1. Introduction
The most common material in construction is reinforced concrete, whose mechanical and chemical properties are important for reliability. However, impairment of concrete structures, which is associated with corrosion in the reinforcement bars, has been reported in the literature (Pérez, 2009). Most bridges and piers in México have been built using concrete reinforced with carbon steel. An exception is the pier in Progreso, Yucatán, and some sections of the pier in Coatzacoalcos, Veracruz. The former uses stainless steel as reinforcement material and the latter galvanized steel. This information indicates that the resistance against aggressive environments is limited (especially in the case of environments with chloride ions and carbon dioxide). Traditionally, different types of methods are applied for counteracting the corrosion damage in concrete structures. Those methods can be classified into four categories based on the protection mechanism (Kepler, 2000):
●Concrete matrix modification
Water/ concrete ratio; Adding cementing materials
●Barrier Methods
Polymer coatings; Paintings; Metallic coatings
●Electrochemical Methods
Cathodic protection by impressed current (ICCP) or galvanic anodes (CPGA); Corrosion inhibitors; Electrochemical extraction of chlorine ions; Electrochemical re-alkalinization.
●Rehabilitation of concrete structures with new materials.
Composite materials, Stainless Steel.
The rehabilitation and refurbishing techniques are many and diverse; some are applied to the steel, others in the concrete, and others in both materials (Gonzalez 2010). The preservation of infrastructure is vital in both economic and social terms, because it provides security and supports social development. However, concrete structures corrode and must be repaired after 10, 20, or 30 years of service because the consequences affect not only the structural integrity but also human safety. Moreover, corrosion reduces the functionality and the value of a structure, leading to large financial expenditures needed to repair, refurbish, or replace the corroded infrastructure. Owing to these reasons, there is a need to develop processes for controlling and preventing corrosion in reinforcement steel bars embedded in concrete structures (Rougier, 2010; Terradillos, 2008). In this way, stainless steel reinforcement bars for concrete structures represent an attractive option that has been proposed for several years in order to increase the endurance of concrete in aggressive environments (BSSA, 2003;Medina, 2013).
Many researchers, for instance Brown (1976), Treadaway (1989), Sorensen (1990), Nurnberger (1996) McDonald (1998), Pedeferri (1997), Bertolini (1998), and Baltazar (2007), have carried out studies to evaluate the behavior of stainless steel as reinforcement material for concrete structures. On the other hand, Lundin, (1982), Doddy, (1992), Ospina, (2007), García (2011), and Pérez-Quiroz (2016) have researched the metallurgy and mechanical properties of dissimilar welded joints, and their results demonstrated that the application of these joints is feasible for refurbishing concrete structures. Considering that stainless steel is more expensive than carbon steel, carbon and stainless-steel reinforcement bars can be joined by connectors or weld joints to improve the corrosion resistance of a concrete structure and reduce costs.
Perez Quiroz (2016) pointed out that to avoid carbon diffusion into the stainless steel and to minimize the damage risk due to corrosion during welding, buttering using Inconel 182 is a good option. Thus, it is desirable to investigate the metallurgy of dissimilar welded joints and the corrosion behavior of such welded unions. Today, there are few studies that evaluate the corrosion behavior of joints between carbon and stainless steel with and without buttering using Inconel. Therefore, in this work the corrosion resistance of welded joints between carbon and stainless-steel bars with and without buttering using Inconel 182 was tested to evaluate this methodology for refurbishing the concrete structures of maritime piers (Figure 1).
2. Experimental procedure
The materials and processes applied in this project were selected under two criteria: cost of the joint(s) and feasibility for field application of the welding process and electrodes. Table 1 lists the materials, equipment, and chemicals that were used in this research, and Table 2 provides the chemical compositions of the base metals, 309L electrode, and Inconel filler metal.
Table 1 Materials, equipment, and chemical solutions.
Materials | Equipment | Chemical solutions |
---|---|---|
ASTM A615 reinforcement bars. AISI 304 reinforcement bars. ER 309L electrode Inconel 182 electrode |
Saw cutting machine Automatic disc cutting machine Conventional lathe machine Conventional milling machine Castolin Eutectic, Master NT2000 AC/DC welding machine Electro discharge machine Grinding double disc machine Polishing double disc machine Magnetic heater Fluke multimeter Gamry interface1000 equipment Reference electrode Ag/AgCl |
3.5 weight % Sodium chloride solution (NaCl) (sea
water). Saturated solution calcium hydroxide (Ca (OH)2) |
Table 2 Chemical compositions of base metals, 309L electrode and Inconel filler metal.
