Introducción
En la perspectiva de la industria automotriz, el Tratado de Libre Comercio de América del Norte (TLCAN) fue el resultado de las estrategias que siguieron las ensambladoras de autos: General Motor, Ford y Chrysler. Las “Big Three” para tener acceso al mercado mexicano, tanto como proveedor de mano de obra barata, abundante y calificada, como de un mercado para sus productos. Desde sus inicios, la estrategia de estas empresas también perseguía la implantación de fábricas de vehículos y autopartes sin regulaciones que pudieran entorpecer sus proyectos expansivos y, al mismo tiempo, que dichas nuevas plantas estuvieran cerca de su mercado de consumo principal, es decir, Estados Unidos de Norteamérica (US). También se conseguía el acceso a un país que les facilitó enormes ventajas fiscales (exenciones de diversos gravámenes, como el Impuesto al Valor Agregado (IVA) y el Impuesto Sobre la Renta (ISR) a importaciones temporales, entre otras) y laborales (como sindicatos dóciles y sometidos a los intereses empresariales y obreros hábiles y responsables).
Cuando se firma el TLCAN en diciembre de 1992 para su entrada en vigor el 1 de enero de 1994, las Big Three (BT) ya tenían un amplio historial en México que data de la instalación de la primera fábrica de Ford en 1925, de General Motors (GM) en 1935 y de Chrysler en 1938; paralelamente se instalaron plantas de fabricación de autopartes propiedad de estas mismas empresas: Visteon, Delphi y Mopar respectivamente.
Las BT estuvieron lidiando con las regulaciones mexicanas por muchos años, especialmente con aquellas que estaban encaminadas a lo que se llamó la mexicanización de la industria (decretos automotrices de 1962, 1972, 1977, 1983 y 1989). Sin embargo, todas ellas habían sido bien sorteadas por las empresas armadoras en México, de manera que, apenas antes de la entrada en vigor del TLCAN, se produjeron en México 1.1 millones de automotores en 1993 de los que 635 mil (56%) correspondían a las armadoras norteamericanas, y se empleaban 386 mil personas directas en el sector. De estos, 51 mil empleos correspondían a las BT y 256 mil empleos a las fábricas de autopartes, entre las que ya figuraban empresas japonesas y alemanas. Veinte años después de la entrada en vigor del TLCAN, se produjeron en México un poco más de tres millones de automotores; los empleos ascienden a más de 65 mil en armadoras y 530 mil en fábricas de autopartes, es decir, casi 600 mil empleos directos.
Con tan sólo esos datos se puede sugerir que el TLCAN fue la culminación de las necesidades de expansión de la industria automotriz extranjera, primordialmente la norteamericana. La parafernalia de los sectores privados nacionales y extranjeros y del gobierno mexicano exaltando que el TLCAN traería mayor inversión y por tanto mayores y mejores salarios, crecimiento y mejoras para la sociedad, fue la manera de justificar y ocultar la rendición a los intereses de las grandes corporaciones. La propaganda justificadora fue dictada por las ‘sugerencias’ macroeconómicas del Fondo Monetario Internacional (FMI), del Banco Mundial (BM) y de la Organización para la Cooperación y el Desarrollo Económico (OCDE) que, como es sabido, estas entidades obedecen a los intereses de las grandes transnacionales de los países industrializados. Asimismo, debe reconocerse que los vaivenes de la industria en el nivel mundial se han visto reflejados en México y sujetos a las políticas que establecen las corporaciones con un papel marginal de las necesidades de crecimiento e industrialización del país.
Finalmente, no puede pasarse por alto que debido a que el salario en México es diez veces menor que en US, la estrategia de transferir producción a nuestro país ha sido utilizada para abatir los salarios y prestaciones en US. Por ejemplo, las contrataciones de nuevos empleados en las empresas automotrices de ese país, ya se hacen en la mitad del salario que ganaban los empleados anteriores, así como que los 500 mil empleos perdidos en Detroit, Michigan desde la década de 1980, tienen su contraparte en las contrataciones en México.
