Serviços Personalizados
Journal
Artigo
Indicadores
-
Citado por SciELO
-
Acessos
Links relacionados
-
Similares em SciELO
Compartilhar
Revista mexicana de ciencias agrícolas
versão impressa ISSN 2007-0934
Rev. Mex. Cienc. Agríc vol.7 no.1 Texcoco Jan./Fev. 2016
Articles
Isolation and characterization of cellulose obtained from Agave salmiana fibers using two acid-alkali extraction methods
1Escuela Nacional de Ciencias Biológicas-IPN. Carpio y Plan de Ayala S/N. México, D. F. C. P. 11340, México.
2Instituto Mexicano del Petróleo. Eje Central Lázaro Cárdenas 152, San Bartolo Atepehuacan, México, D. F. C. P. 07730.
3CEPROBI- IPN, Carretera Yautepec-Jojutla, km 8.5, Col. San Isidro, A. P. 24, C. P. 62731, Yautepec, Morelos, México.
4Escuela Superior de Física y Matemáticas-IPN. Av. Instituto Politécnico Nacional S/N, San Pedro Zacatenco, C. P. 07738, México, D. F.
5Instituto Tecnológico del Altiplano de Tlaxcala, San Diego Xocoyucan, Tlaxcala, Tlaxcala.
Fibers were obtained in order to make use of the agave leaves (A. salmiana) once the heart of the plant was removed. The leaves were treated with acid hydrolysis (HCl) and alkaline hydrolysis (NaOH), using a pressure of 1.1 kg/ cm2 (acid-alkali TAF with pressure). The percentage of cellulose and lignin was determined, as well as the physicochemical changes through Differential Scanning Calorimetry (DSC), Thermogravimetric Analysis (TGA), X-ray Diffraction (XRD), Infrared Spectroscopy (IR) and Environmental Scanning Electron Microscopy (ESEM). The highest cellulose content (79.95%) was obtained from the acid-alkali TAF treatment without pressure, presenting a higher crystallinity as well (50.07). The microstructure showed that the acid-alkali TAF treatment with pressure presented more empty spaces, this due to the degradation of the fibers which is associated with cellulose loss. Both treatments affected the structure and composition of the agave fibers.
Keywords: acid-base treatment with pressure; acid-base treatment without pressure; agave fibers; cellulose; lignin
Para aprovechar las pencas de agaves (A. salmiana) una vez que se retiran de la piña de la planta, se obtuvieron fibras. Las hojas fueron tratadas con hidrólisis ácida (HCl) e hidrólisis alcalina (NaOH), usando presión de 1.1 kg/cm2 (FACT ácido- álcali con presión), a 121 °C por 4 h y otro tratamiento a presión atmosférica con reflujo (FACT ácido-álcali sin presión). Se determinó el porcentaje de celulosa y lignina, así como los cambios fisicoquímicos por medio de calorimetría diferencial de barrido (DSC), termogravimetría (TG), Difracción de rayos X (DRX), Espectroscopia infrarroja (IR) y Microscopia electrónica de barrido ambiental (MEB). El mayor contenido de celulosa (79.95%) se obtuvo para el tratamiento FACT ácido-álcali sin presión, presentando también una mayor cristalinidad (50.07). La microestructura mostró que el tratamiento FACT ácido-álcali con presión mostró más espacios vacíos, esto debido a la degradación de las fibras, lo cual se asocia a una pérdida de celulosa. Ambos tratamientos afectaron la estructura y composición de las fibras de agave.
Palabras clave: celulosa; fibras de agave; lignina; tratamiento ácido-base sin presión; tratamiento ácido-base con presión
Introduction
Agave is a xerophytic plant used for the elaboration of unconventional alcoholic beverages such as pulque or mezcal. In order to produce 1 L of mezcal, 15 kg of Agave salmiana are needed, generating 6 kg of bagasse as a waste product (López-Álvarez et al., 2012). As a result, the waste material from the heart or the head of the maguey left in the field during the harvest is approximately 10.5 kg per plant, and is mainly comprised of leaves, rhizome and lateral thorns. Chávez-Guerrero (2010) reported that in 2007 around 1 692 tons of bagasse (dry base) were obtained from the production of mezcal in the state of Tamaulipas, not considering the organic material that remained in the field.
