur content was performed adding in the resulted solution of the calorimeter bomb after combustion a diluted sodium hydroxide to convert sulphur to sulphates, which are largely precipitated with barium chloride as barium sulphate. The following formula was used to calculate the % sulphur content of the sample for a one-gram sample as follows [46]:
Ash content (AshC) was estimated in accordance with technical standard “EN14775:2009 [47]. Solid biofuel: Determination of ash content”. The ash quantity was calculated from the difference of the bomb crucible masses before and after combustion. The procedure was previously described [48]. For precision determinations, the ash content measurements were repeated three times.
Moisture content (w) was estimated in accordance to EN 13183-1:2004 standard and is expressed as the water proportion contained in the ground biomass [49].
Bulk Density
In order to determine the bulk density (ρ b ), the same analytical balance was used. An empty cylindrical container (150 mL) was weighed. The container was filled with the sample and the material was slightly compacted to ensure absence of large void spaces. The container and the sample were then weighed. The bulk density of the sample was calculated from the following Eq. 2:
Where: ρ b - The bulk density of the sample (g· cm-3); W 2 - The weight of the container and sample (g); W 1 - The weight of the container (g) V- The volume of the container (cm3). The standard method CEN/TS 15103 was followed [50].
Volatile matter content
Through mass difference, the volatile matter content (V d ) is determined for the considered samples (three times determination), according to EN ISO 18123:2015 standard and the following equation was used for calculation [51]:
where: m 1 - weight of empty vessel, g; m 2 - weight of vessel with sample before heating, g; m 3 - weight of vessel with sample after heating, g; w - moisture content, %.
The volatile matter and ash content were corrected to dry basis by using the moisture content.
Fixed carbon
FC- The fixed carbon (conform ASTM D3172 - 13) of samples was calculated by subtracting the sum of AshC- ash content (%) and V d - volatile matter (%) from 100. The fixed carbon is the residue left after removing the volatile matter and the ash from the substance.
Energy density
Energy density or caloric density was calculated using bulk density and calorific value of biomass feed stocks. The energy density was calculated based on the expression [52-53]:
where, ρ h - the bulk density of the biomass, kg/m3, CV - the calorific value of the biomass, MJ/kg.
Fuel value index
Fuel value index (FVI) was calculated in order to establish the suitability of the agricultural by products for energy production. The procedure was previously described [54-55]. The following formula was used:
FVI is the fuel value index (GJ/m3), q net - the net calorific value (GJ/kg), ρ b -the bulk density (kg/m3) AshC - the ash content (%), w- the moisture content (%).
Results and discussion
At regional level, there are a lack of studies-potential analysis of biomass by type and a reduced market for biomass products: briquettes, pellets- necessary for individual heating applications for dwellings.
The selected agricultural by-products may be a potential heating biomass source due to their availability in a large quantity from classical cultures and also due to the growing demand for thermal energy by reducing emissions related to energy deployment, thus knowledge of their characterization is essential.
The aim of the research was to evaluate the qualitative properties of coarse ground grist of sorghum seeds, rape seeds, soyabean, sunflower seeds and their mixture with coal for production of solid fuel. Our target, in this work, was to increase the interest in this topic by delivering the characteristic parameters. The know-how of the engineering features of the studied samples, such as bulk density, heating value, moisture and ash content is essential for the design and operation of procedure efficiency for handling, storage, transportation and conversion to fuels, heat and power [56].
