1. Introducción
El Bioetanol se ha convertido en uno de los energéticos atractivos para algunos centros de investigación y para ser producido en la industria porque proviene de materia prima biológica renovable, no corrosivo, ni tóxico y mejora el desempeño de la gasolina al ser usado como aditivo oxigenante o combustible en vehículos [27]. Sin embargo para que el etanol pueda ser utilizado como carburante es necesario que su contenido de agua sea muy bajo, con el fin de evitar la formación de dos fases liquidas en la mezcla.
Para lograr una purificación más allá del punto azeotrópico, existen técnicas de destilación como la azeotrópica, extractiva, extractiva con sales y/o solvente, reactiva, de difusión y al vacío [27, 14, 8, 28]. Otras tecnologías aplican los principios de adsorción y permeación que necesitan la utilización de materiales especiales como como agentes de separación, por ejemplo, las zeolitas (tamices moleculares para adsorción) y las membranas de pervaporación [1, 7, 17].
La adsorción con tamices moleculares por oscilaciones en presión o PSA ha desplazado las principales técnicas industriales de destilación que han sido usadas para deshidratar etanol (destilación azeotrópica y extractiva), debido principalmente a que el proceso PSA alcanza un alto grado de pureza (99.5% en peso) con costos de operación y consumos energéticos bajos, comparados con los otros procesos industriales, como es el caso de la destilación azeotrópica heterogénea. Otra ventaja del proceso PSA es que el producto obtenido no contiene trazas del agente de separación y no requiere uso de solventes tóxicos. En este proceso ocurren simultáneamente fenómenos térmicos, termodinámicos, cinéticos y difusivos. además, es un proceso cíclico que necesita la configuración de varias etapas y/o pasos; es decir, opera en un estado pseudo-estacionario.
La tarea de configurar los diferentes pasos o etapas es difícil, implica definir la duración, condiciones de operación, etc. en cada uno de ellos. En cuanto al modelado de este proceso, este implica la consideración de variaciones temporales y espaciales en diferentes variables, por su carácter cíclico necesita la definición de condiciones iniciales y de frontera para los diferentes pasos o etapas. Hay diferentes variables con efecto sobre la pureza del producto y por lo tanto existen diferentes posibilidades de abordar el problema de control.
En la literatura se proponen diferentes variables para controlar la composición (pureza) en procesos PSA. Algunas posibles entradas de control pueden ser: presión, temperatura, fracción molar, tiempo del paso de adsorción o purga, tiempo ciclo completo.
Para el control de composición o pureza del producto, en [1], por ejemplo, se propuso un modelo con estructura Hammerstein que incluye dos partes; un modelo no lineal (estático) que no considera la dinámica cíclica del proceso y un modelo lineal tipo 'wavelet' que considera la dinámica del proceso. El modelo Hammerstein fue usado para diseñar el control; en particular, un control de seguimiento de trayectoria de la composición y para asegurar la trayectoria deseada en presencia de perturbaciones utilizaron un control secundario (por retroalimentación).
Otros trabajos sobre el control PSA para diferentes aplicaciones se presentan en [25, 18], en general estos recurren a controladores tipo PID, pero también es común encontrar la aplicación de técnicas de control robusto y predictivo [11]. De acuerdo con la literatura revisada, algunos de los controladores propuestos parecen ser adecuados para estos sistemas dinámicos complejos, ya que permiten mantener la pureza del producto y ante cambios, obtener la pureza deseada en pocos ciclos de adsorción/desorción [22, 28, 12, 19, 4].
Hay poca información sobre el control de procesos PSA y escasos estudios sobre el control de procesos para separar la mezcla etanol-agua; sin embargo, la información encontrada sirvió de base para el desarrollo de este trabajo.
El presente trabajo tiene como objetivo principal desarrollar un simulador (planta virtual) que considere los principales fenómenos que caracterizan el sistema, y que pueda generar los perfiles de concentración, temperatura y presión a lo largo de dos columnas empacadas con zeolitas, en todas las etapas configuradas para ciclos de adsorción-desorción. La idea es reproducir el comportamiento dinámico y la interacción entre variables de manera realista con el fin de poder diseñar y evaluar de manera eficaz el Controlador Predictivo (Óptimo para el proceso PSA que produce bioetanol al 99%. El simulador sirve entonces, como plataforma para analizar la dinámica del proceso, diseñar y evaluar el rendimiento del control de composición de etanol anhidro.
En este trabajo se demuestra que es posible mantener la pureza deseada, cumpliendo en todo momento los estándares internacionales de calidad del etanol carburante, gracias a la atenuación, por control de perturbaciones (cambios de concentración, temperatura de alimentación, tiempo de purga) que afectan al proceso PSA aun cuando el sistema es altamente no lineal, que involucra diferentes pasos y opera en régimen pseudo-estacionario.
El documento se organiza de la siguiente manera: en la sección 2 se presenta el modelo matemático (Modelo riguroso PSA) utilizado para simular el proceso PSA, el cual fue generado mediante el programa Aspen Adsim. En la sección 3 se establece el modelo reducido identificado (Hamerstein-Wiener) que es capaz de capturar las dinámicas importantes del modelo riguroso PSA, este modelo se utilizó para diseñar del Controlador Predictivo (Óptimo. En la sección 4 se presentan los resultados obtenidos al implementar y validar la robustez del controlador Predictivo utilizado como planta el modelo riguroso PSA. Finalmente, la sección 5 contiene las conclusiones del presente trabajo.
2. Configuración del modelo PSA
La primera decisión en el proceso de configuración del proceso es la selección del adsorbente. Para deshidratar etanol se consideró el uso de zeolitas tipo 3A, son esferas de 1 a 2 mm (Figura 1). Este puede soportar la adsorción de agua hasta en un 22 % de su propio peso, presenta una atracción mayor sobre las moléculas de agua, capacidad elevada de regeneración, soporta altas temperaturas y bajas presiones, proporciona un área de superficie muy grande en comparación con otras zeolitas [5, 24, 16].

Fig. 1 Zeolita sintética (tipo 3A), con un aumento utilizando un microscopio electrónico de barrido (SEM)
En consecuencia, una de las principales ventajas es que tiene una capacidad de adsorción mayor a otros tipos de zeolitas. Comercialmente está disponible y es vendido por la empresa Silica Gel. Para la simulación del proceso se consideran entonces las características de una zeolita sintética tipo 3A.
El diseño general del proceso y las condiciones de operación fueron definidos considerando como referencia el proceso reportado por [31].
El proceso consta de 2 columnas (lechos) empacadas con zeolita tipo 3A, estas columna operan en 2 etapas (adsorción/regeneración) que involucran 4 pasos: adsorción (etapa I), despresurizaron, purga y represurización (etapa II).
Cada paso se realiza en un tiempo apropiado para cumplir con el objetivo operacional correspondiente. La Figura 2 muestra el diagrama de flujo del proceso e indica los tiempos de cada paso. La presión para llevar a cabo la adsorción es mayor que la presión atmosférica (3.79 de bar), ya que a mayor presión, las zeolitas atraen de manera más efectiva a las moléculas de agua. La presión para la etapa de regeneración es menor que la presión atmosférica (0.13 bar), ya que a una presión baja se puede romper fácilmente el enlace débil adsorbente-adsorbato [1, 7, 16].

Fig. 2 Diagrama de flujo del PSA, el cual consta de dos lechos, Considera 4 pasos que conforman un ciclo: Adsorción, despresurización, purga y represurización
Sin embargo la temperatura de producción debe mantenerse aproximadamente constante y superior a los 440 K (ya que se trabaja en fase gaseosa). El mantener la temperatura elevada ayuda a liberar las moléculas de agua adsorbidas por la zeolita en el paso de regeneración. Se considera que la composición de alimentación de la mezcla etanol-agua es cercana al punto azeotrópico (8% en peso de agua y 92% en peso de etanol).
Así mismo, el diagrama de flujo incluye 10 válvulas que sirven para cambiar la dirección del flujo y mantener los flujos a los valores deseados a través de los lechos. El simulador de la planta fue desarrollado con el software ASPEN ADSIM.
