Highlights:
94.24 wt.% weight loss of shea waste shows its excellent insulating properties.
19.48 MJ/kg of clean energy capacity of shea waste determined
Low compaction technique of shaping bricks found useful for indoor construction.
Enviromental safe method of reusing waste for making ligthweigth bricks presented.
1. INTRODUCTION
An emerging trend in the clay brick construction industry, Consolidated by legislative enaetments in some jurisdictions (Chen, Zhang, Chen, Zhao & Bao, 2011; Kuusk, Kalamees & Maivel, 2014), is gravitating towards the manufacture of clay bricks incorporating waste materials.
The increasing popularity of waste incorporation into clay bricks manufacture could perhaps be attributed to the growing importance of sustainability (Kinuthia & Oti. 2012; Miqueleiz et al., 2012), environmental protection (Arsenovic, Radojevic, Jaksic & Pezo, 2015) and the need for affordable supply of essential commodities (Menezes. Ferreira, Neves, Lira & Ferreira, 2005; Zhang, 2013).Other main factors may include declining development in energy/electricity generation (Al-Hadhrami & Ahmad. 2009), conservation and efficient use of limited non-renewable natural resources (Quijorna, Goza, Andresa, & Cheeseman, 2012; Vinai, Lawane, Minane & Amadou, 2013) . In particular organic waste incorporation into clay brick matrices are noted to have; (1) excellent ecofriendly valorization potentials (Barbieri, Andreola, Lancellotti & Taurino, 2013), (2) efficient energy-saving capacities (Sutcu, José del Coz Díaz, Álvarez Rabanal, Gencel & Akkurt, 2014) and (3) outstanding thermal insulation properties (Muñoz, Morales, Mendívil, Juárez & Muñoz. 2014) . Thus, the issues of organic waste recycling in clay brick manufacture could créate new winning ways of solving the increasing environmental related waste problems while concurrently being used in developing economic and sustainable clay bricks with enhanced properties.
To this end, several organic residues have extensively been researched on (Barbieri et al., 2013; Bories. Borredon, Vedrenne & Vilarem, 2014; Raut, Ralegaonkar & Mandavgane, 2011) because of their varied enhancing effects on clay bricks. Some of these works include; use of recycled paper processing residue to improve the thermal conductivity of bricks (Sutcu & Akkurt, 2009), addition of olive mili solid residue for lightweight brick production (La Rubia-García, Yebra-Rodríguez, Eliche-Quesada, Corpas-Iglesias & Lopez-Galindo, 2012), manufacturing of porous bricks with rice husk addition (Górhan & Simsek, 2013) and development of better insulation bricks by adding mushroom compost waste (Velasco, Morales Ortíz, Mendívil Giró & Muñoz Velasco, 2014). Other notable works are; application of spent grains to improve porosity in bricks (Russ, Mórtel & Meyer-Pittroff, 2005), use of grasses as cheap supply of renewable production raw materials (Demir, 2008), recycling sugarcane bagasse ash as an alternative sustainable way of providing raw materials (Faria, Gurgel & Holanda 2012) and incorporation of organic residue as combustible fuel-containing materials (Monteiro & Vieira, 2014).
Considering the enormous potentialities of using organic residue to tailor clay bricks beneficially, spent shea waste (SSW) - a substantial industrial organic waste generated from shea butter processing, could possibly be utilized in the clay construction sector advantageously; though limited information exist regarding such an attempt hitherto. The shea tree [Vitellaria paradoxa (C.F. Gaertner); synonyms Butyrospermum paradoxurn (C.F. Gaertn.)], is an ecologically valuable resource that naturally flourishes as a wild plant in the predominant shea parklands in a geological formation popularly called the "Shea belt" as shown in Figure 1 (Adazabra, Viruthagiri & Ravisankar, 2016). Shea butter is recognized etS el multifunctional essential ingredient in the pharmaceuticals and traditional medicines conceivably because of its anti-inflammatory, anti-tumor-promoting effects and cáncer chemopreventive therapeutic valué (Akihisa et al., 2010; Akihisa et al., 2007). It is also widely used in cosmetics and beautification industries as a skin moisturizer (Lamien et al., 2006). In addition, shea butter finds suitable application in detergent industries because of its high fatty content (Rousseau, Gautier & Wardell. 2015). Most of all, recent amendments to the European Commission regulations permitting the use of substitutes for cocoa butter in the confectionery industries has altogether made available great Ímpetus for the widespread commercialization of the shea butter processing plants. Thus, the increasing stockpile of SSW is assuming alarming proportions.
The effective management of SSW is proving difficult than expected of a typical organic residue. The traditional method of disposing organic residue in farmlands to decay into manure (Demir, 2008) is being flawed with SSW because of its oily nature. The significant reduction of SSW vía open burning is essentially pointless with the increasing significance of the Kyoto protocol (Lau, Lee & Mohamed, 2012); besides, it is among the least desirable environmental disposal options. The excellent energy potential and relatively low carbón content of SSW (Nimmo, Daood & Gibbs, 2010; Woods et al, 2006) has attracted its minute exportation to United Kingdom for co-combustion in coal power plants; however, the converse is currently not true in the African sub-Saharan regions due to limited power infrastructural challenges. The excessive oozing out of CEL, gas to the atmosphere, with its associated long-term ravaging effect on the climate (Muñir, Nimmo & Gibbs, 2010), is a major constraint in reusing SSW for land reclamation purposes. Low admixing ratios of SSW inundates its viable use as animal and poultry feeds (Pousga, Boly, Lindberg & Ogle, 2007). Thus despite the internationally soaring demand for shea butter product, which ensure the huge corollary generation of SSW, at present an ecofriendly viable option of managing the voluminous SSW materials is still a mirage.
