Introducción
Los residuos constituyen hoy en día una preocupación a nivel mundial, entre ellos tenemos el vidrio reciclado. El cual es un producto que no tiene salida en el mercado y tarda mucho tiempo en degradarse, lo que se convierte en un problema ambiental de suma importancia, ya que a diario se generan desechos, convirtiéndose en un gran problema a nivel internacional. En un informe del Banco Mundial “se analiza el panorama de administración de los desperdicios sólidos hasta 2050 en el mundo, se reporta que, si no se actúa urgentemente, la generación de residuos aumentará en un 70% debido al rápido desarrollo urbano y el crecimiento social” [5].
“La industria del reciclaje de vidrio, permite a los recolectores y empresas relacionadas con esta actividad, la oportunidad de mejorar su economía actual a través del aprovechamiento este recurso, el cual se encuentra presente entre los principales residuos sólidos de su localidad” [10].
En la actualidad, las construcciones son las que producen mayor desarrollo en nuestro país, sin embargo, hay una gran cantidad de construcciones que están generando una sobreproducción de recursos no degradables, lo que implica una contaminación de avance rápido en el Perú. Se tiene conocimiento que se ha explorado diversos materiales que pueden sustituir en porcentajes a la mezcla del concreto como respuesta para elevar la resistencia del mismo, pero a pesar de ello, la mayor parte daña y contamina el medio ambiente. “En la ciudad de Huaraz se puede observar gran contaminación de las calles, lo que implica un problema difícil de controlar por parte de las autoridades a causa del desuso de vidrio y su bajo costo, lo que hace más fácil reemplazar el material que reusarlo” [6].
El vidrio cuenta con propiedades favorables para la construcción por ser una materia tenaz a la compresión, así como también las conchas de abanico el cual está conformada de caparazones de carbonato cálcico, llegando a ser materiales no nocivos para el concreto y con características similares al agregado convencional, considerándolos como componentes alternativos para elaborar concreto.
Debido a la problemática se formuló la siguiente pregunta ¿Cuál es la influencia de la incorporación de vidrio pulverizado y conchas de abanico calcinadas en la resistencia a la comprensión del concreto f’c=210 kg/cm2? El objetivo general es determinar la influencia de la incorporación de vidrio pulverizado y conchas de abanico calcinadas en la resistencia a la comprensión de concreto f’c=210 kg/cm2. Los objetivos específicos son:
Determinar las características del vidrio pulverizado y las conchas de abanico calcinadas mediante fluorescencia de rayos x.
Realizar el diseño de la mezcla de un concreto con agregado convencional, y con adición del vidrio pulverizado y conchas de abanico calcinadas de una resistencia de f'c=210 kg/cm2.
Analizar la resistencia a la comprensión de la mezcla de concreto con la incorporación de vidrio pulverizado y conchas de abanico calcinadas con el concreto patrón f’c=210 kg/cm2.
Dentro de la hipótesis se concluyó que la incorporación de vidrio pulverizado y conchas de abanico calcinadas mejora la resistencia a la comprensión de concreto f’c=210 kg/cm2; así como en las hipótesis específicas podemos observar que la composición química del vidrio pulverizado y las conchas de abanico calcinadas mediante fluorescencia de rayos x tienen características similares, con el porcentaje añadido de vidrio pulverizado y conchas de abanico calcinadas se logrará la combinación más práctica con mayor eficiencia en los procesos constructivos y referente a la mezcla diseñada con el vidrio pulverizado y conchas de abanico calcinadas, ello aumentará la resistencia a la comprensión del concreto con respecto al concreto base.
Metodología
El proyecto de investigación es del tipo aplicada, porque se busca poner en práctica los conocimientos para adaptarlos directamente a los diversos problemas que aqueja a la sociedad respecto al uso de un determinado porcentaje de vidrio pulverizado y conchas de abanico calcinadas como adición al concreto, con el objetivo de aplicar una mejor determinación en la elección de un mejor diseño [8]. El diseño es experimental por ser un proceso en la cual se va, a someter al concreto a diversas condiciones y tratamientos, con el fin de examinar los efectos, o las reacciones que estas producen [2].
