Introduction
The automotive industry has a long trajectory in the implementation of strategies to foster quality, innovation, productivity, and lower costs. And Lean Manufacturing (LM) is an effective strategy to achieve that. It includes three elements: the tools, the philosophy, and principles; and the management (Vienazindiene and Ciarniene, 2013; Larteb, Haddout and Benhadou, 2015). Lean Manufacturing (LM), also known as Toyota Production System (TPS) has evolved along time, and it demonstrates that it is a system that provides better products at lower costs. It also allows employees at every level to face more challenges and have a fulfilled work (Womack et al., 2007; Durakovic et al., 2018).
According to Hosono, Page and Shimada (2020) lead companies in global value chains require suppliers to deliver high-quality inputs at competitive prices and implementing lean manufacturing can increase the competitiveness of a company (Chen et al., 2010). As Durakovic et al. (2018) mention: “…waste reduction and efficiency improvement are the main objectives of this initiative.” (p. 130).
The main concern of TPS is to respond to the needs of clients. It assumes that each client is different and has particular needs, so that mass production only causes, in the long run, high costs. In Ohno's words: “We are now unable to sell our products unless we think ourselves into the very hearts of our customers, each of whom has different concepts and tastes” (Ohno, 1988, p. XIV).
Lean manufacturing has been applied by many companies, there are many tools and techniques available; however, only in 10% of cases are results obtained that significantly boost the competitiveness of companies. (Vienazindiene and Ciarniene, 2013). On the other hand, many articles have been written about lean manufacturing; however, most of these analyze its implementation in developed countries, it is necessary to document the implementation process in developing countries (Marodin et al., 2016; Durakovi et al., 2018; Maware et al., 2021). Specially since these types of practices must be adapted to the context of each region. And through this article we want to contribute to this arena.
The objective of this article is to analyze the implementation of the Lean Manufacturing (LM) strategy in a multinational auto parts company located in León, Guanajuato through the reconstruction of its trajectory during the period 1997 to 2018. To do that, a qualitative research was carried out, longitudinal, through a case study. Field work research was performed in three moments: from August to September of 2012, from June to July of 2015, and April 2018; in-depth interviews were applied with blue-collar workers, front-line managers, mid-level managers as well as top-level managers.
We seek to contribute to the comprehension of the LM implementation in emerging countries. However, being a case study, the results only support the formulation of hypothetical assumptions and lines of research to be addressed in the future.
The article is organized as follows. In section I, a brief theoretical review is provided. In the second section and for contextual purposes, a brief description of the automotive industry in Guanajuato is made, given its relevance to the state's economy. Methodological design is presented in section III. Empirical results are offered and discussed in section IV. Finally, conclusions are presented.
I. A Brief Theoretical Review
The Toyota Production System (TPS) was implemented by Toyota after World War II, but it attracted attention until the first oil crisis in 1973. It combines the best features of craft production and mass production since its main purpose is to increase production efficiency by eliminating waste; it seeks to reduce costs, increase productivity, and provide a wide variety of products (Ohno, 1988; Womack, Jones and Ross, 2007). Toyota implemented this system in response to the mass-production model (Chen, Li and Shady, 2010). It focused on the continuous identification and elimination of waste, and it is also known as lean manufacturing1. Through the implementation of this system, Toyota was able to obtain remarkable results in indicators, such as, waste reduction, costs reduction and productivity increase (Sander et al., 2016). At the beginning TPS was based on two pillars: Just-in-time and autonomation (Ohno, 1988).
Lean manufacturing gained notoriety in the 1980s with the results of a research project conducted by Womack, Jones and Ross who found that the implementation of this system contributed to an increase in the firm’s competitiveness (Silva, Batalha, Stipkovik Filho et al. 2009). According to Shingo (2005), the basic concept of the TPS is the minus-cost principle. This methodology is a systematic approach to identify and eliminate waste through continuous improvement (Bhuiyan and Baghel, 2005). One important characteristic of this system is standardization, defined by Shingo (2005) as: “… in this context it means creating a precise and commonly understood way to conduct every essential step in every process” (p. 290). The most used tools in TPS are: 5s, Poka Yoke, Just-in-Time, Continuous Flow Manufacturing, Standard Work, Quick Setup, and Total Productive Maintenance (Silva et al., 2009). TPS is a management system based on Kaizen (Hosono, Page and Shimada, 2020; Katai, 2020; Taj and Berro, 2006; Shah and Ward, 2003).
Liker (2004) emphasizes the importance of implementing the Toyota Model as a whole; it comprises the Toyota Production System and the Toyota Way. The Toyota Way includes four main categories: Philosophy, Process, People and Partners, and Problem Solving. These four categories are also supported by two pillars: continuous improvement and respect for people. So, the implementation of the Toyota model should change the culture of the company. Many companies fail because they only introduce lean tools without making a change in their management style.
