1. Introduction
Researchers are striving hard to make different types of service robots that can perform any work related to day to day life. Wheeled robots are being used in many applications such as manufacturing, healthcare, warehouse, fire stations, etc. The navigation and control of a wheeled robot is less complicated compared to the leg-type robots. Therefore, the concept of the wheeled robot has been used in most of the service robots. The firefighting robot designing and controlling problems are being investigated by several researchers (AlHaza et al., 2015; Khoon et al., 2012; Li et al., 2019; Tsai et al., 2010; Pack et al., 2004; Park et al., 2008; Taha & Marhoon, 2018) because, during fire rescuing operations, many firefighters have lost their lives. Tsai et al. (2010) designed the Deoxyribonucleic Acid (DNA) algorithm and implemented this algorithm in the FPGA chip to control the motion and direction of an omnidirectional firefighter wheeled robot. In reference (Khoon et al., 2012), the autonomous firefighting mobile platform was proposed to patrol and monitor the fire through a flame sensor-based two- wheeled robot. The developed wheeled robot could travel only in the smooth terrain, and the fire extinguisher unit has not been used in their developed model.
Another interesting work can be found in the article (Park et al., 2008), where the authors make the wireless communication system between the firefighting robot and remote operator. Additionally, they briefly discuss the complete system architecture of the firefighting robot. However, in their model, fire extinguisher gas arrangement was not found. An example of Simultaneous Localization and Mapping (SLAM) technology and infrared thermal imaging techniques can be seen in Li et al. (2019). The authors implemented these techniques for map-based navigation and fire detection for fire reconnaissance robot in their work. In an article (AlHaza et al., 2015), the authors have designed the three-dimensional AutoCAD model of the indoor firefighting robot and discussed the fire extinguisher unit's control features. However, in their work, the fire fighting robot's physical model and experimental studies were not found.
Pack et al. (2004) have conducted an autonomous firefighting robot design competition. In that competition, different types of firefighting robots were presented and tested during the fire extinguishing process in a maze environment. Water-based firefighting wheeled robot has been made by Taha & Marhoon (2018). However, the water cannot control the fire effectively as compared to extinguisher gas. Further, Samkari et al. (2019) make the liquid-extinguisher tank equipped smart firefighting robot system for fire detection and control. However, real-time experiments during the fire extinguishing process were not performed in their work. An extensive review article on a short history of mobile firefighting robot was reported in the article (Tan et al., 2013). Besides, they provide a reference for new future research. A voice- controlled fire extinguisher vehicle was found in the article (Pednekar et al., 2015). The small water pump connected with the pipe was installed above the vehicle to overcome the fire in that work. In references (Aliff et al., 2019; Sampath, 2011), the authors design the water-based compact size firefighting robots. However, their robots could travel only on the flat surface.
After elaborate study of the literature review, we have found that the various types of firefighter robots have been designed and presented by the researchers. However, many robots could travel only on the flat surface. Besides, most firefighter robots use water as a fire extinguisher, which cannot control the fire effectively compared to extinguisher gas. Therefore, in this article, we design and present the all-terrain differential- driven caterpillar-wheeled based unmanned FER, which can detect, monitor, and extinguish the fire by spreading the gas in any field. Moreover, it can climb the staircase also. Presentation of our work is as follows: - Section 2 presents the kinematic analysis of an unmanned fire extinguisher robot. Section 3 provides a brief description of the all-terrain differential-driven caterpillar-wheeled-based unmanned fire extinguisher robot. The outcomes of the experiments are organized and elaborated on in Section 4. Finally, the conclusion and future research work of the present work are summarized in Section 5.
2. Kinematic analysis of an unmanned fire extinguisher robot (FER)
This section presents the kinematic equations for an unmanned Fire Extinguisher Robot (FER), which are useful to control the motion and orientation of FER. Figure 1 illustrates the schematic representation of kinematic parts of an all- terrain differential-driven caterpillar-wheeled based unmanned fire extinguisher robot in the two-dimensional plane. It consists of caterpillar driving wheels, which carry the mechanical chassis. The six caterpillar driving wheels, attached with the six DC motors drive the FER. The three caterpillar driving wheels set, connected on the left side of FER, are controlled as a left wheel driving system. Similarly, another three caterpillar driving wheels set, attached on the right side of FER, are completely run as a right wheel driving system. The V L denotes the left wheel driving system, and V R indicates the right wheel driving system in the kinematic equations. The FER moves in the solid plane, and a rigid chassis make it. The axes (x, y) are the present posture of the FER from the origin 𝑂 point in the global frame {O, X, Y}. In Figure 1, θ denotes the orientation angle of the FER with respect to an axis (O, X), L is the track width between the left and right driving systems, R is the radius of the wheel, C is the center of the mass of the FER system. The following kinematic equations control the velocities and steering angle of the FER: where, V and ω are center (mean) linear velocity and center angular velocity of the FER, respectively. These V and ω control the motion and orientation of the FER in the C/C++ microcontroller programming, respectively. Next, ωR and ωL represent the angular velocities of the right wheel driving system and left wheel driving system, respectively.