Yet, recent studies on the thermal characterization of SSW shows a large loss on ignition valué of 76 wt.% at 600 °C firing postulating its excellent pore forming capability (Adazabra et al., 2016). This research therefore cardinally seeks to leverage on the abundance of SSW for use in the manufacture of lightweight clay bricks with improved thermal insulation properties. In this regard, about 5, 10, 15 and 20 wt.% of brick making clay was replaced by equivalent weighed amount of SSW. The physical, chemical and thermal properties of the brick raw materials were characterized from mechanical, spectroscopic and thermal analysis. The technological properties including green density (G.D), percentage linear fired shrinkage (%L.F.S), fired density (F.D), cold compressive strength (CCS), water absorption coefficient percentage apparent porosity (%A.P) of the prepared brick samples were investigated. Variations in technological properties of the bricks due to differentials in firing temperaturas were compared to elucídate optimized condition of developing this type of bricks. Due attention was dedicated to ascertaining the porosity and insulation properties of the fired brick samples with SSW incorporation.
Consequently, via laboratory insightfulness, the present research is aimed at creating a new path of possibility on the synergistic incorporation of SSW in the manufacture of lightweight clay bricks with improved thermal insulation properties; besides achieving a potential environment friendly and economically viable disposal option.
2. MATERIALS AND METHODS
2.1 COLLECTION AND CHARACTERIZATION OF RAW MATERIALS
Brick making clay used in the present investigation was received from Government ceramic institute located in Virudachalam, a suburb of Cuddalore district, Tamil Nadu, India. The clay were pretreated to obtain high-grade industrial standard powder via drying at 100 °C for 6 hours in a rotating drier, crushed into powder in an industrial pulverizer and then sieved with a 150 (100 um) mesh size sieve. SSW, the main solid residue from shea butter processing, was acquired from Wakii in Tongo district (upper east región, Ghana, West Africa) as lumpy shea cakes. These shea cakes were manually controlled to suitable packaging size via pounding and sieving and then airlifted to Annamalai university spectroscopic laboratory situated in Chidambaram, Cuddalore district (Tamil Nadu state, India, South Asia).
At the laboratory, the spent shea powder was further subjected to preconditioning through mechanical ball milling, repetitive manual grounding and sieving through a 150 (100 µm) mesh size sieve until a homogeneous fine SSW powder was obtained. In this way, the partióle sizes (i.e. ≤ 100 µm) of SSW and the clay were mechanically characterized. Further, the thermal properties, chemical composition and mineral phases of the pristine SSW and clay materials were characterized from thermogravimetric differential thermal analysis (TG-DTA), X-ray fluorescence (XRF) and X-ray diffraction (XRD) studies, respectively. In addition, the organic composition and calorific valué of SSW were determined from ultímate analysis at an ignition temperature of 440 °C.
2.2 BRICK SAMPLES PREPARATION
Five unique compositional different brick mixtures were separately prepared using accurately weighed amounts of SSW to replace 5,10, 15 and 20 wt% of precisely measured quantities of the brick making clay according to the weighted shemes presented in Table 1. Each compositional different mixtures were homogenized in a laboratory mixer operated at 300rpm speed for 30 min. and sprinkled with 12.5wt% of plasticity water to humidify. The formed granulates were manually compacted into rectangular containers of interior dimensions 90mm x 35 mm x 30 mm to form the brick samples after applying a soaking time of 1 hour. Similarly, aliquot of each prepared granulates were pressed into cylindral containers with 120mm interior diameter and 10mm thickness. Towards improving the accuracy of the measurements, 16 rectangular brick samples were grouped into sets of fours called batches for firing at 900, 1000, 1100, and 1200 °C. Similar set of batches (i.e. each samples were prepared. For easy indentification, comparision and meaningful disscussions, all prepared bricks were named based on their mixtures as BC-SW0: reference standard bricks; BC-SW5: 95 wt.% clay +5 wt.%SSW; BC-SW15,: 90 wt.% clay +10 wt.%SSW; BC-SW15: 85 wt.% clay +15 wt.%SSW and BC-SW20 , : 80 wt.% clay +20 wt.%SSW. Where BC is brick making clay and SW refers to shea waste. The weighted percentage incorporation level of SW was indicated in the superscript. Further, the prepared brick batches were named as Batch 1, 2, 3 and 4 based on their sintering schedules as indicated in Table 1. All the brick batches were subjected to consecutive open sun drying for a week from which their dimensions were recorded with calipers of least count 0.01 mm. Further, the dried weights of the rectangular samples were determined using a high precisión digital balance (least readings ± 0.01 g). The dried bricks were then sintered in an electric kiln operating in a 24 - hour heating cycle applying a heating rate of 2 °C/min. At each reached required sintering temperature, firing was maintained for a minimum time of 2 hours so that the bricks could gain better mechanical strength before turning the kiln off to cool to ambient temperatures.
Table 1 Weighed admixing ratios of brick mixtures and their firing schedules.
