1. Introduction
Electrochemical industries are among the largest electricity consumers in the manufacturing world. It is still rather common to find processes in which only one of the two sides of the cell produces a desirable transformation, whereas the complementary reaction at the other side is simply selected or allowed as to avoid interference with the target process and/or to offer fast kinetics as not to limit the main activity [1]. This is typically accompanied by a lack of an explicit interest about the use or the commercial value of the products or transformations generated through this complementary process that is usually the decomposition of the solvent. Thus, there is much room for improving the optimal energy expenditure by designing processes where current is made useful at both sides of the cell [2-9]. Even though this in itself does not ensure the total greening of a process, it does contribute towards this objective by responding to one of the main principles of green chemistry: minimize energy requirements [10]. In the present paper, we give an overview of several possible reaction schemes for this to happen and supplement them with specific selection criteria and examples. In addition, the extensive nomenclature dispersion in this area is revised and a consistent as well as simplified classification and schematization system is proposed.
2. Paired processes according to their mode of action
We propose that most of the paired processes summarized in the systematic review by Paddon et al. [2] can in principle be grouped according to their mode of action. In the following figures a letter inside a square symbolizes a reagent whereas a letter inside a circle symbolizes a product; Red and Ox symbolize the reduced and oxidized species of a redox pair, respectively; and the not enclosed letters symbolize intermediate species. Note that redox mediators reacting directly at the electrodes can be designated as electrochemical mediators, whereas those acting in the electrolytic solution are homogeneous redox mediators.
2.1 Use of reversible redox mediators
2.1.1 Single redox mediated systems.
An example is the synthesis of p-benzoquinone and hydroquinone from benzene [2,11]. The redox mediator in the cathodic side is the Cu2+/Cu+ system. Cu+ reduces O2(g) to a peroxo intermediate thus generating a peroxide complex with copper that oxidizes the aromatic ring and yields the same product as in the corresponding anodic oxidation of the aromatic species at a PbO2 electrode in a single H-cell (i.e., hydroquinone or quinone). In the paired process, both reactions occur simultaneously in the undivided cell (see Fig. 1). Peroxo intermediates are useful oxidizers produced by cathodic reactions, and whose chemical behavior is equivalent to the anodic reaction as shown in this example, whereby benzene is electrochemically oxidized and, at the same time, it is chemically oxidized to hydroquinone by this Cu-peroxo intermediate produced cathodically. Depending on experimental conditions, hydroquinone can be oxidized to quinone by the Cu-peroxo complex or else anodically. The result is a paired process with only one final product.
2.1.2 Multiple redox mediated systems
An example is the synthesis of sulfones (R-SO2-R) from sulfides (R-S-R) [2,5,12]. The redox mediator at the cathodic side is the HWO5 2-/ HWO4 2- system, while the OsO4(OH)2 2-/OsO2(OH)4 2- system mediates the electron removal at the anodic side. See Fig. 2. As in the previous example, hydrogen peroxide (cathodically produced by the 2e-dioxygen reduction) is used as the oxidant for generating the tungsten oxidizing species that produce the desired sulfones.
2.2 Use of at least one irreversible redox mediator
An example is the epoxidation of propylene at interdigitated electrodes [2,13]. The redox mediator here is the Br2/Br¯ system. Upon alkaline hydrolysis the anodically made Br2 yields HBrO that reacts with the double bond of propylene (A = CH3CH=CH2) to produce the corresponding bromohydrin (B = CH3CHOHCH2Br). Removal of the bromine atom and the acidic H in the OH- group by the OH¯ ions coming from the cathodic reduction of water promotes bromine elimination during the 3-member ring closure with the generation of the epoxide. See Fig. 3. The irreversibility stems from side reactions, one of which irreversibly generates BrO3 - ions [13].
