1. Introducción
Los primeros estudios sobre fatiga fueron documentados por Albert [1] desde 1937, y desde entonces hasta la actualidad es un tema de gran interés entre la comunidad científica. Todo este interés tiene su motivación en el hecho de que el fenómeno de fatiga es común en las fallas de materiales. Zerbst et al [2] reportaron que entre el 80 y el 90% de los casos registrados de fallas estructurales tienen a la fatiga como la causa. Esto se manifiesta en estructuras y componentes de máquinas, usadas en áreas como las ingenierías aeroespacial, civil y mecánica [3]. La mayoría de los componentes mecánicos que se someten a cargas cíclicas son susceptibles a desarrollar grietas y eventualmente causar fallas por fractura, que a menudo ocurren sin previo aviso y con consecuencias catastróficas [1].
En la fatiga se desarrollan esfuerzos cíclicos a través del tiempo, que degradan el material hasta el punto en que las pequeñas grietas se nuclean. Después la grieta comienza a propagarse y termina en la ruptura final de la pieza [4]. El estudio de la propagación de grietas por fatiga es importante, debido que de ahí depende la seguridad de las partes mecánicas y estructurales, para evitar accidentes que conducen a pérdidas económicas, humanas y ambientales.
2. Antecedentes
Paris y Erdogan [5] fueron los primeros investigadores que utilizaron el factor de intensidad de esfuerzos para determinar una relación entre la condición de carga, la longitud de grieta y la velocidad de propagación. La ley de París es el tratamiento de resultados de muchos datos experimentales en el marco de la solución elástica del problema de propagación de grietas. Como consecuencia, esta ley no explica la naturaleza física del proceso de propagación de grietas en los metales e inicia muchas discusiones científicas e intentos de derivar una descripción alternativa de la ley de propagación de grietas.
Recientemente, se han propuesto enfoques experimentales para evaluar la propagación de grietas [6,7], principalmente a partir del desarrollo de las técnicas modernas de medición de la temperatura, la cual, como se reporta ampliamente en la literatura [8-12], se puede correlacionar con la propagación de grieta por fatiga debido a que una gran variedad de estudios demuestran que, en la mayoría de los materiales metálicos, la energía de histéresis por deformación plástica se convierte en calor, como se reportó en el trabajo de Meneghetti et al [13]. Por lo anterior, se considera que la mayor parte de la energía mecánica de entrada se disipa en forma de calor y eleva la temperatura del material y, en el caso particular de la etapa de propagación de grieta, existe una distribución de temperatura que alcanza su valor máximo en la vecindad de la punta de la grieta, como lo demostraron Pandey y Chand [14].
Actualmente es posible encontrar trabajos como el de Meneghetti y Ricotta [15], quienes, a través de la medición de la temperatura en probetas sometidas a fatiga, demostraron que existe disipación de calor en la punta de la grieta, por lo que la medición de temperatura por termografía se ha aplicado ampliamente en la investigación del comportamiento a fatiga en los últimos años [16-18].
Resultados de trabajos recientes demuestran que, a medida que crece la grieta, hay un aumento de la temperatura superficial de la probeta, lo cual plantea la necesidad de comprender los fenómenos físicos en la propagación de grietas por fatiga desde el punto de vista de la Termodinámica. Un ejemplo es el trabajo de Idris et al [19], quienes midieron simultáneamente la temperatura y la longitud de la grieta durante los ensayos de crecimiento de grietas por fatiga hasta la ruptura, bajo condiciones de carga de amplitud constante y variable. Hajshirmohammadi y Khonsari [20] reportaron un modelo matemático para determinar la tasa de propagación de grietas, el cual considera la temperatura superficial de la probeta como variable.
Por lo anterior, en el presente estudio se propone la medición de la temperatura en la vecindad de la punta de la grieta durante la propagación de la grieta por fatiga bajo una carga de modo I de amplitud constante para un acero AISI 1018 bajo condiciones de esfuerzo plano para correlacionar el comportamiento del crecimiento de grieta y la evolución de la temperatura en la punta de la grieta.