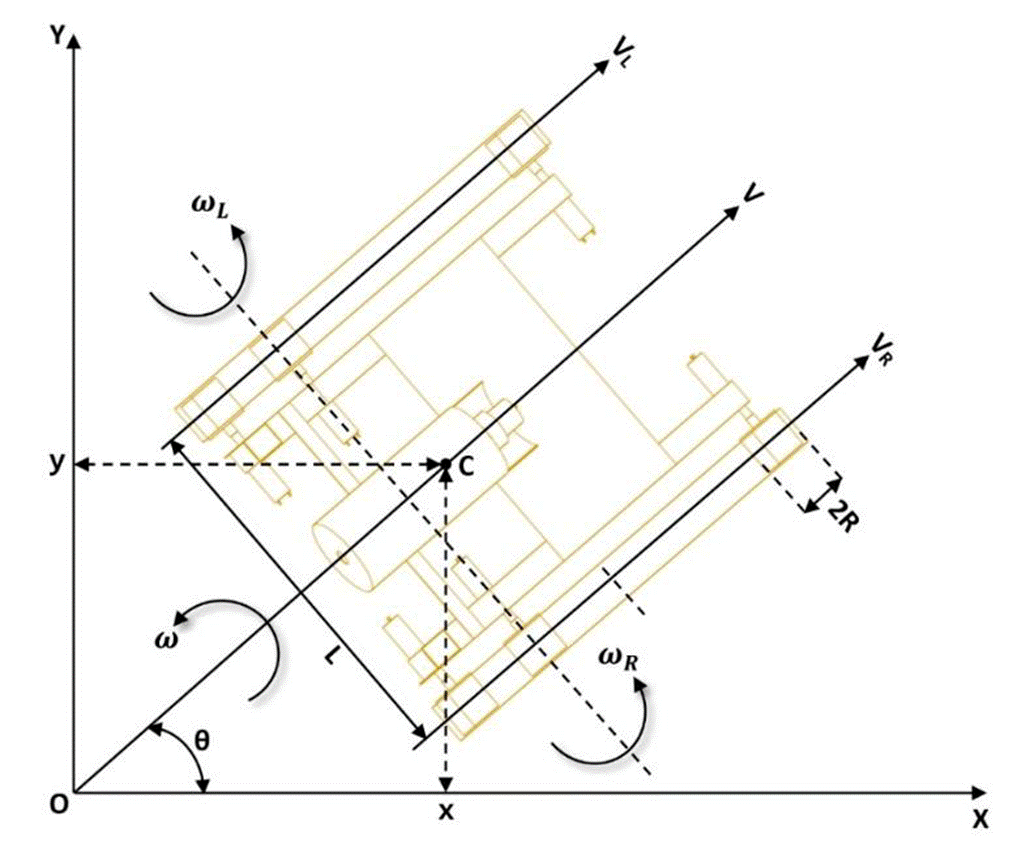
Figure 1 Schematic representation of kinematic parts of all- terrain differential-driven caterpillar-wheeled based unmanned FER in the two-dimensional plane.
Further, the following equations express the velocity (linear and angular) with respect to time (𝑡):
Next, the following conditions are used for the straight motion and orientation control of the all-terrain differential- driven caterpillar-wheeled based unmanned FER:
3. Brief description about the all-terrain differential- driven caterpillar-wheeled based unmanned fire extinguisher robot (FER)
This section portrays briefly about the developed all-terrain differential-driven caterpillar-wheeled based unmanned Fire Extinguisher Robot (FER). SolidWorks software is used to design the two-dimensional (2D) and three-dimensional (3D) models of the FER. Figures 2-8 show the various 2D and 3D views of the FER. Table 1 reveals the part number and name of the various components of an unmanned FER. FER's mechanical structure has been divided into the two assembled units, one unit drives the FER, and another unit does spread the fire extinguisher gas through the nozzle of the equipped cylinder. The brief description of some figures and the connections of various components have been described below:
Table 1 Part number and name of the various components of an unmanned FER.