2.3 Use of at least one reversible and one irreversible redox mediators
An example is the synthesis of epoxides and dibromides from olefins [2,14], where anodically generated Br2 adds irreversibly to an olefin (A = RCH=CHR´) producing the corresponding dibromide (B = RCHBrCHBrR´). The same olefin is simultaneously oxidized by the redox mediator [VO(acac)2OOH] to yield its epoxide (C = RCHCHR´O). The spent homogeneous redox agent is then regenerated by H2O2 produced cathodically from O2. See Fig. 4.
2.4 Use of multiple electron exchange processes
An example is the cathodic generation of nitrogen heterocyclic anions that react with anodically generated radical aromatic cations [2,15]. For example, 1 H-tetrazole (the simplest tetrazole, see species A = CH2N4 in Fig. 5) is cathodically converted by a one-electron transfer into its anion B (CHN4 -), which then pairs in a nucleophilic fashion with the electron-rich cation D (p-(CH3O)2C6H4 .+) produced by the anodic oxidation of 1,4-dimethoxybenzene (C = p-(CH3O)2C6H4). This step generates a complex intermediate that releases a second electron at the anode, yielding a mixture of tetrazolemethoxyarenes. See Fig. 5.
2.5 Use of multiple chemical reaction processes coupled to electron exchange processes
An example is the formation of protected homoallylic alcohols (see Fig. 6). Here, the cation F (CH2=N+(CH3)CHO, generated from the oxidation of N,N-dimethylformamide used as solvent) reacts with the anion D (CH2=CHCH2CH(Ar)O¯) resulting from the reaction between an aromatic aldehyde (C = ArCHO) and the allylic anion B (CH2=CHCH2 ¯), generated by the cathodic dehalogenation of allyl bromide, A (CH2=CHCH2Br) [2,16]. Both electron-transfer processes at the electrodes are followed by consecutive chemical reactions that yield the final product, G (CH2=CHCH2CH(Ar)OCH2N(CH3)CHO). The cationic intermediate of DMF F (CH2=N+(CH3)CHO) is obtained by a two-electron, one-proton release from the solvent, whereas the alkoxy intermediate D (CH2=CHCH2CH(Ar)O¯) is obtained after a 2-electron incorporation accompanied by bromide elimination to obtain the stabilized allylic anion.
3. Terms used in the literature
All of these processes involve steps that are more elementary and/or can be classified in global, simpler schemes. We have identified all the terms devoted in the literature to designate that useful reactions occur at both sides in an electrochemical cell; they are rather diverse and do not necessarily convey similar meanings, which leads to confusion and scattering. Table 1 summarizes the various terms that have been used.
4. Classification proposal
As can be easily perceived, this great disparity in terms and meanings obstructs communication and understanding within the electrochemical community and with people in other fields as well. Consequently, a simplified global scheme that encompasses all the terms included in Table 1 should be based on: a) reserving the terms combined and coupled to their most common usage on this table, b) noting that the terms concurrent, conjugate, dual, paired, and simultaneous refer essentially to the same type of processes, and c) noting that the term duet has the same meaning as the term linear and corresponds to processes where the same product is generated at both sides of an electrochemical cell through the production of reactive redox mediators at the electrodes. Therefore, these reactions can be clustered under the term linear paired electrolysis[51].
All these names of reactions can be accommodated within the term used by most references (i.e., paired). Therefore, we hereby match this proposal with the simplified global nomenclature system and schemes for the paired electrochemical reactions essentially proposed by Aust [3], Steckhan [42], and Paddon et al. [2] and merged as follows.
4.1 Parallel paired electrolysis
Both cathodic and anodic reactions are matched and contribute usefully to the formation of the final product(s) (see Fig. 7) [2]. Examples include the industrial cathodic synthesis of phthalide (B = C6H4COOCH2) from dimethyl phthalate (A = C6H4(C2H3O2)2) with the simultaneous anodic production of tert-butyltoluene dimethylacetal (D = (CH3)3CC6H4CH(OCH3)2) from tert-butyltoluene (C = (CH3)3CC6H4CH3) [3,7]; the cathodic synthesis of aniline from nitrobenzene with the simultaneous anodic generation of Cl2 from NaCl [25]; and the galvanostatic synthesis of Michael adducts (an enolate in the cathodic side and the Lewis acid BF3 in the anodic side, in the ionic liquid 1-ethyl-3-methylimidazolium tetrafluoroborate) [52].