Este es un simulador especializado para diagramas de flujo de procesos de adsorción, es útil para diseño óptimo, simulación, optimización y análisis de procesos de adsorción [10, 19, 14, 5]. Sirve para simular una variada gama procesos industriales de adsorción para aplicaciones con líquidos y gases. Se puede usar para desarrollar e identificar adsorbentes óptimos, diseñar ciclos de adsorción y mejorar la operación de plantas. De igual manera, es posible sincronizar este software con otros programas para facilitar las tareas de control.
Tabla 1 Nomenclatura
Letras | |
ap | Superficie de la partícula (m2/m3) |
ci | Concentración molar (i, kmol/m3) |
Dm | Difusividad molecular (i,m2/s) |
Dei | Difusividad efectiva (i,m2/s) |
Cps | Calor especifico (solido) (MJ/kmol/K) |
Ezi | Coeficiente dispersión axial (i,m2/s) |
Cpai | Calor específico (MJ/kg/K) |
Hs | Coeficiente de transferencia de calor (J/s)/m2/K |
M | Peso molecular (kg/kmol) |
IP(1,2,3,4,)i | Parámetros de isoterma del componente (i) |
Ji | Velocidad de transferencia de massa (kmol/m3(bed)/s) |
MTCs | Coeficiente de transferencia de massa (sólido) (1/s) |
ksa | Conductividad térmica (MW/m/K) |
P | Presión del gas (bar) |
Wi | Cantidad adsorbida (i, kmol/kg) |
|
Cantidad de equilibrio adsorbido (i, kmol/kg) |
R | Constante de gas (8.31451e - 3) (MJ/kmol/K) |
rp | Radio de la partícula esférica (m) |
t | Tiempo (s) |
Tg | Temperatura del gas (K) |
Ts | Temperatura del sólido (K) |
T | Temperatura, (K) |
F | Flujo (Kmol/hr) |
vg | Velocidad superficial del gas (m/s) |
z | Coordenada de la distancia axial (m) |
yi | Fracción molar del gas (componente) (i) |
Símbolos | |
|
Vacío del Lecho (intraparticular) m3(void)/m3(bed) |
|
Vacío interparticular |
ρb | Densidad del lecho (kg/m3) |
ρs | Densidad del adsorbente (kg/m3) |
ρp | Densidad de la partícula (kmol/m3) |
ρg | Densidad molar del gas (kmol/m3) |
ΔHi | Calor de adsorción (i,MJ/kmol) |
Ψ | Factor de la partícula |
Μ | Viscosidad dinámica (Ns/m2) |
Ω | Parámetro |
Subíndice | |
F | Flujo de alimentación |
I | Componente agua (w) o etanol (e) |
G | Fase gas |
S | Fase sólido |
P | Partícula |
B | Bulto o lecho empacado |
Este simulador es una herramienta muy útil, sin embargo para obtener resultados apropiados es importante que los datos de entrada en ADSIM sean los adecuados y correctos para el proceso. Es de gran importancia conocer muy a fondo cada sección del programa, así como conocer el proceso, de tal manera que la configuración de las diferentes partes del modelo matemático, del ciclo, de las conexiones y la distribución y organización de las válvulas sean apropiados y correctos [5, 13, 16, 18, 9, 4]. Los resultados en lazo abierto, obtenidos a través de este simulador son comparados con los resultados obtenidos en [8]. El diagrama de flujo del proceso se muestra en la Fig. 2.
2.1. Configuración del simulador Aspen-Adsim
El modelo matemático, se basa en las suposiciones que a continuación se mencionan:
El balance de materia incluye la convección, dispersión axial, acumulación de la fase gaseosa y transferencia de masa.
La presión de la fase gaseosa varía con el tiempo y la dirección axial.
No hay reacciones químicas.
La fase vapor se comporta como gas ideal.
La conducción térmica axial para la fase solida se caracteriza por un parámetro constante, pero la contribución radial no se cuantifica.
La operación es no isotérmica y el sistema es adiabático.
La entalpía de la fase adsorbida es significativa y se estima asumiendo las capacidades de calor constantes.
El calor de la adsorción y el coeficiente de la transferencia de calor son constantes, los efectos de la temperatura, presión, carga local o las variaciones de la velocidad no se consideran.
La constante de tiempo de difusión es pequeña en comparación con el tiempo de ciclo.
La transferencia de masa se modela con una ecuación de parámetros concentrados. La fuerza motriz para el sólido es lineal y se estima con un coeficiente de transferencia de masa constante.
El equilibrio de adsorción es modelado por la ecuación de Langmuir, en términos de parámetros dependientes de la temperatura.
2.2. Modelo del proceso PSA
Balance de materia:
Termino de dispersión axial:
El coeficiente de dispersión axial se estima en función del radio de la partícula, de la velocidad del gas y de la difusividad molecular:
Termino de convección:
Termino de acumulación de materia en la fase gaseosa:
Flujo sobre la superficie del solido:
donde:
Para establecer el balance de energía, se considere) una operación no isotérmica con conducción de gas, así mismo se definió el calor de adsorción y coeficiente de transferencia como constante.
Balance de energía:
El balance de energía es aplicado para determinar las cantidades de energía que es intercambiada y acumulada dentro de un sistema. La velocidad a la que el calor se transmite depende directamente de dos variables: la diferencia de temperatura entre los materiales calientes y fríos y de la superficie disponible para el intercambio de calor.
También influyen otros factores como la geometría y propiedades físicas del sistema y, así como de las condiciones de flujo.
Ksa es la conductividad de la zeolita:
La acumulación de energía en el sólido es:
Mientras que el calor que adsorbe la zeolita se calcula de la siguiente forma:
y el calor de adsorción es:
La transferencia de calor solido-gas se caracteriza por el coeficiente de transferencia de calor y del área de transferencia de calor:
Las relaciones de los equilibrios cinético y termodinámico (ecuaciones 14 y 15), se definieron para la zeolita 3A. Se asumió un modelo lineal. Se considera la ecuación de Langmuir (es decir, se considera que la adsorción que se presenta una mono-capa). Esta ecuación puede ser formulada en función de la presión parcial o de la concentración.
2.3. Ecuación de Langmuir (modelo termodinámico)
Langmuir dedujo la isoterma Tipo I (14) empleando un modelo simplificado de la superficie de un sólido:
La superficie proporciona un cierto número de posiciones para la adsorción y todas son equivalentes.
Solo se adsorbe una molécula sobre cada position.
Su adsorción es independiente de la ocupación de las posiciones vecinas (las moléculas adsorbidas no interaccionan entre sí).
donde:
Pi es la presión parcial.
IP1, IP2, IP3 son los parámetros de la isoterma.
Ts es la temperatura del adsorbente. Modelo cinético (LDF):
El modelo de fuerza motriz lineal (LDF, por sus siglas en inglés), ampliamente usado para operaciones de adsorción, se empleó para representar la cinética. Si se considera que la principal resistencia a la transferencia de masa se presenta en el interior de las partículas, el coeficiente global se relaciona directamente con la difusividad del agua en el adsorbente. La ecuación (15) muestra la forma empleada para calcular el coeficiente de transferencia.
Los parámetros se obtuvieron de [4], solo se considera la dependencia con la temperatura:
donde: Dei Es la difusividad efectiva y puede ser calculada de la siguiente manera:
con Ω = 15. [3] se ha demostrado que se desprecia la magnitud del coeficiente de transferencia de masa para tiempos cortos de adsorción. Durante el paso de adsorción este valor se puede calcular con la siguiente ecuación:
Como los tiempos de adsorción son cortos, el Ω = 15 en este trabajo.
Caída de presión:
Se utilizó la ecuación de Ergun para estimar las caídas de presión, de acuerdo con [4]:
El método numérico que se utilizó para resolver el sistema de ecuaciones diferenciales parciales que se resume en la Tabla 2 fue Colocación Ortogonal sobre Elementos Finitos de segundo orden, identificado en ADSIM como OCFE2.