1. Una firma, dos países. Ford: ejemplo de gestión laboral y salarial
Desde la instalación de Ford Motor Company (Ford) en México en 1925, seguida por la de General Motors Corporation (GM) en 1928 y finalmente Chrysler en 1938, las armadoras de US iniciaron la venta de sus vehículos, para posteriormente instalar plantas ensambladoras, con subensambles fabricados en su país. Ford inició la construcción de su primera planta en 1930 en un local rentado en las proximidades de San Lázaro en la Ciudad de México, siendo su Vicepresidente Adrián René Lajous, que había estudiado en la Cornell University de New York, quien negoció personalmente con el Presidente mexicano Plutarco Elías Calles ventajas para Ford en México, tales como 50% de descuento en los derechos de importación de materiales y concesiones de tarifas de carga en ferrocarriles. Asimismo, el gobierno le ofreció que no habría ningún problema sindical; a pesar de esto, en Ford México se formó un sindicato en los inicios de 1932 (habrá que considerar que por ley es necesario que los obreros estén agrupados en un sindicato y que es a través de éstos que se les controla, así que, realmente no puede considerarse que fue una desventaja para Ford). Con respecto a los salarios, Lajous estableció no pagar más de tres pesos al día, lo que significaba un salario alto, pues el promedio en esa fecha era de 1.25 pesos diarios.
En 1932 Ford establece una nueva planta en los alrededores de la Villa que tenía 250 empleados y una capacidad de ensamblaje de cien autos diarios, pero solamente armaban 50 vehículos modelo A, que fue el que reemplazó al famoso modelo T que dejó de fabricarse en 1927 después de haber establecido el récord de quince millones en sus 20 años de fabricación -1908 a 1927- en todo el mundo (lo que implica que se fabricaron y vendieron 750 mil Ford T anuales en promedio. Cifra difícil de concebir, aun ahora. Hasta la fecha, no ha pasado nada que se le aproxime) que sería roto por el Beetle de Volkswagen en 1972, es decir, 45 años después (Volkswagen los fabricó de 1945 a 1972, es decir, en 27 años, pero de 1945 a 1950, se hicieron solamente 86 mil beetles por estar reacondicionando las fábricas de Wolfsburg bombar-deadas durante la guerra).
Vale la pena referir, con la intención de tener en perspectiva las proporciones de las operaciones mundiales de esta empresa, que en 1932 Ford fabricaba más del 33% de la producción mundial, la cual ascendía a cerca de cuatro millones de vehículos. La planta de Dearborn, Michigan inició su construcción en 1917, finalizándola en 1928, en la que trabajan cien mil empleados; mide 2.4 kilómetros de largo y 1.6 de ancho; tiene 96 edificios con 1.5 km2 de superficie construida; un puerto dragado para barcos grandes; 160 kms. de pista para el tren que está dentro de los terrenos de la fábrica; cuenta con planta de energía eléctrica propia; tenía fábrica de vidrio y de estampado, entre muchas otras características. Está documentado en los anales de la United Auto Workers (UAW) que la policía de Ford dentro de la fábrica era más numerosa y más sanguinaria que la de la ciudad de Detroit. Los trabajadores tenían prohibido hablar dentro de las plantas, ya fuera en horas de trabajo o en la hora de comida.
La Segunda Guerra Mundial resultó conveniente para Ford México ya que tuvieron utilidades que fueron desde 112,000 dólares en 1939 a 851,000 en 1945; como consecuencia de ello, los directivos decidieron expandir la planta de la Villa en 1949. Con el periodo de la posguerra, en México se inició un sentimiento de nacionalismo económico. A pesar de que se redujeron los derechos de importación de autopartes y componentes, se impusieron cuotas sobre los materiales para ensamble importados, con la intención de evitar importar subensambles. A partir de 1951 se implantaron sistemas de precios para autos y camiones, situación que se postergó hasta 1977, lo que provocó que los precios de los autos fueran entre 50 y 100% más altos en México que en los EUA, pues el gobierno consideraba que la importación de autos afectaba la balanza comercial al destinar dólares de la reserva a ese fin. Para mediados de la década de 1950 Ford tenía el 28% del mercado nacional, GM el 33% y Chrysler el 20% (History of Ford Motor Compamy).