Part Number | Part Name |
---|---|
1 | Left Wheel Driving System |
2 | Right Wheel Driving System |
3 | Track Belt |
4 | Wheel |
5 | Left Chassis Leg |
6 | Right Chassis Leg |
7 | DC Motor |
8 | DC Motor Clamp |
9 | Open and Close Valve of Gas Cylinder |
10 | Extinguish Gas Cylinder Holder |
11 | Nozzle |
The driving unit of unmanned FER consists of left driving wheel system (1), right driving wheel system (2), track belt (3), wheel (4), left chassis leg (5), right chassis leg (6), DC motor (7), and DC motor clamp (8). Similarly, the fire extinguisher gas unit consists of the open and close valve of fire extinguish gas from the cylinder (9), holder (10) that carries the extinguish gas cylinder, and nozzle (11). Figure 2 illustrates the isometric view of the FER. In the model, the left driving wheel system (1) and right driving wheel system (2) provide the forward, backward, clockwise, and anti-clockwise motion to the FER. Further, Figure 7 shows the exploded view of the driving unit of FER. In this figure, all the driving system components have been disassembled from the mechanical structure of FER. The three DC motor clamp (8) carries the three DC motors (7) on the left chassis leg (5) of the FER. Similarly, another three sets of DC motors (7) with clamp (8) are attached to the right chassis leg (6) of FER. The central part of the mechanical structure supports the fire extinguish gas unit. Figure 8 demonstrates the isometric view of the fire extinguisher gas cylinder unit. In this figure, the motor driver sends the command to the DC motor (7) to open or close the valve of a gas cylinder (9), and the valve spreads the fire extinguisher gas from the nozzle (11).
4. Experimental study
This section briefly discusses the electronic components of an unmanned FER and real-time experiments during the fire extinguishing process on the wall. The snapshots of different FER’s physical model views have been illustrated in Figure 9 (A to E). The FER is 48.8 cm long, 38.1 cm in width, 21.7 cm in height, and its total weight is 9 Kg weight. The chassis is made from an aluminum sheet of 4 mm thickness because of its lightweight and robustness. Also, the aluminum can endure sustained temperatures up to 200°C. The FER includes various electronic components like Arduino MEGA (ATmega2560) microcontroller, DC geared motor, motor driver, breadboard, Bluetooth module, on-off switch, gas sensor, temperature sensor, rechargeable lithium-polymer (LiPo) battery, voltage regulator IC (IC-7805), and jump wires. The FER can move forward or backward direction, and it can travel with a top speed of 1.2 m/sec. The Bluetooth module (HC-06, four pins) has been used for communication purposes in an unmanned FER. It can transfer the data up to a distance of 10 meters. The attached temperature sensor (DS18B20) can measure the temperature changes between the -55°C to +125°C. This sensor is used to measure the temperature changes that occur during the fire in the workspace. Similarly, one gas sensor (MQ- 2) is installed in an unmanned FER to detect various gases present in the fire like methane, CO, and hydrogen, etc.
