Introducción
Toda empresa, sin importar su área de especialización, se halla en la búsqueda de mejorar sus procesos y su productividad para contribuir a la optimización de recursos, mejorar sus condiciones de trabajo y ser más competitivas (Vargas-Hernández et al., 2016). Para lograrlo, actualmente existe una serie de herramientas, filosofías y metodologías ágiles enfocadas en obtener el mayor beneficio a los recursos disponibles. Entre las más utilizadas se pueden mencionar metodología de manufactura esbelta (Vilana Arto, 2011), metodología kanban (Gómez et al., 2020), 5’S (Quiroz-Flores y Vega-Alvites, 2022), diagrama de spaghetti (Torres Rodríguez, 2019), tableros kanban (Carrera Cabezas, 2019), entre otras.
Por ejemplo, Gisbert Soler (2015) menciona que la metodología lean manufacturing (manufactura esbelta) se orienta a la eliminación o reducción de desperdicios en los procesos productivos, lo que permite su adaptabilidad a diferentes áreas. Por otra parte, en el laboratorio de mecánica de suelos se realizan, de manera particular, pruebas de análisis a materiales para la construcción, los cuales comprenden la construcción y mantenimiento de vías terrestres y edificación de estructuras de concreto. Este tipo de laboratorio maneja diariamente volúmenes de muestras variables, de ahí que se consideren los tiempos de entrega de resultados, lo cual varía entre cinco y diez días, según el tipo de cliente.
Ahora bien, en el caso concreto de este estudio, se ha observado que la empresa analizada se enfrenta a diferentes problemas de organización en el área de ejecución de pruebas de laboratorio, lo que provoca que el flujo de las actividades no sea constante y se generen retrasos en la entrega de resultados. Otra situación detectada es que la empresa cuenta con áreas de trabajo y herramientas de uso común donde se generan choques o interrupciones constantes al momento de realizar las actividades. Todo esto repercute en un ambiente de laboral difícil, principalmente en los meses de septiembre a noviembre, cuando la carga de trabajo es mayor.
Por otra parte, se puede indicar, de manera general, que el sector de la construcción no ha sido estudiado en profundidad y el porcentaje que considera la implementación de aspectos de la manufactura esbelta solo es del 2.73 % (Tapia Coronado et al., 2017). Algunos ejemplos de ello han llevado a la creación del término lean construction, aunque esta manufactura aún está en desarrollo (Albalkhy y Sweis, 2021). En esta se procura mantener en niveles significativos los procesos de productividad y calidad, minimizar los tiempos muertos, las mudas o desperdicios, así como otros indicadores del desempeño de una empresa.
Este proceso descrito fue adaptado del sistema de producción de Toyota (Ahmed et al. 2021), el cual permite una reducción en costos, duración del proceso, riesgos de seguridad, accidentes, errores, retrabajos, desperdicios, entre otras, así como mejoras en sustentabilidad, manejo de inventarios, predictibilidad del trabajo, productividad y satisfacción del cliente (Albalkhy y Sweis, 2021). Para Shuquan et al. (2020), la técnica de lean construction se dedica principalmente a eliminar todo lo que no contribuya o no agregue valor al producto final, sin importar cuál sea este y teniendo una visión total de negocio.
Tomando en cuenta lo anterior, se puede generar un enfoque multidisciplinario que aplique los principios de la ingeniería industrial a un área diferente, como salud (Martin et al., 2014), educación (Montes Dorantes et al., 2020), metal mecánica (Montes Dorantes et al., 2018), manufactura (Montes Dorantes y Méndez, 2023; Mexicano et al., 2022) o construcción. En particular, este enfoque puede ser aplicado al laboratorio de mecánica de suelos, el cual desempeña un papel crucial en la investigación destinada a asistir a ingenieros y arquitectos en la selección del tipo de construcción más adecuado en función de las condiciones del suelo.
Por lo tanto, resulta necesario implementar estrategias que optimicen los procesos dentro del laboratorio, lo cual no solo mejorará los procedimientos existentes, sino que también permitirá aprovechar al máximo los recursos disponibles, como el personal, el equipo y el tiempo.
Antecedentes
En esta sección se presentan ejemplos de enfoques multidisciplinarios que representan casos exitosos de la aplicación de herramientas de la ingeniería industrial en diversas áreas, con distintas características industriales. Por ejemplo, Martin et al. (2014) aplicaron herramientas como 5'S, A3 (genera un informe simple del problema con su resultado actual y una sugerencia), mapas de cadena de valor y eventos de mejoramiento rápido en los procesos de quirófano en el Seattle Children’s Hospital para optimizar la atención de pacientes y el trabajo en equipo del personal.
Por otra parte, Torres Rodríguez (2019) utilizó herramientas DMAIC (definir, medir, analizar, mejorar y controlar, por sus siglas en inglés), 6S, diagramas de spaghetti y kanban para mejorar en 12.5 % las líneas de manufactura en la compañía Stryker; con este trabajo se consiguieron mejoras significativas en la eficiencia y en la reducción de las distancias de transporte del material. Bosnjak y Bosnjak (2020) presentaron un método basado en la gestión lean para mejorar la atención médica, para lo cual implementaron herramientas como 5'S, kanban, eventos Kaizen y diagramas de spaghetti.