En 1962 Ford compró la planta Studebaker Packard que estaba en Tlalnepantla, Estado de México en donde se empezó a fabricar el chasis y herramental para troquelado de partes. Los ingenieros de Ford México desarrollaron matrices que se podían utilizar en varios modelos de autos, hecho que fue implantado en las fábricas de Ford de todo el mundo, mientras en Detroit siempre se fabricó un herramental para cada modelo. En este año se emite el decreto automotriz que establecía que a partir de septiembre de 1964, 60% del costo de producción de los autos fabricados en el país debía ser de partes fabricadas en México, así como el tren motriz, componentes del motor, de la transmisión y los ejes traseros. La respuesta de Ford al llamado gubernamental consistió en adquirir 1200 partes nuevas locales de un total de 1800.
En 1964 Ford establece una planta en Cuautitlán, Estado de Méxi-co para ensamblar autos y fabricación de motores V8. Los empleados pasaron de 1,209 en 1960 a 3,291 en 1965. Las ventas totales de automóviles producidos en México apenas superaban las cien mil unidades anuales (1970), principalmente porque todavía se vendían al doble del precio que en EUA. El gobierno mexicano alegaba que el único camino para romper la inercia de altos costos por el bajo volumen era producir para exportación y a eso respondía el decreto para que las armadoras incrementaran su cuota de producción. A pesar de que ya se exportaba a 23 países, incluyendo EUA, Ford México no estaba dispuesta a competir con Detroit en la exportación de vehículos ensamblados. El argumento de los altos costos por el bajo volumen resulta poco verosímil porque casi la totalidad de las partes eran importadas de la misma Ford o de su filial Visteon y la única diferencia consistía en el costo de la mano de obra que, además de representar un bajo porcentaje del costo total (cerca del 30%), el salario pagado en México era más bajo que en EUA (menos de una quinta parte).
La devaluación del peso en 1976 incrementó bruscamente el precio de las autopartes importadas, elevando los costos de Ford. Las medidas antinflacionarias, redujeron la posibilidad de contratar préstamos para la adquisición de autos, lo que provocó la caída en las ventas y márgenes de utilidad, aunque las ventas siguieron creciendo porque los mexicanos cambiaron a adquirir autos compactos. En estos años Ford realizó una coinversión con el Grupo Alfa para fabricar las cabezas de aluminio de los motores; con Vitro para fabricar los vidrios y con el Grupo Visa para los componentes de plástico. En 1980 Ford México produjo el auto un millón en la planta de la Villa, que cesó el ensamble de vehículos en 1984 trasladando la producción a la planta de Cuautitlán. La fábrica de motores se abrió en 1983 en Chihuahua.
La crisis económica de México de 1982 fue mucho más severa que la de 1976 y el peso se devaluó mucho más: de 26 a 149 pesos por dólar (470% de devaluación contra 60% en 1976: de 12.50 a 20.00 pesos). Debido a ello, las ventas de Ford México cayeron de 78,947 a 62,821 unidades y el presidente de la compañía dijo que el margen de utilidad bruta había bajado entre 50 y 75%, por lo que Ford enfocó su atención en producir autos para exportarlos a EUA. El efecto más importante de la devaluación es que los trabajadores mexicanos, a partir de ésta, reciben un salario aún menor que los trabajadores de EUA (disminuye en la misma proporción que la devaluación) y por tanto, lo más conveniente es exportar autos por la disminución del costo. Por eso se entiende que en 1984, Ford anuncia la inversión de 500 millones de dólares para fabricar vehículos en una nueva planta en Hermosillo, Sonora, a 240 kilómetros al Sur de la frontera con Texas.