Tabla 2 Ecuaciones del modelo PSA
Balance de materia |
|
Balance de momento |
|
Balance de energía |
|
Modelo cinético |
|
Modelo termodinámico |
|
3. Proceso de identificación de un modelo reducido y diseño del esquema de control para el proceso PSA
Para diseñar un controlador es necesario un modelo simplificado o reducido. Una opción para obtenerlo es formular un modelo matemático que relacione las variables de control a partir de datos de entrada y salida de la planta. Para el presente trabajo, la planta está representada por el simulador conteniendo el modelo riguroso PSA.
El modelo del simulador es no lineal y toma en cuenta variaciones espaciales, por lo tanto no es adecuado para el diseño de controladores, pero si es suficientemente representativo de un proceso real. El modelo reducido debe capturar las dinámicas importantes del proceso PSA [1, 6, 7 y 5].
Antes de identificar un modelo reducido se realizó un análisis de sensibilidad para poder establecer el lazo de control (seleccionar las entradas y salidas del controlador).

Fig. 3 Diagrama de flujo de los 4 pasos (adsorción, despresurización, purga y represurización) utilizando las válvulas de control
El simulador del proceso de adsorción para deshidratar etanol, desarrollado en la plataforma de ASPEN ADSIM, fue construido asegurando una configuración adecuada de diferentes partes.
En resumen:
-
El modelo matemático del proceso se definió respetando las suposiciones de modelado y la selección de relaciones para cálculo de equilibrio y caídas de presión que fueron presentadas en la Sección 2. Para configurar el modelo se introdujeron los parámetros proporcionados en la Tabla 4. Para completar la definición del modelo matemático, las condiciones en la frontera fueron definidas tomando en cuenta las condiciones en las corrientes de entrada (Tabla 3).
Como condición inicial para las simulaciones en lazo abierto se consideró el arranque de la planta y el tiempo de simulación fue el necesario para que el proceso alcanzara el estado pseudo-estacionario.
Para llevar a cabo las simulaciones en lazo abierto, el proceso se inicia en las condiciones nominales; es decir, una vez establecido el estado pseudo-estacionario.
Para resolver el sistema de EDPs que constituyen el modelo del proceso se hace una discretización en la variable de posición axial, usando 20 nodos, aplicando un método de discretización de Colocación Ortogonal en Diferencias Finitas.
Tabla 3 Condiciones iniciales y de frontera
Pasos del ciclo | Siguiente ciclo | |
---|---|---|
I. Adsorción | ||
t = 0 | y = W = 0, T = TF , P = PF | y = y(IV) W = W(IV) T = T(IV) P = P(IV) |
z = 0 | y = yF , T = TF , P = PF , F= FF | |
z = L |
|
|
II. Despresurización | ||
t = 0 | y = y(I) , W = W(I) , T = T(I) , P = P(I) | |
z = 0 |
|
|
z = L |
|
|
III. Purga | ||
t = 0 | y = y(II) , W = W(II) , T = T(II) , P = P(II) | |
z = 0 | Y = YP , T = TP , F= FP | |
z = L |
P =
PP, |
|
IV. Represurización | ||
t = 0 | y = y(III) , W = W(III) , T = T(III) , P = P(III) | |
z = 0 | y = yP , T = TP , F= F (válvula) | |
z = L |
|
Tabla 4 Parámetros del lecho para adsorber agua y producir etanol
Alimentación | Valor |
---|---|
Fracción molar del agua yw | 0.182 |
Fracción molar del etanol ye | 0.818 |
Temperatura de producción TF | 440 oK |
Presión de producción PF | 3.79 bar |
Presión de purga Pp | 0.1379 bar |
Longitud del lecho l | 7.3 m |
Diámetro del lecho D | 2.4m |
Vacío inter-partícula |
0.4 |
Vacío intra-partícula |
0.63 |
Densidad del adsorbente |
729.62 kg/m3 |
Coeficiente de transferencia de masa (e) MTC | 1.99605 1/s |
Coeficiente de transferencia de masa (w) MTC | 2.941 1/s |
Difusividad molecular (e) Dm | 2.1796 e-5m2/s |
Difusividad molecular (w) Dm | 3.728e-6 e-6m2/s |
Calor del adsorbente en la fase adsorbida (e) Cpa | 118720.0 J/kmol/K |
Calor del adsorbente en la fase adsorbida (w) Cpa | 37470.0 J/kmol/K |
Calor específico del adsorbente Cps | 1260 J/kg/K |
Constante de calor de adsorción (e) ΔH | -3.93 e7J/kmol |
Constante de calor de adsorción (w) ΔH | -51.9e7J/kmol |
Constante para el coeficiente de transferencia de calor HTC | 1.e6J/s/m2/K |
Conductividad de calor de la fase gaseosa ks | 41.26 W/m/K |
Área de la superficie específica del adsorbente ap | 1133.86 1/m |
Radio de la partícula adsorbente rp | 0.0015875 m |
Parámetro de isoterma (e) (IP1) | 0.0 n/a |
Parámetro de isoterma (w) (IP1) | 1.9064e-7n/a |
Parámetro de isoterma (e) (IP2) | 0.0 n/a |
Parámetro de isoterma(w) (IP2) | 6242.13 n/a |
Parámetro de isoterma (e) (IP3) | 0.0 n/a |
Parámetro de isoterma (w) (IP3) | 1.7874e-5n/a |
Parámetro de isoterma (e) (IP4) | 0.0 n/a |
Parámetro de isoterma (w) (IP4) | 6242.13 n/a |
Parámetros computacionales | |
Nodos (axial) | 20 |
Método de discretización axial | OCFE2 (Colocación ortogonal sobre elementos finitos) |
3.1 Análisis de sensibilidad de la columna de 7.3 m.
Se analizó la influencia de las siguientes variables sobre la pureza del producto una vez alcanzado el estado pseudo-estacionario (EPE): temperatura de producción, tiempo de purga, composición de alimentación, presión de producción, presión de purga, y flujo de alimentación. El proceso se simulo con variaciones de ±1 % (una entrada escalón) en las entradas citadas y se registraron la pureza del etanol, el número de ciclos necesarios para alcanzar el nuevo EPE y la sensibilidad calculada como:
A partir de este estudio paramétrico se definió la variable manipulada (entrada) para poder controlar la pureza deseada (salida).
Como resultado del estudio paramétrico del proceso se observó que el índice de sensibilidad es muy similar para cualquiera de los cambios en las entradas que fueron probados. Aun cuando frecuentemente se selecciona el tiempo de ciclo o de alguno de los pasos del ciclo como entrada de control, la sincronización entre el simulador del proceso y el controlador simulado en otra plataforma es difícil de lograr, y lo mismo ocurriría con una planta real.
Al compilar los dos programas (ASPEN ADSIM y Matlab) no es posible simular el proceso utilizando variables que no tienen un tiempo continuo como; presión de purga, tiempo de purga y tiempo de adsorción. La sincronización es difícil de lograr debido que ASPEN ADSIM debe compilar por lo menos un tiempo de alguno de los pasos (adsorción, despresurización, purga y represurización) continuamente.
El coeficiente de sensibilidad resulto mayor para variaciones del flujo de alimentación, indicando una influencia más importante de esta entrada sobre la pureza; sin embargo, también se observó que al cambiar el flujo de alimentación el estado pseudo-estacionario se alcanza con un mayor número de ciclos y además la pureza aumenta cuando el flujo disminuye, pero disminuye con el aumento de flujo.
La temperatura, el tiempo de purga y la composición de alimentación tienen una influencia muy similar en la pureza del producto, y alcanzan el nuevo estado pseudo-estacionario en un número de ciclos, también similar. Variaciones pequeñas de la presión del proceso y de la presión de purga afectan de manera menos importante la pureza del producto, y el proceso tarda más en llegar a un nuevo estado estacionario. En función de la sensibilidad del proceso y tomando en cuenta las dificultades para implementar el controlador, por la naturaleza cíclica del proceso, se decidió usar como entrada de control el flujo de alimentación al proceso. El actuador es por lo tanto, la válvula de alimentación. Los resultados del estudio paramétrico se resumen en la Tabla 5.