Huerta Estévez (2021) aplicó lean manufacturing, incluyendo mapeo de procesos y diagramas de recorrido, para reducir paros de línea en una planta ensambladora de autos. Lista et al. (2021) realizaron una redistribución de planta basada en principios lean manufacturing en una empresa textil, lo cual les permitió disminuir costos y movimientos innecesarios. Rapale (2018) implementó metodologías DMAIC, seis sigma, 5'S y tarjetas de colores para optimizar la búsqueda de materiales y herramientas en una empresa de productos de limpieza, lo que optimizó la eficiencia y la organización.
Por su parte, Pedraza et al. (2021) utilizaron herramientas de lean manufacturing como mapas del flujo de valor para aumentar la productividad y calidad en una microempresa de productos derivados del maní. Asimismo, Escudero (2020) aplicó herramientas como la gráfica de equilibrio, 5S y manufactura celular para eliminar desperdicios en una empresa de armado de pizzas, lo que disminuyó el tiempo de procesamiento y aumentó la productividad. En el área de la construcción, Carrera Cabezas (2019) empleó metodologías lean six sigma, mantenimiento productivo total (TPM), justo a tiempo (JIT) y kanban en una empresa de losas alveolares de concreto, lo que redujo la sobreproducción de hormigón y las disconformidades en los productos.
Sin embargo, Latorre (2017) y Pons Achell (2014) explican que la filosofía lean construction es una metodología en crecimiento en la construcción que se centra en proyectos globales, considerando costos y duración del proyecto en su conjunto, en lugar de actividades individuales. La tabla 1 resume las metodologías y herramientas empleadas por los autores previamente analizados.
Tabla 1 Metodologías y herramientas empleadas por distintos autores
AUTORES | TRABAJO | METODOLOGÍA | RESULTADOS |
---|---|---|---|
Marmolejo et al. (2016) | Mejoramiento mediante herramientas de la manufactura esbelta en una empresa de confecciones. | 5’S y control visual. | Reducción de tiempos perdidos por actividades que no generaban valor (tiempos de transporte) al proceso. |
Bošnjak y Bošnjak (2020, p. 127) | LEAN System Management in Hospitals. | Lean, 5’S, kanban, eventos kaizen, diagramas de spaghetti, Heijunka, entre otros. | Empleo de herramientas lean para mejorar y aumentar los entandares en la atención médica. |
Martínez et al. (2016) | Mejora en el tiempo de atención al paciente en una unidad de urgencias por medio de lean manufacturing. | Herramientas de lean manufacturing como value stream mapping y diagrama de spaghetti. | Reducción en tiempo de espera en los pacientes de hasta 67 %. |
Martin et al. (2014, p. 6) | Mejoramiento de los procesos en el quirófano mediante la aplicación de la metodología lean de Toyota | Lean, como 5S, A3, mapas de la cadena de valor, eventos de mejoramiento rápido. | Mejoró los procesos en un quirófano y la calidad en la atención de los pacientes y el trabajo del personal. |
Fuertes y Sepúlveda (2016) | Scrum, kanban y canvas en el sector comercial, industrial y educativo. Una revisión de la literatura. | Scrum, kanban y metodología canvas. | Sector comercial, herramienta Scrum, kanban y canvas: 38 % Sector Industrial, Scrum y kanbam: 33.33 % Sector educativo: Scrum: 28.57 % |
Pérez y Quintero (2017, p. 411) | Metodología dinámica para la implementación de 5’S en el área de producción de las organizaciones. | 5’S, JIT (Just in Time), kanban y kaizen. | Propuesta de metodología dinámica en el área de producción en las organizaciones. |
Peláez Saladriga (2014) | Identificación del cuello de botella en la cadena de producción de luminarias de 100 W de la empresa de producciones electromecánicas. | Análisis por envoltura de datos DEA (Data Envelopment Analysis). | Implementación de DAE para obtención de cuellos de botella. |
Pons Achell (2014) | Introducción a lean construction. | Lean Production, Just in time (JIT), jidoka y kaizen o mejora continua, plan de acción PDCA (Plan-Do-Check-Act) o ciclo de Deming. | Empleo de filosofía Lean Production, y aspectos de sistema de producción Toyota en la construcción. |
Torres Rodríguez (2019, p. 5) | Mejoras de proceso en una línea de producción. | DMAIC, 6S, diagrama de spaghetti, kanban. | Aumento en la eficiencia de 16 %. Reducción de espacio un 12.5 %. Reducción de distancia de transporte de materiales hasta 40 % en una compañía de tecnología médica. |
Rapale González (2018) | Diseño de optimización en logística de organización. | DMAIC, seis sigma, 5’S, diagrama de spaghetti y tarjetas de colores. | Optimizó el tiempo de búsqueda y obtención de materiales y herramientas en una empresa dedicada a la manufactura de productos de limpieza. Aumento del flujo de trabajo. |
Sánchez Quiroz (2021) | Propuesta de mejora del proceso de mantenimiento de instrumentos de medición y herramientas para reducir los tiempos de atención. | Manufactura esbelta Value Stream Mapping (VSM), 5’S, Poka yoke (a prueba de errores), kaizen (mejora continua). | Reducción de costos de operación, tiempos de atención del proceso de mantenimiento de instrumentos de medición y herramientas. Ampliación de la capacidad del laboratorio de calibraciones del 72 % al 95 %. |
Huerta Estévez (2021, p. 52) | Reducción del manejo de materiales en línea en una ensambladora de autos mediante la aplicación de lean manufacturing. | Lean manufacturing como mapeo de procesos y diagrama de recorrido. | Logró un ahorro del 50 % en la línea de producción y disminución del 85 % en los ciclos de trabajo en una planta ensambladora de autos. |