Brick Mixtures | Wheighed amounts of (wt%) brick materials | Number of Replicates | Firing Schedules | |||||
---|---|---|---|---|---|---|---|---|
Brick Clay | SSW | Rectangular | Cylindrical | Batch 1 900 °C | Batch 2 1000 °C | Batch 3 1100 °C | Batch 4 1200 °C | |
BC-SW0 | 100 | 0 | 16 | 12 | BC-SW0 | BC-SW0 | BC-SW0 | BC-SW0 |
BC-SW5 | 70 | 5 | 16 | 12 | BC-SW5 | BC-SW5 | BC-SW5 | BC-SW5 |
BC-SW10 | 65 | 10 | 16 | 12 | BC-SW10 | BC-SW10 | BC-SW10 | BC-SW10 |
BC-SW15 | 60 | 15 | 16 | 12 | BC-SW15 | BC-SW15 | BC-SW15 | BC-SW15 |
BC-SW20 | 55 | 20 | 16 | 12 | BC-SW20 | BC-SW20 | BC-SW20 | BC-SW20 |
2.3 CHARACTERIZATION OF BRICK SAMPLES
The green densities of the dried rectangular brick samples, %L.F.S, and F.D valúes of the fired rectangular brick samples were evaluated prior to sintering and after sintering following the EN 772-16 standard procedure (EN 772-16, 2011). With this procedure, the green weights and dimensions of the dried rectangular brick samples were evaluated using a sensitive digital balance (detection limits ±0.01 g) and venier calipers of least readings 0.01 mm. In the same way, the F.D valúes of the fired rectangular brick samples were ascertained. The %L.F.S valúes of the fired rectangular brick samples were determined with reference to their dried dimensional data. All measurements were determined in quadruplicates and standardized using equations (1), (2) and (3), respectively.
Where N is number of measurements,
W d.i and V d.i represent the weight (g) and volumen
(cm3) of rectangular brick before
firing, respectively,
W f.i and V fj are the weight (g) and volume (cm3) of
rectangular brick after firing,
respectively,
L d.i and l m,i denote the length (cm) of dried
rectangular brick and the length (cm)
of rectangular container, respectively.
Prior to water absorption coefficient (Aw) determination, the replicates of each fired unique brick composition were oven-dried at 100 °C until constant dry weights (W dry,i ) were recorded. These replicates were then wetted at varying time (t) and weighed (W damped ) from which the water absorbed were expressed per unit surface área (A) using equation (4).
Where W damped , W dry are measured in grams, W m is amount of moisture per unit surface área and A is measured in cm2
The Aw values of each unique compositional brick sample was then obtained from graphical plot of equation (5) .
Where
is expressed in terms of hours.
In line with ASTM standard C373-88 (ASTM C373-88, 1998), water absorptions and apparent porosities of the fired rectangular brick samples were assayed using the water displacement method. The varying wet samples were then totally immerse in a water bath for 24 hours from which their new wet weights (W wet , i ) were measured. Further, these wet bricks were boiled continuously in a hot water system for 6 hours after which their respective suspended weights (W supended, i ) were determined with samples submerged in water and saturated weights (W saturated, i ) evaluated out of water. The data obtained from the various quadruplicate (N) measurements was then used to calcúlate %W.A and %A.P applying equation (6) and (7), respectively.
The TS EN 772-1 standard (TS EN 772-1, 2002) was applied to determine the cold compressive strengths of the fired rectangular brick samples using a 94100 modeled UNITEK compressor. The test rectangular brick samples were horizontally positioned along their widths and a localized unit forcé of less than 1 Mpa/s was slowly applied on the upper surface until total breakage occurred. Recording the breakage pressure and then noting the dimensions of the bricks, the average cold compressive strength valúes from quadruplicate measurements were evaluated using equation (8).
2.4 PORES EVALUATION AND THERMAL CONDUCTIVITY TEST
As a way of elucidating the effect of firing on the porosity of the SSW incorporated bricks, the SEM micrographs of freshly fractured BC-SW15 brick specimens with dimensions less than 4 mm x 4 mm x 1 mm were examined using a JEOL JSM 6610 LV SEM instrument (secondary mode, working voltage of of 15 kV). Each different sintered specimen was stubbed to the specimen holder with a double-sided adhesive carbón tape and coated with a thin layer of platinum. The specimens were coated using a JEOL IFC-1600 Auto Fine platinum coater applying a current of 20 mA for 120 seconds. The micrographs revealing the nature of pores developed in the fractured surfaces were then recorded at 10 pm resolutions.
The Lee's disc method of evaluating the thermal conductivity (T.C) of an insulator was applied to determine the T.C valúes of the fired cylindrical brick samples. The fired cylindrical brick samples were machined to precise diameters comparable to the Lee's disc from which their respective thicknesses were ascertained using a micrometer screw gauge and diameters measured with venier calipers. The cooling rate, difference in temperature between steady chamber and steam chamber were ascertained, secondary data form the Lee's apparatus and the dimensional parameters of the cylindrical disc were used to evalúate the T.C. valúes as presented in equation (9).