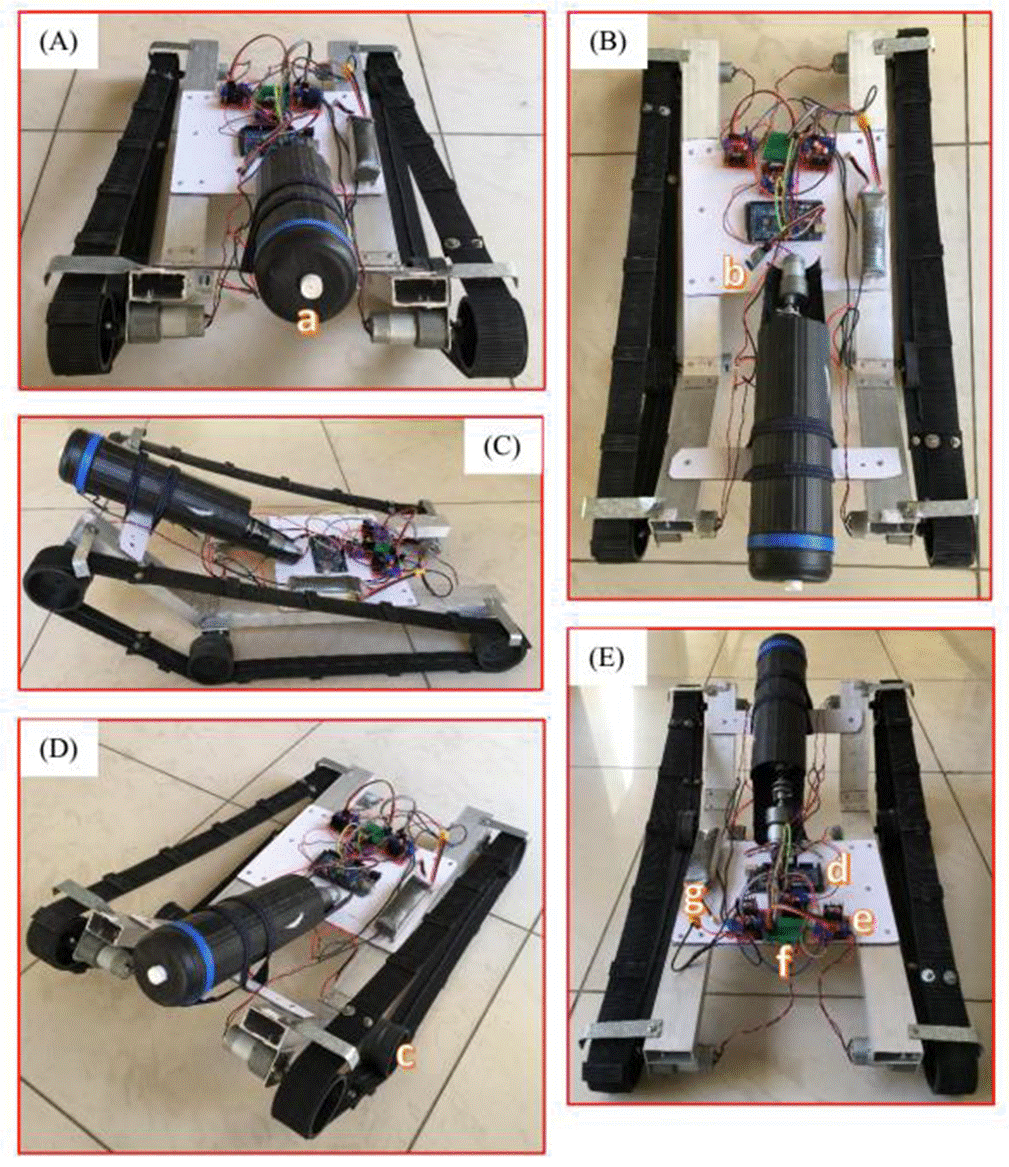
Figure 9 Snapshots of different views of the physical model of FER: (A) Front view, (B) top view, (C) side view, (D) isometric view, (E) rear view. Note: a-Fire extinguisher gas cylinder unit, b-Bluetooth host serial transceiver module, c-DC motor, c-driving wheels, d-Arduino MEGA microcontroller, e-motors drivers, f- breadboard, g-LiPo battery.
In this study, the FER’s minimum and maximum speed have been fixed between 0.4 m/sec to 1.2 m/sec. It consists of a gas sensor and a temperature sensor. These sensors can detect fire, smoke, and heat. The FER is equipped with an Arduino MEGA (ATmega2560) microcontroller, and it makes a sensor-actuator system for the FER. The kinematic equations (listed in Section 2) of FER are embedded in the Arduino MEGA (ATmega2560) microcontroller as a navigational controller to guide the FER during the navigation and fire extinguishing process. The navigation controller programming has been written in the C and C++ language and embedded in the microcontroller. This microcontroller sends the control commands to the motor drive, and according to this command, the motor driver adjusts the motion of the left wheel driving system and right wheel driving system. The motor driver’s input pins also provide the clockwise and anti- clockwise motion to the left wheel driving system and right wheel driving system of the FER.
Similarly, the motor driver’s enable pins to control the velocities of the left wheel driving system and right wheel driving system of the FER through the Pulse Width Modulation (PWM) signal. Besides, one DC motor through a motor driver and microcontroller controls the gas cylinder’s open and close valve. The lithium-polymer (LiPo) batteries, 11.1 Volt, 2200 mAh, give the power to the FER to perform the fire extinguishing process. The voltage regulator IC-7085 drops 11.1 Volt to 5 Volt to provide the power to the Arduino MEGA (ATmega2560) microcontroller.