3. Metodología
Se realizaron 2 ensayos experimentales de crecimiento de grieta por fatiga bajo la norma ASTM E647 [21], en la que menciona que se debe realizar los ensayos en dos etapas: preagrietamiento y propagación de grietas. En la etapa de preagrietamiento, la norma ASTM E647 [21] especifica que la longitud inicial de pregrieta corresponde a la longitud del centro del orificio de carga hasta la punta de la muesca (10 mm) que se muestra en la Figura 1. En la etapa de propagación de grieta, la longitud de grieta inicial fue de 11.3 mm, que corresponde a la suma de la longitud inicial de pregrieta y el tamaño de la pregrieta. A partir de 11.3 mm se midieron simultáneamente la longitud de grieta y la temperatura en la punta de la grieta en una probeta de tensión compacta (CT, por sus siglas en inglés). Se realizaron intervalos de medición de la longitud de grieta ∆α de 0.033 mm, debido a que la norma ASTM E647 [21] recomienda que para probetas CT de 40 mm de anchura (w), los intervalos de medición deben ser menor o igual a 1.6 mm. La temperatura se registró en cada intervalo de longitud de grieta con su respectivo número de ciclos.
3.1 Materiales y equipo
El material utilizado en este estudio es un acero AISI 1018. Este tipo de acero es muy usado en construcción de puentes, tuberías y edificios [22]. El acero es de tipo estructural y de bajo contenido de carbono. La composición química del material se encuentra en la Tabla 1. Las propiedades mecánicas y cíclicas de dicho acero se presentan en la Tabla 2.
Tabla 1 Composición química del acero AISI 1018 [23]
% C | % Mn | % P | % S |
0.15 - 0.20 | 0.60 - 0.90 | 0.040 | 0.05 |
Tabla 2 Propiedades del acero AISI 1018 [24].
Módulo de elasticidad (GPa) | 200 |
Relación de Poisson | 0.29 |
Densidad (kg/m3) | 7850 |
Esfuerzo de fluencia (MPa) | 386 |
Esfuerzo último (MPa) | 634 |
Las muestras de tensión compacta (CT) se obtuvieron de una placa de acero AISI 1018 de medidas 10 x 8 x 3/8 de pulgadas, la cual se maquinó para dimensionarla de acuerdo a la norma ASTM E647 [21] para obtener las dimensiones que se muestran en la Figura 1. Se seleccionó la muesca en V y se maquinó mediante el proceso de fresado.
Con el fin de realizar una observación adecuada del crecimiento de la grieta en las probetas, una de las caras de las probetas se pulió en acabado espejo. En la otra cara se realizó un pulido menos fino, con la finalidad de que la rugosidad de la superficie no afectara la trayectoria de la grieta, durante la propagación de la misma. El desbaste se realizó con papeles abrasivos de carburo de silicio, de tamaño de grano grueso a un tamaño de grano muy fino (de lija #100 hasta lija #2000). Se utilizó agua como medio de lubricación y el pulido se realizó de forma manual. La cara menos pulida se recubrió con una fina capa de pintura negra rociada en la superficie para aumentar la emisividad térmica al valor conocido de 0.98.
Para garantizar una punta de grieta aguda, fue necesario generar un preagrietamiento sobre la entalla. La pregrieta se generó mediante carga cíclica de tensión-tensión. El manual ASM [25] menciona que para ensayos de tensión-tensión, la relación de carga debe ser mayor a 0, por lo que recomienda una relación de 0.1. También hace mención que las frecuencias de forma de onda sinusoidal son más fáciles de controlar en máquinas de ensayo equipadas con sistemas servo hidráulicos. Las cargas aplicadas se propusieron en ciclos de carga sinusoidal con una frecuencia de 10 Hz y una relación de carga
Para el proceso de preagrietamiento, cada una de las probetas fue sometida a cargas cíclicas en la máquina universal MTS Landmark servo hidráulica de circuito cerrado (ver Figura 2a), con una celda de carga de 100 kN de capacidad (ver Figura 2b), en modo de control de carga en condiciones de amplitud de carga constante, ΔP. La sujeción de las probetas (CT) se realizó en mordazas tipo “clevis”, ajustando la altura de las mordazas con el controlador Flextest 40 de la máquina servo hidráulica. Los datos para preagrietamiento de cargas máxima, mínima y promedio, se introdujeron en una computadora mediante el software MTS TestSuite. Con un microscopio óptico Struers modelo PSM- 10, se ajustó el punto de observación en la punta de la muesca.