Steel | C | Si | Mn | P | S | Cr | Mo | Ni | Al | Co | Cu | Fe |
---|---|---|---|---|---|---|---|---|---|---|---|---|
ASTM A 615 | 0.24 | 0.18 | 0.77 | 0.03 | 0.03 | 0.08 | 0.04 | 0.07 | 0.01 | 0.01 | 0.23 | 98.3 |
AISI 304 | 0.01 | 0.33 | 1.39 | 0.07 | 0.03 | 18.1 | 0.27 | 8.61 | 0.01 | 0.18 | 0.38 | 74.1 |
Element | C | Mg | Si | Cr | Ni | Fe | ||||||
Composition 309L (%) | 0.03 | 1.92 | 0.80 | 23.8 | 13.3 | Balance | ||||||
Element | C | Si | Mn | P | S | Cr | Ni | Nb | Fe | >Ti | ||
Composition Inconel (%) | <0.1 | <1 | 5-9.5 | <0.03 | <0.015 | 13-17 | >59 | 1-2.5 | <10 | ><1 |
The identification of the samples was made as indicated in Table 3.
Table 3 Designations of test samples.
Designation | Type of sample |
---|---|
A.C. SW | ASTM A615 carbon steel in NaCl 3.5% wt solution |
A.I. SW | AISI 304 stainless steel in NaCl 3.5 % wt solution |
A.C. HC | ASTM A615 carbon steel in calcium hydroxide |
A.I. HC | AISI 304 stainless Steel in calcium hydroxide |
Dissimilar welded joint BsAM1 | Single bevel joint without buttering in NaCl 3.5 % wt solution |
Dissimilar welded joint BcAM2 | Single bevel with buttering in NaCl 3.5 % wt solution |
Dissimilar welded joint BsHC1 | Single bevel joint without buttering in calcium hydroxide |
Dissimilar welded joint BcHC2 | Single bevel joint with buttering in calcium hydroxide |
The samples were carbon and stainless-steel bars with the following dimensions: 1.9 cm in diameter and 10 cm in length (Figure 2). The bevel of the joint was prepared at 45°, in accordance with NMX-H-121-1988 and ANSI/AWS D1.4-M 2005. The welding process for the joints was Shielded Metal Arc Welding (SMAW), because this process is the most commonly used in field welding of reinforcement bars.
The applied filler metal for the welded joints was AISI 309L stainless steel. In the case of buttering welding, the electrode was Inconel 182. This step consisted of applying a 2 mm thick layer on the frontal surface of the AISI 304 bar. The welding machine was a Castolin Eutectic, Master NT2000 AC/DC and the welding parameters are given in Table 4.
Table 4 Welding parameters.
Diameter of the bar (mm) | 19 |
Diameter of the electrode (mm) | 3.2 |
Electric potential (V) | 22 |
Welding intensity (A) DC-PI | 90-95 |
Welding speed (mm/min) | 45 |
Heat input (kJ/mm) | 2.5 |
After welding, the samples were longitudinally and transversally cut with an ACTSPARK electrical discharge machine. The samples were mounted in epoxy and then prepared for metallography according to ASTM E 3. Before polishing, the stainless-steel base metal of each sample was drilled to introduce a copper wire to achieve the electrical contact necessary for electrochemical testing. The corrosion behavior of the welded dissimilar joint was evaluated with a Gamry Interface 1000 potentiostat (Figure 3) by applying the following electrochemical techniques: measurement of corrosion potential according to ASTM C 876; linear polarization resistance test in accordance with ASTM G 59, and electrochemical noise measurement under ASTM G 199.
Linear Polarization Resistance (LPR)
This technique consists of measuring the relationship between the potential and the current density in steady state, exciting the system by application of direct-current signals. To perform the Rpl test, a three-electrode cell was used: the reference (Ag / AgCl), an auxiliary electrode (graphite), and the working electrode was an AC / SS specimen. The electrodes were placed in the cell and the Rpl test was performed using the Gamry interface1000 potentiostat with the following settings: scanning of +/- 20 mV with a scanning rate of 10 mV / min, in accordance with ASTM G 59.
Electrochemical Noise (EN)
Electrochemical noise is a technique that measures the spontaneous fluctuations of the potential and the current in electrochemical systems, which are of low frequency (<10 Hz) and amplitude. Electrochemical noise originates, in part, from natural variations in electrochemical kinetics during a corrosion process. Frequently, EN is considered and analyzed as a random (stochastic) phenomenon coupled to deterministic kinetics.