Another important feature of TPS is lean thinking defined by Womack and Jones (1996) as, “the endless transformation of waste into value from the customer’s perspective”. As we mentioned, one of the main important characteristics of TPS is eliminating waste. This is also known as muda and refers to a wide range of non-value-adding activities; it implies wasted effort, materials, and time (Womack et al., 2007). In other words, “…anything that takes time but not add value for your customer” (Liker, 2004, p. 10), or in other words, muda is any activity that the customer is not willing to pay for (Bhuiyan and Baghel, 2005; Chen et al., 2010). Toyota divides muda into seven resources that are frequently wasted and there is a tool called, 7+1 Types of wastes. These wastes are (Liker, 2004, pp.28-29):
Unnecessary transport or conveyance - a cost that adds no value to the product but increases the risk of a product being damaged, lost or delayed, carrying work in process (wip) long distances, creating inefficient transport.
Excess Inventory - a capital outlay that if not processed immediately produces no income; excess raw material, wip; or finished goods causing longer lead times, obsolescence, damaged goods, transportation and storage costs and delay.
Unnecessary movement - any damage inflicted through the production process, such as normal wear and tear in equipment, repetitive stress injuries, or by unforeseen accidents; any wasted motion employees must perform during their work, such as looking for, reaching for, or stacking parts, tools, etc.
Waiting (time in hand) - products that are not in transport or being processed.
Over-processing or incorrect processing- when more work is done than necessary, or when tools are more complex, precise, or expensive than necessary.
Over-production - larger batches or more products being made than is required which is basically producing items for which there are no orders.
Defects - the loss involved in rectifying faulty parts or products.
Unused employee creativity: losing time, ideas, skills, improvements, and learning opportunities by not engaging or listening to your employees.
A strategy used to reduce muda is Kaizen, its purpose is to involve every employee in thinking up small improvement ideas on a regular basis (Chen et al. 2010). In Japan, according to Hosono, Page and Shimada (2020, p.3) “…Kaizen developed inclusive and participatory approaches to improving quality and productivity by aligning and adapting statistical quality control and productivity movement methods thar were introduce from the United Stated to a higher level of worker participation”.
Toyota’s results in managing suppliers have been in Toyota’s relentless oversight of every design, production, and logistics process by asking hard questions about performance every day. (Womack, 2007, p. 293). Also, Toyota is recognized for its efficient production system (Ishigame, 2020).
Blue-collar workers’ involvement and systematized observation: two key soft lean tools
The involvement of blue-collar workers and middle manager are fundamental pillars for the success of continuous improvement programs. In fact, lean manufacturing focuses on the empowerment of employees (Nilsson-Wintell et al., 2005; Sanders et al., 2016; García-Lozano, Prado-Prado, and García-Arca, 2000). This idea arises from the fact that workers are responsible for creating products and offering services, then, firms must provide them with a labor environment to suggest improvement proposals and it is very important that they acknowledge their ideas and suggestions. According to Vienazindiene and Ciarniene (2013) one of the reasons of Lean Manufacturing implementation fails is to focus only on tools and techniques and leave people out. It is important to involve all the employees of the company, train them and motivate them so that the strategy works.
The Toyota Production System requires a high level of managerial presence on the factory floor, so if there is a problem in this area, it must first be properly understood before it can be solved. This action is found in the phrase Genchi Genbutsu which can be understood in English as “go and see for yourself to thoroughly understand the situation”. The nature of the phrase has less to do with the physical act of visiting a site, but more to do with a personal understanding of the full implications of any action within an environment. The best practice is to go and see the location or process where the problem exists to solve that problem more quickly and efficiently.
In this sense, a systematized observation is very important. Observation is one of the tools from the lean toolbox and its objective is to attack both process waste and process variability (Arumugam, Antony and Douglas, 2012). Nonetheless, observation alone is not useful since it is essential to carry it out through a systematic way. It additionally supports continuous improvement when the communication channel is two-way, supervisor acting as observer and worker assumes the role of observed (Ingvaldsen et al., 2013).
Liker, 2004, cited by Arumugam, Antony and Douglas, (2012, p. 279) “…concludes that observation leads to deep understanding of the process which results in improved knowledge and that helps to make reasoned decisions and ultimately become a true learning organization.”
Finally, Slack and Rowley (2001) gave the following reasons to support the importance of observation as an effective method of data collection: 1) It can sometimes be used to collect data to which the researcher might not otherwise have access; 2) it can yield direct information about the nature of the leisure experience in specific leisure environments, and 3) students and others need to learn to make effective observations, and to use such information in the learning process. These authors pointed out that effective observation is a skill that needs to be acquired and refined.