Tiene un enfoque cuantitativo porque recolecta y analiza datos con el fin de contestar preguntas y probar hipótesis, la investigación cuantitativa toma una forma estructural con el fin de recopilar y analizar datos obtenidos, lo que indica el uso de diversas herramientas informáticas, estadísticos y matemáticos, esto ayudará a obtener resultados. Su propósito es de medir el problema y ver qué tan propagado se encuentra, por medio de la búsqueda de resultados proyectados a una determinada producción [1].
La población serán todas las probetas de concreto que se pueda elaborar, puesto que la población a ser estudiada es un grupo de casos, se encuentra limitado, pero es accesible, sirve de referencia para elegir la muestra [3].
La muestra estuvo integrada por una cantidad de 18 testigos, utilizándose la totalidad de ellos, 9 probetas de concreto patrón y 9 probetas de concreto con adición de vidrio pulverizado y conchas de abanico calcinadas, en un 2% cada uno. El muestreo en esta investigación es no probabilístico porque al seleccionar los testigos de concreto no dependen de probabilidades.
La principal herramienta para la recolección de datos fue la guía de observación, los ensayos de fluorescencia para el vidrio pulverizado y las conchas de abanico calcinadas.
En este sentido primero se efectuó la recolección de muestras del vidrio en la ciudad de Huaraz y las conchas de abanico del botadero de Huarmey. Después se trituró el vidrio en un mortero y calcinó las conchas de abanico en un horno para luego molerlas, y así obtener moléculas de conchas de abanico calcinadas. Para los ensayos de fluorescencia se mandaron las muestras de vidrio pulverizado y conchas de abanico calcinadas a un laboratorio, con el fin de ver la composición química elemental de cada una de las muestras e identificar los elementos que contienen y las cuales aportarán para la resistencia del concreto.
También se ejecutó el diseño de mezcla por el método ACI con los agregados de la cantera de Tacllan, posteriormente se hicieron las 18 briquetas, 9 probetas patrón y 9 probetas con la muestra de vidrio pulverizado y conchas de abanico calcinadas, basándose en la norma E-060.
Finalmente se ejecutó el ensayo de compresión simple de las probetas a los 7, 14 y 28 días tanto para el concreto patrón y la muestra, para evaluar los resultados obtenidos y ser representados en gráficos comparativos.
Resultados y discusión
Se puede observar que la resistencia a la comprensión de la muestra al cual se añadió vidrio pulverizado en un 2% y conchas de abanico en el mismo porcentaje, resulta favorable para el concreto, puesto que las cifras que arrojan en el laboratorio nos muestran que a los 28 días es más favorable respecto a los 7 y 14 días, comparando a la resistencia del concreto patrón, en los 28 días el concreto patrón llego a tener una resistencia de 295.4 kg/cm2, mientras que el concreto con adición de vidrio pulverizado y conchas de abanico calcinadas mostraron como resultado una resistencia de 306.1kg/cm2, guardando relación con lo que indica [7], porque en los resultados de su investigación muestran el incremento en la resistencia a la comprensión del concreto al ir añadiendo los porcentajes de vidrio molido, concluyendo que es viable emplear estos materiales, porque cada uno de estos cumplió con la resistencia del diseño base.
La tabla 1 y la figura 1 , muestra que la mezcla diseñada a la cual se añadió vidrio pulverizado y conchas de abanico calcinadas, a los 28 días, es más favorable que al de los 7 y 14 días respecto al concreto patrón, mostrando una diferencia de f´c=10.7 kg/cm2 entre el concreto patrón, ello nos indica que al emplear vidrio y conchas de abanico mejoran la resistencia a la comprensión del concreto.
Tabla 1 Comparación de la resistencia a la comprensión promedio.