Cuando se inauguró la planta en noviembre de 1986 tenía una capacidad para producir 130 mil autos anuales y empezó la fabricación del Mercury Tracer de diseño japonés para los mercados de EUA y Canadá. La planta implantó el sistema “Just in Time” para 2400 componentes e instaló 96 robots Kawasaki que realizaban el 95% de la soldadura de partes; se invirtieron otros 300 millones de dólares para incrementar el número de robots a 128, adquisición de computadoras personales, y con otras medidas, lograr incrementar la capacidad de la planta a 170 mil unidades anuales y elaboración de nuevas matrices para fabricar el Ford Escort. En 1990 la planta produjo 48 mil Tracer y 41 mil Escort. En 1990 y 1991 hubo una caída mundial de la demanda de autos, que puede ser la explicación de la baja utilización de la planta.
A mediados de marzo de 1987, 800 obreros estallaron una huelga que duró seis semanas, hasta que recibieron el 34.5% de incremen-to salarial más otro 20% por ajuste inflacionario; El costo de la hora de trabajo era de $1.09 pesos para 45 horas semanales. En septiembre de ese mismo año Ford despidió 3,200 obreros de la planta de Cuautitlán como respuesta a la huelga de nueve semanas en esa planta. Estas medidas, obviamente, respondían a la profunda caída de las ventas de autos en todo el país, mayor al 45%, sin descartar que las huelgas las provocó la misma empresa.
En 1990 hubo otro problema laboral en la planta de Cuautitlán, cuando trabajadores de la Confederación de Trabajadores de México (CTM) entraron en la planta con uniformes de obreros y provocaron violencia, llegando a matar a un trabajador disidente y herir a siete más. La planta paró por un mes y Ford despidió a 2,400. Contrató a 1,300, pidiendo nuevos reemplazos a la CTM. En 1991, Ford anunció la inversión de 700 millones de dólares para la planta de Chihuahua, para fabricar motores de cuatro cilindros. La producción empezó en 1993. Como se dijo anteriormente, la fuerte baja en la demanda mundial de autos, considerando además que los autos japoneses ya estaban siendo más solicitados por el mercado, fue aprovechada por Ford México para realizar los arreglos con los sindicatos incómodos, cosa que no podían en EUA por la fuerza de la United Automobile Workers (UAW).
Otras plantas que Ford México tiene y que son 100% subsidiarias de Ford Motor Co., son una fábrica de partes de plástico y cuatro plantas maquiladoras en Ciudad Juárez, justo en la frontera con Texas: Coclisa (radiadores, calentadores, y componentes para el aire acondicionado), Altec (radios y componentes electrónicos), Autovidrio (Vidrios) y Glamosa (convertidores catalíticos). También tiene participación en Nemak (caja de aluminio), Vitroflex (vidrio) y Climate Systems Mexicana (aire acondicionado, líneas de refrigeración y acoplamientos). Asimismo, para el periodo 1995-1996 invirtió 250 mmd.
En 1993, es decir, un año antes de entrada en vigor del TLCAN, Ford produjo en México 209 mil vehículos, el 3.5% de su producción mundial que fue de 5,936 miles. En el año 2012 produjo en México 452 mil, el 8.1% de su producción total de 5,595 miles, más que duplicando en el periodo de 20 años su producción en México. En EUA en 2012 produjo 2,152 miles (38% de su producción total). El 96% de la fabricación de vehículos en México, o sea 435 mil, fueron para exportación y solamente el 4% para el mercado nacional.
Ford, al festejar sus 85 años de estancia en México el 23 de junio del 2010, manifestó tener 7,500 empleados, lo que le ha permitido tener utilidades por $ 2,700 millones de dólares (mdd) en 2009 y $ 2,100 mmd el primer cuatrimestre del 2010.