4.2 Convergent paired electrolysis
The products generated at both sides of the cell react to form one final product (see Fig. 8) [3]. Examples include the generation of ClO2 from ClO3 ¯ (at the cathode) and from ClO2 ¯ (at the anode) [53]; the production of simultaneous electroluminescence from the emission of the 3-aminophthalate dianion radical (generated at the cathode by oxidation performed by the hypochlorite ions generated from the reduction of ClO2 ¯, and at the anode by the direct oxidation of luminol) [54]; and the simultaneous production of glyoxalic acid (C = CHOCOOH) by the cathodic reduction of oxalic acid (A = COOHCOOH) and the anodic oxidation of glyoxal (B = CHOCHO) [55,56].
4.3 Divergent paired electrolysis
Two different products are formed at the electrodes using a single starting material (see Fig. 9) [2]. Examples include the production of sorbitol (B = CH2OH(CHOH)4CH2OH) at the cathode and of gluconic acid (C = CH2OH(CHOH)4COOH) at the anode from glucose (A = CH2OH(CHOH)4CHO) [57-59] (58); the generation of l-cysteic acid (at the anode) and l-cysteine (at the cathode) from l-cystine [60,61]; the cathodic generation of ethylene and the anodic generation of oxalic acid from acetylene [62]; and the simultaneous anodic acetoxylation and cathodic carboxylation of conjugated dienes (e.g., 1,3-cyclohexadiene) and CO2 to produce the corresponding 1,4-diacids and 1,4-diols used as key synthetic precursors [63].
4.4 Linear paired electrolysis
One product is synthesized at both sides from the substrate by one or two-mediated electrode processes (not shown in this figure, see the simplified Fig. 10) [3]. For a more complete scheme, see for example Fig. 2. Examples include the production of n-butyric acid from n-butanol through its indirect anodic oxidation (by NiO(OH)) and indirect cathodic oxidation (by H2O2) [64]; the simultaneous oxidation of sodium gluconate to D-arabinose using the Fe3+/Fe2+ and ClO¯/Cl¯ redox mediators in the anolyte and the Fe3+/Fe2+ and V5+/V4+mediators in the catholyte [65]; the indirect cathodic oxidation of a hydroxylamine (A = CH3(CH2)3N(OH)(CH2)3CH3) by the O2/H2O2/WO5 2-/WO4 2- redox system to produce the corresponding N-amine N-oxide (i.e., a nitrone, B = CH3(CH2)3N(O)=CH(CH2)2CH3), coupled to the indirect anodic oxidation of the same hydroxylamine in the presence of a halide/halogen system (i.e., Br2/Br¯ or I2/I¯) [12]; and the production of amino imino methane-sulfonic acids from the corresponding thioureas, catalyzed by the WO5 2-/WO4 2- and Cl2/Cl¯ redox pairs. Here, the WO5 2- is continuously regenerated by H2O2 coming from the cathodic reduction of O2, as shown in Fig. 2. The nature of the sulfur-containing group defines the type of current efficiency response with the applied current density [66].
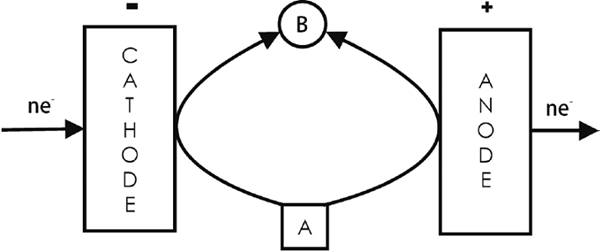
Fig. 10 Simplified linear paired electrolysis scheme [2,3,12,62,63,65,66]. A more complete description of these systems can be seen in Fig. 2. For example, a) A = n-butanol, B = n-butyric acid [64]; b) A = sodium gluconate, B = D-arabinose [65]; c) A = CH3(CH2)3N(OH)(CH2)3CH3, B = CH3(CH2)3N(O)=CH(CH2)2CH3[12]; and d) A = a thiourea, B = the corresponding amino imino methane-sulfonic acid [63].