Where M, S, r, h, d and ϑ
2
are the mass (kg), specific heat capacity [(J/(kg.K)], radius (m),
thickness (m) of metallic disc, d is thickness of insulating material (m) and
steady temperature of the Lee's disc (m), respectively. - is
3. RESULTS AND DISCUSSION
3.1 CHARACTERIZATION OF BRICK STARTING MATERIALS
Table 2 presents the chemical compositions of the clay material and SSW from XRF analysis. As evident in Table 2, A1203 (27.10 wt.%) and Si02 (52.97 wt.%) mainly constituted the clay material with minor concentration of CaO (5.32 wt.%), Fe203 (0.38 wt.%), BaO (0.10 wt.%), MgO (0.09 wt.%) and trace amount of MnO (0.02 wt.%). The recorded 27.10 wt.% of AI2O3 shows the excellent quality-index of the clay material (Muñoz Velasco. Morales Ortíz, Mendívil Giró & Muñoz Velasco, 2014). The dominant concentration levéis of SÍO2, is characteristic of clay materials as reported in literature (Eliche-Quesada, Iglesias-Godino, Pérez- Villarejo & Corpas-Iglesias, 2014 ; Nirmala & Viruthagiri, 2015). Si02, reacts with A1203 to form mullite at higher sintering temperatures, which is responsible for mechanical strength of fired brick. Oxides of MnO, BaO and MgO are noted for their fluxing abilities (Caldas, Moráis, Monteiro & Vieira, 2012; Sena da Fonseca, Galhano & Seixas 2015).
Table 2 Chemical analysis of brick making clay and spent shea waste presentad in wt.% unless stated otherwise.
Oxides | Brick making clay (BC) | SSW |
---|---|---|
A1203 | 31.74 | 0.37 |
BaO | 0.11 | 51.87 (µg/g) |
CaO | 5.32 | 0.36 |
CdO | - | 1.35 (µg/g) |
Cr203 | - | 7.06 (µg/g) |
Fe203 | 0.45 | 0.07 |
K20 | - | 2.11 |
MgO | 0.10 | 0.10 |
MnO | 0.02 | 30.81 (µg/g) |
NiO | - | 9.60 (µg/g) |
PbO | - | 38.50 (µg/g) |
Si02 | 62.15 | 0.35 |
Ti02 | - | 0.01 |
V2Os | - | 18.72 (µg/g) |
ZnO | 0.01 | 174.19 (µg/g) |
SSW showed relatively low oxides amounts of K20 (2.11 wt.%), A1203 (0.37 wt.%), CaO (0.36 wt.%), Si02 (0.35 wt.%), MgO (0.10 wt.%) and Fe2O3(0.07 wt.%). The rest of the oxides were determined in traces as indicated in Table 2. The relative low elemental concentrations and peculiar dominance of K20 in SSW is characteristic of an organic material (Datta, Chowdhury, Verma & Reddy. 2011). The myriad presence of inorganic elements in SSW indicate its excellent diversity of fluxing agents. Fluxes are responsible for the formation of glassy phases at relatively lower sintering temperatures (Monteiro & Vieira, 2014; Kadir & Mohajerani, 2015). An important valué of incorporating SSW into clay materials could therefore be attributed to their fluxing properties.
Excessive amounts of Fe203 causes efflorescence and undesirable formation of "black core" or "black nucleus" under oxygen-deficient firing conditions. Therefore, recommended limits of Fe203 is not more than 10 wt.% (Muñoz Velasco et al., 2014). Similarly, 10 wt.% is the recommended limits of CaO; perhaps because of their possible role in crack formation from the absorption of moisture. As observed in Table 2, the concentrations of Fe203 in the clay material as well as SSW and CaO in both starting materials were well within recommended limits. These observations therefore suggest the potential suitability of the brick starting materials for used in structural construction application due to their complimentary chemical compositions.
Further, the organic content and henee estimated calorific value as energy-contribution capability of SSW was determined from ultímate analysis as presented in Table 3. As can be seen in Table 3, the 95.19 wt.% CHNO total concentration of SSW authenticated its low oxide content from XRF analysis (Table 2). Estimating its calorific value using Channiwala and Parikh (2002) relation (equation (10)) indicates an energy content of 19.48 MJ/kg.
Where A is the ash content, and S = 0.
Table 3 Organic compositional analysis of spent shea waste determined in wt.% and its estimated calorific value (MJ/kg).
Calorific Valuea | C | H | N | S | Ob | Moisture | Ash |
19.48 | 47.95 | 5.83 | 3.17 | *ND | 38.24 | 0.29 | 4.52 |
aEstimated by applying Channiwala and Parikh (2002) relation
*ND=Not Detected, bComputed on weight déficit
The non-detection of sulphur (S) in SSW suggest its combustión is an environmental friendly process since sulphur-containing materials are more prone to releasing substantial amounts of the deleterious acid rain forming sulphur dioxide gas. These analysis imply that about 19.48 MJ/kg of clean energy could possibly be made available for use in meeting the sintering energy requires of fired clay bricks incorporating SSW. Thus, enormous savings of energy via the incorportion of SSW in brick matrices. Analysis of the energy-contribution potentials of other organic residue show similar magnitude of calorific valúes as reported in cited literature (Parthasarathy, Sheeba & Arockiam, 2013; Velasco, Ortiz, Giró, Melia & Rehbein. 2015).
The XRD patterns of the brick mixtures are shown in Figure 2. As clearly shown in Figure 2, the brick mixtures exhibited similar diffraction patterns in terms of their diffraction angles as well as intensities. This observation suggest any of the brick mixtures incorporating SSW could suitably be assigned for the manufacture of structural construction clay bricks without significant changes to the bricks mineralogical content. This observation purports that significant quantities of SSW could synergistically be utilize in brick making without adverse effect on the mineralogical composition of the bricks formed. Analysis of the diffraction peaks commonly reveal the presence of quartz (SÍO2, Card No. 81 - 1665), kaolinite (Al2Si208(OH)4, Card No. 83 - 0971) and calcite (CaCOs, Card No. 86 - 2339). The rest are hematite (Fe203, Card No. 89 - 8104) and goethite (FeO(OH), Card No. 81 -0464). The identification of these minerals is in agreement with the chemical compositions of the brick mixtures (Table 2). Other researchers reported similar minerals content in brick raw materials (Manoharan, Sutharsan, Dhanapandian & Venkatachalapathy, 2012; Nirmala & Viruthagiri, 2014). For short, the XRD studies of the brick mixtures support the substantial replacement of clay materials with SSW for various varied purposes including sustainable production route, a disposal method and beneficial enhancement of bricks technological properties.