II. In context: the automotive industry in Mexico and Guanajuato
In recent years there has been an exponential growth of the automotive industry in Mexico. This has been caused by three reasons: a) a corporate strategy to relocate the plants seeking better conditions (Covarrubias, 2014); b) an industrial policy through government incentives (Martínez and Carrillo, 2017), and c) the 2008-2009 crisis caused a restructuring of the automotive industry, first a change in the hierarchy of the dominant OEMs, GM leaves VW and Toyota as the main firms in the global market, and second a change in the hierarchy of countries and Mexico was benefitted by this restructuring (Micheli and Carrillo, 2021).
In the case of Guanajuato, the conformation of an automotive cluster in the region began with the arrival of General Motors in 1994 and its start-up in 1995, which attracted suppliers, especially Tier 1 and Tier 2 to the state, such as American Axle, Hirotec, Continental Teves, Kasai, Seglo, Arela, Lear, Aventec, Flex N Gate, among others (Martínez, García and Murguía, 2009; Martínez, García and Santos, 2014). However, the boom in this sector began in 2006 with the investment attraction policy that is reflected with the arrival of four assembly companies: Hino, Honda, Mazda and Toyota (Martínez and Carrillo, 2017).
Automotive production in Mexico during 2010-2018 grew 8.2%, the highest rate in the world. And its contribution to world automotive production went from 3.01% in 2010 to 4.09% in 2020. The effects of the health contingency and its impact on the economy caused that the participation of the automotive industry in the manufacturing fell two percent compared to 2019. During 2020, the Mexico’s Gross Domestic Product (GDP) decreased 8.5%, and 647,000 jobs were lost. In that year the automotive industry contributed 3% of the GDP and 18.9% of the manufacturing GDP; and the vehicle production was 3,176,600 units, thus production decreased by 15.8% (596,261 vehicles) compared to 2019, in which 3,772,861 automobiles were manufactured. Despite these results, the automotive industry is very important for Mexico.
III. Methodological design
The information presented is the result of the qualitative and interpretative analysis of a case study of a Tier 2 auto parts company located in Leon, Guanajuato. The company was founded in 1974 and shifted its business focus from supplier of leathers for the footwear industry to the automotive industry. This change led it to worry about being more efficient and productive, so it began to establish quality practices to achieve this and over time implemented a continuous improvement program based on the lean manufacturing philosophy.
The field work research was carried out in three periods: from August to September of 2012, July 2015, and April 2018; the information was gathered through in-depth interviews applied to blue-collar workers, front-line managers, mid-level managers as well as top-level managers; diverse visits and tours around the plant, and analysis of documents given by the company. We carried out 43 interviews in the three periods of time (Table 1).
Table 1 In-depth interviews applied
Position | 2012 | 2015 | 2018 |
---|---|---|---|
Blue-collar workers | 20 | 4 | 5 |
Quality coordinator | 1 | 1 | |
Environment coordinator | 1 | ||
Production coordinator | 1 | 1 | |
Improvement continuous Engineer | 2 | 1 | |
Production manager | 1 | ||
Human resources manager | 1 | ||
IT manager | 1 | ||
Maintenance manager | 1 | ||
Plant director | 1 | 1 | |
Total | 27 | 9 | 7 |
Source: Author’s elaboration.
Each interview lasted between 20 minutes to 70 minutes and depended on the interest and will of the informant. During the interviews, we asked questions about the lean manufacturing strategy: its process, its elements, how they identify the problems to be solved and how they integrate teams to solve them, the workshops they carry out, the results, important events, among others.
We analyze the evolution of quality practices and their approach through the reconstruction of their trajectory. To do this, we adapted a process followed in a previous investigation (Martínez, 2006): first, we identified the main changes that caused a disruption in the company's trajectory. We recognized three important changes: 1997, focuses on being a supplier to the automotive industry; 2006, the company is acquired by the multinational Alpha Autoleather and started to supply to Toyota; and in 2013 seeking be more competitive began to include workers in the continuous improvement projects. We describe the elements of the continuous improvement program that were carried out at each stage.
All the interviews were recorded, then transcribed and finally coded and analyzed using the Atlas.ti software. As codes we used the following words: “continuous improvement”, “observation”, “quality”, “kaizen”, “tachinbo”, “APS”, “blue-collar workers”, “participation”, “genba”, “suggestion box”, “genchi genbutsu”, “lean manufacturing”, “muda”, “waste”, “problem identification”, “problem solution”, “teamwork”, “work team”, and productivity.