Tabla 5 Análisis de sensibilidad
TF (oK) |
t (s) |
Yw |
PF (bar) |
Pp (bar) |
Flujo |
Purezae (wt %) |
Ciclos | Sensibilidad |
---|---|---|---|---|---|---|---|---|
440 | 15 | 0.182 | 3.79 | 0.1379 | 512 | 99.57 | 350 | |
435 | 15 | 0.182 | 3.79 | 0.1379 | 512 | 99.61 | 240 | -19 |
444 | 15 | 0.182 | 3.79 | 0.1379 | 512 | 99.48 | 251 | 20 |
440 | 14 | 0.182 | 3.79 | 0.1379 | 512 | 99.59 | 233 | -18 |
440 | 16 | 0.182 | 3.79 | 0.1379 | 512 | 99.54 | 232 | 19 |
440 | 15 | 0.180 | 3.79 | 0.1379 | 512 | 99.52 | 228 | 14 |
440 | 15 | 0.184 | 3.79 | 0.1379 | 512 | 99.60 | 229 | -15 |
440 | 15 | 0.182 | 3.75 | 0.1379 | 512 | 99.58 | 485 | -5 |
440 | 15 | 0.182 | 3.83 | 0.1379 | 512 | 99.56 | 489 | 7 |
440 | 15 | 0.182 | 3.79 | 0.136 | 512 | 99.50 | 501 | 15 |
440 | 15 | 0.182 | 3.79 | 0.14 | 512 | 99.61 | 497 | -14 |
440 | 15 | 0.182 | 3.79 | 0.1379 | 504 | 99.79 | 510 | -45 |
440 | 15 | 0.182 | 3.79 | 0.1379 | 520 | 99.26 | 503 | 40 |
Una vez configurado el modelo del proceso PSA, es necesario conectar el simulador ADSIM con la plataforma de Simulink, de tal forma que los datos entrada-salida de la planta puedan ser usados para identificar el sistema. El modelo resultante es usado para diseñar el controlador.
3.2. Modelo reducido (Hammerstein-Wiener)
Para obtener un modelo por identificación del proceso a partir de los datos de entrada-salida provenientes de la planta se utilizó el ToolBox de identificación de MatLab, pero antes se filtró la señal obtenida del modelo riguroso PSA ya que era imposible obtener un ajuste superior al 70%. Después de analizar y probar algunas estructuras básicas como ARX o ARMAX para modelar el sistema, se concluyó que este no puede ser modelado adecuadamente con estructuras lineales.
El problema se resolvió mediante la formulación de un modelo no lineal con estructura Hammerstein-Wiener, el cual está formado por 3 bloques: un bloque de entrada, no-lineal (relación estática), un bloque lineal (dinámico), y un bloque de salida no-lineal (también modelado con una relación estática).
Estos bloques están conectados en serie como se observa en la Fig. 4. En esta representación, la entrada Ut es el flujo de alimentación y la salida Yt es la composición de etanol.
Aun cuando solo se modela la relación entre estas dos variables, los datos entrada-salida incluyen el efecto y las interacciones con otras variables del sistema; entonces, el modelo identificado es una simplificación y es válido solo cerca de las condiciones nominales, pero se plantea la hipótesis de que este modelo no lineal es suficientemente bueno para poder desarrollar un controlador que tolere algunas variaciones en las entradas del proceso multivariable.
El modelo del bloque lineal es una función de transferencia con 2 zeros y 3 polos. Este modelo se muestra en la ecuación 20.
Después de obtener la parte lineal del modelo se identificaron los bloques no lineales (estáticos) del modelo Hammerstein-Wiener. El modelo estático es una relación construida por segmentos de rectas que, combinadas, aportan la relación no lineal entre dos variables.
Cada señal se reproduce con 4 diferentes ecuaciones de rectas, dependiendo del valor de la señal de entrada se toma solo una de las ecuaciones de recta. Las funciones que representan los bloques de entrada y salida no lineal son las que se muestran en las Tablas 7 y 6, respectivamente.
Tabla 6 Funciones del bloque no lineal de entradas
Entrada, Ut | Funciones, UL |
---|---|
-0.0061 > Ut >= -0.009 | UL = 0.68 * Ut + 512.0 |
-0.0006 > Ut >= -0.006 | UL = 0.45 * Ut + 511.9 |
0.0047 > Ut >= -0.0006 | UL = 0.45 * Ut + 512.0 |
0.0083 > Ut >= 0.004 | UL = 0.68 * Ut + 511.9 |
Tabla 7 Funciones del bloque no lineal de salidas
Entrada, YL | Funciones, Yt |
---|---|
0.984 > YL >= 0.6639 | Yt = 263 * YL - 343.1 |
0.988 > YL >= 0.9843 | Yt = 18824 * YL - 18614 |
0.668 > YL >= 0.9888 | Yt = 22882 * YL - 22626 |
0.992 > YL >= 0.6686 | Yt = 346 - 263.1 * YL |
El bloque de entrada no-lineal representa la relación que existe entre la señal Ut y UL del modelo Hammerstein-Wiener como se observa en la Fig. 5. Estas funciones fueron calculadas tomando en cuenta el rango de variación de Ut y Yt presente en los datos de la simulación.
Para el bloque de salida no-lineal las funciones que relacionan las señales YL y Yt del modelo Hammerstein-Wiener se evidencian en la Fig. 6 y en la Tabla 7 se muestran las 4 diferentes ecuaciones de rectas que se forman entre los puntos.
Como UNL actúa en el puerto de entrada del bloque lineal, esta función se denomina no linealidad de entrada . Similarmente, como YNL actúa en el puerto de salida del bloque lineal, esta función se denomina no linealidad de salida.
Si el sistema contiene varias entradas y salidas, se definen las funciones UNL y YNL para cada señal de entrada y salida. No siempre es necesario incluir bloques no lineales tanto en la entrada como en la salida en la estructura del modelo.
Cuando un modelo contiene solo la no linealidad de entrada UNL, este es un modelo Hammerstein. Del mismo modo, cuando el modelo contiene solo la no linealidad de salida YNL se denomina modelo Wiener.
La no linealidad de entrada es una función estática (sin memoria), donde el valor de la salida en el tiempo t depende solamente del valor de entrada en el tiempo t. Es posible configurar la no linealidad de entrada como una red sigmoide, wavelets, saturación, zona muerta, función lineal por trozos, polinomio unidimensional o mediante una red personalizada.
Similar a la no linealidad de entrada, la no linealidad de salida es una función estática. Esta se configura de la misma manera que la no linealidad de entrada. También es posible eliminar la no linealidad de salida, tal que YL = Yt.
Las relaciones entre la entrada y la salida de los bloques no lineales son calculadas con el toolbox de MatLab, así como la función de transferencia del bloque lineal.
3.3. Control predictivo óptimo basado en un modelo Hammerstin-Wiener
El Controlador Predictivo Óptimo se basa en el control predictivo modo dual (predicciones utilizando el modo dual) y el paradigma de lazos cerrados (predicciones en lazo cerrado). El control modo dual es una estrategia que tiene dos modos.
El primer modo se utiliza cuando el sistema se encuentra lejos del estado estable o del punto de operación. El segundo modo se utiliza cuando el sistema se encuentra cerca del punto de operación deseado [2].
El concepto de modo dual no implica que se realice una conmutación entre los modos, sino que es una descripción de como las predicciones se plantean. Considere un horizonte de predicción ny la predicción se divide en dos partes:
En el modo uno se toman las primeras nc predicciones, donde nc son los grados de libertad de controlador (es decir cuántos valores puede calcular el optimizador):
En el modo dos se toman las predicciones restantes, donde seria usual seleccionar ny infinito:
Por otra parte el paradigma de lazo cerrado establece escoger una ley de control que estabilice y asuma que esta ley de control está presente a lo largo de las predicciones (en lazo cerrado se van a realizar las predicciones en donde se va introduciendo la Ganancia K).
El controlador LQR es un control óptimo de horizonte infinito. Este controlador genera la ganancia de retroalimentación de estado K para cada instante de muestreo k[2y 5]. Al incluir esta ganancia en el esquema de control predictivo, origina que las predicciones se generen en lazo cerrado como se mencionó anteriormente. A la ley de control estabilizante se le agrega una perturbación, la cual asegura el cumplimiento de las restricciones (Fig. 7).