Lista et al. (2021, p. 5) | Lean layout design: a case study applied to the textile industry | Lean manufacturing VSM, diagrama de espaghetti. | Realizaron una redistribución de planta en una empresa de la industria textil, reduciendo costos de manejo, movimientos innecesarios y ajustes de arreglos |
Pedraza et al. (2021, p. 151) | Aplicación de la metodología lean manufacturing para reducir el tiempo de producción de bolas de maní. | Lean manufacturing Value Stream Mapping (VSM). | Identificar cuellos de botella, mejorar la productividad y calidad en una microempresa dedicada a elaborar y distribuir productos derivados del maní. Disminuyeron los tiempos de procesos y aumentó la producción 35 %. |
Escudero (2020, p. 51) | Mejora del lead time y productividad en el proceso armado de pizzas aplicando herramientas de lean manufacturing. | Grafica de equilibrio, 5S y manufactura celular. | Detectó y eliminó desperdicios en una mediana empresa, reduciendo el lead time de 99 % e incrementó la productividad 20 %. |
Carrera Cabezas (2019) | Mejoramiento del proceso de producción de losas alveolares bajo metodología lean six sigma en la empresa pública cementera EPCE. | Lean Six Sigma. Mantenimiento productivo total (TPM). Justo a tiempo (JIT). Kanban. | Al aplicar las herramientas TPM, JIT y kanban se disminuyó el tiempo de proceso de 29.75 a 22.58 horas. Se realizó una adecuación a los carretes portables, disminuyendo el tiempo de tendido de 75 minutos a 30 minutos por pista. Al implementar TPM se eliminó el proceso de acondicionamiento de máquinas, ahorrando 60 minutos, y al implementar JIT y kanban se produce solo el hormigón necesario. Así, se evitan tiempos muertos y disminuye 30 minutos el tiempo del colado. |
Fuente: Elaboración propia
Con base en la información presentada en la tabla 1, se planteó el uso de los principios de lean manufacturing para optimizar los procesos de la empresa.
Materiales y métodos
La metodología utilizada en este proyecto se llevó a cabo a lo largo de cinco meses en el laboratorio de mecánica de suelos, y se basó en la observación y en la familiarización con la organización del laboratorio y sus necesidades. Una vez completado el análisis inicial, se optó por aplicar los principios del lean manufacturing, cuyo propósito es mejorar los procesos al eliminar el despilfarro o desperdicios, es decir, todas aquellas actividades que no aportan valor al producto (Vargas-Hernández et al., 2016). Esto se logró mediante el uso de herramientas diseñadas para mejorar la eficiencia y la organización en el entorno de trabajo.
Las herramientas lean seleccionadas para su implementación en el laboratorio de mecánica de suelos se caracterizan por su adaptabilidad a diferentes contextos laborales. Para ello, se comenzó con el enfoque en las 5'S y el control visual, que se basan en cinco principios: Seiri (eliminar), Seiton (ordenar), Seiso (limpieza e inspección), Seiketsu (estandarización) y Shitsuke (disciplina) (Pérez y Quintero, 2017). Estos principios se aplicaron en todas las áreas de trabajo, lo que facilitó la organización y clasificación de las herramientas utilizadas por el personal, la eliminación de herramientas en mal estado y la promoción de la disciplina en cuanto al orden.
El mantenimiento productivo total (TPM) fue otra herramienta empleada para maximizar el rendimiento de los equipos, lo que permitió a los operarios efectuar tareas básicas de mantenimiento (Carrera Cabezas, 2019). Dado que el equipo del laboratorio requiere calibraciones certificadas periódicas, se autorizó al personal para llevar a cabo mantenimientos y limpiezas en las prensas y herramientas. De ese modo se procura prolongar la vida útil de los equipos hasta la próxima calibración certificada.
El sistema kanban, que se basa en el uso de tarjetas para controlar y programar la producción y los materiales (Gómez et al., 2020), se implementó para llevar un registro de los materiales utilizados en el laboratorio. Cada uno de ellos se identificó mediante tarjetas que especifican claramente las áreas y las pruebas de laboratorio a las que deben someterse, lo que facilita la ubicación de las muestras y la recopilación de resultados para el personal y el jefe de laboratorio.
Además, se utilizaron herramientas como Heijunka, que se basa en la sincronización de operaciones para minimizar movimientos innecesarios (Bošnjak y Bošnjak, 2020), y los diagramas de spaghetti para visualizar los flujos de trabajo en el laboratorio y las áreas de mejora. Es importante señalar que los directivos del laboratorio tienen la intención de implementar la filosofía Kaizen en el futuro. Kaizen es una cultura de mejora que involucra a todo el personal de la empresa y forma líderes para alcanzar mejoras a largo plazo (Dinas Garay et al., 2019).
Estas herramientas fueron empleadas para desempeñar actividades de forma paralela, disminuir las mudas, cuellos de botella, dar orden a las actividades y aprovechar los recursos con los que cuenta el laboratorio siguiendo la metodología descrita a continuación.
Metodología
La metodología implementada consta de cuatro etapas principales: 1) familiarización con las áreas de trabajo, 2) análisis de los procesos: estado inicial, 3) implementación experimental y 4) resultados y análisis del estado después de la aplicación de herramientas. Estas etapas se muestran en la figura 1.