In the next section, we present and discuss the results.
IV. Alpha: implementation of a lean manufacturing strategy
A brief history and description of the firm
“Alpha Leon”2 is in Leon, Guanajuato, Mexico; it was established in 1974 and focused on the production of leather for the footwear industry; at the beginning the company belonged to an important local business family. In the mid-1980s, the company began supplying the automotive sector, and in 1997 it decided to produce exclusively for this sector. Initially, its main clients were: General Motors, Volkswagen, Chrysler, and Ford. In 2003 it was subcontracted by a foreign multinational: “Alpha Autoleather3” and in 2006 it acquired it. This acquisition responded to a double strategy of this corporation: low-cost production and transition operations from United States to Mexico. With this acquisition Alpha Autoleather had three plants located in Mexico: Saltillo, Nuevo Laredo, and Leon. In 2008, an Asia-based private equity firm called Advantage Partners LLP acquired Alpha Autoleather, and in 2018 it was acquired by Black Diamond Capital Management LLC4.
The company produces leather interiors for automobiles for the automotive industry. The plant in Leon has three production areas: 1) Cutting, 2) Finishing, and 3) Retanning. It has 1,050 employees and most of the blue-collar workers come from different rural communities around Leon. The destination of its production is 60% for export (mainly to the United States and Japan) and 40% for the domestic market.
Alpha Leon has the following certifications: ISO TS16949 (Cutting area), ISO 9001 (Retanning and Finishing areas), ISO/LEC 17025 (Laboratory), ISO 14001, CCC5 and Great Place to Work. Although its direct client is Lear, assembly companies maintain direct relationships with the company. For example, General Motors performs various audits at its three plants and requires some certifications from them, and Toyota worked with Alpha Leon in the implementation of the Toyota Production System. In addition, the assembly companies decide the prices, the specifications, and the release of the leather.
The company produces 30,500 hides per week which equates to 100 hides per worker per day. In the company, there is a dual labor market: 1) a group of blue-collar workers that are employed by Alpha Leon, and 2) a group of blue-collar workers employed through outsourcing. The firm evaluates workers of the second group every six months in terms of punctuality, attendance, and performance to transfer the best evaluated workers to the first group.
Its main competitors are Eagle Ottawa and Bader, all these companies compete to be suppliers of the Original Equipment Manufacturers (OEMs). To do this, they must be able to offer competitive prices; in fact, each year their prices must be lower than the previous year (reverse auction). For this reason, companies are very concerned about being competitive through higher productivity and lower costs. One mechanism that helps companies achieve these goals is the lean manufacturing program. In the next section we will analyze the program established by Alpha Leon.
Implementation of Lean Manufacturing (LM): an analysis of its trajectory
We identify three stages in the implementation of the LM strategy. Table 2 presents the main characteristics of each one, and a brief description is made below. We focus on the analysis of the third stage, because it represents the complete LM strategy.
Table 2 Lean Manufacturing Trajectory
Period / Item | 1997 to 2005 | 2006 to 2012 | 2013 to 2018 |
---|---|---|---|
Stage | Nascent Lean Manufacturing: The Beginnings | Foundations of the Alpha Production System | Towards and inclusive Alpha Production System |
Main facts | Mid 80’s started to supply automotive sector 1997 focused only to supply automotive sector | Alpha Autoleather acquired the company Toyota becomes its main client | Workers play an important role in continuous improvement projects |
Capital ownership | Mexican | 2006-2007 American 2008-2012 Japanese | 2013 - 2017 Japanese 2018-beyond American |
Owner | Important Mexican business family | 2006-2007 MNC: Alpha Autoleather 2008-2012 Financial group: Advance Partners LLP | 2012-2017 Financial group: Advance Partners LLP 2018-beyond, Financial group: Black Diamond Capital Management LLC |
Headquarter | Leon, Mexico | Michigan, USA | Until 2017 Michigan, USA 2018 Rochester Hills, USA |
Sector | Automotive sector | Automotive sector | Automotive sector |
Clients | General Motors Volkswagen Chrysler Ford | Toyota General Motors Volkswagen Chrysler Ford | Toyota General Motors Volkswagen Chrysler Ford |
Lean
manufacturing elements |
5 s Kanban Teamwork | Kaizen 7 wastes | Alpha Production System: 7+1 wastes Soft lean tools: observation and workers involvement |
Role of
blue-collar workers |
Weak | Weak | Strong |
Incentives | Attendance bonus | Attendance bonus Non-pecuniary | Productivity bonus Non-pecuniary |
Some important economic facts |
1974 - 1993 closed economy 1994 NAFTA 1995 General Motors arrived at Guanajuato 1995 - 2000 State Industrialization Policy | From 2006 State Investment Attraction Policy 2008 - 2009 The Great Recession | Restructuring of the global automotive industry |
Source: Author’s elaboration based on field work research.