El principio de optimalidad de Bellman establece que cualquier segmento de una trayectoria optima también es óptima para nc = ny = ∞. Esto es porque en la planeación inicial de la trayectoria óptima se asume que el problema no cambiara y que el sistema evoluciona como se predijo asumiendo que el modelo es perfecto, por lo tanto, la trayectoria óptima inicial se sigue.
Como el Controlador Predictivo Óptimo para generar la ganancia K utilizó el controlador LQR óptimo, por lo tanto cumple con el principio de optimalidad de Bellman.
Por lo tanto al utilizar el paradigma de lazo cerrado y el modo dual, realizando las predicciones en lazo cerrado se garantiza la estabilidad, otra manera de verlo es en la función costo J obtenida, es una función de tipo Lyapunov que garantiza la estabilidad.
Se define la siguiente función costo en términos de
P se obtiene de la solución de la ecuación de Lyapunov:
Por otra parte el Controlador Predictivo Óptimo se basa en el modelo lineal (bloque lineal) en espacio de estados estándar, sin considerar perturbaciones, para este trabajo tiene la siguiente forma:
donde
El bloque lineal en función de transferencia, se convirtió a espacio de estados quedando de la siguiente manera:
La señal de control que se aplica se presenta de la forma:
donde ck es una variable de compensación. Esta variable, es la variable de decisión que va optimizar en el esquema de control predictivo.
Así mismo K es la ganancia de retroalimentación y Pr
es la matriz de prealimentación para que el sistema en lazo cerrado siga la
referencia deseada, esta se obtiene de la siguiente
Pr =KPx +
Pu. En donde Px y
Pu son matrices optimizadas y
donde xss y uss son los valores de estado estable del sistema, en (Muske & Rawlings, 1993) se dan los detalles para la obtención de Px y Pu.
El objetivo clave del controlador es regular la pureza del etanol ante perturbaciones. El valor de referencia es 0,9885 fracción molar del etanol (99.58% fracción molar del etanol), y las perturbaciones probadas fueron cambios en la temperatura y fracción molar en la composición de alimentación, así como variaciones del tiempo de purga.
Para hacer el diseño del controlador se obtuvieron las funciones inversas de los 2 bloques no lineales estáticos (entrada y salida) del modelo Hamerstain-Wiener como se muestra en la Fig. 8. En donde ahora el bloque de entrada pasara a ser la salida (función inversa del boque de entrada) y el bloque de salida pasara a ser la entrada (función inversa del bloque de salida) del modelo Hammerstein-Wiener.
3.4. Diseño e implementación del controlador predictivo óptimo al modelo riguroso PSA
Para sintonizar el controlador Predictivo Óptimo se utilizó el bloque lineal y las funciones inversas de los 2 bloques no lineales estéticos como se observa en la Fig. 9. En este punto se establecieron las restricciones para el controlador.
El rango de la señal que genera el controlador es (ecuación 27):
donde uk es señal generada por el Controlador Predictivo Óptimo, la cual está restringida en el rango mencionado arriba, esta señal que genera el controlador se introduce en el bloque no-lineal inverso, el cual nos arroja la entrada real (valor del flujo de alimentación) que se necesitó para la planta PSA, la entrada real está comprendida en el siguiente rango:
La señal de entrada debe estar comprendida en este rango:
donde yk es la salida (fracción molar o pureza obtenida) de la planta PSA en la cual la restricción es que no puede de ser mayor a 1.
Así mismo se sintonizo el controlador adecuándolo para su buen funcionamiento para lograr una pureza deseada en menos tiempos de ciclos ante perturbaciones. Los parámetros de sintonización son: R (matriz de ponderación de los estados), Q (matriz de ponderación de la entrada de control), nc (horizonte de predicción de la entrada de control) y ny (Horizonte de predicción de las salidas).
Se observó que para una R=200, Q=1000, nc=2 y ny=35, la señal de control y la evoluciones de los estados es suave (lenta) pero con pocas oscilaciones o ruido.
Para poder simular y controlar la planta PSA, se estableció la comunicación entre el programa Matlab/Simulinkcon Aspen adsorption (ADSIM). El modelo que se creó en ADSIM se pudo transportar como un bloque de funciones en Simulink (diagrama de bloques), estos dos programas trabajaron en con el mismo periodo de tiempo (1 segundo), efectuando los 4 pasos del proceso PSA sin ningún problema y sin perder información (datos obtenidos al simular y controlar) en cada instante del tiempo de muestreo.
Como anteriormente se mencionó, es necesaria la utilización de las funciones inversas de los 2 bloques no lineales (entrada y salida) para implementar el controlador Predictivo Óptimo quedando el esquema como se muestra en la Fig. 10.
4. Resultados
4.1 Simulaciones en lazo abierto de un proceso PSA con dos columnas de 7.3 m.
En esta primera parte de resultados se muestran las simulaciones en lazo abierto del proceso de deshidratación de etanol mediante PSA. A través de las simulaciones se presenta la evolución de las variables hasta llegar al EPE, es decir, se muestran los perfiles de presión P, la temperatura T, composiciones de etanol y agua yi en función del tiempo (t) y a largo de la dirección axial (z) del lecho con geometría cilíndrica. El propósito de simular el desempeño del sistema en lazo abierto es en primer lugar mostrar el funcionamiento del proceso, así como el comportamiento que presentan las variables en las etapas y/o pasos que conforman el ciclo de adsorción-desorción y cuando se realiza el enlace entre los mismos. En segundo lugar, el propósito es mostrar la eficacia del simulador ya que los resultados deben coincidir con el trabajo del cual se toma el diseño del proceso [8].
Inicialmente la cantidad adsorbida en la columna C1 es de 0 kg, el adsorbente está totalmente limpio o regenerado y esta presurizado a 3.79 bar, opera a una temperatura de 440 K para poder alimentar la mezcla etanol-agua en fase vapor. Se alimenta un flujo de 512 kmol/hr de una mezcla con composición de 0.182 fracción molar de agua (8 % en peso de agua) y 0.818 fracción molar de etanol (92% en peso de etanol). En cuanto el vapor conteniendo etanol-agua entra en contacto con las zeolitas, una adsorción rápida se presenta acompañada del calor (proceso exotérmico) que se desprende dentro de la columna C1. Después de cierto tiempo, realizando varios ciclos con sus respectivos pasos (adsorción, despresurización, purga y represurización) se muestra el comportamiento dinámico del sistema hasta llegar al EPE, en el cual se alcanza la pureza deseada (99.58%) (Fig. 11). Es importante notar que el EPE se logreo después de 241500 s de funcionamiento (350 ciclos).
En la Fig. 24 se observa también lo siguiente: Los perfiles de composición de etanol y agua con respecto al tiempo tienen la forma de una exponencial de crecimiento y decrecimiento monótono respectivamente, inician en el tiempo cero con una composición igual a la composición de alimentación y evolucionan aumentando la composición de etanol al mismo tiempo que la composición de agua disminuye.
Los valores que se grafican corresponden a la composición de etanol y agua en el vapor de salida (producto) de la columna de adsorción que es C1 durante 345 s, C2 los siguientes 345 s, y así continua el cambio periódicamente. Aun cuando parece que se establece un estado de equilibrio, una vista aumentada del perfil de composición de etanol permite observar la oscilación de esta variable con una amplitud pequeña en comparación con la diferencia entre el estado inicial y el estado en equilibrio; sin embargo esta amplitud puede aumentar en función de las entradas.
Esta oscilación se debe a la operación cíclica del proceso, ya que este se lleva a cabo en pasos a diferentes condiciones, de ahí el nombre del proceso, adsorción con oscilaciones en presión. Debido a que cada pico corresponde a la variación de la composición en un ciclo, la composición está continuamente cambiando; sin embargo, después de varios ciclos, esta variación de concentración es el mismo ciclo y entonces se dice que el proceso alcanzo un estado pseudo-estacionario.
En esta simulación se realizaron un gran número de ciclos, alcanzando el estado pseudo-estacionario o EPE en 350 ciclos.
Posteriormente, la Fig. 12 muestra los perfiles de composición de agua en la etapa de adsorción (una vez establecido el EPE) en función de la coordenada axial (z), para diferentes tiempos de operación. La línea continua corresponde al perfil de composición al final de la etapa de adsorción, mientras que los perfiles en tiempos inferiores se muestran con líneas punteadas.