Figura 2 Configuración con termopares. a) Máquina universal MTS, b) Celda de carga, c) Mordaza, d) Carro, e) Microscopio, f) Ocular de medición, g) Lente de objetivo, h) Botón de lámpara LED, i) Termopar, j) Monitor del termopar.
La medición de la pregrieta se monitoreó con la regla graduada incorporada en el ocular de medición hasta que la pregrieta alcanzó 1.33 mm de longitud. La longitud final de la pregrieta fue determinada de acuerdo a las indicaciones que especifica la norma ASTM E647 en el numeral 8.3.2, en el cual se sugiere que el valor mínimo que debe tener la pre-grieta, es de 1 mm. Los datos de ensayo para la etapa de preagrietamiento, se muestran en la Tabla 3.
Tabla 3 Condiciones de carga de preagrietamiento.
Dato | Símbolo | Valor |
Carga máxima, kN | Pmáx | 6.56 |
Carga mínima, kN | Pmin | 0.656 |
Carga promedio, kN | Pprom | 3.609 |
Una vez que se finalizó el proceso de preagrietado, se realizaron los ensayos de propagación de las grietas. Se consideró usar la misma frecuencia de 10 Hz y una relación de carga R=0.1, debido a recomendaciones de la norma ASTM E647 [21]. El microscopio óptico se ajustó en la punta de la pregrieta generada, la cual fue la referencia de las mediciones para la etapa de propagación de grieta. Se registraron el número de ciclos cada 0.03 mm de avance de grieta. La prueba se consideró finalizada cuando la probeta se fracturó totalmente. Los datos de cargas máxima, mínima y promedio introducidos en la máquina de ensayos para la etapa de propagación de grieta, se muestran en la Tabla 4.
3.2 Medición de crecimiento de grieta
La medición de la grieta se realizó de manera visual (ver Figura 2). Se colocó el microscopio al frente de la muestra y con la lente de objetivo (ver Figura 2g) se realizaron observaciones con aumentos de 50x. El microscopio se desplazaba horizontalmente mediante un carro (ver Figura 2d) para seguir la trayectoria de la punta de grieta. A medida que se registraba cada avance de longitud de la grieta, también se consideraba el registro del número de ciclos.
3.2 Medición de temperatura de la grieta
La temperatura superficial de la muestra se midió a través de una cámara infrarroja marca Hti modelo HT-18 con resolución de 220 x 160 píxeles y sensibilidad térmica de 0.07 °C. La cámara infrarroja se instaló en la parte posterior de la probeta apoyada en un tripié (ver Figura 3d). El proceso de registro de temperatura se hizo en simultaneidad con el crecimiento de grieta mediante captura de imágenes.
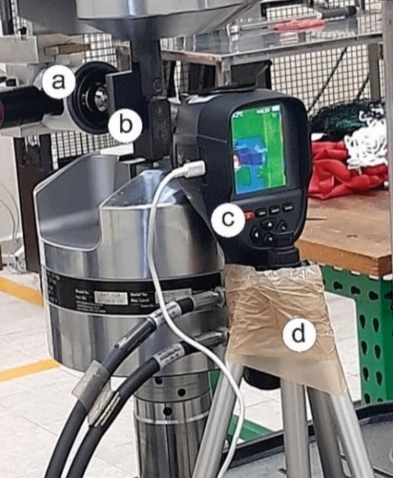
Figura 3 Configuración con cámara termográfica. a) Microscopio, b) Probeta, c) Cámara termográfica, d) Tripié.