The EN technique was performed with the help of a Gamry Interface 1000 potentiostat. This equipment is capable of measuring in real time the oxide-reduction phenomena that occur in the electrodes. The number of readings per test piece was 2048, with stabilization time of 10 seconds; the test time was 45 min. This test requires three electrodes, two are identical steel electrodes, and a silver / silver chloride (Ag / AgCl), as reference electrode.
3. Results and discussion
Before electrochemical testing, the samples were observed using a stereoscopic microscope, and cracks were observed in the samples where buttering was carried out (Figure 4); those cracks (approximately 2 mm in length) are associated with hot cracking owing to the nickel content in the Inconel 182 used for buttering. Recall that buttering is applied to dissimilar welded joints in order to prevent carbon diffusion, phase segregation, and chromium carbides precipitation, as these phenomena influence corrosion behavior in stainless steel. The results match those of Evans (1962), who reported that nickel alloys welded to stainless steel are susceptible to hot cracking. The macrographs in Figure 4 show some lack of fusion near the carbon steel/filler metal/ buttering interface. Such defects should not influence the corrosion behavior of the welded joint because they are in the interior of the metal, but if the electrolyte were to make contact with them, they would become an anode and would allow localized corrosion. On the other hand, they have a strong impact on the mechanical properties because they act as stress risers / concentrators.
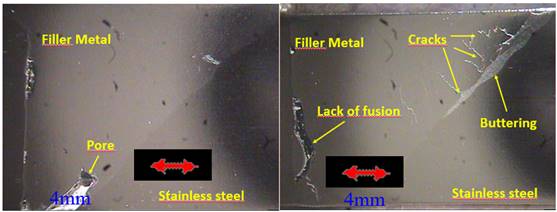
Figure 4 Samples at 7x magnification showing cracks and lack of fusion of the dissimilar welded joints.
3.1 Corrosion potential (Ecorr).
In Figure 5, the results of the corrosion potential of the base metals are shown. Measurements were carried out over 14 days for samples immersed in NaCl and Ca(OH)2. In Figure 5, the more negative values occur for carbon steel in salt solution (A.C.), which simulates sea water. Such results indicate a high probability of corrosion under ASTM C 876 (2015). Sistonen (2002) indicated that such values represent a severe risk of corrosion. In the case of the stainless steel (A.I.), the results of the corrosion potential are more positive than for carbon steel in the same solution and in accordance with ASTM C876 (2015), the results fall within the uncertainty zone. Such results can be explained by the passive layer of chromite on the stainless steel, which protects the material to some extent. Sistonen (2002) suggested that the corrosion potential should be interpreted based on the criteria shown in Table 5.
Table 5 Criteria for corrosion potential of carbon steel and stainless steel (Sistonen, 2002).
Corrosion condition | Black Steel bar mV vs CSE | Stainless Steel bar mV vs CSE |
---|---|---|
Low corrosion risk around 10% | > - 200 | > - 100 |
Medium corrosion risk | - 200 a - 350 | - 100 a -250 |
High corrosion risk < 90% | - 350 a - 500 | -250 a - 400 |
Severe corrosion risk | < - 500 | < - 400 |
In the case of the Ca(OH)2 solution, the corrosion potential results for both base materials are more positive than in sea water because of the alkalinity of the Ca(OH)2 solution, per the ASTM C 876 (2015) standard. The same standard mentions that the probability for damage of carbon steel in such environments is minimal. Based on Sistonen’s (2002) criteria, both steels are in the medium corrosion risk category.
Figure 6 shows the relationship between corrosion potential and time for single bevel welded joints in 3.5 wt % NaCl solution. The values fall within the high probability corrosion range according to ASTM C 876 (2015), but in accordance with Sistonen (2002), they fall within the range of severe corrosion risk. Note that the variation of the corrosion potential of sample BsAM2 was caused by experimental error, although the trend follows the other samples, where the corrosion risk is high.
By comparing Figure 5 to Figure 6, it is not easy to detect any effect of the buttering on corrosion potential. However, such comparison indicates that the corrosion potential of an entire joint dropped to more negative values, which are very similar to the values of carbon steel immersed in sea water. These results indicate higher corrosion susceptibility.