Fig. 12 Perfiles de concentración de agua a diferentes tiempos, el valor 0 en la abscisa se refiere a la parte inicial del lecho
Así mismo, en la la Fig. 13 se presenta el perfil de temperatura en función de la dirección axial (z) a diferentes tiempos. Se observa el incremento de la temperatura conforme avanza la etapa de adsorción y como el máximo se va desplazando a lo largo del lecho empacado.

Fig. 13 Los perfiles de temperatura en el lecho durante la etapa de adsorción en el EPE en función de la dirección axial. La posición (z) 0 representa la parte superior del lecho y la dirección de flujo va desde la parte superior a la parte inferior del lecho
En la Fig. 14 se presenta el perfil de la composición de agua en función de la dirección axial en el lecho empacado (z), el cual corresponde a la etapa de regeneración del lecho de zeolitas. Este perfil se obtiene con el proceso operando ya en el EPE. A los 345 s la composición de agua es de cero ya que el lecho ha sido limpiado.

Fig. 14 Los perfiles de concentración en el lecho durante la etapa de regeneración en el EPE en función de la coordenada axial. La posición 0 representa la parte superior del lecho y la dirección del flujo es desde la parte superior a la parte inferior del lecho
Al disminuir la presión en la columna, la zeolita libera parcialmente el agua adsorbida y la concentración del vapor de agua aumenta. El perfil inicial, en 0 s de la Fig. 15 es el mismo que el último perfil (345 s) de la etapa de adsorción. En los primeros segundos de la etapa de regeneración una parte pequeña de agua es liberada, esto se observa en el perfil correspondiente a los 35 s de operación.
A medida que disminuye la presión, estos perfiles de concentración de agua en fase vapor presentan un valor mínimo, mostrando que el agua que existía en el absorbente fue retirada del lecho mediante una pequeña purga con producto puro, libre de agua.
Por otro lado, en la etapa de regeneración se lleva acabo como un proceso endotérmico y la temperatura en el lecho disminuye conforme avanza la limpieza o recuperación del lecho (Fig. 15). Una vez más, valores máximos de temperatura se desplazan a lo largo del lecho, y en general la temperatura va de un valor elevado a uno bajo.
En la Fig. 16 se observan las variaciones de presión y de temperatura en función del tiempo, cuando ya ha sido establecido el EPE. La presión de operación cambia de 3.79 bar en la adsorción a 0.134 bar en la regeneración.
El conocimiento de la dinámica del proceso y la interpretación de los perfiles del ciclo EPE es muy útil para entender el comportamiento del sistema. El simulador desarrollado para el proceso de deshidratación de etanol obtiene resultados equivalentes a los presentados en [1]. Por lo tanto, este simulador es usado como planta virtual para probar la eficacia del control diseñado a partir de un modelo obtenido por identificación del sistema.
4.2. Validación del modelo. Hammerstein-Wiener identificado para el proceso PSA
El análisis de sensibilidad presentado antes ayudo a definir la entrada de control. Un escalón del 1 % en el flujo de alimentación tuvo mayor efecto en la pureza de etanol, comparado con el efecto de las otras variables de entrada (presión de purga, temperatura de alimentación, tiempo de purga, presión de producción y composición de alimentación). En cuanto al tiempo o número de ciclos necesarios para alcanzar el estado pseudo-estacionario después de los cambios aplicados, se observó que la variación del tiempo de purga implica menos ciclos para alcanzar el nuevo EPE y por lo tanto actúa de manera más rápida sobre la pureza del producto.
Sin embargo, el flujo de alimentación fue seleccionado como entrada de control debido que la manipulación de esta variable se facilita porque evoluciona continuamente, tomando valores en uno u otro paso o etapa del proceso de adsorción-desorción; además, es posible actualizar su valor en el mismo tiempo de muestreo que se usa en MatLab/Simulink.
Por otro lado, algunas variables como el tiempo de purga tienen una influencia en la pureza del producto, similar a la del flujo de alimentación, además, el tiempo de purga permite incluso modificar de manera más rápida el proceso. La dinámica del flujo de alimentación es rápida y su manipulación es sencilla ya que se puede hacer a través de una válvula. Una vez seleccionada la entrada de control, se obtuvo un modelo con estructura Hammerstein-Wiener.
Para poder construir la Secuencia Binaria Pseuudoaleatoria (PRBS por sus siglas en inglés) fue necesario simular la planta después de haber llegado al EPE (Figs.17 y 18), esto sirvió para conocer el tiempo de estabilización del sistema de tal forma que la frecuencia de las variaciones de la PRBS permitieran incluir al menos una vez la simulación hasta la estabilización del sistema.

Fig. 17 Simulación dinámica de la fracción molar del etanol desde el arranque de la planta, hasta llegar al CCS, utilizando un entrada de 0.05%
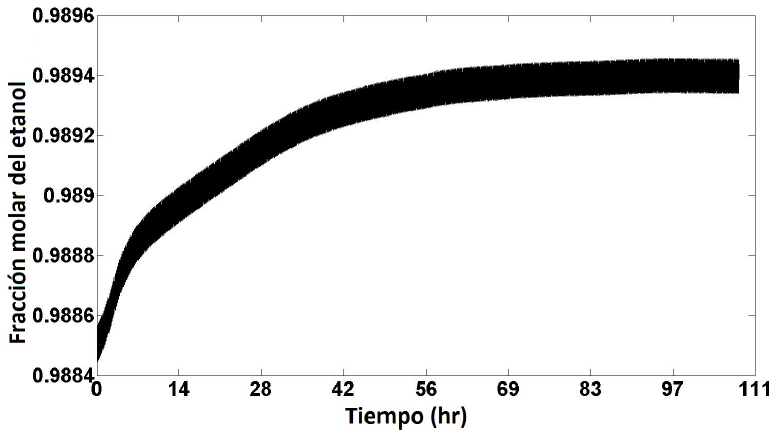
Fig. 18 Vista aumentada de la pureza obtenida después de aplicar un escalón del 0.05%, con un tiempo de convergencia de 310500 s (450 ciclos) para utilizarlo en la PRBS
La formulación del modelo inicia con la generación de una señal PRBS de 5 bits para excitar al sistema representado por el modelo riguroso PSA implementado en el simulador (Fig. 19). La señal de salida se muestra en la Fig. 20.

Fig. 19 PRBS de 5 bits con un periodo de muestreo de 62100 s, aplicada para modificar la el flujo de entrada al proceso con el fin de excitar al proceso para obtener información dinámica del mismo
Se utilizó el ToolBox de identificación de MatLab para formular el modelo no lineal con estructura Hammerstein-Wiener. Aplicando un escalón del 0.05% en el flujo de alimentación, la identificación se logre con un ajuste (FIT) del 80.4%. Esta buena aproximación es evidente en la Fig. 21, con este resultado se consideró que el modelo obtenido captura bien las dinámicas importantes de la planta simulada a través del modelo riguroso PSA.

Fig. 21 Comparación de la salida de la planta vs señal de salida del modelo Hammerstein-Wiener usando los datos de entrada para identificación (señal PRBS)
Para validar el modelo se simulo nuevamente el proceso, pero en esta ocasión se aplicó un escalón del 1.5% en la entrada. En la Fig 22 se observa que la señal de salida simulada con el modelo Hamerstein-Wiener tiene el mismo comportamiento dinámico que la predicción del modelo riguroso PSA. Por lo tanto a partir de este Modelo reducido se realizó el diseño del controlador predictivo óptimo.
4.3. Simulación y prueba del controlador predictivo óptimo al modelo riguroso PSA
El desempeño del controlador predictivo óptimo diseñado fue evaluado implementándolo en la planta virtual (simulador con modelo riguroso PSA) aplicando el esquema de control descrito en la Fig. 23. Una primera prueba consistió en verificar la eficacia del controlador para un seguimiento de trayectoria. La trayectoria seleccionada permite aumentar la pureza del producto desde una fracción mol de etanol igual a 0.9884 hasta una fracción mol de 0.9975.