En otra medición de temperatura, se colocaron termopares tipo K modelo Fluke 52 II (ver Figura 2i). Las terminales de los termopares se fijaron con cinta adhesiva laminar a 1.33 milímetros de la punta de la grieta y el valor de la temperatura se registraba en un monitor. El proceso de registro de temperatura se hizo en simultaneidad con el crecimiento de grieta.
4. Resultados
Después de concluir la prueba de propagación de grietas por fatiga, se notó una clara diferencia en la apariencia física en ciertas áreas superficiales de sección fracturada de la probeta (ver Figura 4). Se encontró que el área fracturada con condiciones de superficie lisa y plana (región a), mostró un crecimiento gradual de la grieta, que es la etapa de propagación de grieta por fatiga. En esta superficie fracturada, no se muestra ninguna marca de playa a simple vista en la región de crecimiento de grieta. Esto demostró, de acuerdo con la literatura [26-27], que las marcas de playa en la superficie de la fractura son invisibles cuando se usa la carga de amplitud constante, en comparación con cargas de amplitud variable, que son vistas a simple vista.

Figura 4 Aspecto de la superficie de fractura de las probetas CT. a) Región de propagación de grieta, b) Región de crecimiento inestable de grieta, c) Fractura repentina de la pieza.
El área fracturada con condiciones de superficie rugosa e irregular (región b), mostró un crecimiento de grieta inestable y puede caracterizarse como un crecimiento rápido de la longitud de la grieta. Cuando la pieza tiene una fractura repentina y completa (región c), se observó un desprendimiento irregular de material en los extremos del espesor de la probeta y la superficie mostró porosidad. La transición de crecimiento de grieta estable a inestable se puede distinguir notoriamente debido al tipo de superficie liso y rugoso.
En la Figura 5 se muestra la curva de longitud de grieta contra ciclos de fatiga (a-N) para el acero AISI 1018. Los datos experimentales de propagación de grietas por fatiga (ver Figura 5), muestran que la grieta inicialmente creció a un ritmo lento como se reporta en la literatura [5], y comenzó a acelerarse el crecimiento de grieta después de 150000 ciclos a partir de una longitud de 19 mm aproximadamente. La tasa de crecimiento de la grieta aumentó junto con la longitud de la grieta.
Los ciclos totales hasta la falla fueron en promedio de 174773 ciclos bajo las condiciones de carga mostrados en la Tabla 4. El punto final de la curva indica la fractura final de la probeta durante la prueba.
La curva de la temperatura respecto al número de ciclos mostrada en la Figura 6 se obtuvo a partir de los datos de termopares, y la cámara termográfica se usó para corroborar datos. La temperatura mostró un incremento lento y constante desde el inicio hasta los 150000 ciclos donde la probeta pasa la mayor parte de su vida de fatiga. Después de los 150000 ciclos, la temperatura aumentó continuamente hasta llegar a la fractura total de la muestra que corresponde 174773 ciclos. Este comportamiento en el incremento estable de temperatura es debido a un equilibrio entre la disipación de calor y la generación de energía por deformación plástica, que ha sido documentado por Meneghetti y Ricotta [15].
El incremento continuo de temperatura representa entre 5 al 10% de la vida de fatiga [28], ya que un aumento repentino de temperatura representa una pequeña cantidad de ciclos después de los 150000 ciclos. La temperatura registrada en la probeta fue en un inicio con una temperatura de 24.6 °C y finalizó con 29.2 °C. La diferencia entre las temperaturas inicial y final fue de 4.6 °C.
5. Discusión de resultados
En este estudio se encontró que la temperatura aumenta a medida que la grieta crece hasta la fractura final de la prueba (ver Figura 7). Esta información se puede utilizar para predecir el punto de transición entre el crecimiento estable e inestable de la longitud de grieta, y que se manifiesta en los incrementos de temperatura de la probeta.