Biomass combustion is a series of chemical reactions by which carbon is oxidized to carbon dioxide and hydrogen is oxidized to water [57]. Agricultural residues are good fuels for combustion, being rich in hydrogen and carbon. Ideally, all hydrogen and carbon would split off and combine with the oxygen in the air to create water vapor, carbon dioxide and heat [58]. Below is the generalized formula for a combustion reaction:
Complete combustion of biomass requires a certain amount of air. Air consists of 21% oxygen and about 79% nitrogen. Therefore, the product of a stoichiometric combustion of biomass in air will include carbon dioxide, water vapor and nitrogen. The stoichiometric equation for the combustion of biomass is given as follows [58]:
The heating value is expressed as higher heating value (HHV) and higher heating value of ash free sample (HHVf), calculated after substraction of ash from sample weight of HHV experiments for studied samples. In Table 1 are presented the values for HHV and HHVf (MJ/kg), bulk density (kg/m3), fuel value index FVI, (J/cm3) and volatile matter (%), for co fired and non-cofired samples. From Table 1 is ascertained that the cofired samples have higher heating value than non-cofired ones. The gross calorific value of studied agricultural biomass varied from (17.74-18.57 MJ/kg). Moderate calorific values were obtained for sunflower grist (18.57 MJ/kg), rape grist (18.35 MJ/kg) and soya grist (18.32 MJ/kg). For sorghum, calorific value is 17.74 MJ/kg. Higher values for the mentioned agricultural grists were obtained for the co-fired samples and ranged between 19.47-20.27 MJ/kg.
Table 1 Determination of physical and chemical properties of selected biomass agricultural residues for energetic use.
Species | Higher heating value (HHV)±S.D. (MJ/kg) | Higher heating value of ash free sample (HHVf)±S.D. (MJ/kg) | Bulk density (kg/m3) | FVI (J/cm3) | Volatile Matter (%) |
Sorghum grist | 17.13±0.1 | 17.74±0.11 | 232.38 | 103.76 | 89.10 |
Cofired sorghum grist | 19.05±0.02 | 20.16±0.02 | 280.2 | 472.07 | 83.66 |
Rape grist | 17.72±0.18 | 18.35±0.21 | 497.9 | 1008.9 | 84.02 |
Cofired rape grist | 18.92±0.1 | 19.47±0.13 | 486.8 | 3543.17 | 80.36 |
Soya grist | 17.39±0.1 | 18.32±0.7 | 621.06 | 399.02 | 89.79 |
Cofired soya grist | 19.22±0.02 | 20.01±0.02 | 410.4 | 745.16 | 83.30 |
Sunflower grist | 18.4±0.14 | 18.6±0.2 | 467 | 1743 | 89.76 |
Cofired sunflower grist | 20.1±0.16 | 20.3±0.12 | 446 | 4223.3 | 79.05 |
Coal | 29.1±0.05 | 29.4±0.07 | 788.12 | 13175.6 | 28 |
S.D.- represented the standard deviation based on a sample.
Our calorific values of sorghum pellets correspond to the values published by other authors, of about 17.9 MJ/kg [59] or 17-19 MJ/kg [60]. The heat of combustion for sunflower grist is comparable with the hemp and corn heat of combustion (ca. 18 MJ/kg). Among the co-fired samples, the higher heating value was obtained for co-fired sunflower grist, 20.27 MJ/kg and the lowest value is reported for co-fired rape grist, about 19.47 MJ/kg. The obtained calorific values for the co-fired samples are relatively high, which implies high energetic levels for all studied materials.
For co-fired mixtures a high-quality coal was used, its calorific value is about 29 MJ/kg (see Table 1), being in agreement with literature data for anthracites and bituminous coals, their calorific values being ranged from 25 to 33 MJ/kg; low quality coals, such as lignite, and peat-based fuels have calorific values of under 20 MJ/kg [61].
One of the major problems in transportation of residues is associated with their shipping costs. This is due to the low biomass density compared to wood and other biomass species; thus, the trucks cannot carry the allowed load. An alternative to resolve the transportation problems of large quantities of biomass over long distances is the densification procedure. This method also simplifies the stockpile and turns the biomass in a ready to be used form. Pellets from agricultural residues facilitate the transport and the storage issue due to the fact that are already processed. An important parameter influencing the transportation and storage as well as feeding the material into the thermochemical conversion system, is bulk density [62]. The calculated bulk density for the studied samples varies between 232 kg/m3-621 kg/m3 and along with the moisture content are important factors for downstream processing. These values are low compared to high quality coals like bituminous ones with values between 800-900 kg/m3.