CONCRETO DE RESISTENCIA 210 KG/CM2 | EDAD | KG/CM2 |
Concreto patrón | 7 | 194.5 |
Ensayo de mezcla de concreto con 2% de vidrio pulverizado y 2% de conchas de abanico calcinadas | 7 | 196.5 |
Concreto patrón | 14 | 237.8 |
Ensayo de mezcla de concreto con 2% de vidrio pulverizado y 2% de conchas de abanico calcinadas | 14 | 238.9 |
Concreto patrón | 28 | 295.4 |
Ensayo de mezcla de concreto con 2% de vidrio pulverizado y 2% de conchas de abanico calcinadas | 28 | 306.1 |
Fuente: Resultados obtenidos en el laboratorio NICOLES HYDGEOSTRUCT S.A.C
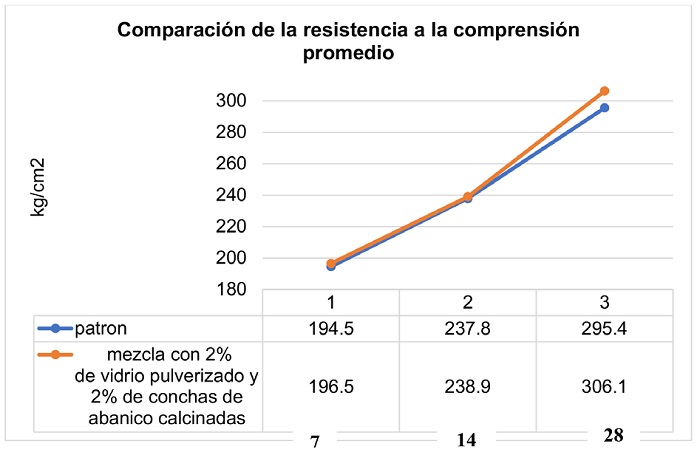
Fuente: Elaboración propia
Figura 1 Resistencia a la comprensión con adición de vidrio pulverizado y conchas de abanico calcinadas.
Las características del vidrio pulverizado y las conchas de abanico calcinadas mediante fluorescencia de rayos x, mostraron los siguientes resultados:
En la tabla 2 y la figura 2 se observa que los elementos más significativos que conforman al vidrio pulverizado son el silicio, sodio y calcio mientras que las conchas de abanico calcinadas están compuestas en mayor cantidad por el calcio, hierro y potasio, apreciando que el calcio que compone las conchas de abanico calcinadas, supera al calcio que compone el vidrio pulverizado en una diferencia de 86.854%.
Tabla 2 Composición química elemental del vidrio pulverizado y conchas de abanico calcinadas, analizado en el laboratorio a través del método de fluorescencia de rayos x.
COMPOSICIÓN QUÍMICA DEL VIDRIO PULVERIZADO | COMPOSICIÓN QUÍMICA DE LAS CONCHAS DE ABANICO CALCINADAS | MÉTODO UTILIZADO | ||
COMPOSICIÓN QUÍMICA | RESULTADOS, %⁽¹⁾ | COMPOSICIÓN QUÍMICA | RESULTADOS, %⁽¹⁾ | |
Silicio, Si | 47.074 | Silicio, Si | 0.363 | Espectrometría de florescencia de rayos X de energía dispersiva ⁽²⁾ |
Sodio, Na | 35.218 | Sodio, Na | 0.000 | |
Calcio, Ca | 10.449 | Calcio, Ca | 97.303 | |
Aluminio, Al | 3.443 | Aluminio, Al | 0.000 | |
Magnesio, Mg | 2.516 | Magnesio, Mg | 0.000 | |
Potasio, K | 0.432 | Potasio, K | 0.499 | |
Azufre, S | 0.408 | Azufre, S | 0.026 | |
Hierro, Fe | 0.307 | Hierro, Fe | 1.066 | |
Cromo, Cr | 0.061 | Cromo, Cr | 0.000 | |
Fosforo, P | 0.036 | Fosforo, P | 0.000 | |
Circonio, Zr | 0.033 | Circonio, Zr | 0.019 | |
Estroncio, Sr | 0.023 | Estroncio, Sr | 0.490 |
Fuente: Resultados obtenidos en el laboratorio LABICER

Fuente: Elaboración propia
Figura 2 Comparación entre vidrio pulverizado y conchas de abanico calcinadas.