This lignocellulosic material can be used through superficial fiber treatments. For example, when the process of maceration is applied together with the use of acid-alkaline treatments, the separation of hemicellulose and lignin fibers occurs, which also improves the fibers in regards to their thermal stability and tensile strength, necessary factors for the elaboration of composites. These treatments also help the elimination of impurities such as waxes, pectin and mineral salts increasing surface area (Saucedo et al., 2010; Sghaier et al., 2012; Rosli et al., 2013).
The particle size reduction in the fibers generates a larger contact surface area with chemical substances such as acids and alkalis, which together with the pressure succeed in further modifying the fibers. The aim of this work was to obtain treated fibers with a high cellulose content from the native fibers of A. salmiana, and to characterize them through thermogravimetric, spectroscopic and microscopic techniques in order to use them in the food industry as fiber or as material for the manufacturing of biodegradable packaging.
Materials and methods
Materials
A. salmiana leaves of approximately 8 to 19 years old were used; they were obtained from plantations in the state of Tlaxcala, Mexico. These leaves were washed, weighed, stripped from all cuticles, pressed, dried at 70 °C for 12 h, lyophilized for 12 h with the intent of processing them, and finally grinded until obtaining a powder with particles the size of 120 microns. These samples were designated untreated agave fibers (UAF).
Preparation of agave fibers
Powdered leaves were subjected to two different treatments. In treatment 1, a modification to the acid-alkaline hydrolysis process was used as suggested by Saucedo et al. (2010) aiming to separate the non-fibrous components. For this, a first acid hydrolysis was carried out on the powdered leaves, using a HCl solution at 2% at 60 °C for 2 h, using a ratio of 1:100 (p/v) in a round-bottom flask equipped with a reflux condenser and an electric burner at a constant temperature. Afterwards, it was neutralized to a pH of 7.0 with an alkaline solution (NaOH 20%), centrifuged (8 049 x g for 10 min), and washed with distilled boiled water. It was then centrifuged again in the same conditions.
The separate solid residue was placed in a round-bottom flask and 2% ammonium oxalate was added at a ratio of 1:30 (p/v), adjusting the pH to 3.5. It was stirred constantly at 50 °C for 4 h, and then left to settle for 1 h at 85 °C. This was done in order to increase the formation of calcium oxalate, which was then eliminated with an acid solution. Once the process was over, the solution was centrifuged (8 049 x g for 10 min) and 200 ml of 95% ethyl alcohol were added, letting it settle for 12 h at 5 °C for the precipitation of the pectin.
Once the insoluble residue was separated, it was then centrifuged (8 049 x g for 10 min) and a second acid hydrolysis (H2SO4 4%) was applied to the solid obtained in a ratio of 1:30 (p/v) with controlled stirring and a temperature of 130 °C for 1.5 h in order to eliminate the greatest number of reducing sugars. It was centrifuged (8 049 x g for 10 min) and the solid obtained was placed inside a round-bottom flask. In order to break the lignin links, an alkaline hydrolysis with 5% NaOH for 1.5 h at 70°C (ratio 1:30 p/v) was done. Two washings of the sample were done with distilled water with a ratio of 1:30 (p/v), the first of these at 70 °C and the second at 90 °C, both for 1.5 h. These samples were designated treated fibers without pressure (TAF without pressure).
For treatment 2, the technique reported by Hernández et al. (2009) was used. A solution of HCl at 1.2% in a ratio of 4:60 (p/v) was added to the powdered agave fibers through an autoclave at 121 °C for 4 h and a pressure of 1.1 kg/cm2. The pH was adjusted to 5.0 with NaOH and centrifuged (3.08 x g 10 min at 5 °C). Distilled water was added to the solid obtained in a ratio of 30:1 (p/v) and then it was centrifuged (8 049 x g for 10 min at 5 °C). A solution of NaOH at 2% (p/v) was added to the supernatant and it was then placed in an autoclave at 121 °C/1.1 kg/cm2/4 h. It was centrifuged (10 397 x g /10 min/5 °C) and decanted, and then the precipitate was used adding 250 ml of doubly distilled water and placed once again in an autoclave under the same conditions. It was then centrifuged and the residue was lyophilized. These samples were designated treated fibers with pressure (TAF with pressure).
Chemical composition
A. Salmiana fibers were subjected to a chemical analysis for the determination of the ash content 31.013 AOAC (1985), total reducing sugars (Ting, 1956), lignin through the Klasson method and cellulose-lignin according to the standard ISO 13906:2008 (CEN/TC327, 2009). The cellulose content was determined through a value difference of cellulose-lignin determined by the standard ISO 13906:2008 (CEN/ TC327, 2009).