Figure 10 (A to D) illustrates the snapshots of FER’s experimental results during fire extinguishing operations on the wall. For experimental purposes, we paste some pages on the wall and set the pages on fire. The gas sensor and a temperature sensor of FER detect the smoke and fire in the workspace, and the microcontroller receives the sensor reading and indicates this to the operator. After identifying the fire, the operator sends the navigation control command to FER’s microcontroller through the Bluetooth signal from an android phone (remote). Once the FER is reached near the fire, the operator gives a valve opening control command to the gas cylinder’s DC motor. After spreading the extinguisher gas on the fire, the operator closes the cylinder’s valve through the remote. The fire extinguish process is done by the remote control; therefore, we can say that the FER controls the fire in hazardous conditions without harming the operator. Besides, we have tested this FER in the staircase and presented the broad overview of the navigation results during the stair climbing in Figure 11 (A to D). Figure 12 reveals the real-time recorded angular velocities (in Degree/Second) of left and right wheel driving systems of FER during the stair climbing process in Figure 11.
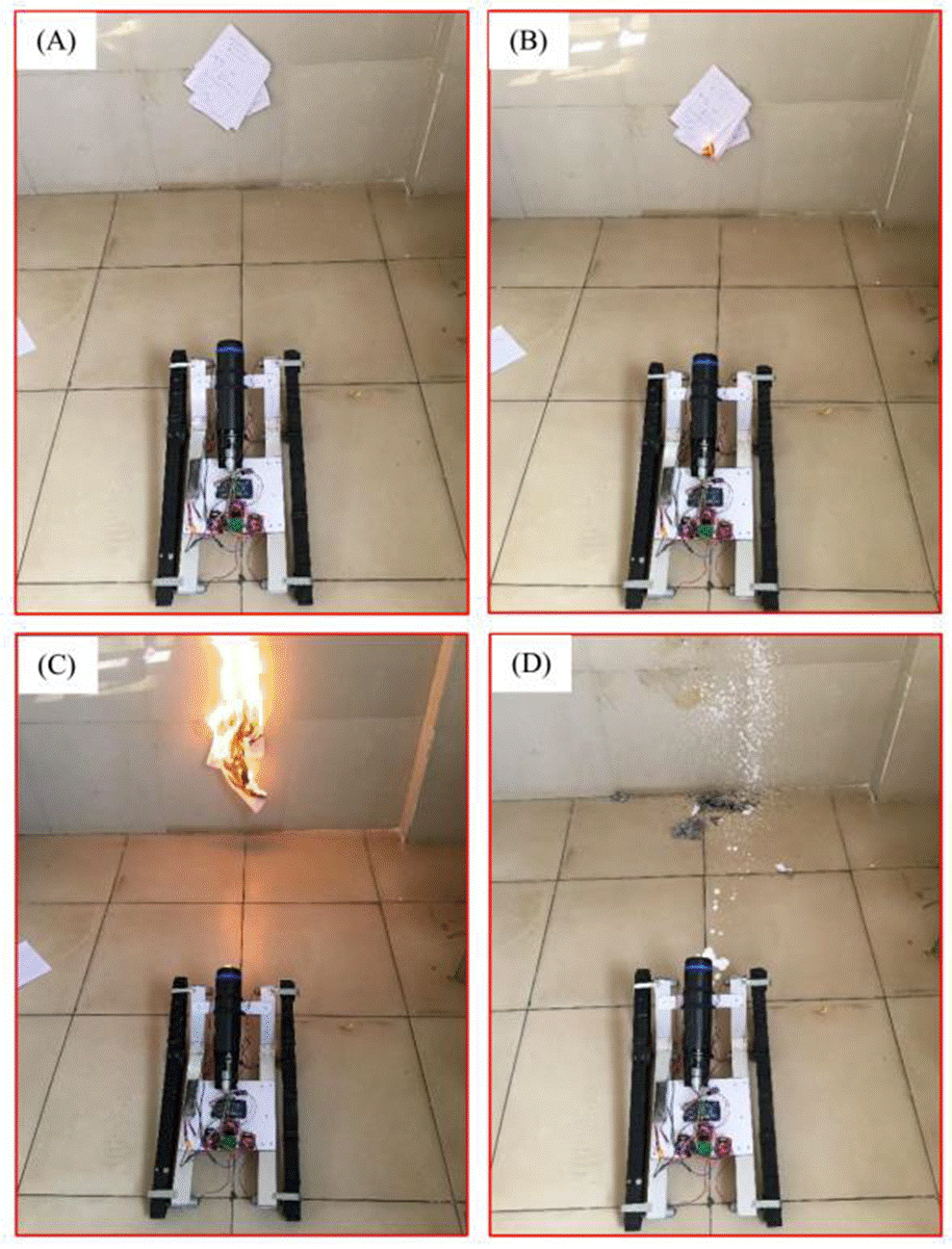
Figure 10 Snapshots of the experimental results of FER during fire extinguishing operations on the wall.