The paired processes discussed so far, essentially involve organic starting materials and products (other than the redox mediators). Particular processes in other areas are presented next.
5. Inorganic paired electrochemical processes
Compared to the achievements and proposals in the organic paired electrosynthesis field, inorganic processes are rather scarce [67]. Selected examples are summarized below. (For simplicity, the physical state of aqueous species is omitted.)
5.1 The well-known chlor/alkali process is the most important paired process from the commercial standpoint. World production of these two inorganic compounds (i.e., Cl2 and NaOH) is the highest among all the electrochemical processes and it is higher than almost all the inorganic chemical processes (except that of sulfuric acid). The cathodic reaction consists of water reduction, whereas the anodic reaction consists of the oxidation of chloride ions from brine as the raw material [68]. This is a parallel paired electrolysis (see Fig. 7). The reactions involved in the process are:
5.2 In a cell equipped with a Pb anode and a Na2CrO4 aqueous solution in the anolyte, PbCrO4(s) is produced in this chamber while NaOH is generated in the catholyte as a result of Na+ migration and OH¯ production from water electrolysis. Linear voltammetry signaled the appropriate potential to be used for Pb dissolution. Cell voltage vs. time curves helped to identify undesired electrode passivation by an insoluble product layer [69]. This is an example of parallel paired electrolysis (see Fig. 7).
5.3 An unusual oxidant production scheme involves dehydration of HNO3 to N2O5 (note the same oxidation state for N in both compounds), where HNO3 is reduced at the cathode to yield N2O4. Due to the high volatility of the latter, it is then distilled from the cooled catholyte and directed towards the anolyte where re-oxidation occurs to generate N2O5 (i.e., a much safer nitrating agent than concentrated HNO3) [68,70]. An alternative is to avoid the heating step by using a membrane process [71]. This is a parallel paired electrolysis (see Fig. 7); in this example, product B from the cathode becomes reagent C in the anolyte.
5.4 In the classical process of electrorefining of metals applied on a large scale to the electrolytic refinement of copper, impure copper anodes are dissolved electrolytically to produce copper (II) ions, which are then transported to the cathode whereby they deposit without the impurities contained in the initial copper metal source [72]. This is a parallel paired electrolysis (see Fig. 7), except that in this example product D from the anode becomes reagent A in the catholyte.
5.5 The co-production of ClO2 and NaOH is achieved in a divided cell by the anodic oxidation of a NaClO2 solution with simultaneous H2O reduction. The Na+ ions migrate towards the cathode through a cation exchange membrane to compensate for the negative charges of the OH¯ generated there and produce NaOH [73]. This is a parallel paired electrolysis (see Fig. 7).
5.6 The production of the oxidizing agent NaBrO3 is based on the initial anodic oxidation of Br¯. The Br2 thus produced reacts with NaOH generated at the cathodic side from water electrolysis, giving rise to a disproportionation reaction that produces a mixture of Br¯ and BrO¯ ions. Afterwards, three BrO¯ ions disproportionate yielding the desired product, i.e., BrO3¯ and two Br¯ ions that can in principle be recycled into the process [74]. This is a parallel paired electrolysis (see Fig. 7) except that in this example products B and D react to form BrO¯ that disproportionates as described above.
6. Environmentally-related paired electrochemical processes
Fortunately, the idea of paired processes has reached the environmental arena and some processes have been developed in this area as well. Selected examples are described next. Since the objective of most of them is not a synthetic one, the processes in this section are different from those described above throughout this paper.