Thermogravimetric analysis (TGA) and infrared spectroscopy (IR-FT)
The untreated agave fiber samples (UAF) and the treated fibers (TAF) were analyzed in a thermogravimetric equipment (Equinox, Bukkler, Finland) coupled with a thermoanalyzer (STA 409 PC Luxx, Netzsch, Germany) and a module of infrared spectrometer with Fourier transform in order to characterize the fibers with their functional groups. The conditions were: nitrogen flow of 4 cm3 min-1, temperature of 50 to 380 °C, flow speed of 10 °C min-1, and wavelength of 4 000 -500 cm-1 with a resolution of 4 cm-1.
Differential scanning calorimetry (DSC)
The UAF and TAF samples were analyzed in a calorimeter (DSC 2010, TA Instruments Inc, USA) within a temperature range of 80 to 620 °C, with increases of 10 °C min-1. Each determination was done separately under nitrogen atmospheres with a flow of 20 cm3 min-1. This technique was used in order to determine the transition phases of the fiber components.
X-ray diffraction (XRD)
The TAF and UAF samples were analyzed using a diffractometer (Bucker D8 Advance Vantec, Germany) using radioactive Cu Kα (1.5418 Ǻ), a Ni filter and a scintillation counter as a detector at 35 kV and 30 mA in rotation from 3 to 37° at a scale of 2θ according to the technique described by Singha and Rana (2010). The samples were pulverized and homogenized before being exposed to X-rays. These were distributed in the cavities of the support. The crystallinity index (CI) was determined using the diffraction count at an angle of 2θ close to 15 and 22°, which was calculated based on the following formula:
Where: Ic and Ia are the crystalline and amorphous intensities at a scale of 2θ at 15 and 22°.
Morphologic characterization through environmental scanning electron microscopy (ESEM)
The morphology of the UAF and TAF samples with and without treatment were analyzed using an environmental scanning electron microscope (XL30, Philips, England), tungsten filament at a pressure of 0.94 torr, a temperature between 2-20 °C and a resolution of 3.5 nm. The chemical composition of the UAF and TAF was determined through an X-ray spectrum detector of dispersive energy (Edax, USA) attached to the environmental electronic microscope, using the “Microanalysis System Software” 3.31XL version.
Results and discussion
Chemical composition
The chemical composition of the UAF and TAF under their two treatments can be observed in Table 1. The UAFs are mainly comprised of cellulose in 48.94 ± 5.27%, as well as lignin in 8.48 ± 1.78%, respectively. While the TAF under acid-alkali treatment with pressure obtained a value of 33.23 ± 6.28% cellulose, the TAF under the acid-alkali treatment without pressure obtained a value of 79.95 ± 16.9%. The first TAF treatment had 61.82 ± 5.85% lignin, and the second TAF treatment 8.12 ± 0.38%; in this case, it can be observed that the NaOH was efficient in the decrease of the presence of lignin, weakening its links, as well as the waxes and pectins. The acid-alkali TAF treatment with pressure was more drastic as it presented a cellulose loss of 67.89% concentrating on the lignin ratio.
Table 1. Chemical composition of A. salmiana fibers without treatment and acid-alkali treatments with and without pressure.
Lignina (%) | Celulosa (%) | Otros a | Cenizas | |
---|---|---|---|---|
A. salmiana FAST | 8.48±1.78 | 48.94±5.27 | 40.26 | 2.32±0.92 |
A. salmiana FACT ácido-álcali con presión | 61.82±5.85 | 33.23±6.28 | 1.53 | 5.27±1.71 |
A. salmiana FACT ácido-álcali sin presión | 8.12±0.38 | 79.95±16.9 | 4.75 | 7.18±0.18 |
On the other hand, H2SO4 acts in the hydrolysis of the hemicellulose, calcium oxalate and the fructooligosaccharides according to what was reported by Summerscales et al. (2010). The difference presented with the TAF under acid-alkali treatment with pressure is due to the dual effect of the action of the acid-alkali and the pressure, which generates a hydrolysis of the cellulose. The content of reducing sugars in the acid-alkali UAF and TAF with and without pressure was very low, with concentrations of 0.10±0.005% for UAF, 0.000% for acid-alkali TAF with pressure and 0.02±0.004% for acid-alkali TAF without pressure.