Nascent Lean Manufacturing: The Beginnings
Since 1997, when the company decided to supply only to the automotive sector, it has been concerned with achieving the best quality indicators. One of its main actions was to offer a specialized diploma developed in conjunction with Tec de Monterrey, a consulting firm called Tecno Consultores and the company itself called "Managing the transformation towards Alpha Leon 9000".
At the end of 1998, the company obtained the certification QS 9000 for the Cutting area. At that time, their company-wide quality system consisted of 5s and Kanban, and the operator was responsible for meeting quality specifications.
Foundations of the Alpha Production System
However, the main trigger for the company’s growth was its business relationship with Toyota. The demands of this company had a positive impact, as Alpha began to grow in order, to work with improvements on a routine basis and to emphasize the development of its employees. Here is the testimony of the Crust manager:
(…) through this system the company acquired that work philosophy, from Toyota, which is its production system, and we have adopted tools for our work system. and in their visits, they invite us to improve” (personal communication, August 2012).
They began, in 2006, to establish a continuous improvement program based on the lean manufacturing philosophy and during the first four years this program only involved managers and coordinators who were trained in the United States.
During this period, the company began to use continuous improvement workshops. The company established a monthly goal of improvement ideas, and each manager was responsible for proposing, carrying out and documenting them. The goal was to have "lessons learned". Managers defined a problem and invited workers to participate.
Alpha Leon began the implementation of the APS Workshops because of their supplying Toyota. Toyota runs workshops called BAMA6. BAMA is a corporation made up of its Tier-one suppliers who share a common vision with the company of delivering vehicles of the highest quality at the lowest cost, and in the shortest delivery time.
The workshop is not compulsory, Toyota invites its suppliers to participate in it, yet its implementation brings many benefits to the company such as a better work environment, waste reduction, higher productivity, lower costs, etc. At this point it is important to mention what Womack et al. (2007, p. 293) pointed out:
“What we still lack as lean production diffuses across the world is a stable way for firms and independent suppliers sharing product value streams to work together to rigorously optimize the performance of the whole, not just the parts”.
Towards and inclusive Alpha Production System
In 2013, the firm introduced the Alpha Production System (APS) replacing the name “Toyota” with the company name “Alpha.” At that time, they recognized the role played by blue-collar workers in the effectiveness and sustaining of the program and decided to involve them; according to the Continuous Improvement Engineer this change was very important “…because the operators spend all of their time in the shop floor and so they know all the production details” (personal communication, April 2018). It is important to mention that there is a specific department in charge to implement the Alpha Production System, and quality and lean principles are integrated. In fact, the workers oversee the quality of their products, this allows the integration of the production and quality system. Important binomial for the system implementation to work (it coincides with the results found by Durakovic et al., 2018).
Currently the continuous improvement program comprises a) APS workshops, b) Tachinbo workshops, and c) Suggestion box. It also seeks to promote the creation of a quality culture with systematized observation and blue-collar workers’ involvement as its main pillars. It is important to emphasize the role played by culture factors for the successful implementation of this kind of practices; and in this sense Alpha has been able to create a quality culture. Next, we will address the 4 components of the program and the two pillars.
APS workshops
During this stage the firm decided to involve its blue-collar workers. According to the pre-finish production coordinator, "... right now our operators attend the workshops and, curiously, the most effective improvements are those proposed by them because they are the ones who are on the production line all the time" (personal communication, June 2015).
The decision to include operators was because the company realized their participation is very important to permeate the culture of continuous improvement towards all areas of the firm. In each workshop four teams are formed and one of the members is an operator. And this decision was very important to foster the successful implementation of Lean Manufacturing (LM), and coincides with Larteb et al. (2015), who found that training and motivation can be considered as the main drivers to promote successful projects, and training is provided to the team and the shop floor workers involved in the implementation.
At the beginning the workshops were held every 3 months but since 2015 they were held monthly. The purpose of the APS Workshops is to promote a process improvement culture where “People share the same vocabulary, they know what is ‘Yokoten’, ‘the 7 + 1 wastes,’ they identify the members of the Continuous Improvement department and tell them their improvement proposals” (Continuous Improvement Engineer, personal communication, April 2018).
It is important to mention that to identify an improvement opportunity, the company considers two possibilities: an area that is having problems or an area that has a stable performance and that has not made changes for a long time. The Continuous Improvement Department monitors the improvement proposals.