Familiarización con las áreas de trabajo
Tomando en cuenta lo fundamental de adquirir un conocimiento completo y una comprensión detallada de las áreas de trabajo disponibles en el laboratorio, así como de las actividades que se llevan a cabo rutinariamente y las situaciones excepcionales que puedan surgir en estas áreas, en la etapa 1, denominada “Familiarización de las áreas de trabajo”, se realizó una observación detenida. Esta permitió identificar que el laboratorio de mecánica de suelos se divide en dos tipos de áreas de trabajo distintas. En primer lugar, están las “Áreas especializadas”, destinadas a la realización de diversas pruebas de laboratorio. Estas no son flexibles en cuanto a su disposición, ya que albergan equipos especializados que permanecen en su ubicación fija (sombreadas en amarillo). En segundo lugar, encontramos las “Áreas de trabajo común”, donde el personal tiene acceso a herramientas compartidas y de uso general que son necesarias para realizar diferentes tipos de pruebas o etapas de trabajo (sombreadas en morado). Adicionalmente, en el plano (figura 2) se indican con flechas de color verde las dos entradas por las cuales ingresan los materiales al área de trabajo. Las áreas de secado de materiales, tanto interiores como exteriores, se resaltan en color naranja en el esquema. Es importante destacar que este plano del laboratorio se diseñó utilizando AutoCAD y se presenta de manera visual en la figura 2 para una comprensión más clara.
Análisis de los procesos: estado inicial
En esta etapa se pudo constatar que el laboratorio de mecánica de suelos organiza sus operaciones en torno a tres áreas principales: “terracerías y materiales pétreos”, “asfaltos” y “concretos”. Tras un análisis exhaustivo de estas áreas de trabajo, se determinó que este proyecto se centraría en la línea de trabajo más amplia, es decir, el área de “terracerías y materiales pétreos”.
La figura 3 presenta en detalle el diagrama correspondiente a la línea de trabajo relacionada con los materiales de “terracerías y materiales pétreos”. Este diagrama ilustra cómo esta línea se desglosa a medida que avanza a través de sus diversas fases, que comprenden la entrada de materiales, la preparación, la primera distribución, la segunda distribución y culmina con la recopilación de toda la información en un solo reporte de calidad.
Ingreso, etiquetado y preparación de muestras de laboratorio
En esta etapa, el jefe de laboratorio recibe los materiales y los ingresa al sistema (figura 3, actividades resaltadas en verde claro). Luego, procede a etiquetarlos, lo cual implica registrarlos en la bitácora y asignarles un número de trabajo. A continuación, asigna las pruebas específicas que deben llevarse a cabo y distribuye los materiales según las distintas líneas de trabajo, ya sea terracerías y materiales pétreos, concretos o asfaltos. Finalmente, inicia los procesos correspondientes.
Es importante destacar que dado que el jefe de laboratorio realiza todas estas operaciones, se observa un cuello de botella en la empresa desde el momento de la recepción de los materiales. Esto se debe a la acumulación de muestras en espera antes de que puedan comenzar su proceso, lo que resulta en retrasos en la ejecución de las pruebas.
Una vez que los materiales obtienen sus números de trabajo, se pasan al área de secado, la cual puede ser interior o exterior, dependiendo de las condiciones climáticas del día. En días soleados, se utiliza el área de secado exterior, mientras que en días lluviosos se recurre al área interior (figura 2). No obstante, esta variabilidad en el lugar de secado dificulta considerablemente las actividades de los empleados.
La figura 3 presenta un diagrama de flujo que ilustra la línea de trabajo en el laboratorio, marcando con diferentes colores las distintas pruebas a las que se someten las muestras. Para obtener un detalle más completo de los flujos, ver las figuras 4 y 5.

Fuente: Elaboración propia
Figura 4 Diagrama de spaghetti del recorrido completo de una mesa de trabajo, organización original
Recorrido de una muestra por las áreas de trabajo en el laboratorio (procesos)
Después de que el material se ha secado, se realiza la prueba de peso volumétrico seco (PVS) (figura 3, casilla color rosa) y se lleva a cabo la primera distribución del material, el cual se divide en cuatro porciones. La primera se traslada a la mesa de trabajo común, la segunda se utiliza en el área de prueba Porter (figura 3, casilla en color amarillo), la tercera se destina a la prueba Aashto (figura 3, casilla en color gris) y la cuarta se almacena.
El material que se envía a la mesa de trabajo común se somete a la prueba de granulometría gruesa (figura 3, casilla en color celeste) y el material fino obtenido se distribuye nuevamente entre las áreas de trabajo para llevar a cabo las pruebas de límites de consistencia (como se señala en color naranja en la figura 3). Esto incluye la prueba de equivalente de arena, representada en color verde oscuro en la figura 3, así como el envío al área de lavado para continuar con el proceso de granulometría fina, marcado en color morado en la figura 3.
Es importante destacar que durante esta segunda distribución del material se crea un segundo cuello de botella. Esto ocurre porque la cantidad de muestras por procesar puede ser significativa, y algunas pueden tener mayor prioridad que otras según las necesidades del cliente y la temporada de trabajo. La etapa de análisis de una muestra se da por concluida cuando se recopilan los resultados correspondientes de cada área de trabajo y se incorporan en un informe de control de calidad, el cual se entrega primero a la dirección y luego al cliente, como se ilustra en la última etapa de la figura 3.