Infrared spectrometry (IR-FT) and thermogravimetric analysis (TGA)
Infrared spectrometry
The IR-FT specters were carried out in order to characterize the chemical structure when identifying the functional groups present in each sample. These are shown in Figure 1. The 1164 cm-1 band can be attributed to the location of asymmetrical valence C-O-C, noting that on the acid-alkali TAF with and without pressure a lower signal was present in regards to the untreated fibers. The acid-alkali TAF without pressure and the acid-alkali TAF with pressure had 0.06% and 0.4% less than the UAF. The 3 460-3 412 cm-1 band, which is attributed to the elongation vibration of the hydrogen link of the functional O-H group, decreased in intensity in acid-alkali TAF with and without pressure in regards to the A. salmiana UAF. The 1 640 cm-1 signal is related to the absorption of water, increasing its intensity slightly in the acid-alkali TAF without pressure, while this intensity decreased significantly in acid-alkali TAF with pressure. This is consistent with research by Johar et al. (2012). This author reports that the intensity increase is based on the lengthening of the hydrogen links and the bending of the OH that are joined to the structure of the cellulose, thus increasing the water absorption. In a similar manner, Lojewska et al. (2005) noted the lengthening of the water’s OH to 1 640 cm-1, that even when dry, the absorbed water in the cellulose molecules is very difficult to extract due to the cellulose-water interaction.

Figure 1. IR-FT specters of A. salmiana fibers with treatments: (1) UAF; (2) acid-alkali TAF without pressure; and, (3) acid-alkali TAF with pressure.
The decrease of intensity indicates that there is a lower proportion of cellulose which agrees with the results in Table 1. At 2 900 cm-1, the TAF decreased the lengthening vibration in comparison to the UAF, due to the presence of the -CH2 in the samples. On the other hand, the intensities of the vibration bands -H and the vibration of C-O (1 060-1 050 and 890 cm-1) decreased mainly in the acid-alkali TAF with pressure and to a lesser extent in the acid-alkali TAF without pressure, which could be due to the hydrolysis of the cellulose (Johar et al., 2012). These results are consistent with the ones presented in Table 1 where the treatment with a more significant effect on the quantity of cellulose obtained was the acid-alkali TAF treatment with pressure. The 3 420 cm-1 signal is within the interval of 3 440-3 400 cm-1 corresponding to the C-H and O-H groups described as the lengthening of the hydrogen links and the bending of the hydroxyl groups (OH) linked to the structure of the cellulose. Johar et al. (2012) indicate that in this band the cellulose is not removed during the chemical treatment.
The 1 735 cm-1 band corresponds to the lengthening vibration of the C-O groups of the residue of the acetyl groups and the uronic esters of pectin, hemicellulose or of the ester links of the carboxyl group in the ferulic and p-coumaric acids of lignin and hemicellulose (Sain and Panthapulakkal, 2006). In the acid-alkali TAF with and without pressure, intensity was reduced, being greater in the acid-alkali treatment with pressure. This is consistent with the results obtained in Table 1, where the content of the “other” components (which are residues of hemicellulose and/or pectins) decreases more with the effect of pressure. Johar et al. (2012) also noted this band, finding a decrease in this functional group due to the rupture of the acetyl link between the lignin and the hemicellulose during the pulping with NaOH.
Among the bands within 1 200-900 cm-1, a significant decrease is noted in the specter corresponding to the C-OH and the C-O of the cellulose in the acid-alkali TAF with pressure of A. salmiana, which indicates a mercerization of the cellulose due to the abrupt fall of transmittance. Due to their composition, the acid-alkali action and the temperature-pressure allow the division of the cellulose chains. This is consistent with the statements of Gassan and Bledzki (2001), who report that there is thermal degradation on the flax cellulose at temperatures of 170 and 210 °C for 120 min in convection ovens.
Thermogravimetric analysis
The thermogravimetric analysis was done in order to characterize the fibers obtained according to the temperature, as well as to evaluate the treatments applied. Figure 2 shows the thermograms concerning the acid-alkali TAF with and without pressure, comparing them with the UAF. The loss curve of the UAF and TAF with and without pressure showed three stages of loss related to: (i) the evaporation of humidity; ii) reducing sugars; and, (iii) the degradation of hemicellulose.