In general terms, the process is as follows: a) an opportunity for improvement is identified by a mid-level manager or a top-level manager, b) a multidisciplinary work team is formed and its members belong to different areas (i.e., quality, production, maintenance, engineering, etc.) and different levels (blue-collar workers, coordinators, mid-level managers, among others); it is important to mentioned that this kind of composition is fundamental to promote better results (Martínez, García and Santos, 2014); c) all the members of the different teams are registered in a workshop, d) a leader is identified and he must belong to the area where improvement will be implement. These first four steps are part of planning the workshop. Then there is the application: e) the workshop lasts one week, the first two days are dedicated to explaining the company’s quality philosophy: Kaizen, 7 + 1 wastes and in this course, participants learn how to identify wastes and how to attend them. They also learn how to measure the impact of the improvement; f) then, the work team is assigned to the area and its first and most important function is observation. They work for 3 days to find a solution to the identified problem. At the end of the week, the work team presents the results obtained from the applications of the recommendations. In the presentation of the results the Director of the plant, coordinators of the involved areas, and managers participate. It is very important that the different teams share their results and important information about the process carried out such as some aspects of the problem, tools they use, limitations, among others.
One important thing must be noted that the observation is undertaken in a collective way. This should reduce the likelihood of bias if the observation were individual because “observers bring a range of preconceptions that influence the way which they observe” (Slack and Rowley, 2001, p. 37).
In this system they apply the scientific method: a problem to be solved is identified, then observation begins, a hypothesis is established, and the fourth stage is where the employees begin to give some proposals to solve the problem.
Proposals must be aligned with the company’s goals (quality, costs, deliveries, safety, customer satisfaction) and must try to address one of the seven wastes (overproduction, waiting, excessive transportation, incorrect or unnecessary processes/procedures, inventory, motion, and rework/ defects). Each proposal is classified according to the type of improvement generated: AK (incremental), Kaikaku (disruptive) or Kaizen (see Image 1).
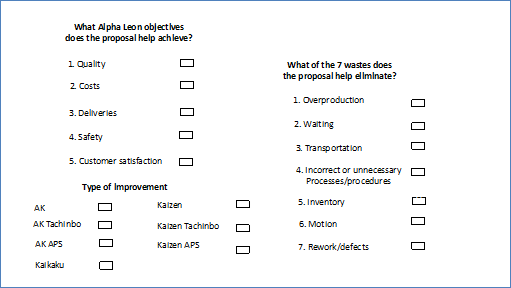
Source: Author’s elaboration based on field research.
Image 1 Some features about continuous improvement program in Alpha
After the workshop is finished, it is followed up on for 8 weeks. The Continuous Improvement Team does a weekly monitoring.
The objective during the week of the workshops is not only to identify the root cause that is provoking the problem, but also the solution, its implementation, and possible indicators to follow up at the end of the workshop. According to the firm, in 2017, 162 projects were carried out and the results obtained were an annual saving of 287,787 hours and $142,270 USD. The distribution of these projects is shown in Graph 1.
Tachinbo workshops
They are workshops like the APS workshops, but more focused on the problem to be solved, 20% of the time is dedicated to theory and 80% to practice. They have supported the promotion of the culture of continuous improvement. Initially the implemented improvements were generated in the APS workshops, now the workers observe and identify what improvements can be made to support them in the 7 + 1 wastes. All the implemented proposals are documented in an indicator called “Improvement actions carried out”.
Tachinbo is a method to solve problems using the methodology called TEAM which is based a lot on observation. It implies staying in a place and studying the real situation of a specific problem. It comprises two steps: 1) Genchi Genbutsu: Go, see, and understand, and 2) Yokoten: Share information. Its purpose is totally pragmatic, to solve certain identified problem. Another important part of the process is sharing the knowledge. Can what you learned in one area be applied to another?
Tachinbo is a Japanese word that means “to observe” and the other important word is Genba that means “the place where the actual work is done”. The Genba is the most important location in a Toyota factory, a place where time, productivity, and space are crucial and not to be wasted.
These workshops give support to participants for them to develop confidence and make contributions as well as to share their ideas to improve the process. Blue-collar workers can observe their work environment and come up with diverse suggestions for improvement. This is the result of the hard work developed by the firm to make the Continuous Improvement System part of the organizational culture:
“How can I improve my work environment? Doing “Tachinbo”, doing “Genchi Genbutsu”… and with simple changes I can improve the workstation of my employees, for example, I can place the drink water closer to them, and with this simple change I am able to eliminate unnecessary movements and increase the productivity. Another change that we implemented was to place in each workstation the required supplies for each activity, so the blue-collar workers are only concerned about their main activity: to produce …” (Personal Communication with the Production Coordinator of the Crust Area, July 2015).