En la tabla 3 y la figura 3, se aprecia que ambas muestras contienen óxido de calcio CaO, en el vidrio encontramos un 7.976% y en las conchas de abanico un 96.815%, dando una diferencia de 88.839%, mientras tanto en el óxido de silicio se aprecia que el vidrio contiene un 65.157% y las conchas de abanico contiene un 0.681%, dando una diferencia de 64.476%.
Tabla 3 Muestra del análisis químico expresado en óxidos del vidrio pulverizado y de las conchas de abanico calcinadas.
DESCRIPCION | VIDRIO PULVERIZADO | CONCHAS DE ABANICO | |
1 | óxido de silicio, SIO2 | 65.157 | 0.681 |
2 | óxido de sodio, Na2O | 20.037 | 0.000 |
3 | óxido de calcio, CaO | 7.976 | 96.815 |
4 | óxido de aluminio, Al2O3 | 3.845 | 0.000 |
5 | óxido de magnesio, MgO | 1.743 | 0.000 |
6 | óxido de azufre, SO3 | 0.587 | 0.552 |
7 | óxido de potasio, K2O | 0.289 | 0.491 |
8 | óxido de hierro, Fe2O3 | 0.231 | 1.006 |
9 | óxido de cromo, Cr203 | 0.046 | 0.000 |
10 | óxido de fosforo, P2O5 | 0.045 | 0.000 |
11 | óxido de circonio, ZrO2 | 0.027 | 0.019 |
12 | óxido de estroncio, SrO | 0.016 | 0.435 |
Fuente: Resultados obtenidos en el laboratorio LABICER

Fuente: elaboración propia
Figura 3 Comparación de vidrio pulverizado y conchas de abanico calcinadas expresados en óxidos.
La tabla 4, tabla 5, tabla 6 y la tabla 7 nos detalla la cantidad de material a utilizar para la obtención del diseño de la mezcla de un concreto, con agregado convencional y con adición del vidrio pulverizado y conchas de abanico calcinadas, de una resistencia de f'c 210 kg/cm2, basándose en la medida de la probeta mostrada en la figura 4.
Tabla 4 Peso de materiales por kg/m3
Descripción | Cemento (kg/m3) | A. fino (kg/m3) | A. grueso (kg/m3) | Agua (lt/bolsa) |
Seco | 475.74 | 833.85 | 931.53 | 216 |
Húmedo | 475.74 | 869.16 | 940.98 | 169.64 |
Por cada bolsa | 1 | 77.65 | 84.06 | 15.15 |
Fuente: Elaboración propia
Tabla 5 Peso de materiales por bolsa
PROPORCIONAMIENTO EN PESO | |||
42.5 | 77.65 | 84.06 | 15.15 |
C | AF | AG | AGUA |
BLS | KG | KG | KG |
Fuente: Elaboración propia
Tabla 6 Proporción de materiales por 9 probetas de la muestra patrón
PARA 9 PROBETAS DEL DISEÑO | ||
v=pixr2xh | 0.005301 | m3 |
v=0.005301*9 | 0.047709 | m3 |
v=1.2*0.047709 | 0.057251 | m3 |
cemento=0.0572508*475.74 | 27.2365 | kg |
Af=0.0572508*869.16 | 49.76011 | kg |
Ag=0.0572508*940.98 | 53.87186 | kg |
Agua efectiva=0.047709*169.64 | 8.093354 | lt |
SUMA | 138.962 | kg |
Fuente: Elaboración propia
Tabla 7 Proporción de materiales por probeta, añadiendo 2% de vidrio pulverizado y 2% de conchas de abanico calcinadas
PARA 9 PROBETAS DEL DISEÑO | Vidrio pulverizado y conchas de abanico calcinadas | ||||||
v=pixr2xh | 0.005301 | m3 | |||||
v=0.005301*9 | 0.047709 | m3 | 2% vidrio pulverizado | 2.779 | |||
v=1.2*0.047709 | 0.057251 | m3 | 2% conchas de abanico calcinadas | 2.779 | |||
cemento=0.0572508*475.74 | 27.2365 | kg | SUMATORIA | 5.558 | |||
Af=0.0572508*869.16 | 49.76011 | kg | |||||
Ag=0.0572508*940.98 | 53.87186 | kg | |||||
Agua efectiva=0.047709*169.64 | 8.093354 | lt | |||||
SUMA | 138.962 | kg |
Fuente: Elaboración propia
Para realizar la mezcla de 9 probetas se usarán: cemento 27.2365 kg, agregado grueso 53.87 kg, agregado fino 49.76 kg, agua 8.09 kg; de los cuales para las 9 probetas que se emplearán como muestras, se añadirá el vidrio pulverizado al 2% que representan un total de 2.779 kg, lo mismo para las conchas de abanico calcinadas se usarán 2.779 kg.