2. Una estrategia de expansión rentable y exitosa: General Motors en México
General Motors Corporation (GM) nació en 1908 en Detroit, Michigan, EUA, pero fue hasta 1935 que constituyó operaciones en México, sólo como oficinas de ventas. Al siguiente año organizó su primera exhibición en el Salón del Automóvil, cuya principal atracción fue un Chevrolet con carrocería totalmente de acero. De manera que fue hasta 1937 que la planta de GM en la Ciudad de México comienza sus operaciones fabricando camiones; contaba con sólo 222 trabajadores y se producían diez unidades diarias. Para el siguiente años empezó a ensamblar automóviles de la marca Chevrolet modelo Club Coupé Sedán. Casi 15 años después, hacia 1951, GM producía 12 mil unidades anuales con 1750 personas. Al finalizar los años setenta, llegó a producir por primera vez 50 mil unidades por año y en 1981 se inaugura la planta de ensamble de Ramos Arizpe, Coahuila.
De acuerdo con Quiroz (2009), la huelga de GM México del 7 febrero al 28 mayo 1980 en el Distrito Federal (DF) se convirtió en una caja de resonancia sobre los tintes políticos de la reubicación geográfica de las plantas automotrices, sus ventajas para las direcciones empresariales y los costos para un sector importante de sus trabajadores. En 1980, con un comité ejecutivo identificado con las banderas de la democracia sindical, se propuso recuperar la titularidad del sindicato de la nueva planta de Ramos Arizpe. El sindicato, en el mes de julio, se lanzó a la huelga por aumento salarial y violaciones al contrato colectivo de trabajo. En este último rubro se incorporaba la demanda de obtener la titularidad del contrato de la nueva planta. Después de 106 días de huelga, los obreros tuvieron que levantarla sin que fuera satisfecha su demanda principal. Negociaron el aumento salarial y volvieron al trabajo sin avanzar nada con relación al contrato de la multicitada planta. Detrás de esa acción técnico-económica estaba el objetivo político empresarial de que las nuevas plantas no pertenecieran a un sindicato combativo como el de GM del DF. En lo económico, además de las ventajas geográficas de las nuevas plantas, estaban las diferencias salariales entre el norte y el sur y las características de los obreros de Ramos Arizpe que serían más jóvenes, con menor experiencia sindical y que, de entrada, estarían controlados por una central corporativa tradicional como la CTM. En la planta de Ramos Arizpe se ofrecían salarios diarios promedio de $90.00 y $98.00, que contrastaban con los $450.00 que se pagaban en la planta del DF. Estas diferencias, elocuentes antes de la inaugura-ción de la planta, se quedarían cortas al momento de que iniciara operaciones. En 1982, los días de descanso obligatorio en la planta GM del DF (GMDF) eran 17, en la de Ramos Arizpe (GMRA) eran 10 días; el seguro de vida era de $ 90 000.00 para la GMDF, y de $ 75 000.00 para GMRA; el aguinaldo era de 23 días para la GMDF y de 18 para la GMRA. En cuanto a la duración de la jornada de trabajo semanal, la diurna era de 48 horas en GMRA y de 40 horas en la del DF; la mixta era de 45 horas en RA y de 37.5 horas en el DF; la nocturna era de 42 horas en RA y de 35 en el DF. En lo que se refiere a las vacaciones para el nivel más alto -con 10 años o más de antigüedad- en RA se darían 16 días, mientras que en el DF se daban 19. Finalmente, en el renglón de los salarios, el más alto salario diario pagado en el DF era de $ 1 307.00, y en RA era de $ 808.50; el más bajo semanal en el DF era de $ 684.00, mientras que en RA era de $ 347.00.
Entre 1980 y 1981, el proceso de reestructuración de la industria basada en la exportación hacia el mercado estadounidense se intensificó. Además de la planta de GM de Ramos Arizpe, con capacidad para producir 500 mil motores de seis cilindros por año, Chrysler anunció la construcción de otra planta similar en el mismo lugar para producir 270 mil motores en la primera fase, de los cuales 220 mil estaban destinados a EUA. La Ford Motor Company de México construiría una planta para producir motores en Chihuahua, y su meta productiva sería de 500 mil. Nissan mexicana ya estaba exportando 70 mil motores de su planta en Lerma, Estado de México, y planeaba construir una nueva planta en el bajío -finalmente escogería a la ciudad de Aguascalientes- para fabricar motores para la exportación.