Suggestion mailbox
Alpha Leon began to implement suggestion mailbox in June 2015 as a requirement to obtain the ISO TS certification. This certification was requested by General Motors (GM), and although the direct client of the company is Lear, gm conducts audits at the company. The difference between the Suggestion Box and the Tachinbos and APS workshops is the source of the suggestions. First, they are proposed individually and answer the following question: How to improve your workplace?
Therefore, the idea of the suggestion mailbox is that each person in the plant can make suggestions for improvement focused on the APS culture; four mailboxes were placed on the floor, these are known by the name of SISI (from the Spanish expression “¡Ah, si, si!” And it refers to the question: How can we make something work?). They are located strategically along the productive process, so the workers can fill the special formats designed for this purpose during their labor hours.
There is a committee that evaluates the received ideas which should be focused on solving some of the 7 + 1 wastes. The ideas that are accepted will be implemented through a work team, called CAPI (Coalescence, Authority, Power, and Influence). The team is multidisciplinary and the person who proposed the idea is part of the implementing team and can take any of the roles of CAPI or just be a participant. Once implemented, the impact will be evaluated and based on it, there will be positive reinforcement through incentives. To recognize the ideas contributed, in 2015, a system of non-pecuniary incentives was established based on the contribution made. Before implementing the Suggestion Box, there was no formal way to define and solve problems. Employees of the Continuous Improvement Area had to find a situation to improve.
There is a specialized format that is used to report improvement suggestions. They can be proposed by blue-collar workers and managers of middle and higher level. 80 % of the proposals attended belong to the production department.
In summary, the process for suggesting and evaluating is:
Employees present their ideas.
A committee evaluates them considering the following aspects: productivity, security, quality, costs, inventories (all according to the “Seven + 1 wastes” tool which is very important to be able to focus attention and not lose it in other aspects that do not contribute to improving the company’s performance.
The accepted ideas are implemented by a multidisciplinary team formed by the company and at the end of the implementation the savings will be measured.
If an idea is not selected, proponents will receive “positive feedback” via letter to encourage their participation later.
In Table 3 we can see some examples of projects carried out in 2015, for each project there is a proponent, a champion - person who will in charge of the execution, and a person who will review the progress. In addition, the initial situation and the result are described, highlighting the benefits that were obtained.
Table 3 Some examples of projects carried out in 2015
Project | Issue before Kaizen | Result |
---|---|---|
Change of sandpaper in polishing | Excessive stops due to lack of material when changing the tool (Type of sandpaper). Stop time: 27min | Reduction of sandpaper change time after SMED: 7min (73.4% saving-20min) |
Leather optimization in "Scraped Desorille" | The optimization of the leather in the scraping area is not visualized, to impact the use of this in the cut. | Use of 0.9% equivalent to US $5,309.00. Chemical savings for leather 2.67% RTE-Finish Annual projection of savings US $80,246.00 in chemicals |
Conditioning, conservation, and supply of staples | Poor work ergonomics, unsuitable tools, untidy work areas | Sustainability of renewable materials, greater ergonomics of work, cost-benefit savings of materials, zero accidents by using the right tool. |
Proper Area Relocation for Ammonia “Totes” | Workers carry out tours of the street carrying ammonia totes, which is an unsafe act as an accident or ammonia spill can occur on the street | An adequate area was established for the storage of ammonia (there was a saving of 210 mts of travel) and the transport is safer since it is carried out inside the plant. |
Source: Author’s elaboration based on field research.
Analyzing the information presented, we can note that the factors mentioned repeatedly by the interviewees that take place in the components of the continuous improvement program are observation and operators’ involvement. Next, we cover a little more each of them.
Soft Lean Manufacturing tools: observation and worker’s involvement
According to Larteb et al., (2015), some authors mentioned different critical success factors to implement Lean Manufacturing, Table 4 resume this and add the success factors that we found in our research. Of the 8 factors that we found, 6 coincide with those mentioned by the authors; those that we add are the observation and involvement of the workers.
Table 4 Success factors to implement a continuous improvement program
Author | Success factors |
---|---|
Garnier, 2010 | Personalized demarche Top management commitment Allocation of resources Strong communication Structural methodology Multifunctional teams Continuous performance measurement |
Lila, 2012 | Leadership and management Finance Skills and expertise Supportive organizational culture |
Lyonnet, 2010 | Personalized demarche Top management commitment Problem solving culture The teamwork |
Duque and Cadavid, 2007 | Preparation and motivation of
people Roles in the change process Methodologies for change Environment for change |
Alpha Leon | Top management commitment Strong communication Scientific methodology Multifunctional teams Problem solving culture Preparation and motivation of people Observation Worker’s involvement |
Source: Author’s elaboration based on Larteb et al. (2015) and field research.
