1. Introduction
Foam rubbers are considered as key material in many important industries, such as, avionics, aerospace, mechanics and automotive. As the uses of foam rubbery materials increases, the need of synthesizing high quality elastomers with exceptional physical properties also increases. Foam rubbers are a set of elastomers formed by decomposition of blowing agent and thermal curing of rubber base material in presence of many additives. These additives provide many enhancements to the mechanical and physical properties of the cured rubber [1-6]. The most important additives are the vulcanization agents, which form the cross-linking between the chains of rubber and increase the tensile strength and hardness [7-9], and blowing agents that thermally decompose and provide trapped gaseous phase hence decreasing rubber density. Moreover, the filter material serves as an enhancer of the mechanical properties. Some common additives like activators, accelerators and plasticizers are also used.
In response to this trend, we decided to study the effect of changing the concentration of azodicarbonamide foaming agent on the physical properties of both sulfur and peroxide cured Ethylene Propylene Diene Monomer (EPDM) foam rubber. We choose EPDM foam because of its great industrial importance and for its reliability in many everyday life products. Besides EPDM rubber has resistance against many environmental conditions such as oxygen, ozone, heat and irradiation [10-12]. We prepared a number of samples based on the recipes given by previous works on EBDM foam with different ingredients concentrations [13,16]. We also applied tensile, compression and swelling American Society for Testing and Materials (ASTM), standard tests on the prepared samples.
2. Experimental setup
To study the effect of the foaming agent on the mechanical properties of sulfur and peroxide cured EPDM rubber, we prepared two different master batches of EPDM samples with different concentration of azodicarbonamide as foaming agent. The first batch is made from sulfur cured EPDM and the second one is made fromperoxide cured EPDM. The ingredients of samples are blended at room temperature on two-roll mill of 0.3 m length and radius 0.15 m diameter. The rotation rate of slow roll and gear ratio are 18 rpm and 1:4 respectively. Table I shows the ingredients of the prepared samples and the order of addition. After 24 hours, the sample was vulcanized and molded at temperature 150°C and pressure 15 MPa for 30 min.
Table I Ingredients of the prepared samples of sulfur and peroxide cured EPDM foamed rubber.
Substance | Ingredients (phr)a | ||||||||
Sulfur Cured EPDM Batch | Peroxide Cured EPDM Batch | ||||||||
Sample ES0 | Sample ES5 | Sample ES10 | Sample ES15 | Sample EP0 | Sample EP5 | Sample EP10 | Sample EP15 | ||
EPDM | 100 | 100 | 100 | 100 | 100 | 100 | 100 | 100 | |
Stearic acid | 2 | 2 | 2 | 2 | 2 | 2 | 2 | 2 | |
ZnO | 5 | 5 | 5 | 5 | 5 | 5 | 5 | 5 | |
Paraffin Oil | 20 | 20 | 20 | 20 | 20 | 20 | 20 | 20 | |
Silica | 20 | 20 | 20 | 20 | 20 | 20 | 20 | 20 | |
MBTSb | 2 | 2 | 2 | 2 | 2 | 2 | 2 | 2 | |
Sulfur | 3 | 3 | 3 | 3 | 0 | 0 | 0 | 0 | |
DCPc | 0 | 0 | 0 | 0 | 3 | 3 | 3 | 3 | |
ADC/Kd | 0 | 5 | 10 | 15 | 0 | 5 | 10 | 15 |
aparts per hundred parts of rubber by weight.
bDibenzothiazyl disulfide.
cDicumyl peroxide.
dAzodicarbonamide.
The samples were prepared in three standard forms: a) 0.2 cm thick standard Die-D cut dumbbell shape strips for tensile test, b) 1.3 cm thickness x 3 cm diameter disks for compression, and c) 5 x 2.5 x 0.2 cm sheets for swelling test. The densities of samples are mentioned in Table II.
Table II The measured densities of samples of sulfur and peroxide cured EPDM foamed rubber.
Sample name | ρ(Kg/m3) | Sample name | ρ(Kg/m3) |
ES 0 | 1048±4 | EP 0 | 965±4 |
ES 5 | 590±3 | EP 5 | 560±3 |
ES 10 | 570±3 | EP 10 | 543±3 |
ES 15 | 544±3 | EP 15 | 519±3 |
Three standard tests were applied to the samples [17-18], which were shelf aged for 48 hours, to investigate their mechanical properties. These tests are according to ASTM standards number: D412-98a, D395-98 (method B) and D471-98e1 for measuring tensile strength, compression and swelling of rubber samples, respectively. For the Test D 412-98a, the samples were tested using a homemade standard tensile testing machine of the Polymer lab.
3. Results and discussion
Figure 1 shows that the true tensile strength of the sulfur cured EPDM is higher than that cured by peroxide at almost zero ADC/K, concentration. As the ADC/K concentration reaches 5 phr both EPDM types seemed to have the same value. At ADC/K concentrations of 10, and 15 phr, the value of sulfur cured EPDM lead once again, as shown in Fig. 1a. The true strain at break of both EPDM types versus ADC/K concentration was similar to that of the true strength as shown in Fig. 1b.