The TG - DTA thermograms of SSW are shown in Figure 3. As illustrated in Figure 3, the TG curve of SSW reveal a prominent two-step decomposition process. The observed initial 10.94 wt.% weight loss oceurring around the 60 - 165 °C range, which corresponds to an endothermic peak at 110 °C represent the evaporation of moisture content in the SSW. The final 83.30 wt.% weight loss recorded in the broad 165 - 750 °C reaction range that matches with the single excessive wide exothermic peak at 800 °C, shows the collective decompositions of cellulose, proteins, hemicellulose, triacylglycerols and lignin components in SSW (Darvell et al., 2010; Adazabra et al.. 2016). Of significant importance to the incorporation of SSW into clay material for insulation fired brick making is the massive total weight loss of 94.24 wt.%, which reveáis its excellent pore forming abilities as portrayed in Figure 3. The recorded 94.24 wt.% weight loss of SSW was a good match to its 95.15 wt.% organic content from ultímate analysis (Table 3). Analysis of similar organic waste such as sawdust, grape seeds and cherrie seeds show similar range of weight loss as reported by Barbieri et al. (2013).
Figure 4 shows the TG-DTA curves of the brick making clay material. As shown in Figure 4, the clay material thermograms present slight inflexions at 237 and 327 °C, sharp peaks at 554 and 969 °C and a total weight loss of 16.08 wt.%. The 1.01 wt.% weight loss given rise to the exothermic peak at 237 °C represent the decomposition of organic content in the clay material. Organic matter are known to impart good moulding abilities and plasticity properties to clays conceivably due to their high specific surfaces (Sócrates, 2001; Manoharan et al., 2012). The 1.01 wt.% determination of the organic content in the clay material used in this research is therefore in consonance with their excellent plasticity properties. The endothermic peak observed at 327 °C corresponding to a bare change in weight of the clay material specifies the hydroxylation of goethite into hematite (Manoharan et al., 2012).
The markedly 15.07 wt.% weight loss conforming to the sharp endothermic peak occurring in the 487 - 606 °C reaction range, is attributed to the transformation of kaolinite into metakaolin via dehydroxylation (Ptácek. Soukal, Opravil, Havlica & Brandstetr, 2011; Ptácek. Frajkorová, Soukal & Opravil, 2014). The recorded high weight loss tentatively indicate the abundance of kaolinite minerals in the clay materials. Earlier researchers observed similar magnitude of weight loss on the thermal analysis of kaolinitic clays (Teixeira, Souza & Moura, 2001: Teixeira et al., 2011). The exothermic peak at 969 °C indicate mullitization reactions due to the structural transformation of metakaolinite into mullite (Zhou, Qiao & Yu, 2013). In a way, the thermal analysis of the clay material complements the spectroscopic analytical methods. Overall, the instrumental characterization of the brick starting materials revealed their suitability for use in structural construction application. The incorporation of SSW into the clay materials had showed promising beneficial results of enhancing the fluxing content of the starting materials as well as ensuring economic sintering process.
3.2 EVALUATION OF BRICKS TECHNOLOGICAL PROPERTIES
The technological properties such as green density, fired shrinkage, fired density, mechanical resistance, water absorption and apparent porosity of a brick is a cardinal determining factor for use in construction works aside its raw material composition, sintering temperature and manufacturing methodology (Karaman & Esmeray, 2006; Tudisca et al., 2011). The green densities of the dried rectangular brick samples are shown in Figure 5. The relative low specific gravity of SSW was demonstrated via the significant reduction in green densities from the reference standard bricks at its higher incorporation levéis. As depicted in Figure 5, the G.D valúes decreased from an average valué of 1.66 g/cm3 in the reference standard bricks to around 1.42 g/cm3 in BC - SW20 brick samples. The lightening effect manifested on the bricks weights could plausibly to linked to the replacement of the clay material with SSW. Similar lightening phenomena have been established in literature on the incorporation of organic additive into clay brick matrices (Eliche-Quesada et al., 2011; Muñoz, Juárez, Morales, & Mendívil, 2013). Henee, the decreasing trend in green densities permit to theorize the development of lightweight bricks via SSW incorporation.
Optimizing the extent of contractions or expansions within fired brick matrices is a critical quality-determining factor because extensive dimensional changes could créate tensión or complete structural failure. The %L.F.S is a convenient measure of the extent of contraction or expansión of a fired brick product (Xu, Yann, Xu, Rúan & Wei, 2014). It is also most relevant in the specification of the physical dimensions of fired bricks. Figure 6 exhibit the %L.F.S valúes of the fired rectangular brick samples as a function of their firing temperatures. The less than 4.0 % shrinkage valúes of brick fired at 900 °C could primarily be attributed to SSW decomposition. The higher %L.F.S valúes (i.e. mostly > 6.0%) recorded above 900 °C sintering suggest the dominance of vitrification reactions. Thus, sintering temperature is a major determining factor of fired shrinkage aside SSW burn out. Compared to literature valúes, the obtained %L.F.S valúes in the present study were high (Eliche-Quesada et al., 2012: Sutcu & Akkurt, 2009). Nevertheless, quality bricks are known to exhibit shrinkage valúes below 8% (Shih, Wu & Chiang, 2004; Yang, Cui, Qin & Cui, 2014). As shown in Figure 6, all brick samples showed shrinkage valúes within expected standard requirements.