Regarding samples in the sodium chloride (NaCl) and calcium hydroxide (Ca(OH)2) solutions, the trend of the corrosion potential values with respect to time is between -0.500 V to -0.670 V vs Ag/AgCl, because the more active metal is carbon steel (Figure 5) according to ASTM G 82. Because the corrosion potential of carbon steel is -approximately -0.600 V vs the stainless-steel potential which is -0.300 V vs Ag/AgCl (Figure 5). The potential values shown in Figure 6 with respect to ASTM C876 indicate that there is a 90% probability of corrosion because they are more negative than -0.350 V vs Ag/AgCl. Figure 6 also shows that the value of the corrosion potential is in the range of -0.500 V to -0.650 V vs Ag/AgCl.
Samples with higher numbers of defects (pores, cracks, etc.) were selected for testing in calcium hydroxide to investigate if they generated a passive layer, which reduces the corrosion rate. Figure 7 shows the results, indicating that after 15 days, the values are in the probable corrosion range according to ASTM C 876 (2015) and Sistonen (2002). However, after 20 days the corrosion potentials changed to more positive values. These results indicate that the corrosion process occurred during the first 14 days, after which a compact, adherent passive layer was formed on the surface of the samples owing to the alkalinity of the environment, according to ASTM C 876 (2015) and Sistonen (2002). Thus, based on these criteria, further corrosion damage in carbon steel, stainless steel, and the welded joint should be minimal. Note that for this test, samples with a higher number of defects were selected (with and without buttering). Thus, the results suggest that alkaline conditions lead to minimal damage due to corrosion in the case of reinforcement bars for concrete.
3.2 Measurements of corrosion rate based on polarization resistance.
Figure 8 shows the corrosion rates for the samples immersed in sea water, where all rates are in the range between 0.15 to 0.25 mm/y. The values are 10 times higher than the recommendations made by DURAR (1997). Thus, it can be stated that corrosion under these conditions is unavoidable for the base material and the filler metal. As mentioned previously, the electric connection of sample BsAM2 was lost, indicating why the values of that sample are almost zero.
Figure 9 displays changes in corrosion rate for calcium hydroxide, which are related to the beginning of the corrosion process and the possible passivation of the sample surfaces because of the alkaline medium in which the samples were tested.
Figure 9 shows the corrosion rates of the welded joints immersed in a calcium hydroxide solution, which are many orders of magnitude lower than the corrosion rates in sea water (see Figure 8). As mentioned previously, this can be explained by the formation of the passive layer due to the alkaline environment of the solution, even with the welding defects shown in Figure 4. These facts support the argument that stainless steel is a good option for partly substituting carbon steel in reinforcement bars in concrete structures, as those shown in Figure 1. Moreover, assuming that stainless steel bars were embedded in new concrete, the material would already be passivated and severe corrosion damage would not occur quickly. The previous statement is justified by the Pourbaix (1966) diagram of iron, which indicates that in the alkaline ranges, it is protected by passivation.
Researchers such as Medina (2012), Bastidas (2014), Velasco (2013), Sanchez (2013), Bautista (2013), Acosta (2013), Landmann (2013), Andrade (1993), and González (1984) have reported good performance of stainless steel even in saline environments, because the dangerous corrosion rate level for concrete structures (100-125 μm/y) is higher than the results they obtained for stainless steel. Figure 8 verifies that the corrosion rates of the samples are higher than the recommended range of rates, while Figure 9 indicates corrosion rates are substantially lower than those ranges. Thus, repairs using stainless steel would meet the specification for an alkaline environment.
3.3 Measurements of corrosion rate by electrochemical noise
The metallurgical effect of corrosion behavior on welded joints was evaluated using electrochemical noise. This technique consists of setting two electrodes in an electrolyte as described in Chapter 2 of ASTM C 199 and is shown in Figure 3. The results of this technique are shown in Figures 10-13. Two variables characterize the corrosion behavior of the samples: noise resistance (Rn), which is equivalent to polarization resistance; and the second variable is the localization index (IL), which points out the corrosion form of the samples. The following criteria apply: uniform corrosion (0.001 to 0.01), mix between uniform and localized corrosion (0.01 to 0.1), and finally localized corrosion (0.1 to 1). Those criteria have been previously considered by Eden (1987), Kelly (1996), Mansfeld (1999), and Balán (2017).