Fig. 23 Seguimiento de trayectoria usando el controlador predictivo óptimo para establecer un valor más alto de pureza en un menor tiempo
En la Fig. 23 se presentan las simulaciones en lazo abierto y en lazo cerrado. La simulación en lazo abierto toma 222 horas para llegar al nuevo estado pseudo-estacionario, mientras que la simulación en lazo cerrado con el controlador predictivo óptimo converge solo en 42 horas. Entonces, para modificar las especificaciones del producto el controlador ayuda a disminuir considerablemente el tiempo para alcanzar estas nuevas especificaciones, lo que representa un ahorro de costos de producción y de consumo energético.
La señal del controlador óptimo para lograr la pureza deseada se muestra en la Fig. 24. El flujo nominal es de 512 kmol/hr, mientras que la señal de control varía entre 460 y 515 kmol/hr, lo cual representa un cambio del flujo de producción entre -10.16% y +0.6%; una modificación pequeña del flujo de producción y un ahorro importante de tiempo para obtener un producto con 99.75% mol de pureza, superior a los estándares de pureza establecidos en diferentes lugares, estos son: 99.39% mol según la norma europea (CEN prEN 15376), 97.47% mol según la norma de USA y 98.98% mol según la norma brasileña (Resolución ANP36) [1y2].

Fig. 24 Señal del controlador predictivo (óptimo sobre el flujo para establecer una pureza más alta en un menor tiempo de operación
Al inicio hay una pequeña saturación, pero después la entrada va disminuyendo hasta 460 Kmol/hr.
El análisis en lazo abierto de la planta permitió conocer la respuesta dinámica de la planta; debido a las condiciones de operación cambiantes de un paso del proceso a otro, la variación de la composición de etanol es oscilatoria. En cambio, el modelo identificado que es una simplificación a través de la cual se aproxima el efecto del flujo de alimentación sobre la pureza de etanol, es una línea continua que indica una variación promedio de la composición del producto. Aun con las simplificaciones consideradas, el control basado en el modelo Hammerstein-Wiener funcionó adecuadamente.
En un segundo conjunto de pruebas, el esquema de control propuesto fue evaluado por medio de un análisis ante perturbaciones, considerando uno a uno, cambios de la temperatura de alimentación, la fracción molar en la corriente de alimentación y la duración de purga. Las perturbaciones se introdujeron después de llegar al EPE (690 s es equivalente al tiempo de un ciclo y se requieren 350 ciclos para alcanzar el EPE a partir del arranque de la planta).
En la Tabla 6 se proporciona la información sobre los cambios realizados en las entradas, así como el número de ciclos que se requirieron para alcanzar el estado pseudo-estacionario después de los cambios. El número de ciclos necesarios para establecer el EPE después de la perturbación se indica tanto para las simulaciones en lazo abierto como para las simulaciones en lazo cerrado. La comparación de la velocidad para alcanzar el EPE es también un indicador de la efectividad del control propuesto para mantener la regulación de la pureza ante las perturbaciones probadas.
En la Fig. 25 se observa el desempeño del Controlador Predictivo ¿Óptimo para mantener la pureza de etanol ante una perturbación aplicada en la temperatura de alimentación, una perturbación aplicada en el tiempo de purga y una perturbación aplicada en la composición de alimentación. En general, las perturbaciones son atenuadas, especialmente después de 16 horas de operación; sin embargo las variaciones de pureza antes de alcanzar la referencia ocurren en un rango reducido, de 98.8% a 99.1 %.

Fig. 25 Control de pureza de etanol expresada en fracción mol, aplicando perturbaciones en la temperatura de alimentación, en el tiempo de purga y en la composición de alimentación
Con este desempeño del controlador se logra mantener la pureza deseada dentro de un rango aceptable ante diferentes perturbaciones en la entrada. La señal de control se muestra en la Fig. 26; en general, se requiere que el flujo de alimentación disminuya en lugar de aumentar y esto implica reducir la producción, sin embargo, el flujo de alimentación mínimo es de 475 kmol/hr, no muy alejado del flujo nominal de 512 kmol/hr. Por otro lado, la perturbación que requiere una acción de control con menor amplitud es el cambio del tiempo de purga. Además, aplicando la perturbación la planta PSA en lazo abierto, la pureza baja hasta cerca del 95% y aun cuando la señal de control es de menor amplitud para el cambio del tiempo de purga, en lazo abierto, el efecto de la variación del tiempo de purga es más importante (Fig. 27).

Fig. 26 Señal de control para las pruebas ante perturbaciones escalón en la composición de alimentación, tiempo de purga y temperatura de alimentación

Fig. 27 Simulación en lazo abierto aplicando perturbaciones escalón en la composición de alimentación, tiempo de purga y temperatura de alimentación
Observando la respuesta de la planta ante una perturbación en la composición de alimentación, en las Figs. 25 y 27 se hace evidente que la simulación en lazo abierto con este cambio en la entrada (composición de alimentación) implica una desviación menor en la pureza del producto y como consecuencia, la variación de la señal de salida en lazo cerrado es también más suave en comparación con la salida producida en las otras pruebas; sin embargo, la acción requerida de control es mayor que la acción requerida para compensar el cambio del tiempo de purga.
Finalmente, se observa que la desviación más grande en lazo abierto se produce cuando se induce un escalón en la temperatura de alimentación. Esto significa que la temperatura de alimentación tiene una influencia importante en la pureza del producto y el efecto que produce también se ve reflejado en la señal de control, ya que implica una entrada de control mayor que en las otras pruebas.
La diferencia entre las relaciones entrada-salida para las pruebas presentadas se debe a la naturaleza no lineal de la planta y se puede concluir que el hecho de usar un modelo identificado no lineal ayuda a obtener buenos resultados de control del proceso y atenuación de las perturbaciones, aun cuando se aplicó un controlador con una entrada y una salida para regulación y seguimiento de trayectoria en un proceso multivariable. De acuerdo con la Tabla 8, el establecimiento de la pureza del producto después de las perturbaciones fue menor para el control ante un escalón en el tiempo de purga, requiriendo 50 ciclos, contra 150 ciclos para regular la pureza ante un cambio en la temperatura de alimentación.
Tabla 8 Condiciones y resultados de las pruebas del controlador con tres tipos de perturbaciones únicas en las entradas
Variable de entrada y valor nominal |
Perturbación ( %) (Nuevo valor de entrada) |
Establecimiento Número de ciclos (con control) |
Establecimiento Número de ciclos (sin control) |
---|---|---|---|
Alimentación temperatura (Valor nominal 440 K) |
-13.5 (60 K) | 150 | 218 |
Alimentación Fracción molar (Valor nominal 0.182 fracción mol) |
21 (0.03822 fracción mol) | 72 | 232 |
Duración de la purga (Valor nominal) 15 s) |
11.5 (2 s) | 50 | 290 |
El controlador predictivo óptimo diseñado a partir de del modelo reducido (Hammerstein-Wiener) funciona correctamente logrando seguir y mantener la trayectoria deseada a pesar de que el modelo riguroso PSA es un modelo altamente no lineal y dada su naturaleza cíclica (oscilatoria) al pasar de una etapas a otra del proceso de manera periódica. Se puede concluir que cada una de las perturbaciones que se presentaron, fueron atenuadas logrando mantener la pureza deseada.
Posteriormente para probar con mayor exigencia la robustez del controlador, este fue probado ante perturbaciones simultaneas, combinando 2 perturbaciones en la entrada de la planta virtual simulada con el modelo riguroso PSA. Las condiciones de las pruebas y algunos resultados se proporcionan en la Tabla 9.