Tensile tests reveal that the true stress-strain curve of the samples shows an explicit superiority of initial elastic modulus (Young’s modulus) for zero concentration ADC/K peroxide cured EBDM over all samples, this is due to the strong carbon-carbon bond strength compared to the weaker sulfur -carbon bond [15]. The values of elastic modulus of samples are presented in Table III. On the contrary, the break point of the zero concentration ADC/K sulfur cured EBDM sample was the highest among all samples, as shown at Fig. 2a.
Table III The elastic modulus of samples of sulfur and peroxide cured EPDM foamed rubber.
Sample name | E(MPa) | Sample name | E(MPa) |
ES 0 | 1.87 | EP 0 | 3.10 |
ES 5 | 1.56 | EP 5 | 1.87 |
ES 10 | 1.51 | EP 10 | 1.74 |
ES 15 | 1.51 | EP 15 | 1.62 |
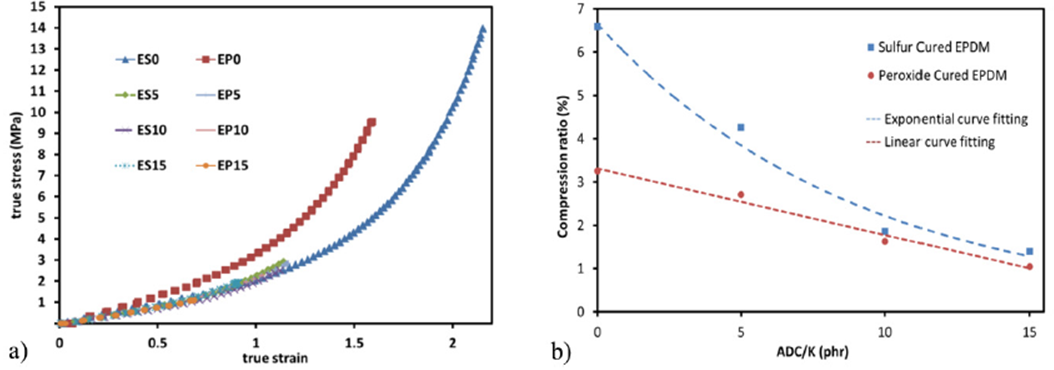
Figure 2 a) True stress-strain curve for all samples. b) Compression ratio versus ADC concentration for both sulfur and peroxide cured samples.
Compression test shows an exponential behavior of compression ratio for sulfur cured EBDM samples with ADC/K concentration. On the contrary, for Peroxide cured EBDM samples, a linear behavior of compression ratio with ADC/K concentration is observed, as shown in Fig. 2b.
For swelling test, Xylene ((CH3)2 C6H4) was used as solvent for both sulfur and peroxide cured samples. As shown in Fig. 3, tests revealed that the degree of swelling for sulfur cured EBDM samples was higher than that of peroxide cured samples. To model the swelling behavior of the tested sample versus time, we applied an empirical fitting equation used by Kumnuantip and Sombatsompop [19] in which the degree of swelling Mt is given by Eq. (1):
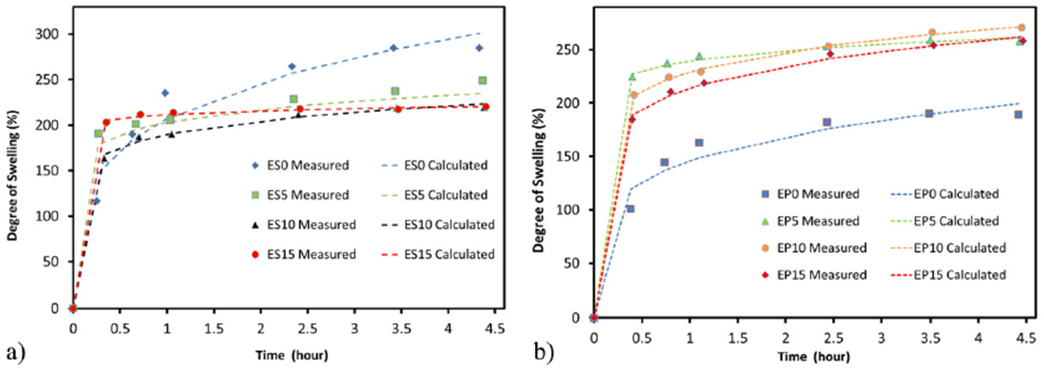
Figure 3 Measured and calculated percent change in samples mass versus time for a) sulfur cured EBDM samples, b) peroxide cured EBDM samples.
Where W0 is the dry initial weight and Wt is the swollen weight after time t, M∞ is the degree of swelling at saturation, K and n are arbitrary fitting parameters determined by the least squares method. Figure 4 shows the numerical values of K and n that matched the swelling behavior of all ADC/k sample concentrations.
It is worth mentioning that at ADC/k concentration of 10%, the value of k for sulfur cured samples intersected with that of the peroxide cured samples and an inflection of slopes occurred. The same results were obtained for the value of n accounting for the small differences between both sample types.
4. Conclusion
The study reveals an strong dependence of the investigated mechanical properties on the mentioned foaming agents concentration, as discussed by other relevant works. A 15 phr of ACD/K enhances the compressive properties of the samples, especially for peroxide cured EPDM, and decreases the degree of swelling for sulfur cured EPDM. The elastic modulus of peroxide cured EPDM is larger than the sulfur cured EPDM one for each same concentration of ACD/K .The obtained results represent a helpful boost for the understanding of foam rubber based industrial applications.