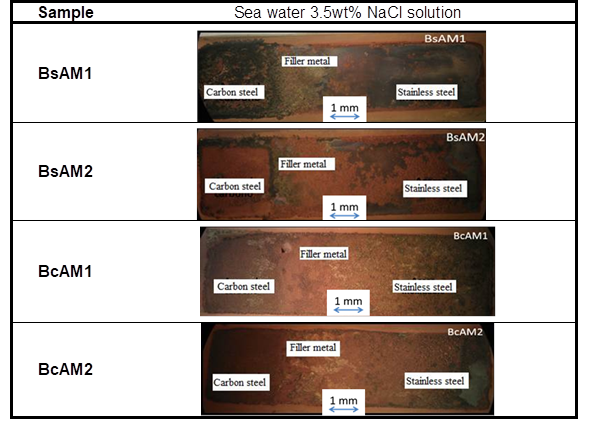
Figure 11 Stereographic images of BsAM and BcAM tested in sea water (3.5wt % NaCl solution). (Ramírez 2016)
Figure 10 shows that the values of IL of the BsAM samples are in the localized corrosion range. Recall that those samples had no buttering layer and were immersed in sea water. Therefore, corrosion is expected in those samples. Figure 11 shows that the corrosion products are on specific spots of the sample surfaces, as predicted by ASTM G 199.
Although the values of IL of the BcAM samples are in the localized corrosion range, the corrosion products are uniformly distributed on the sample surfaces, which agree more closely with the mixed corrosion criterion. This suggests that buttering leads to more uniform corrosion. The general scientific consensus is that uniform corrosion is less aggressive than pitting and crevice corrosion, because the latter types of corrosion cause structural damage and can lead to catastrophic failure.
Figure 12 shows the results of the samples tested in calcium hydroxide. Those results indicate localized corrosion occurs in the defects of the welded joint (as can be observed in Figure 13), where such corrosion occurs by the formation of differential aeration corrosion cells. Sample BsHC, which did not contain welding defects, exhibited a white layer on the surface of the welded joint (Figure 13), which inhibited corrosion. Therefore, the only places susceptible to localized corrosion were the welding defects.
In this case, the behavior of sample BsCH is related to the graph of Figure 12. This sample shows a corrosion tendency like BcCH because the results of both samples are in the localized corrosion range. However, in the case of BcHC it is considered that corrosion is associated with welding defects as well as with localized dissolution of the nickel layer. As explained by Pourbaix (1966), nickel corrodes slightly in alkaline solutions before forming a passive layer. The behavior of the BcHc sample agrees with this statement and explains the differences in the results between the two samples.
Figure 13 shows stereographic images of samples tested in calcium hydroxide, which were covered with a white color layer (calcareous deposit), which forms a passive layer on the samples’ surfaces.
Resistance noise (Rn) is a very powerful tool to assess the low corrosion rate of the BsHC and BcHC samples immersed in calcium hydroxide and is similar to polarization resistance. Therefore, this technique was applied to those samples and the results are shown in Figures 14 and 15. ASTM G 102 (2015) specifies the relationship between Rp and icorr, which is inversely proportional. In other words, the higher the values of noise resistance, the lower the corrosion current density, indicating a lower corrosion rate. Samples in sea water (NaCl 3.5wt% solution) exhibited lower noise resistance values than the samples in the Ca(OH)2 solution, thus had a higher corrosion current density, indicating higher corrosion rates. Figures 14 and 15 highlight these results. The results agree with the results reported by Kelly (1996) and Garcia (2014).
4. Conclusions
The results of this work indicate that refurbishing of concrete structures using stainless steel is feasible, particularly if the steel is passivated. The construction or repair of a concrete structure must be carried out following the applicable standards in order to verify that the repaired area undergoes passivation to reduce future corrosion.
Measurements of corrosion potential were useful to determine the corrosion behavior in two different environments for bars made of carbon steel, stainless steel, and a dissimilar metal welded joint between the two materials buttered with Inconel 182 and without buttering. It was found that carbon steel in sea water is susceptible to corrode with 90% probability, while stainless steel is in the range of uncertainty. However, essentially opposite results were obtained for an alkaline environment (Ca(OH)2 solution), where the probability of corrosion was 10%.
Both dissimilar welding joints with and without buttering resulted in a 90% probability of corrosion in sea water, while in the alkaline media the probability of corrosion for either joint decreased to 10%. This was explained by a passive layer found on the sample surfaces.
The corrosion rate of the welded joint with buttering was lower in an alkaline environment (Ca(OH)2 solution) than in sea water (NaCl 3.5 wt% solution). These results were also explained by formation of a passive layer on the surface defects of the samples in the alkaline environment.
The results of electrochemical noise were used to describe electrochemical behavior in the alkaline solution and in sea water of welded joints with and without buttering. The results indicated that the corrosion type on such samples was mixed corrosion, and they match the results obtained by polarization resistance and corrosion potential measurements.