En la tabla 8, se muestra el cronograma para el análisis de la resistencia y en la figura 5 muestra la comparación de la resistencia a la comprensión en las edades 7, 14 y 28 días; mostrando mínima diferencia entre el concreto patrón y el concreto añadido vidrio pulverizado y conchas de abanico, a los 7 y 14 días en 1 kg/cm2 y 1.1 kg/cm2 respectivamente, mientras que en los 28 días la diferencia es de 10.7 kg/cm2, esto nos indica que la resistencia a la comprensión da mejores resultados a los 28 días de curado.
Tabla 8 Cronograma para el análisis de la resistencia
DESCRIPCION | CANTIDAD DE MUESTRAS | FECHA | EDAD EN DIAS | |
ELABORACION | ROTURA | |||
Ensayo de mezcla de concreto patrón | 3 | 03/09/2022 | 10/09/2022 | 7 |
Ensayo de mezcla de concreto con 2% de vidrio pulverizado y 2% de conchas de abanico calcinadas | 3 | 03/09/2022 | 10/09/2022 | 7 |
Ensayo de mezcla de concreto patrón | 3 | 03/09/2022 | 17/09/2022 | 14 |
Ensayo de mezcla de concreto con 2% de vidrio pulverizado y 2% de conchas de abanico calcinadas | 3 | 03/09/2022 | 17/09/2022 | 14 |
Ensayo de mezcla de concreto patrón | 3 | 03/09/2022 | 01/10/2022 | 28 |
Ensayo de mezcla de concreto con 2% de vidrio pulverizado y 2% de conchas de abanico calcinadas | 3 | 03/09/2022 | 01/10/2022 | 28 |
Fuente: Elaboración propia
Conclusiones
La resistencia a la comprensión del concreto f’c 210 kg/cm2, incorporando vidrio pulverizado y conchas de abanico calcinadas a los 28 días, fue de 306.1 kg/cm2 con respecto al concreto patrón 294.7 kg/cm2, ello nos indica que el vidrio y las conchas de abanico pueden ser incluidas en la elaboración del concreto, al ser muy favorables para obtener un concreto de mayor calidad.
Los compuestos químicos que predominan en las conchas de abanico calcinadas son el calcio en un 97.303% y el hierro 1.066%, mientras que los compuestos químicos que predominan en mayor cantidad en el vidrio pulverizado son : el silicio con un 47.074%, el sodio 35.218% y el calcio 10.449%, indicando que el compuesto químico que predomina en ambas muestras es el calcio.
Se concluye que a través del método A.C.I 211.1 basado en la norma ASTM C33 se determinaron las proporciones de los materiales como son (1:1.98:2.07/15.15); para el cemento, agregado fino, agregado grueso y el agua resaltando que al añadir el vidrio pulverizado al 2% y conchas de abanico calcinadas al 2%, los resultados a los 7 días dieron un promedio de 196.5 kg/cm2, a los 14 días arrojo un resultado de 238.9 kg/cm2 y a los 28 días se obtuvo una f¨c máximo de 306.1 kg/cm2 en promedio, mostrando que el vidrio pulverizado y las conchas de abanico añaden un 45.7% de resistencia a la comprensión del concreto, no obstante a las 7 y 14 días de curado también tienden a ser superiores que el concreto patrón aunque en menor porcentaje.