6.1 Paired organic pollutant degradation
A proof-of-concept of the paired electrochemical treatment of two organic molecules involves the cathodic reduction of dichlorophenol and the anodic oxidation of phenol in aqueous solution [75]. Another example involves the cathodic production of hydrogen peroxide from dioxygen reduction with the simultaneous degradation of phenol, where both processes occur on boron-doped diamond electrodes. These processes are carried out at the same acidic pH in order to use the peroxide produced in a second pollutant degradation scheme using Fenton's reaction (see below) [76].
6.2 Paired ligand degradation and metal ion recovery from metal complexes
The cathodic removal of metal ions (e.g., Cd(II), Cu(II), Ag(I)) and the anodic oxidation of their ligands (typically CN¯) from the electroplating, metal finishing, and metallurgical industries have been thoroughly studied [30-32, 46, 77]. While the chemical route generates large amounts of sludge containing metal hydroxides [31], the electrolytic route offers the possibility of recovering metals in their elementary solid form (or else as oxides [47]), while directly or indirectly destroying their ligands [30,31,46,48,77]. In the case of CN¯ ligands, such destruction is through their oxidation to CNO¯ (which is much less toxic than CN¯) followed by further oxidation to innocuous N2. Seawater may be added to the process to generate chlorinated oxidants capable of performing this transformation into N2 [46,48]. The undesirable side oxidation of CNO¯ into NO3¯ ions can be minimized by regulating the electrolysis time [78]. Interestingly, a judicious combination of surface area (that controls the potential in a typical galvanostatic process) and pH can facilitate the global reduction of NO3¯ to N2(g) [45].
6.3 Paired COD (chemical oxygen demand) removal and metal ion recovery
In a similar fashion as above, the paired cathodic removal of copper ions and the anodic oxidation of COD can be achieved with excellent yields [30,33,47,79]. Part of this success has been attributed to the simultaneous cathodic generation of strong oxidizers capable of attacking organic matter [33].
6.4 Paired inorganic pollutant degradation or removal
A pollutant is transformed into its pure, useful elemental components in very few cases. In one of them, the highly noxious H2S is electrochemically treated either directly or indirectly with the resulting simultaneous production of high purity H2(g) at the cathode and of S(s) in the anolyte (H2SO4 or IO3¯ ions can also be produced) [80-82] (81). In the indirect case, the gas is first absorbed into a liquid containing an oxidizing agent that oxidizes S2- ions to elemental S(s). The spent oxidizer can be anodically regenerated and returned to the absorbing system in an outer-cell process [34,83]. Simultaneously, protons from water are reduced at the cathode and produce H2(g). Electrochemical methods offer an additional variety of possibilities for H2S treatment, although not all of them are paired processes [83-92]. Another process involves the electrochemical treatment of N-containing wastes by the paired cathodic reduction of NO3¯ ions and the anodic oxidation of NH3 in aqueous solution. This can be achieved using a zero-gap solid polymer electrolyte, ZGSPE. Although the selectivity for the NH3 oxidation to N2 needs enhancement, no undesirable NO2¯ ions are generated and N2 is the main product [39]. In yet a different case, Ag can be cathodically recovered from photographic wastes containing Ag+ and S2O3 2- ions. Here, the anodic generation of H+ provides the required low pH for the disproportionation of S2O3 2- into S(s) and SO3 2- or SO2(g) [51], or else into S2- and SO4 2-[93]. The sulfide ions then precipitate with the silver (I) ions present, forming insoluble Ag2S that is recovered easily by filtration. Interestingly, insoluble Ag2S is also generated in the catholyte by the reaction between the Ag(I) ions and the S2- ions produced by the reduction of S2O3 2-, making this a linear paired process [51].