Por otra parte, la figura 4 muestra un diagrama de spaghetti (Bošnjak y Bošnjak, 2020) del recorrido completo de una muestra a través de cada una de las áreas de trabajo. Este diagrama se elabora considerando los desplazamientos del personal y mide el número de pasos dados para llevar a cabo cada actividad. Es importante señalar que este recorrido se presenta tanto en la mesa número 1 como en la mesa número 2 cuando la carga de trabajo es elevada, lo que permite realizar trabajos de manera simultánea.
Cada color representa una prueba de laboratorio diferente y su recorrido a través de las áreas de trabajo (figura 5). Cabe resaltar que la prueba Aashto se realiza en un área específica fuera del mapa, por lo que no afecta en la toma de resultados.
La mesa de uso común tiene la capacidad de llevar a cabo dos pruebas simultáneamente, pero en la práctica se utiliza generalmente para una sola muestra a la vez. Además, se observa que el personal colisiona constantemente mientras se proveen de materiales de uso común para las pruebas especializadas. Este problema se acentúa especialmente en el caso de la mesa de trabajo común y las básculas, ya que son elementos que el personal necesita con frecuencia.
Adicionalmente, se ha observado una acumulación significativa de herramientas y residuos de materiales en las áreas de trabajo común, lo que crea dificulta las operaciones del personal. En la figura 6, se puede apreciar claramente la acumulación de herramientas fuera de las áreas designadas, lo que resulta en pérdida de herramientas y tiempo al buscar el equipo necesario.
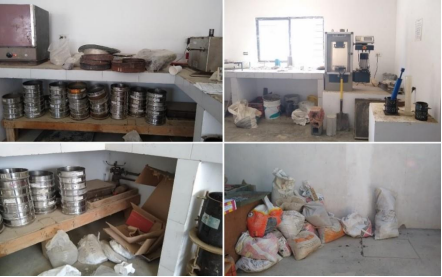
Fuente: Elaboración propia (laboratorio de mecánica de suelos)
Figura 6 Herramienta de uso común invadiendo espacios de trabajo
En las figuras 6 y 7 se observa la acumulación de material de desperdicio y herramienta, tanto debajo las áreas de trabajo común como en las áreas de secado. Esto creaba confusión entre los empleados, pues no sabían si los materiales se encontraban registrados o procesados.
Implementación experimental
Durante la etapa 3 (Implementación experimental), se empleó la herramienta 5’S (Pérez y Quintero, 2017) para atender los problemas de organización. Esto permitió determinar las condiciones en las que se encuentran las herramientas, máquinas y espacios de trabajo para luego ordenarlos y organizarlos siguiendo las recomendaciones de Manzano Ramírez y Gisbert Soler (2016). Además, se emplearon tableros kanban para registrar el avance del flujo de los trabajos.
Implementación de 5’S en las áreas de trabajo
Seiri (eliminar): Se comenzó clasificando y eliminando los elementos innecesarios en las áreas de trabajo. Para eso, se revisó minuciosamente que las herramientas de uso común cumplieran con las especificaciones de los manuales de procedimientos y se las clasificó en tres categorías: en buenas condiciones, para reparar y desperdicio. Las herramientas y equipos que no se utilizarían en un lapso mayor a una semana se almacenaron en la bodega para evitar acumulaciones innecesarias.
Seiton (ordenar): Con las herramientas de uso común en buenas condiciones, se crearon dos juegos completos y se colocaron a ambos lados de la mesa de trabajo principal. También se reubicaron las básculas para permitir que los empleados pudieran trabajar sin chocar entre sí, lo que redujo los movimientos innecesarios (Vilana Arto, 2011). Se tuvieron en cuenta las opiniones y sugerencias del personal, siempre y cuando el jefe de laboratorio lo autorizara y no interfirieran con las operaciones de las otras áreas de trabajo.
Seiso (limpieza e inspección): Se efectuó una limpieza exhaustiva de las áreas de trabajo, retirando todo lo que se consideraba desperdicio y asignando un lugar específico para cada herramienta (figura 8). El área destinada originalmente para la basura y los materiales no deseados estaba invadida por materiales que no podían desecharse hasta que hubiera transcurrido un mínimo de tres meses desde su ingreso al laboratorio. Para evitar deshacernos de materiales que no debían eliminarse, se establecieron áreas separadas para la basura y los materiales guardados. Además, se programó un viernes al mes para desechar los materiales que habían cumplido el tiempo mínimo para ser descartados. Esta actividad fue supervisada por el jefe de laboratorio. También se capacitó al personal y se le permitió realizar mantenimientos preventivos en el equipo para prolongar la vida útil de la maquinaria mientras se esperaba la calibración certificada (Pillado Portillo et al., 2022).

Fuente: Elaboración propia (laboratorio de mecánica de suelos)
Figura 8 Comparativa del área de límites antes (izquierda) y después (derecha) de la implementación de 5’S
Seiketsu (estandarización): Se colocaron ayudas visuales en las áreas de trabajo para guiar al personal en los procesos, siguiendo los manuales correspondientes a cada prueba. También se optó por realizar reuniones informales los viernes antes de finalizar la jornada laboral para plantear dudas y sugerencias que serían analizadas por el equipo.