Another important physical characteristic of a sintered brick is its fired density (Bories et al., 2014; Weng, Lin, & Chiang, 2003). Figure 7 displays the fired densities of the brick samples as a function of SSW incorporation content. As shown in Figure 7, bricks fired at 1200 °C decreased from 2.02 g/cm3 in the reference standard bricks to 1.58 g/cm3 at increasing SSW incorporation content. Bricks fired between 1000 and 1100 °C showed marked similarities in fired densities as their densities together varied from 1.80 g/cm3 in the reference standard bricks to about 1.44 g/cm3at 20 wt.% incorporation of SSW. Bricks fired at 900 °C consistently exhibited lower fired densities. Bories et al. (2014) opined that incorporation of pore-forming agents into brick matrices decrease their fired densities due to the burn out of these agents during the manufacturing process.
The observed decease in fired densities at the various sintering temperatures could therefore most probably be due to the burn out of the SSW content in the brick matrices. The differentials in fired densities among the differently sintered bricks could be credited to the preferred transformation of the clay materials at those sintering temperatures. The striking similarities in fired densities observed between the 1000 and 1100 °C fired bricks suggest the occurrence of similar phase transformation reactions in the 1000 - 1100 °C temperature range. According to Weng et al., (2003) recommended fired density of a conventional brick range between 1.8 and 2 g/cm3. In this context, bricks fired at 900 °C are of low quality due to their indicated 1.6 geni3 valué of reference standard bricks. Reference standard bricks fired at 1000 - 1100 °C met recommended standard requirements indicating their good quality. The decrease in fired densities of the 1000 - 1200 °C fired bricks below 1.8 g/cm3 at increasing SSW incorporation content therefore permit to classify these category of bricks as being lightweight.
A measure of the sorption capability of a construction material is essential (Szodrai & kos Lakatos, 2017). Water absorption coefficient, which is an established critical performance parameter, expresses the sorptivity of a construction material (Sicakova, Draganovska & Kovac. 2017). Figure 8 shows a trend of water absorption coefficient of rectangular brick batches with increasing SSW incorporation ratio. The brick Aw valúes obtained in this research are comparable to other construction materials reported in current published literature (Sicakova et al., 2017). As can be inferred from Figure 8, brick batches sintered at 900 °C showed consistently high Aw valúes relative to those fired at 1000 - 1200 °C. These results speculate that bricks sintered at 900 °C develop much larger specific external surfaces than similar samples sintered at higher temperatures (Szodrai & kos Lakatos, 2017). The comparable Aw valúes among the 1000 and 1100 °C fired brick samples imply similar pore circuitry within their matrices. Low pore circuitry within bricks sintered at 1200 °C could plausibly account for the marginal Aw valúes obtained. The slight increase in Aw valúes among the brick batches could be linked to increased pore creation from SSW burnout.
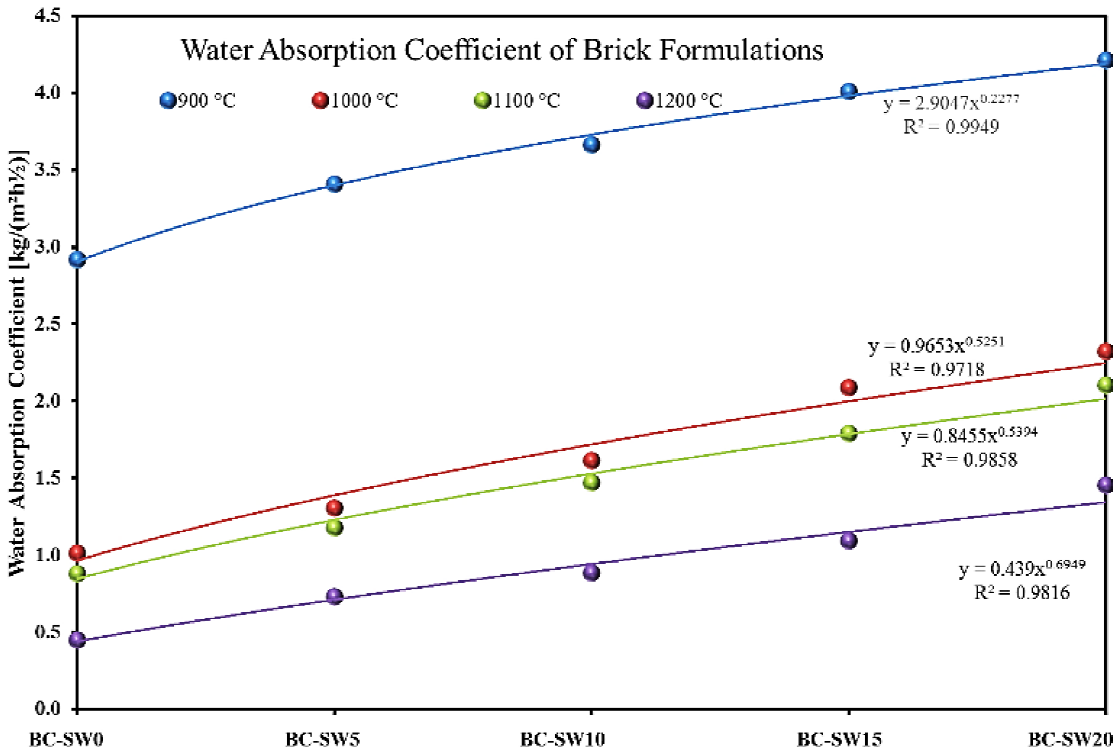
Fig. 8 A graph showing water absorption coefficient values of brick formulations at increasing spent shea waste addition.