The fuel value index (FVI) is a parameter which highlights the suitability of the studied agricultural residues for energy production. FVI depends upon calorific value, density, moisture, and ash content. A high value of the FVI reveals a good quality fuel, generally exceeding 500 GJ/m3 [63]. From Table 1 it can be seen that co-fired sunflower grist and co-fired rape grist present the highest values of the FVI among the studied species, the lowest value being calculated for non-cofired sorghum grist. This statement highlights the advantage of co-firing procedure of the samples with coal in order to enhance the quality of the fuel. The energy content of biomass is determined by its calorific value, which is influenced by biomass elemental composition, ash and moisture content. Moisture content is the most important factor that influences the calorific value of biomass [64]. From Fig. 2 it can be seen that the lower heating values of the studied biomass samples are caused by high moisture and ash contents.
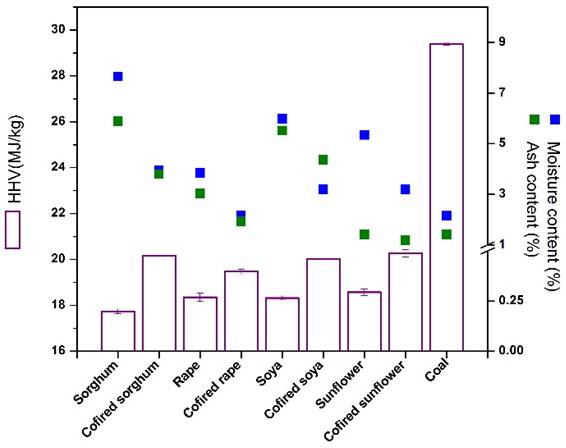
Fig. 2 Variation of higher heating value versus moisture and ash content for the studied co-fired and non-cofired samples.
Biomass has a substantially lower heating value than most coals. This is due to the high oxygen and moisture content. A possible problem when biomass is co-fired with coal is carbon consumption [65].
Our samples were pre-dried before examination and met humidity requirements of wooden pellets. The process of drying components is one of the steps of pellet production thus humidity value of the studied samples is in agreement with the humidity of pellets produced from the examined material. A decrease of the calorific value with increasing of the moisture content is observed from Fig. 2. In this regard, when moisture value is 90-100 %, the combustion becomes inefficient because all the energy is consumed to remove water from samples. A commonly accepted moisture content for biomass is 10-20 %, but not more than 40-50 %, because a part of it participates in the reaction of combustion.
Moisture content is an essential parameter regarding the selection of energy conversion process technology. Biomass fuels with low moisture content are more suited for thermal conversion technology while biomass fuels with high moisture content are more suited for biochemical process such as fermentation conversion. On this basis, from Fig. 2, it can be ascertained that biomass fuels under investigation are most favourable biomass feedstock for thermal conversion technologies, their moisture content ranging between 1-7 %.
Another parameter influencing the combustion process is the ash content which affects the handling and processing of biomass. The presence of the ash is closely related to operational problems such as slagging, fouling, sintering and corrosion. From Fig. 2, it can be seen that ash content ranged from 1-5 % depending on biomass type. While the ash content and volatile matter in bituminous coal is 20 % and 28 %, respectively, biomass fuels have the advantages of low ash content and high volatile matter that make them the ideal feedstock for pyrolysis and gasification. Our results indicate that the ash content is low, which represents a good indicator of combustion use due to the fact that there are low quantities of residual materials after the process.
Volatile matter, ash, and moisture are important components used for the quality characterization of fuel materials. Volatile matter, a key component of solid fuels, is used to measure the combustion characteristics. According to literature data high volatile matter (from 70 to 86 %) improves the combustion rate of the biomass during the devitalization phase [66]. On the contrary, low volatile matter causes high smoke within incomplete combustion and release toxic gases. Our values for volatiles are in the range 80-89 % (see Table 1). As it can be seen, biomass has a higher volatile yield than coal, this statement being a proof that these products are easier to ignite and burn.
Another calculated parameter is energy density (caloric density) presented in Fig. 3. Energy density and fuel value index (FVI) are important parameters for solid fuels characterisation. Energy density measures the amount of energy stored in a given volume of material.