Cuando se inaugura la planta en Silao, Guanajuato, en 1995, se le asegura a la empresa el abastecimiento de agua y se le obsequia el terreno de 230 hectáreas, además de las ventajas de vías férreas y carreteras hacia el norte y la cercanía al aeropuerto internacional del Bajío.
Además de esta referencia de las que abundan en la literatura de la industria automotriz de todo el mundo, muestra la fase represiva y pichicata de las empresas norteamericanas (sabemos que no es exclusividad de ellas, sino que es la postura general de la clase patronal), cuando platicamos con ingenieros de la planta de General Electric en Querétaro que fabrica turbinas para aviones, comentaban que venían ingenieros de GE Norteamérica a aprender sobre lo que se hacía en la planta mexicana y que se sorprendían porque los mexicanos capacitaban a los norteamericanos que ganaban ocho veces más, además de los viáticos por estar en México.
GM México produjo en 1993 192,000 vehículos, el 2.5% de su fabricación mundial que ascendió a 7,783,000; en el 2013 en México se produjo 578,000, 6.2% de un total mundial de 9,285,000, su crecimiento en los 20 años del TLC fue de casi 200%. En EUA se fabricó únicamente 1,985,000 de unidades, el 21.3% de su producción total. Del total de producción mexicana, 467 mil fueron para exportación (81%) y el 19% para el mercado nacional.
3. Las sucesivas crisis de Chrysler y su producción en México
Chrysler es la hermana chica de las “Tres Grandes”, nunca tuvo el tamaño de GM o de Ford, sin embargo, hubo épocas en que destacó por sus diseños e ingeniería. Historiadores de la industria automotriz explican los problemas de Chrysler señalando que esta empresa apostó siempre, hasta la década de 1980, por los autos grandes, de manera que debido al embargo petrolero y el alza de la gasolina de principios de la década de 1970, se vio seriamente afectada su estabilidad financiera por la fuerte caída en ventas. A principio de 1980 inició su gestión al frente de la empresa el controversial Lee Iacocca, quien solicitó al gobierno de EUA un préstamo por cinco mil millones de dólares para sortear la quiebra, mientras que el sindicato, la UAW, también contribuyó con 475 millones de dólares de sus pensiones. Con este dinero y una estrategias de ventas y fabricación de autos medianos y nuevos diseños, se logró pagar al gobierno anticipadamente, en 1983, el crédito obtenido. Nuevamente, la crisis de 1990 la afectó de manera severa, y fue disminuyendo producción y ventas en magnitud mucho mayor que las otras empresas norteamericanas y japo-nesas que despuntaban en el mundo y territorio norteamericano.
La prolongada crisis de la empresa culmina en 1998 con la fusión con Daimler-Benz, a través del intercambio de acciones, creando la Daimler Chrysler. Sin embargo, los problemas de la empresa se mantienen hasta que finalmente Daimler-Benz decide en 2007 vender su participación a Cerberus Capital Management, el fondo inversiones que ya manejaba parte de sus acciones y que también compró, en el mismo año, GMAC, la financiera de GM.
La firma Chrysler inicia sus operaciones en México en 1938 cuando instala su primera planta armadora de vehículos (compra Automex). Desde aquellos años la empresa fue expandiendo sus actividades de manera que en nuestros días operan: el Complejo Toluca dedicado al ensamble de autos, la planta de estampados y un centro de distribución de partes Mopar; el Complejo Saltillo donde existe una planta de ensamble para camiones y una de estampados, se producen las pick-ups y camiones Dodge Ram. Destaca la planta de motores Saltillo en Ramos Arizpe creada en 1981, actualmente la planta produce más de siete millones de motores, la gran mayoría para exportación. Además, la firma opera desde 2005 un Centro Avanzado de Ingeniería Automotriz con 8,800 m2 destinados a laboratorios de investigación y desarrollo tecnológico.