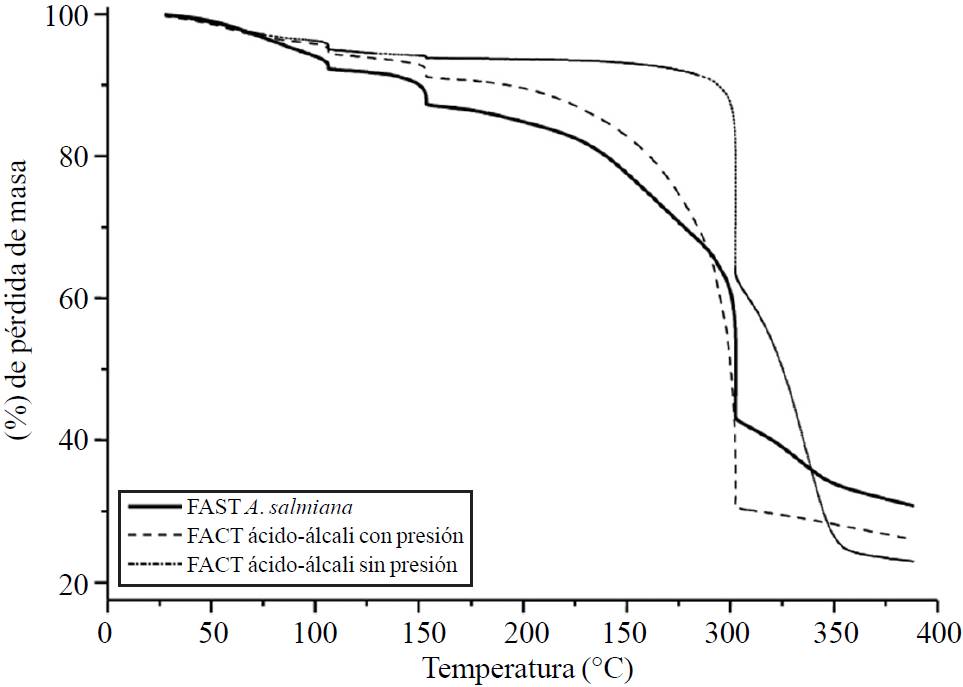
Figure 2. A. salmiana fiber thermograms with treatments UAF, acid-alkali TAF with pressure, acid-alkali TAF without pressure.
The UAF showed to be in the aforementioned stages, remaining at 104.41, 152.22 °C, 302.09 °C. The stabilization temperature of the A. salmiana UAF was 152.22°C with a weight loss of 11.6%. This is consistent with what was stated by Espinosa-Andrews and Urias-Silvas (2012), who indicate that the fructans have a decomposition temperature under 200 °C and up to 230 °C depending on the branched chains of agave fructans. However, these three stages of mass loss are different to what was reported by Kestur (2013), as it mentions that the A. tequilana bagasse has mass loss percentages of 10.8%, 63.8% at temperatures of 80 °C and 360 °C.
In regards to the A. salmiana acid-alkali TAF without pressure, a thermal stability of 152.27 °C with a mass loss of 6% was shown. After this temperature, a decrease can be observed probably due to the degradation of hemicellulose. After 350 °C, the degradation of cellulose begins. The A. salmiana acid-alkali TAF show a decrease of up to 104.32 °C, probably due to the existing humidity in the fiber and a thermal stability of up to 301.94 °C with a mass loss of 25.99%.
Above this temperature, a decrease in the mass loss can also be observed, due to the degradation of the hemicellulose (350 °C). The behavior observed in the acid-alkali TAF with pressure helped to reduce losses due to its high lignin content and low cellulose content. Conversely, regarding the acid-alkali TAF without pressure, it was observed that due to the lower lignin content but higher cellulose content, the cellulose was thermally degraded first, thus obtaining a greater weight loss.
Differential scanning calorimetry (DSC)
As for the DSC results, both treatments showed to be consistent with the thermogravimetric results. The results of the DSC curves are shown in Figure 3. The A. salmiana UAF show an endotherm at 110.73 °C and a plateau at 139.32 °C, in addition to a small endotherm at 213.82 °C corresponding to derived reactions of thermal degradation. These endotherms are due both to the reducing sugars as well as to those hemicelluloses that are still joined to the cellulose-lignin complex. The main difference is that in the endotherms of the treated fibers, the enthalpy is lower when compared to that of the native fiber, probably due to the elimination of larger sugar chains through acid-alkali hydrolysis.