The different collaborators who have participated in APS and Tachinbo workshops recognize observation and workers’ involvement as key tools in this process. According to one of the employees:
“The key to all of this is to observe, observe the person, the environment, even the person’s eyes and his movements. Then all the team members draw up a list of possible problems … the teams are multidisciplinary and multilevel” (Personal communication, July 2015, Process Engineer of Improvement Continuous).
In the words of another of the interviewees:
“The key is to observe, observe the person, observe the surroundings, observe even the person's eyes, because you never know what they are observing, your job is to observe, your job is with your eyes. Therefore, it is important from the observation of the person’s eyes and even the most noticeable movements of her: where she walks, if she raises her arm, goes down or climbs stairs, etc. At the beginning of the workshop, we emphasize that we will be in the workplace for an entire hour to observe, nothing more, and we emphasize that they observe the operator not so much the machinery. An example that we use is, imagine that you are a five-year-old child and you are standing there in the production process, look at the person, what they see, their hands, where they are, their legs, observe what they are doing, their feet, what she wants to reach with her hands and ask yourself everything, like a five-year-old child, do not take anything for granted, and after having observed, observed and observed, mainly the person, write everything down. "(Personal Communication, Continuous Improvement Engineer, April 2018).
With this information collected they work in the classroom. They discuss their findings with the team members and try to identify the main problems and their possible solutions. During the first four days of the workshop, each team implements its proposals and at the end of the fourth day the three teams that participated in the workshop discuss the implementation of each improvement and provide feedback to each other.
Talking about worker’s involvement; as we mentioned, when Alpha Leon began with the continuous improvement program, it only considered the participation of the managers, then it included the coordinators; however, it realized that APS is a philosophy that permeates the culture of the organization, and that although the managers and middle managers had adopted it, the workers had not. In 2015, it decided to take operators into account and began inviting them to the APS workshops.
Therefore, one of the main challenges is to involve the blue-collar workers. Supervisors and middle managers have the culture of improvement and are concerned about how to improve to promote a better place for workers and save money for the company. The importance of their participation is given by the following comment of the Production Director:
…Although we have excellent ideas, if the workers do not identify with these ideas, if they do not feel that these ideas belong to them, then these ideas do not work. (Personal communication, July 2015).
This opinion is reinforced with the following two statements given by of the Production Coordinator in the Crust Plant and the Finishing plant manager:
“…nowadays blue-collar workers participate in the Improvement Workshops, and their proposals are the most effective, the reason is that they live daily the production process” (Personal communication, Production Coordinator in the Crust Plant, July 2015).
"... it does not matter if an improvement proposal is good, for workers to adopt it, they must feel involved, feel that the idea is theirs, otherwise, many improvement proposals stop being made ..." (Personal communication, Finishing plant manager, July 2015).
These comments are in line with the results of Ishigame's (2020) research on automotive companies in South Africa. He found that Kaizen (or continuous improvement) had a positive impact on worker learning about how to improve productivity and quality.
Concluding Remarks
Hosono, Page and Shimada (2020) mentioned there are few empirical studies analyzing the effectiveness of the implementation of continuous improvement programs in developing countries, therefore, this is the intention of this contribution.
The objective of this article was to analyze the implementation of the Lean Manufacturing (LM) strategy in a multinational auto parts company located in León, Guanajuato through the reconstruction of its trajectory during the period 1997 to 2018.
Through the analysis of the three identified stages the main findings were that the determinants for the successful implementation of the lean manufacturing strategy can be classified in two headings: a) soft lean manufacturing tools: observation and workers’ involvement; and b) institutional factors: sector of belonging, size of the company, ownership of capital and relationship with its main client.
Regarding soft lean manufacturing tools, the participation of blue-collar workers is crucial in sustaining the Continuous Improvement Program, it is important that they feel involved in improvement proposals since the effective implementation of these depends to a large extent on this.
And “observation” allows employees to propose and implement incremental innovations in their work areas that will result in a higher productivity, lower costs, higher quality, reduce over processing, among others.
Regarding institutional factors, as it belongs to the automotive sector, the demands of its direct client (Lear) and of the assemblers lead it to seek to be more efficient through the continuous introduction of improvements that allow it to reduce costs, increase quality and productivity. Regarding the size of the company, being a multinational, it has the resources to establish this type of strategy. A finding that we believe is important to highlight is the ownership of the capital, Alpha, like other multinational companies, belongs to an important financial group. These groups buy companies with the potential to make them more profitable, so the establishment of strategies such as lean manufacturing is essential to achieve this. Finally, his main (indirect) customer Toyota has driven him to be more competitive.