6.5 Paired organic or inorganic pollutant removal and useful water electrolysis
Flue gas desulfurization (FGD) processes for the removal of SO2(g), are typically based on its reversible absorption in sodium citrate solutions [94], or its essentially irreversible absorption in basic solutions [95,96]. Problems involving slow kinetics and abundant sludge generation have promoted the search for alternative remediation methods. Electrochemical schemes have been developed based on the direct or indirect anodic oxidationof SO2(g) to SO4 2- (which in acidic media forms H2SO4) or its reduction into elemental S(s); the paired reduction of water produces useful H2(g) [95,97-101]. In another example, organic textile dye effluents are anodically degraded with the paired cathodic generation of NaOH [49] or H2(g) production [102] in an electrochemical membrane cell. Additionally, a paired electroprecipitation and electrogenerated Fenton oxidation method (called peroxicoagulation) for the removal of organics (e.g., vegetal tannins) involves the introduction of Fe(II) ions from an Fe anode into the solution with the paired cathodic generation of H2O2 from O2(g) reduction [103,104]. The combination of Fe(II) with the peroxide generates the well-known Fenton´s reagent that produces highly oxidizing ●OH radicals, Fe(III), and OH¯ [105]. The mineralization accomplished by the radicals, together with the precipitation of the resulting Fe(III) oxyhydroxides, is very effective for the removal of pollutants from synthetic wastewaters [17, 106-108].
6.6 Paired production of environmentally friendly oxidizing/disinfecting agents
The paired production of O3(g) and H2O2 in a flow reactor equipped with a proton exchange membrane avoids the use of two separate cells. In the first one, O3(g) is anodically produced and H2(g) is sacrificially generated at the cathode, whereas in the second one, H2O2 is produced at the cathode and O2(g) is sacrificially generated at the anode [109]. Another example involves the anodic and cathodic electrogeneration of H2O2 and ClO¯ ions from dissolved O2(g) and Cl¯ ions, respectively, in aqueous solution. The combined action of both oxidizing agents degrades selected organics (e.g., formaldehyde) very effectively [40]. A third example involves the production of a disinfecting agent at both sides of the cell through the generation of ClO2 from ClO3¯ (at the cathode) and ClO2¯ (at the anode) as discussed above [53].
7. Advantages of paired processes
As discussed earlier, multiple organic synthetic routes have been designed using this concept (see for example the reviews in refs. 2-8), which has been extended to other fields, such as inorganic synthesis [8, 67-74] and environmental remediation [35,42,75]. Benefits include not only economic aspects, but also electricity savings that contribute to a decrease in fossil fuel usage with its concomitant combustion waste production. This approach also aims at useful products on both sides circumventing further treatments and costly disposal [3,8]. Other advantages of these processes compared to conventional electrolysis include:
7.1 Energy consumption can be reduced as much as 50% and time can be saved [35,40,65].
7.2 Current efficiency can theoretically be increased up to 200% [3,40,41,65]. This is so because current efficiency can be defined as the moles of products per unit of charge moved in the cell [110]. Therefore, yields can be higher than 100% in cells where both sides of the current are used to advantage [2,7,12,14,27,41,66,110,111].
7.3 Resources are preserved by avoiding the need for additional separate electrodes, electrolytes, etc. [3].
7.4 Wastes/emissions can be minimized and processes made greener with higher atom economies [3,7,110].
7.5 Instead of the requirement for two separate reactors, space can be saved and optimized.
7.6 The economics of a process benefit as fewer separation and synthetic steps are required.
8. Reactor/cell design strategies
Due to the highly specific nature of the different processes and the fact that literature reports on paired developments seldom delve into the intricacies of reactor/cell design, a generalization is not possible. However, some observations may offer an initial guide.