Shitsuke (disciplina): El jefe de laboratorio asumió la responsabilidad de verificar semanalmente que los empleados mantuvieran sus áreas de trabajo limpias y ordenadas, con el equipo necesario y en buenas condiciones, de acuerdo a las normas y manuales pertinentes. Esta verificación se llevaba a cabo utilizando una lista de verificación exclusiva para el jefe de laboratorio, que detallaba el equipo necesario para cada área de trabajo. El objetivo era que con el tiempo estas actividades se convirtieran en hábitos para el personal.
Implementación de tableros tipo kanban y ayudas visuales
Para facilitar la organización de los trabajos y evitar la pérdida de muestras, se implementó la herramienta kanban, que consiste en una serie de tableros (Gómez et al., 2020) que permitieron al jefe de laboratorio y al personal operativo identificar de manera rápida y clara el progreso de los trabajos, las prioridades y las pruebas atrasadas. Esta metodología ha sido utilizada con éxito por otros investigadores como Torres Ángel (2019) y Bošnjak y Bošnjak (2020) en sus respectivos proyectos.
En la figura 9(a), se presenta el tablero kanban que estuvo bajo la responsabilidad del jefe de laboratorio. En este se dividen las muestras en columnas etiquetadas como “pendiente”, “en curso” y “hecho”, lo que permitió una ubicación eficiente del estado de avance de los trabajos. La figura 9(b) muestra un ejemplo de la tarjeta de trabajo que se utilizó para etiquetar las muestras. En esta se detalla cuáles análisis deben llevarse a cabo, según un checklist incluido. De esta manera el jefe de laboratorio puede marcar las muestras prioritarias con color rojo en la parte superior.
Para el área de la prueba Porter se generó un tablero tipo checklist, el cual permitió llevar un control diario del trabajo realizado. En este la persona a cargo coloca su nombre (figura 9c) con la finalidad de identificar rápidamente a quienes realizaron una actividad.
Para atender las necesidades del área de equivalente de arena, se diseñó un formato de registro (figura 9d) que permite llevar un control de la calidad de los elementos empleados en cada prueba. Esta supervisión se realiza semanalmente por el personal encargado del área para evitar emplear elementos en mal estado o caducados, así como tener un registro de la distribución de los suministros al personal de campo.
Resultados
Durante la etapa 4 (“Resultados y análisis del estado después de la aplicación de herramientas”), se observó que las herramientas lean utilizadas se adaptaron a las necesidades específicas de la empresa. En tal sentido, es importante señalar que muchas de estas herramientas están originalmente diseñadas para líneas de trabajo en cadena. Sin embargo, dado que parte del proceso de la empresa sigue este enfoque, es fundamental recordar que, dependiendo de los tipos de materiales y las variaciones en el proceso, algunas tareas pueden llevar más tiempo o implicar más etapas.
Esta adaptación de las herramientas se vuelve más evidente al comparar su implementación con la de otros autores, como Torres Ángel (2019), Rapale González (2018) y Escudero (2020), lo que permite obtener una visión más completa de las diversas formas en que estas herramientas pueden aplicarse en diferentes contextos.
En el caso específico de la línea de trabajo “terracerías y materiales pétreos”, la implementación de la herramienta 5'S resultó en una reorganización efectiva del flujo de trabajo. Esto posibilitó abordar diversas problemáticas y permitió que ambas áreas de trabajo en la mesa pudieran utilizarse de manera consecutiva sin interferir con el personal que realiza otras actividades. La figura 10 muestra el diagrama de spaghetti del flujo de trabajo propuesto, el cual optimiza los desplazamientos del personal a través de las áreas, lo que minimiza la cantidad de pasos necesarios para cada tarea y reduce las posibles colisiones entre los empleados.
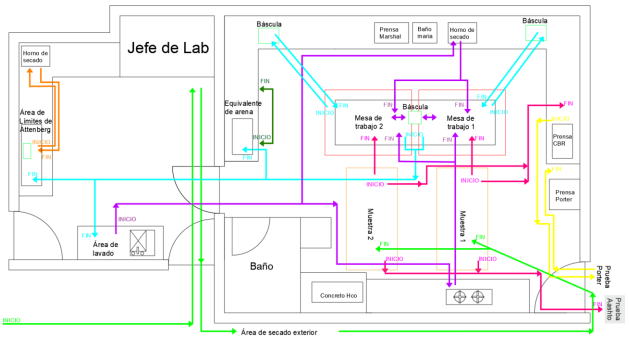
Fuente: Elaboración propia
Figura 10 Diagrama de spaghetti del flujo de trabajo propuesto usando las dos áreas de la mesa de trabajo
Por otra parte, el proceso de manejo de las muestras, que incluye el etiquetado de cada una de ellas (indicado por las flechas de color verde), se lleva a cabo exclusivamente a través de la puerta lateral. Esto permite al jefe de laboratorio llevar un registro detallado de todas las muestras que ingresan al área de trabajo, lo que evita la entrada sin su conocimiento o la pérdida de materiales, y contribuye significativamente a reducir el primer cuello de botella que enfrenta la empresa.
Durante el recorrido de las muestras, el jefe de laboratorio etiqueta los materiales utilizando el sistema kanban y asigna prioridades cuando es necesario. Una vez completado este proceso, los materiales se trasladan al área de secado exterior (si el clima lo permite) sin necesidad de interrumpir las actividades del personal. A diferencia de los sistemas kanban utilizados en grandes industrias (Huerta Estévez, 2021), esta adaptación de los tableros y las etiquetas a una escala menor permite al jefe de laboratorio resolver su necesidad de controlar los ingresos de muestras y sus avances diarios.