Fig. 3 Plot of the variation of the energy density and fuel value index (FVI) for the studied samples.
The bulk and energy density are directly related with each other. The low energy density of the biomass with respect to oil and coal, implies a high cost of transportation and storage [67]. Consequently, the investigation and progress of methods aiming at greater concentration of energy per unit volume, as in pelletizing, are key to increase the use of biomass as an energy source. Pellets are important to the final product with compression and increased energy density, promoting easy handling, low humidity, large storage capacity, in addition to the thermal regularity and efficiency during combustion [67-68]. From Fig. 3 it can be seen that energy density and fuel value index are higher in the case of co-fired samples than non-cofired ones, thus highlighting the importance of the co-firing procedure.
In order to evidence the influence of fixed carbon, sulphur and nitrogen content upon the combustion process, their values were calculated and represented in Fig. 4.
Fixed carbon is the calculated percentage of material that was lost during the testing for volatile matter and ash, being determined in a proximate analysis, rather than through direct measurement [69]. When is an increase in the value of fixed carbon, it is accompanied by an increase in the calorific value of the tested material.
Additional by-products from the combustion process are nitrogen oxides (NOx), sulphur dioxide (SO2), hydrocarbons (HCs) volatile organic compounds (VOCs) and soot. Because of regulatory and efficiency concerns, it is best to minimize the presence of these potentially harmful by-products. The advantages of co-firing mainly relate to environmental benefits. Co-firing of biomass with fossil fuels provides means to reduce SO2 and CO2 emissions and it also may reduce NOx emissions. It is assumed that there is no net emission of CO2 from biomass combustion as plants use the same amount of CO2 during growth that is released in combustion. Every tonne of biomass co-fired directly reduces fossil CO2 emissions by over a tonne.
In the literature [70] the sulphur content for the growing energy crops ranges from 0.1 % to 0.2 %, in agreement to our obtained values. Research showed that the tested biomass contains sulphur in the amount that meets the criteria of the standards for wood pellets. Besides that, the presence of sulphur is a natural consequence of sulphur content in the vegetable proteins, which is a building material of tested biomass. The lower content of nitrogen and sulphur in biomass fuels compared with coal is especially important for environment protection. Low levels of sulphur also indicate a low potential of degrading the furnace which uses as fuel the studied materials.
Blending coal with biomass fuels can reduce fossil-based CO2 emissions. Co-firing of biomass residues with coal brings additional greenhouse gas mitigation by avoiding the CH4 release from the otherwise landfilled biomass.
Taking into account all above mentioned facts, it can be concluded that pellets from sorghum and soyabean grist biomass seem to be very suitable for a clean and efficient combustion. The study of the mixture characteristics helped us to conclude about the energetic efficiency and measure for environmental protection.
Conclusion
From the chemical analysis made on the studied materials, it can be considered that all of them, especially those co-fired, have a relatively high energetic potential and can further be used in firing processes.
The combustion heat of the studied pellets depends on the agricultural material they are made from. Insignificant differences were observed concerning the combustion heat of pellets from sorghum, rape, soya and sunflower grists. Significant differences were observed between the combustion heat of pellets from co-fired and non-cofired samples. The highest value of combustion heat, amounting to 20.27 MJ/kg was observed for pellets made from co-fired sunflower grist. The comparative analyse of biomass calorific properties are performed to emphasize that agricultural residues can successfully be used for renewable energy production, replacing the traditional and pollutant coal.
Our studied samples, especially co-fired ones, offer an alternative material for energy use, which meets the requirements of minimizing CO2, NOx and SOx emissions.
Knowing the physical and chemical characteristics for the studied products is very important in order to better understand the burned fuel behaviour, in order to better consolidate the biomass supply chain viability. The process of obtaining pellets is improved in order to be used for capitalization of agro-industrial residues.
The studied samples showed energy characteristics that indicate its potential to be used as energy sources in the form of pellets and can be considered as very promising feedstock for solid biofuel production.