8.1 The issues of product separation and isolation are of fundamental relevance since an intermediate or product must not return to the opposite electrode where it was formed before reacting (i.e., electrochemical short circuits) as this could destroy key components or reverse the desired reaction. This effect, together with possible reactant cross-contamination, would represent a serious economic drawback [8] and must be avoided [2,3,9,101]. Therefore some researchers have used H-type cells [2,11,12,14,37,64,67,111] and other cells with diverse separation strategies (e.g., fritted glass [40,41,52,65,112,113], porous polymeric membranes [58,71], ion exchange membranes [49,101,102,109,114-116], and ion exchange resins [51]). Fitting electrodes directly into membranes permits more compact designs [101]. Membranes also avoid electrolyte exchange generated by pressure variations [101]. Undivided batch [30,47,78,111,117-119] or semi-batch [38], as well as flow-by [120], flow-through [2,58,67,113,121], flow-through coupled to a continuous stirred tank reactor (CSTR) [113], radial flow [48], and thin layer flow cell systems [122,123] have been employed. Some even consist of 3-compartments that prevent electrochemical short circuits by selectively avoiding reactant migration [101,116,124].
8.2 To determine the current density in an electrolytic reactor design it is necessary to define and/or calculate several engineering parameters like fluid dynamics, heat and mass transfer, separation processes, process modeling and optimization, and process control. As in kinetic models, the determination of current density is a function of the diffusional and activation current densities. At the same time, the activation parameters are expressed in terms of Tafel behavior [125]. For this reason, the capacitive currents represent a less important design factor concerning the operating current density for different paired reactions. The operational current must be smaller than the limiting current of either side of the cell so that the global process can be made efficient and produce high yields. This is achieved when the mass transfer coefficients are raised by either increasing the parameters associated with the corresponding diffusion coefficient or decreasing the convection layer thickness by increasing the convective term of the mass transfer expression [123]. Current densities may vary widely according to the system (e.g., from 1 to 1000 mA cm-2[37,101]).
To obtain the optimum current density it is necessary to maximize its function through an optimization technique as to allow finding the optimum current density without having to resort to heuristic rules, as it was done in the past (generally based on a percentage of the limiting current density) [126]. Simulations and modeling of electrochemical reactors using, for example, the finite element method [127], dynamic simulation [128], and the modified Shooting-Runge Kutta numerical method [113,129] can save time and cost in the design/selection of systems from an engineering point of view.
8.3 Another key aspect to be evaluated during electrochemical reactor design (and consequently to determine the operating current density) is the cell potential. This is of great practical importance since electricity costs are directly proportional to it. As stated earlier, due to the paired processes characteristics many of them use membranes or diaphragms. In these cases, the parameters to determine the cell potential include the anodic and cathodic potentials, as well as the voltage drops caused by ohmic resistance in the anolyte, catholyte, and in the diaphragm or membrane. To minimize the cell voltage for a given current density it is necessary to: 1) properly select the electrode materials for each reaction; 2) minimize the distance between electrodes; 3) maximize the electrolyte conductivities; and 4) select a membrane (or a diaphragm) that produces the lowest potential drop [125]. Ohmic drop considerations are obviously important especially when using membranes, since for example Nafion 125 can offer a resistance of up to 5 ohms cm2 at room temperature even in a 55% H2SO4 electrolyte [101].
8.4 In addition to the ohmic drops it is necessary to determine other reactor parameters such as space-time yield and chemical yield. The former is defined as the mass of product generated by a unit reactor volume per unit of time. The chemical yield is the maximum amount of product that can be obtained for a 100% conversion of the reactant [125].
8.5 Mass transfer can be enhanced for example by vigorous stirring [30,37,47,67,121,130], gas bubbling [12,14,30,40,64,65,114], or by using tridimensional electrodes (e.g., metal meshes [56], porous [17,57,101,121,131,132], particulated [57], or fluidized beds [69]). When volatile solvents are used, reflux condensation may be necessary [130].
8.6 In the case of homogeneous reactions between two shortlived intermediates, microflow systems [4,133,134] and interdigitated band electrode arrays (IBEA) with narrow interelectrode gaps (i.e., 0.25 - 1 mm) that allow an overlap of the cathodic and anodic diffusion layers have been used [2,127,135]. These offer low ohmic losses, enhanced mass transfer, and much higher efficiencies than, for example, parallel plate electrode configurations [127]. Some even avoid the requirement for intentionally added electrolytes [134], thereby increasing the potential for low-emission processes.