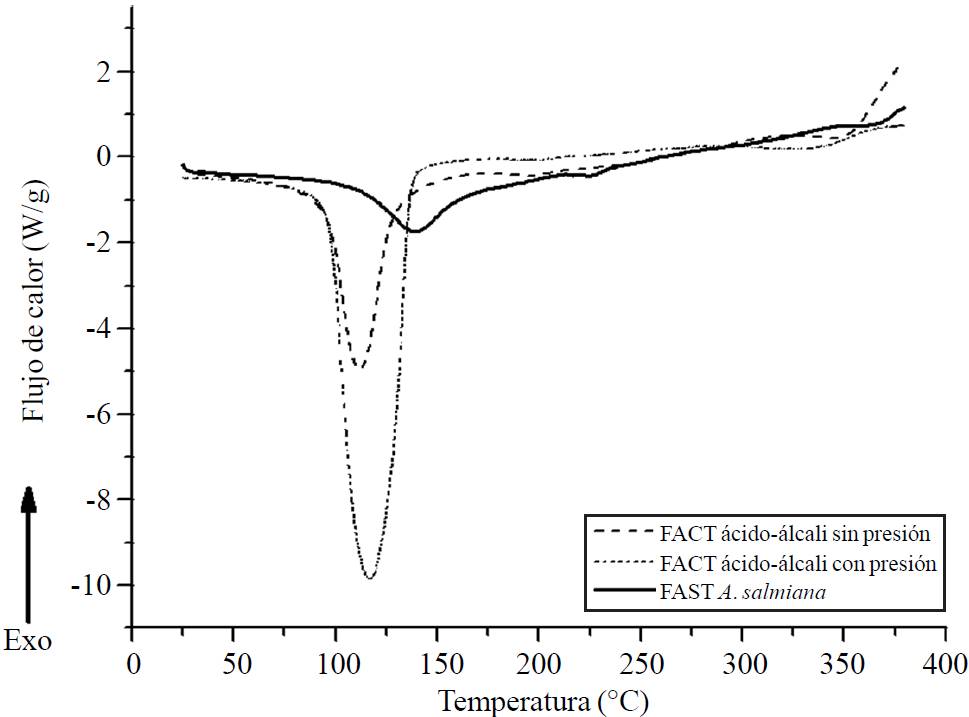
Figure 3. DSC curves of A. salmiana fibers with UAF, acidalkali TAF treatments with pressure, acid-alkali TAF without pressure.
The acid-alkali TAF with pressure show an endotherm at 96.93 °C with a maximum plateau of 116.99 °C and a slight increase in the degradation of the other components. This is due to reactions from substances derived from the degradation of extractable components. Mana et al. (2010) mention that under temperatures of 200 °C, the sugars, along with other volatile components joined to the fibers, are thermally decomposed. Kestur et al. (2013) report that the sugars linked to lignin can be very volatile. Balam et al. (2006) mention that the thermal degradation of the cellulose happens in two stages: in the first a reduction in the size of the chain is observed due to the rupture of links to the generation of free radicals, carboxyl groups and carbonyls as well as the formation of carbon, while the second includes the depolymerization of the cellulose due to the rupture of the glycosidic units and the formation of levoglucosan. The second degradation stage of the cellulose and lignin is attributed to temperatures above 410 °C.
Two endotherms can be seen in the acid base TAF without pressure, one at 120.71 °C and the other at 207 °C with a ΔH= 187.0 J/g and 19.63 J/g. These endotherms are caused both by humidity and by reducing sugars, as well as by hemicelluloses that are still joined to the cellulose-lignin complex. The main difference is that the endotherms of the treated fibers showed a lower enthalpy than the native fiber, probably due to the elimination of polysaccharide chains through acid-alkali hydrolysis. In regards to the hemicellulose, cellulose and lignin components, Espinosa and Urias (2012) mention that there is a humidity loss, specifically in fructans, in temperatures under 130 °C.
Microstructural changes of A. salmiana fibers determined through environmental scanning electron microscopy (ESEM)
Figure 4 shows the ESEM images of the acid-alkali UAF and TAF agave fibers with and without pressure. Figure 4(1) shows the arrangement of a large number of microfibril joined with amorphous material and layers of wax characteristic of the untreated agaves. Bessadok et al. (2008) reported that in the A. salmiana fibers, microfibril are grouped in the form of a bouquet and constitute spiral tracheids, which act as sap conductors. After the chemical treatment, the tracheids are partially freed from the group [Figure 4(2) and 4(3)]. In the acid-alkali TAF treatment without pressure, a higher proportion of cementing materials (pectin substances) can be observed in comparison to the treatment with pressure. Bessadok et al. (2008) mention that the tracheids are comprised of lignin components and hydrophobic materials, as they transport water in the plant. The microfibril size in the case of the A. salmiana UAF was 20.4 μm in a helical structure, while in the TAF with the acid-alkali treatment without pressure the fiber size was 2.84 μm, with a helical structure as well, and in the treatment with pressure it was 7.14μm.