Intrusión of water into brick matrices could cause expansions, contraction, efflorescence and other undesirable natural degrading conditions. Thus, the resistance of a construction material to these degrading conditions are linked to their water absorptions.
Recommended %W.A valúes of quality brick units is 20 wt.%; the lesser the better (Yang et al., 2014). The %W.A valúes of the fired rectangular bricks are presented in Figure 9. Similar range of %W.A were reported in literature on the addition of waste materials to brick matrices (Bilgin et al., 2012). As expected, it can be seen in Figure 9, that bricks samples fired at 900 °C show high %W.A valúes compared to those sintered at 1000 - 1200 °C. Thus, %W.A valúes of the brick samples correlate well with their Aw valúes. However, the 900 °C sintered bricks which showed %W.A valúes above 20 wt.%, indicate their low quality. In this regard, bricks fired at 1200 °C temperature depicted highest quality standard. Nevertheless, considering economic manufacturing process, brick samples fired at 1000 °C temperatures were the most optimized manufacturing condition in terms of meeting quality standards as well as minimal energy requirements for firing.
The extent of porousness of the fired brick samples can be ascertained for %A.P test. Sutcu and Akkurt, (2009), demonstrated that an increase in apparent porosity corollary necessitate an increase in their thermal insulation properties. Figure 10 illustrates the %A.P valúes of the fired brick samples as function of firing temperature. It is evident from Figure 10 that %A.P valúes of the brick samples decreases as the firing temperature increases. The extent of decrease in %A.P valúes at increasing firing temperature were found to obey an empirical first order power series as indicated in Figure 10. However, for each fired temperature, it can be seen that %A.P valúes increase as SSW incorporation amounts increase. Thus, bricks fired at 900 °C showed highest %A.P valúes. The converse is true for the 1200 °C fired brick samples. The overall high %A.P valúes observed in the SSW incorporated brick samples tentatively suggest their improved thermal insulation properties.
In addition to durability, economical low cost, mínimum maintenance requirements and environmentally safe usage, an indispensable engineering-quality deciding factor for use of bricks in construction works is based on their cold compressive strengths. The obtained CCS valúes of the brick samples from compressive strength test are expressed in Figure 11. Perusing Figure 11 shows that the obtained CCS were moderately low relative to reported literature valúes (Benk & Coban, 2012; Sutcu, Alptekin. Erdogmus, Er & Gencel, 2015). Nevertheless, the CCS valúes of the brick compare favourably to those obtained by earlier researchers (TS 705, 1985; Górhan & Simsek. 2013; Xu et al., 2014). For use of vertical perforated bricks in construction, a minimum compressive strength valué of 5 Mpa is required (TS EN771-1, 2005). In the case of horizontal perforated bricks, a recommended range of 2.5 - 7.5 Mpa is mandatory for use of such bricks in construction (TS EN771-1, 2005). In addition, non-load bearing bricks used for indoor structural construction should maintain a minimum valué of 5 Mpa as their compressive strength valúes (TS EN 772-1, 2002). Observation of Figure 11 shows that almost all brick samples met the minimum standard requirements for use in construction works.
The characteristic low CCS valúes obtained in this research could reasonably be linked to low compaction technique used in manufacturing the brick samples. Muntohar, (2011) asserted that clay brick making might be of interest to professionals working in developing countries. This could perhaps be due to the use of clay bricks as main constructional materials in these countries. However, as exemplified in Figure 12 (Custodio-García et al., 2005), the manual low compaction technique, which generally lack the sophistication and automation of industrial high compaction systems, is often adopted to press-shape brick units in these countries. In the context of simulating the low compaction technique in the laboratory, the method adopted in this research is justified.
3.3 THERMAL PROPERTIES AND POROSITY OF BRICK SAMPLES
Microscopio porosity formed by gas bubbles and thermal conductivity of a brick sample are vitally important parameters that determine the net heat transmission and henee the required thermal comfort level of a brick structural envelope (Muñoz et al., 2013). The nature of pores created via the addition of SSW were studied at increasing firing temperature via SEM micrographs. Figure 13(a)-(d) present the SEM micrographs of BC-SW15 fired at 900, 1000, 1100 and 1200 °C, respectively as modeled samples of the SSW incorporated brick samples. Figure 13(a) reveáis meshy microstructures of individual clay grains due to the formation of numerous micro pores from the burn out of SSW. The microstructures presented Figure 13(b) shows partly connected clay grains with reduced micro pores probably attributed to the formation of glassy phases. The dominance of glassy phases conceivably linked to pronounce vitrification of the clay materials with limited number of micro pores are well demonstrated in the microstructures shown in Figure 13(c) . The plate-like microstructures perforated by secondary porosity tentatively provide clues on the formation of the mullite phases. Thus, number of micro pores decreases at increasing firing temperature.