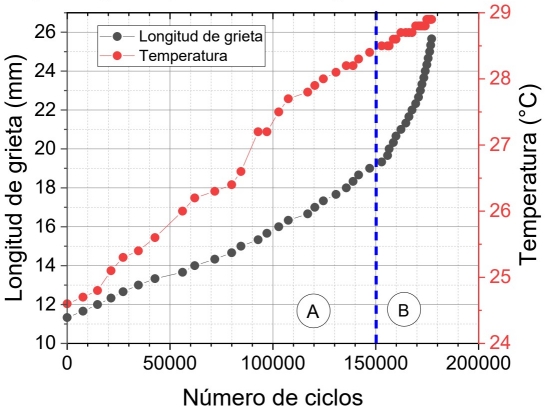
Figura 7 Comportamiento de la temperatura y la longitud de grieta durante el ensayo experimental. a) Región estable, b) Región inestable.
En la Figura 8 se muestra la relación del crecimiento de grieta con la temperatura de la superficie de la probeta, la cual revela que existe una relación exponencial desde la etapa de propagación de grieta hasta la fractura. Se observa una curva más pronunciada después de los 18 mm de longitud de grieta debido a la inestabilidad en su crecimiento. El modelo que se muestra en la ecuación (1), donde T representa la temperatura superficial de la probeta, y la longitud de grieta se expresa como α. El modelo se obtuvo mediante la técnica de regresión exponencial. Se determinó el coeficiente de correlación R 2 con un valor de 0.987 para establecer la correlación entre los resultados obtenidos en el presente modelo y los resultados del experimento.
La velocidad de propagación de grieta
La tasa de temperatura
De acuerdo al modelo presentado en la ecuación (1), la temperatura está relacionado con el crecimiento de grieta. También, la temperatura es una variable termodinámica que involucra la entropía, debido a que la fatiga es un proceso irreversible [30-32]. La temperatura y la entropía son variables que, al estar relacionados con la longitud de grieta, han sido incorporados en modelos de propagación de grietas [19-20] o en predicciones de vida a la fatiga reportado en la literatura [33-35].
6. Conclusiones
Se encontró un modelo que relaciona el comportamiento del crecimiento de grieta y la temperatura en la punta de la grieta, en la propagación de grietas por fatiga. Las pruebas de propagación de grietas por fatiga, realizadas en el acero de bajo carbono AISI 1018 con una relación de carga (R) de 0.1, muestran un aumento en la temperatura superficial de la probeta a medida que crece la grieta por fatiga cada 0.3 mm. El modelo predice la evolución completa de la temperatura durante el proceso de fatiga, incluido el aumento de la temperatura antes de la falla por fatiga.
La comparación de las predicciones del modelo con los resultados experimentales muestra una buena concordancia en la magnitud de la temperatura. Los resultados demuestran que la temperatura es una variable que se puede considerar en modelos de propagación de grietas, debido a su linealidad con respecto al incremento de longitud de grieta que existe exclusivamente en la etapa de crecimiento estable de la grieta.
Se utilizaron técnicas de medición de termopares y termografía para conocer mejor la naturaleza de la propagación de grietas, que demostró un ascenso de temperatura en cada intervalo de número de ciclos. Sin embargo, la dispersión de datos en la tasa de temperatura se debe a que se requiere de una mayor precisión en el equipo de medición de temperatura, por lo que se comenta que es un factor importante a considerar en este tipo de estudios.
Se presentó un aumento repentino de temperatura al final de la vida de fatiga, acompañado de la fractura total de la pieza. Este comportamiento se puede utilizar como una advertencia inmediata de una falla inminente, y puede ser útil, por ejemplo, para interrumpir el funcionamiento de la maquinaria o reemplazar piezas agrietadas en un proceso de mantenimiento, a fin de evitar fallas catastróficas.