Figure 4. ESEM images of A. salmiana fibers with treatments: (1) UAF; (2) acid-alkali TAF without pressure; and, (3) acid-alkali TAF with pressure. UAF= untreated agave fibers. TAF= treated agave fibers.
When applying the acid-alkali treatment with and without pressure, the products of degradation become more pronounced with bigger spaces between them [Figure 4(2) and 4(3)], which confirms the level of polymerization and crystallinity of the untreated agave when compared to the one treated with acid-alkali.
Direct emission spectroscopy (DES) and X-ray
The concentration of elements in the acid-alkali untreated and treated TAF was determined using direct emission spectroscopy (DES). Figures 5(a), 5(b) and 5(c) show the results of the samples mentioned. The presence of C and O can be seen; these are present in all organic materials and in this case comprising a portion of cellulose, waxes and pectins. The A. salmiana TAF with acid-alkali without pressure [Figure (1b)] show a lower proportion of calcium which is present as calcium oxalate. A considerable decrease of this element can be observed in the A. salmiana TAF with acid-alkali pressure treatments. This decrease in the calcium content is relevant because the presence of calcium salts prevents the association of the cellulose fibers with other substances, providing an adequate raw material that will react to other materials or components and thus help obtain biodegradable packaging.
Crystallinity studies
Diffraction patterns were obtained from the agave fibers and from those chemically treated with and without pressure. All diffraction patterns showed peaks around 2ϴ= 15, 22, 24 and 30°, indicating the structure of cellulose type I (Oudiani et al., 2011). There was a difference between the peaks and this was due to the changes in intensities which represent the crystallinity differences of the fibers. These indexes can be observed in Table 2. The differences observed in these indexes are related to the ratio of cellulose in the fiber shown in Table 1. Oudiani et al. (2011) report that those diffractograms with 2ϴ = 14° and 2ϴ = 16° peaks correspond to amorphous material such as lignin, hemicellulose, pectin, and amorphous cellulose and in percentages lower than 20% of NaOH. The peaks that were not marked were considered to be of low crystallinity cellulose, containing a lower ratio of amorphous cellulose. Taking these results into consideration, the acid-alkali TAF present a higher ratio of amorphous cellulose. On the other hand, the acid-alkali TAF without pressure present a bigger peak range, which indicates a higher crystallinity (Table 2).
Table 2. Index of crystallinity of the A. salmiana fibers with and without acid-alkali with pressure and acid-alkali without pressure treatments.
Pico 1 | 2 θ | Pico 2 | 2 θ | Pico 3 | 2 θ | Índice de cristalinidad | |
---|---|---|---|---|---|---|---|
FAST | 1860 | 15 | 3103 | 22.08 | 2795 | 24.48 | 40.06 |
FACT ácido-álcali con presión | 1349 | 14.96 | 2656 | 22.36 | --- | --- | 49.21 |
FACT ácido-álcali sin presión | 1388 | 14.84 | 2780 | 22.6 | ---- | --- | 50.07 |
Conclusions
It was observed that there is hydrolysis in the cellulose, due to the pressure and temperature effect on both treatments, being even more notorious in the acid-alkali TAF with pressure. The content of cellulose and lignin was greater in the acid-alkali TAF without pressure with a higher crystallinity, which fluences the level of fiber purities, resulting in differences in the content of cellulose and lignin. This is important because depending on the composition of these materials, the possible use of the fibers will be determined. The results of the thermogravimetric analysis showed the elimination of chains of polysaccharides by acid-alkali hydrolysis. The acid-alkali treatments with and without pressure showed through ESEM the opening of the helical structures which allowed to be hydrolyzed in different manners.