En cuanto a la comparación del número de pasos y el tiempo requerido por el personal antes y después de la redistribución de las herramientas, se observa una clara mejora en la eficiencia. En concreto, se redujo tanto el número de pasos necesarios como el tiempo empleado por el personal para desplazarse en las áreas de trabajo, ya sea para obtener herramientas o distribuir materiales, lo que resulta en un flujo de trabajo más eficiente. Además, la rehabilitación del horno de secado en el área de límites de consistencia o Attenberg eliminó la necesidad de que el personal se desplace hasta el horno de secado del área común, lo que redujo el traslado de 44 a 14 pasos.
También se logró un aumento en la capacidad de la empresa para atender trabajos en espera al paralelizar el área de la mesa de trabajo principal (mesa de trabajo 1 y mesa de trabajo 2), lo que permitió procesar hasta diez muestras diarias, en lugar de las seis anteriores, sin descuidar los trabajos asignados a las áreas especializadas.
En la tabla 2 se aprecia una comparación detallada del número de pasos y el tiempo requerido por el personal para realizar cada distribución a través de las áreas de trabajo antes y después de la implementación de las filosofías lean. Estos datos se recopilaron para cada muestra procesada en el laboratorio de mecánica de suelos, lo que permitió una evaluación precisa de los cambios en la eficiencia del proceso. Por ejemplo, antes de la redistribución, en el diagrama de spaghetti del recorrido (figura 4), la línea de cuarteado y distribución de la muestra se destacaba en color rosa. En la mesa de trabajo 1 se requerían 30 pasos, mientras que en la mesa de trabajo 2 se necesitaban 38 pasos, lo que sumaba un total de 68 pasos y un tiempo de 46.2 segundos para completar todo el recorrido antes de la redistribución.
Tabla 2 Número de pasos y tiempo requeridos por el personal en cada área de trabajo
Antes de implementar 5’S | Después de implementar 5’S | ||||
---|---|---|---|---|---|
Tiempo seg. | Número de pasos | Número de pasos | Tiempo seg. | ||
9.1 | Etiquetado 15 |
Etiquetado 14 |
8.5 | ||
25.8 | Secado 36 |
Secado 23 |
17.9 | ||
46.2 | Distribución mesa de trabajo 1 30 |
Distribución mesa de trabajo 2 38 |
Distribución mesa de trabajo 1 5 |
Distribución mesa de trabajo 2 5 |
38 |
33 | |||||
Distribución total | Distribución total | ||||
30+38= 68 |
5+5+33= 43 |
||||
115.2 | Gran. Gruesa mesa de trabajo 1 24 |
Gran. Gruesa mesa de trabajo 2 26 |
Gran. Gruesa mesa de trabajo 1 8 |
Gran. Gruesa mesa de trabajo 2 10 |
32.8 |
Distribución a las áreas de trabajo | Distribución a las áreas de trabajo | ||||
72 | 50 | 18 | |||
Granulometría gruesa total | Granulometría gruesa total | ||||
24+72+26+50= 172 |
8+10+18= 36 |
||||
69.4 | Gran. chica mesa de trabajo 1 53 |
Gran. chica mesa de trabajo 2 50 |
Granulometría chica total | 27.8 | |
Granulometría chica total | |||||
53+50= 103 |
41 | ||||
8.0 | Equivalente de arena 10 | Equivalente de arena 10 | 6.5 | ||
26.6 | Límites de consistencia 44 | Límites de consistencia 14 | 8.5 | ||
24.3 | Porter / CBR 40 | Porter / CBR 38 | 23.7 | ||
324.6 seg 5.41 min |
SUMA TOTAL DE PASOS POR MUESTRA 15+36+68+172+103+10+44+40= 488 |
SUMA TOTAL DE PASOS POR MUESTRA 14+23+43+36+41+10+14+38= 219 |
163.7 seg 2.72 min |
Fuente: Elaboración propia
Al aplicar el nuevo flujo de trabajo (figura 10), la misma línea de cuarteado y distribución de la muestra marca cinco pasos del cuarteado a la mesa de trabajo 1, y cinco pasos del cuarteado a la mesa de trabajo 2. Al realizar la distribución del total de los materiales para trabajar en lugar de distribuirlos uno a la vez, se permite realizar un solo recorrido de 33 pasos, por lo que la suma da un total de 43 pasos y un tiempo de 38 segundos de desplazamientos.
En la figura 11 se muestran las gráficas comparativas del número de pasos que requiere el personal para desplazarse en las áreas del laboratorio (gráfica superior), así como la gráfica comparativa del tiempo en segundos de los desplazamientos del personal (gráfica inferior) por cada área de trabajo antes y después de la redistribución propuesta y de la implementación de 5’S. Con la nueva distribución se observa que al dividir la herramienta en juegos separados y colocarlos en las áreas de trabajo común, las dos mesas de trabajo pueden ser empleadas simultáneamente, sin interrumpir las áreas de trabajo especializadas, lo que reduce el movimiento de los empleados en 44.88 % con el nuevo flujo de trabajo. Esto permite dar solución al segundo cuello de botella que presenta la empresa.

Fuente: Elaboración propia
Figura 11 Número de pasos y tiempo requerido por el personal en cada área de trabajo
En la figura 12 se muestran ejemplos de las áreas de trabajo común una vez implementada la metodología 5’S. Las áreas de trabajo fueron limpiadas, reordenadas e identificadas por medio de letreros visibles para todo el personal. Estas acciones permitieron acomodar las herramientas necesarias para la realización de cada prueba y equipo de uso cotidiano lo más cerca posible. Con esto se acortaron las distancias que necesita el personal para realizar sus actividades.