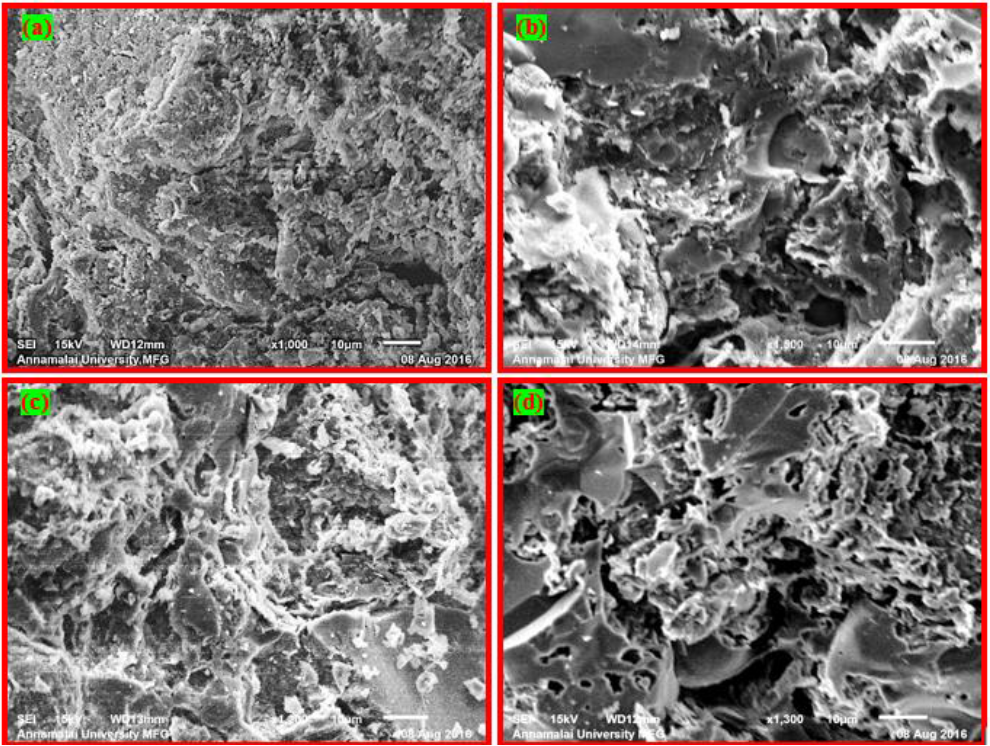
Fig. 13 Electron micrographs showing BC-SW15 brick microstructures fired at (a) 900 (b) 1000 (c)1100 and (d) 1200 °C.
Nowadays, the quest to achieve zero-energy building may be attained via use of bricks with excellent thermal properties (Laaroussi, Lauriat, Garoum, Cherki, & Jannot. 2014). Figure 14 shows the T.C valúes of the 900-1200 °C fired cylindrical brick samples as a function of their SSW incorporation content. As depicted in Figure 14, the 900 °C fired bricks showed T.C valúes ranging from 0.36 - 0.21 W/(mK). The 1000-1200 °C fired reference standard bricks recorded T.C valúes of 0.49 and 0.60 W/(mK), respectively. It is thus, evident that the low T.C valúes of the 900 °C sintered brick samples correlate to their porous nature. The converse is true for bricks sintered at 1200 °C. Henee, it can be inferred that incorporation of degradable materials into brick matrices increase their insulation abilities (Arsenovic et al., 2015). The observed decrease in T.C valúes at increasing SSW incorporation content in the brick matrices is in line with Arsenovic et al. 2015 assertion. In general, T.C valué of a conventional brick unit may be 1.0 ± 0.4 W/(mK) depending or raw materials and manufacturing methodology (Garcia Ten. Orts, Saburit & Silva, 2010; Sutcu, 2015). The observed decrease in T.C valúes of the SSW incorporated brick samples therefore proposes their improved thermal insulation properties.
Overall, in terms of economic manufacturing and meeting quality standard specifications, the 1000 °C fired BC-SW15 brick samples are considered the most optimized manufacturing conditions. These bricks portrayed an average green density of 1.47 g/cm3, 13.82 wt.% reduction in fired density and 7.40 % fired shrinkage. The rest are CCS valué of 6 Mpa, %W.A of 15.95 %, A.P% of 38.31% and T.C valué of 0.33 W/(mK). Thus, the incorporation of SSW into the clay brick matrices resulted in the manufacture of lightweight bricks with improved thermal insulation properties.
4. CONCLUSION
The extensive instrumental characterization of brick making clay and SSW shows that incorporation of SSW into clay materials had no practical influence on the chemical compositions, mineralogical content or thermal behavior of the fired brick samples thereby authenticating the suitability of the raw materials for use in structural construction application. SSW incorporation showed enormous potentials of enhancing the fluxing content. The 19.48 MJ/kg calorific valué of SSW indicated its excellent energy-contribution during firing. Admixing SSW in brick samples significantly reduced their green densities from 1.66 g/cm3 to 1.42 g/cm3 indicating their lightening effect. Fired shrinkages and densities, water absorption coefficients, water absorptions, apparent porosity as well as cold compressive strengths were influenced by the incorporation of SSW and firing temperature. Porosity and thermal conductivity properties of the brick samples beneficially improved by the incorporation of SSW into the brick matrices. Overall, BC-SW15 showed excellent properties in terms of meetings constructional standard requirements as well as a 58.06% decrease in thermal conductivity valúes signifying their improved thermal insulation properties. Consequently, a convincing way of potentially consuming large amounts of SSW for the manufacture of lightweight bricks with improved thermal insulation properties has been provided in the present research.
CONFLICT OF INTEREST
The authors have no conflicts of interest to declare.