Literatura citada
AOAC international. Official Methods of Analysis of A. O. A. C. international. 1995. 16 edición. Arlintong, Virginia, E. U. A. A. O. A. C. [ Links ]
Balam, C. R. J.; Duarte, A. S. adn Canché, E. G. 2006. Obtención y caracterización de materiales compuestos de las fibras de henequén y polipropileno. Rev. Mex. Ing. Quím. 5(1):39-44. [ Links ]
Ben Sghaier, A. E. O.; Chaabouni, Y.; Msahli, S.; Sakli, F. 2012. Morphological and crystalline characterization of NaOH and NaOCl treated Agave Americana L. fiber. Industrial Crops and Products. 36:257-266. [ Links ]
Bessadok, A.; Marais, S.; Roudesli, S.; Lixon, C. and Métayer, M. 2008. Influence of chemical modifications on water-sorption and mechanical properties of Agave fibres. Composites: Part A. 39:29-45. [ Links ]
CEN/TC 327 2009. Animal feeding stuffs- determination of acid detergent fiber (ADF) and acid detergent lignin (ADL) contents. European Committee for Standardization (CEN). http://standards.cen.eu/dyn/www/f?p=204:32:0::::FSP_ORG_ID:6308&cs=151B54DCC1DA2676999693FCE3A6F61BC#top. [ Links ]
El Oudiani, A.; Chaabouni, Y.; Msahli, S. and Sakli, F. 2011. Crystal transition from cellulose I to cellulose II in NaOH treated Agave americana L. fibre. Carbohydrate Polymers. 86:1221-1229. [ Links ]
Espinosa-Andrews, H. y Urias-Silvas, J. E. 2012. Thermal properties of agave fructans (Agave tequilana Weber var. Azul). Carbohydrate Polymers. 87:2671-2676. [ Links ]
Gassan, J. and Bledzki, A. 2001. Thermal degradation of flax and jute fibers. Applied. Polymer Science. Journal. 82(6):1417-1422. [ Links ]
Johar N.; Ahmada I. and Dufresnec A. 2012. Extraction, preparation and characterization of cellulose fibres and nanocrystals from rice husk. Industrial Crops and Products. 37:93- 99. [ Links ]
Kestur, G. S.; Flores-Sahagún, T. H. S.; Pereira Dos Santos, L.; Dos Santos, J.; Mazzaroc, I. and Mikowski A. 2013. Characterization of blue agave bagasse fibers of Mexico. Composites: Part A. 45:153-161. [ Links ]
Lojewska, J.; Miskowiec, P.; Lojewski, T. and Pronewicz, L. M. 2005. Cellulose oxidative and hydrolysis degradation In: situ FTIR approach. Polymer Degradation and Stability. 88(3):512-520. [ Links ]
López-Álvarez, A.; Díaz-Pérez, A. L.; Sosa-Aguirre, C.; Macías- Rodríguez, L. and Campos-García, J. 2012. Ethanol yield and volatile compound content in fermentation of agave must by Kluyveromyces marxianus UMPe-1 comparing with Saccharomyces cerevisiae baker's yeast used in tequila production. J. Bios. Bioeng. 113:614-618. [ Links ]
Rosli, N. A.; Ahmad, I. and Abdullah, I. 2013. Isolation and characterization of Cellulose nanocrystals from A. angustifolia Fibre. Carbohydrate Polymers. 86:1221-1229. [ Links ]
Sain, M. and Panthapulakkal, S. 2006. Bioprocess preparation of wheat straw fibres and their characterization. Industrial Crops and Products. 23(1):1-8. [ Links ]
Saucedo, L. J.; Castro, M. A. J. and Rico, J. L. 2010. Optimization of acid hydrolysis of bagasse from Agave tequilana Weber. Rev. Mex. Ing. Quím. 9(1):91-97. [ Links ]
Singha, A. S. and Rana, R. K. 2010. Graft copolimerization of methyl methacrylate (MMA) onto Agave Americana fibers and evaluation of their physicochemical properties International J. f Pol. Analyt. Charact. 15:27-42. [ Links ]
Summerscales, J.; Nayake, N. P. J.; Virk, A. S. and Hall, W. 2010. A review of bast fibres and their composition. Part 1. - Fibres as reinforcements. Composites. Part A. 41:1329-1335. [ Links ]
Tamahe, T. and Baillie, C. 2007. Influence of fibre extraction method, alkali and silane treatment on the interface of Agave americana waste HDPE composites as possible roof ceilings in Lesotho. Composite Interfaces. 14(7-9):821-836. [ Links ]
Ting, S. V. 1956. Fruit juice assay, rapid colorimetric methods for simultaneous determination of total reducing sugars and fructose in citrus juices. J. Agric. Food Chem. 4(3):263-266. [ Links ]
Revised: August 2015; Accepted: January 2016