Tabla 9 Condiciones y resultados de las pruebas del controlador con tres tipos de perturbaciones simultaneas en las entradas
Variable de entrada y valor nominal |
Perturbación ( %) (Nuevo valor de entrada) |
Establecimiento Número de ciclos (con control) |
Establecimiento Número de ciclos (sin control) |
---|---|---|---|
Temperatura de alimentación y duración de la purga (Valor nominal 440 K y 15 s) |
-13.5 (60 K) 11.5 (2 s) |
162 | 229 |
Composición de alimentación y temperatura de alimentación (Valor nominal 0.182 y 440 K) |
21 (0.03822 fracción mol) -13.5 (60 K) |
84 | 241 |
Duración de la purga y Composición de alimentación (valor nominal 15s y 0.182 fracción mol) |
11.5 (2 s) 21 (0.003822) |
61 | 299 |
En la Fig. 28 se muestra el resultado de las pruebas de control con perturbaciones simultáneas. En primer lugar, se aplicaron cambios tipo escalón a la temperatura de alimentación y al tiempo de purga. Los cambios se hicieron en el ciclo 32 (después de 22080 s o 6 hr). Se puede observar como el controlador logra atenuar las dos entradas aplicadas para perturbar el proceso PSA. Para esta primera combinación de cambios en las entradas se requirió el mayor tiempo de establecimiento del sistema; es decir, el número de ciclos necesarios (162 ciclos) fue mayor que en las otras pruebas (84 y 61 s). En cambio en lazo abierto se requirieron menos ciclos para llegar a un nuevo estado pseudo-estacionario (229 ciclos contra 241 y 299 de las otras dos pruebas).
La segunda prueba con perturbaciones simultáneas consistió en aplicar al mismo tiempo un escalón en la composición de alimentación y en la temperatura de alimentación. Estos cambios también fueron inducidos después de 32 ciclos (2208 s o 6 hr).
Para esta prueba, la pureza de etanol es regulada con cambios más abruptos y mayores desviaciones con respecto a la referencia, pero el tiempo de establecimiento no es tan diferente al de las otras pruebas y las variaciones de pureza se hacen con una diferencia no mayor de 0.001 en fracción mol; además, durante una parte de su evolución, la pureza es mayor a la requerida (Fig. 28).
De igual manera el sistema fue excitado combinando escalones en el tiempo de purga y en la composición de alimentación.
La señal de salida también se presenta en la Fig. 28. Para esta prueba, la pureza controlada presenta mayor oscilación que en las otras pruebas y ocurre la caída más grande de la pureza, pero en un tiempo muy corto; por otro lado, en esta prueba se logra un menor tiempo de establecimiento, ya que el nuevo estado pseudo-estacionario se alcanza en 61 ciclos, contra 161 que se requieren en la primera prueba con perturbaciones simultaneas.
Una observación común en todas las pruebas es que la pureza del etanol en la salida, una vez restablecido el estado pseudo-estacionario tiene una pequeña desviación con respecto a la referencia, a diferencia de las pruebas con una sola perturbación; sin embargo, la desviación es todavía muy pequeña, alrededor de 0.001 fracción mol.
En la Fig. 28 se aprecian bien estas desviaciones debido a la ampliación de la imagen en un rango muy pequeño de composiciones.
La desviación más grande (vista a las 56 horas de simulación) se produce para la primera prueba (cambio combinado de la temperatura de alimentación y del tiempo de purga), mientras que la menor desviación se produce para la tercera prueba (cambio combinado de la composición de alimentación y del tiempo de purga).
Por otro lado, como es de esperarse, el cambio del flujo de alimentación producido como acción de control es hacia la reducción del flujo de alimentación y por lo tanto del flujo de producción, pero para estas pruebas el flujo no disminuyo más allá de 480 kmol/hr (siendo 512 kmol/hr el flujo nominal). La señal de entrada para todos los casos se muestra en la Fig. 29. La segunda prueba (cambios en la composición y temperatura de alimentación) implica el mayor esfuerzo de control, mientras que la tercera prueba (cambios en la composición de alimentación y en el tiempo de purga) implica el menor esfuerzo de control.
Para la primera prueba, en la misma Fig. 29 se puede observar que la señal de entrada que se genera para lograr atenuar la perturbación, esta durante cerca de 20 horas, en la segunda prueba durante cerca de 14 horas y en la tercera prueba cerca de 12 horas, pero después oscila en diferentes grados hasta lograr una señal constante. Al final el controlador predictivo óptimo logra mantener la pureza deseada muy cerca del valor nominal en todos los casos.
La simulación del proceso en lazo abierto se presenta en la Fig. 30. Para los tres casos de simulación con perturbaciones simultaneas, la pureza decae hasta valores que difícilmente pueden cumplir los estándares de pureza. La diferencia entre la salida correspondiente a estos tres casos estudiados es mayor que la diferencia observada en la primera serie de pruebas con perturbaciones únicas en las entradas.
En la presente serie de pruebas, la primera que implica cambios en la temperatura de alimentación y en el tiempo de purga es la que produce una desviación mayor con respecto a las condiciones nominales. Con una sola perturbación, la pureza se mantuvo arriba del 95 %, en cambio, en pruebas con perturbaciones simultaneas, la pureza disminuyo hasta el 93%. Las simulaciones en lazo abierto permiten conocer el grado de influencia de las entradas en la pureza de etanol y proporciona una mejor idea de la eficacia del control.
El proceso en lazo cerrado presenta variaciones muy pequeñas con relación a la referencia. La fineza del control, sin embargo va a estar limitada por la eficacia del sensado de variables; sin embargo, el controlador predictivo óptimo diseñado tiene el potencial suficiente para lograr la regulación de la pureza de etanol en un proceso de adsorción por oscilaciones en presión con buena robustez ante perturbaciones.
5. Conclusiones y trabajos futuros
En este trabajo se comprobó que el modelo riguroso PSA configurado en el simulador Aspen-Adsim presenta resultados confiables porque la predicción con variaciones en el tiempo y espacio, las datos del proceso son comparables a los resultados presentados en [2,1]. El proceso PSA fue simulado con las mismas condiciones; entrada, dimensionamiento de las columnas y configuración de las válvulas y ciclo de operación. Otro aspecto importante de este trabajo fue el modelo reducido obtenido a partir de los datos de entrada y salida del modelo riguroso, se observó que captura las dinámicas importantes del modelo PSA al aplicarle diferentes entradas, obteniendo siempre un ajuste adecuado. Este Modelo reducido (Hammerstein-wiener) se utilizó para el diseño del controlador, y los resultados de la evaluación de su desempeño claramente demuestran los beneficios potenciales de la identificación del sistema representado con un modelo riguroso.
Parte importante de este trabajo se centra en la elección de la variable manipulada (entrada), la cual se tomó después de realizar un estudio paramétrico, esta variable permite obtener una pureza elevada con un número de ciclos comparable a las otras entradas y puede ser utilizada fácilmente con el mismo tiempo de muestreo que se usa en la plataforma MatLab/Simulink, en donde se calcula el control. Este hecho habilita la sincronización entre las plataformas de Aspen Adsorption y Simulink.
Por lo tanto los resultados importantes de este trabajo fueron:
■ El análisis de sensibilidad que se utilizó para conocer que variables presentan mayor efecto sobre la pureza obtenida.
■ El Modelo reducido identificado (Hammerstein-Wiener) que capturo las dinámicas importantes de modelo PSA, el cual toma en cuenta interacciones entre muchas variables y representa adecuadamente un proceso no lineal y fue utilizado para el diseño del controlador.
■ El controlador Predictivo Óptimo diseñado tiene un buen desempeño para seguimiento de trayectoria, permite acelerar cambios requeridos para mejorar la producción o calidad del producto. Con la prueba realizada se logró alcanzar y mantener sin mucho esfuerzo del controlador una pureza superior a la establecida por los estándares dictados por las principales normas internacionales. Así mismo este controlador presenta gran robustez ante diferentes perturbaciones logrando atenuarlas en un menor número de ciclos con desviaciones y oscilaciones que se producen tienen una amplitud muy reducida, de orden de 0.001 de fracción molar como máximo.
Así, como trabajos futuros se proponen los siguientes:
■ Un trabajo futuro que se propone es implementar un control MIMO que permita tener en cuenta más entradas y salidas para regular simultáneamente otras variables secundarias que pudieran convertir el sistema de control en uno más robusto ante perturbaciones múltiples y con variaciones más realistas.
■ El desarrollo de un observador de estado para estimar la composición de etanol en la salida es conveniente para una planta real, dados los tiempos de control y la dinámica lenta de la planta, así como el grado de desarrollo de equipos de medición de concentración y composición de mezclas. De esta forma, el diseño del control como se propone en este trabajo pudiera bien llevarse a la práctica, la estimación fuera de línea no representa un problema.