9. Additional selection criteria for paired reactions related to energy savings
In addition to the considerations discussed above, other factors and recommendations include the following:
9.1 Increased efficiency should be attempted by using side-by-side reactions, neither of which individually is lower in voltage than commercial half-cell reactions, but which together result in an increased voltage drop and high-energy savings. A wrong approach would be to simply prioritize lower voltage reactions [20].
9.2 Both electrode processes must be chemically and electrochemically compatible, i.e., no undesirable reactions should occur among the participating species [3].
9.3 The selection of electrode materials is fundamental for the success of a paired system as it must take into account their possible interaction with the reagents, products and intermediates; a summary has been given elsewhere [2]. In addition, electrode materials must be selected carefully to prevent the global process from being controlled by one of the simultaneous reactions.
9.4 For the selection of complementary reactions:
9.4.1 Concerning hydrogen production
9.4.1a Promote hydrogen production
When the aqueous chemistry of a paired cathodic reaction requires hydrogen atoms, it is suitable to use low hydrogen overpotential electrodes (e.g., Raney Ni). This also betters current efficiency and lowers the necessary operating potential [57].
9.4.1b Avoid hydrogen production
In some cases, it is desirable to avoid hydrogen production by replacing it with a useful cathodic reaction to save assembly and consumption costs from production to application, and to reduce the pressure in the electrolyzer and electricity consumption (e.g., nitrobenzene reduction) [24]. Another alternative consists of using cathodes with high overpotential for hydrogen generation.
During the paired generation of dioxygen, the cathodic hydrogen production coupled to water oxidation can be replaced by the generation of H2O2 and, therefore, the system is converted from a 4e- to a 2e- process. This translates into a considerable decomposition voltage decrease and up to a doubling of the production efficiency [36]. H2O2 can be significantly useful in other specific chemical transformations (see below).
Hydrogen ions may be reduced simultaneously with the species of interest (e.g., nitrates) [39], thus competing for the active sites; this hinders their reduction. Alternatively, adsorbed hydrogen species may hydrogenate intermediates. Both cases are detrimental for the process of interest and this can be analyzed in advance by electrochemical techniques such as cyclic voltammetry [39].
When using divided cells, the H+ generated during electrooxidation of organic compounds can be used in the cathodic chamber for electroreduction processes that require H+. In this way, protons are not accumulated and hydrogen production is limited. A proton-exchange membrane can be used as separator to serve this objective [76].
9.4.2 Concerning dioxygen production
9.4.2a Avoid dioxygen production
The use of a hydrogen gas-fed anode has been reported to avoid the generation of dioxygen that consumes a large amount of energy [121].
The use of acidic solutions is another strategy to inhibit dioxygen generation. This enhances current efficiency for target anodic processes [130].
The use of high oxygen overvoltage electrodes (e.g., boron-doped diamond electrodes, BDDE) limits water oxidation and considerably expands the anodic electrochemical potential limit to allow the occurrence of other reactions of interest [103].
Once the paired reactions are selected, the necessary conditions for the individual reactions can be preliminarily optimized and the conditions for the paired process can be fully optimized afterwards [12].
10. Conclusions
Processes in which current is beneficially utilized at both electrode chambers in an electrochemical cell can result in significant advantages from the economic and environmental points of view. Since such processes are becoming more common, design principles based on thermodynamic, kinetic, and chemical criteria -together with appropriate nomenclature- must be widely disseminated to facilitate their usage. Since the fraction of these processes that have reached industrial scale is minimal, a much greater emphasis needs to be given to such developments to benefit from the multiple advantages discussed in this paper. The electrochemical community is definitely developing more paired processes, which should be available in the near future. From the above discussion, it is clear that the organic synthesis field is reaching maturity while the inorganic synthesis and the environmentally related fields are emerging. The biochemical field is poorly exploited, and thus there is a vast opportunity in this area.