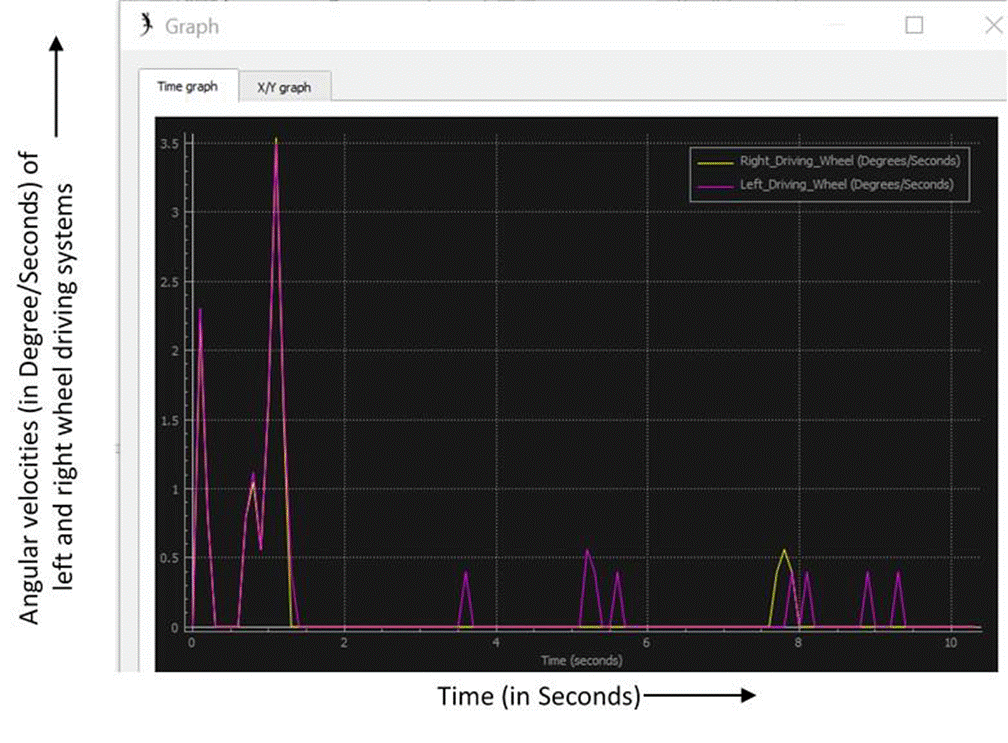
Figure 12 Real-time recorded angular velocities (in Degree/Second) of left and right wheel driving systems of FER during the stair climbing process in Figure 11.
5. Conclusion and future work
This article designs and presents the all-terrain differential- driven caterpillar-wheeled based unmanned Fire Extinguisher Robot (FER), which can detect, monitor, and extinguish the fire in any field. The motion, orientation, and the spreading of fire extinguisher gas in the fire have been controlled through the Bluetooth signal from an android phone (like a remote control). Further, the kinematic analysis of the unmanned FER has been done, and the motion controlling kinematic equations have been derived. Further, the current study also succinctly describes the two-dimensional (2D), three- dimensional (3D) SolidWorks models of the unmanned FER, a physical model of the FER, and its various components. Finally, real-time experimental results show that the developed FER has successfully protected the workspace from the fire by spreading the fire extinguisher gas through the nozzle of the cylinder. Furthermore, this unmanned FER can spread the fire extinguisher gas through the nozzle of the cylinder on the fire from a distance of 213.36 cm. This FER can be used in houses, offices, laboratories, industries, warehouses, railway stations, etc., to detect and control the fire. In the future, the vision sensors with the Wi-Fi module can be incorporated in the designed FER for video surveillance of the fire.