Fuente: Elaboración propia (laboratorio de mecánica de suelos)
Figura 12 Área de trabajo común después de implementar 5'S
Con la implementación de 5’S y redistribución de herramienta se liberó hasta el 32.37 % del área destinada a trabajos especializados y de uso común (tabla 3 y figura 13). Esto permite que dichas áreas sean empleadas en la realización de pruebas específicas, es decir, ahora no se debe esperar a que se libere la mesa de trabajo común.
Tabla 3 Área de trabajo común liberada
Área de trabajo | m2 por área | % por área | |
---|---|---|---|
Área especializada | 5.26 | 45.78 % | |
Área de trabajo común | Empleada | 2.51 | 21.85 % |
Liberada | 3.72 | 32.37 % | |
Total | 11.49 m2 | 100 % |
Fuente: Elaboración propia
En definitiva, como comentan Bosnjak y Bosnjak (2020), una gestión de calidad puede evitar parte de los errores que comente el personal de una empresa. En el caso del sector de la construcción, además de detectar las necesidades y mejorar la gestión, se busca minimizar errores, disminuir tiempos de trabajo, minimizar accidentes y duplicar la capacidad de trabajo del personal, lo que se traduce en ganancias para la organización.
Discusión
Al comparar las actividades realizadas en la presente investigación con los trabajos desarrollados por Martin et al. (2014), se puede apreciar la utilidad de las herramientas lean para identificar áreas con potencial de mejora en diversos entornos de trabajo, independientemente de su naturaleza. Esta posibilidad permite aplicar estas herramientas tanto en empresas pequeñas como en grandes corporaciones, según las necesidades específicas de cada una.
Por otra parte, es importante señalar que a lo largo de la ejecución de este proyecto se identificaron algunas limitaciones. Una de ellas radica en la falta de información sobre técnicas de optimización en áreas que no pertenecen al ámbito industrial, lo cual se hizo evidente durante las conversaciones con el personal de operación. Otra limitación es la variabilidad en la carga de trabajo, que está vinculada a las fluctuaciones estacionales. Predecir las necesidades de los clientes de la empresa se vuelve complicado en este contexto, lo que resulta en largos periodos de alta demanda seguidos por lapsos de actividad reducida.
Conclusiones
Adaptar y aplicar los principios de lean y sus herramientas (5’S, Kanban, diagramas de spaghetti, Heijunka y ayudas visuales) permitió obtener una mejora en los procesos de la línea de trabajo en el área de “terracerías y materiales pétreos” en un laboratorio de mecánica de suelos, el cual presentaba atrasos en sus tiempos de entrega de resultados. Al estudiar el caso, se encontraron diversos problemas como la falta de orden en las áreas de trabajo, cuellos de botella, acumulación de herramienta y equipo en desuso.
Después de implementar 5’S, se logró reducir el 44.88 % de los movimientos que el personal requería en las áreas de trabajo y se liberó el 32.37 % de las áreas de trabajo común que se encontraban invadidas por herramienta y materiales de desperdicio. Asimismo, fue posible paralelizar trabajos en la mesa de uso común y disminuir los tiempos que requiere el personal al desplazarse por cada trabajo, lo cual aumentó el flujo del trabajo y la cantidad de muestras trabajadas (de seis a diez al día), sin descuidar los trabajos de las áreas especializadas.
Al implementar tableros tipo kanban y checklist se logró controlar el avance de los materiales, y al colocar ayudas visuales en las áreas de trabajo especializado se disminuyeron los errores que presentaban los trabajadores durante el proceso de manipulación de materiales. Esto redujo los accidentes que se producían por no seguir los protocolos correspondientes.
Como trabajo futuro la empresa se plantea implementar herramientas kaizen de mejora continua con ayuda de todo el personal. Por último, se busca ampliar el panorama del uso de las herramientas lean en industrias diferentes a las manufactureras. Esto evidencia la adaptabilidad y efectividad en ámbitos que no cumplen con las características clásicas del sector industrial.
Futuras líneas de investigación
El tema de implementación de metodologías provenientes de la industria para dirigir y gestionar los recursos en empresas de construcción es muy amplio debido a la diversidad de áreas involucradas. Esto abre un amplio espectro de posibilidades para futuras investigaciones, que pueden abordar temas que van desde la administración interna de la empresa hasta la optimización de los procesos en el lugar de trabajo, ya sea en la empresa matriz o en proyectos de construcción específicos.
Por eso, un posible trabajo futuro sería la aplicación de la metodología lean para mejorar la comunicación entre el laboratorio de mecánica de suelos y otras áreas de trabajo, particularmente aquellas relacionadas con la ejecución de proyectos en el sitio de construcción. Este enfoque apuntaría a mejorar la fluidez de la información, especialmente en el ámbito administrativo y gerencial, lo que podría tener un impacto significativo en la eficiencia general de la empresa.
Otra área de investigación con potencial es la optimización de la programación y uso de maquinaria dentro del laboratorio de mecánica de suelos. Este enfoque estaría dirigido a mejorar los tiempos y procesos en el área operativa del laboratorio con el objetivo de minimizar el desperdicio asociado con la utilización de maquinaria y recursos disponibles.