Similar a los casos de GM y Ford, los lugares en donde Chrysler ha instalado sus fábricas son los mejor comunicados hacia el Norte del país y hacia los puertos, con vías férreas y buenas carreteras y se les han dado los enormes terrenos, además de urbanizados, regalados (se dice en los informes que a precio simbólico).
Así como para 1993 las armadoras conjuntamente ensamblaron 1,055.000 vehículos, en el año 2000 llegaron a un máximo de 1,918,000, cifra que se vio bruscamente disminuida en los años siguientes hasta 1,507,000 en el año 2004 y volver a repuntar en el año 2008 a 2,168,000. Estas fluctuaciones han obedecido a las crisis generales o a las de la industria automotriz en particular. Salvo la última crisis del 2008, en que se ha disminuido la producción principalmente en EUA, en las crisis anteriores la producción se disminuía más en México. Este hecho parece apuntar a que las ensambladoras, principalmente Chrysler, ya no apuestan por la recuperación de la producción en su país, sino a competirle a las armadoras japonesas y coreanas en espacios geográficos donde el costo es sensiblemente más bajo (notoriamen-te México). Ha sido reiterado en publicaciones especializadas que Toyota en EUA tiene un costo de 1,500 dólares menor que el de las armadoras estadounidenses, y que Nissan EUA es todavía un 30% menor que Toyota. Las políticas de las Big Three han querido hacerse creer que es debido a que el costo de la mano de obra de sus plantas es mucho mayor que las de las japonesas, lo que no es necesariamente cierto, pero eso las ha impulsado a trasladar su producción a países con mano de obra barata.
Chrysler ha sido un caso diferente a GM y Ford, pues siempre ha exportado más del 90% de su producción y las ventas que realiza en el país, proviene de las importaciones de EUA.
En México en 1993 Chrysler fabricó 228 mil vehículos, el 10.4% de los 2,200,000 de fabricación total en el mundo. En el 2012 produjo en nuestro país 455,000, el 19.2% de los 2,371.000 de producción mundial. En los 19 años creció el 100%. Exportó 424 mil unidades, el 93% de su producción.
4. La política automotriz del gobierno mexicano
Ha habido un cambio importante en la política del gobierno mexicano respecto de la industria automotriz, especialmente después de la crisis de 1982 y a partir del TLCAN.
Con la finalidad de revisar los orígenes de la inversión extranjera directa (IED) en la que la industria automotriz ha jugado un papel relevante, ésta se inicia en la primera década de la Revolución (1910-1920) en que no hubo ninguna dificultad para las empresas extranjeras, las que incluso aumentaron su producción. Sin embargo, éstas mostraron hostilidad y oposición a las medidas de gobiernos revolucionarios para obtener recursos para hacer crecer al país, lo que provocó que el nacionalismo de los líderes revolucionarios entrara en conflicto con las empresas y los gobiernos de sus países.
Venustiano Carranza inicia la postura nacionalista al pedir la subordinación del capital extranjero a los intereses de los grupos mexicanos que encabezaba el mismo Presidente; así, la Constitución de 1917 fija las bases para reglamentar los intereses foráneos a las necesidades mexicanas. Esta postura fue brutalmente combatida por los extranjeros por lo que no se pudo aplicar lo que la Constitución mandaba ni con Carranza, ni con Obregón, ni con Calles. De hecho, ante las amenazas de intervención armada del embajador Morrow, Calles en 1927 tuvo que firmar los pactos extraoficiales de Bucareli para tener el reconocimiento de Washington (Cruz González, 1978: 449).
Los gobiernos de las décadas de 1920 y 1930 aprovecharon, hasta donde fue posible, los recursos económicos y la tecnología extranjeras en el desenvolvimiento de México. La regulación jurídica sobre la inversión extranjera se logró con la entrada de México a la Segunda Guerra Mundial, al establecer un decreto de emergencia en 1944 y que permitió hacer valer los intereses nacionales en algunos casos, esto hasta la década de 1960. Este decreto establecía un sistema de permisos previos de operación a empresas mexicanas que tuvieran participación extranjera y la imposición obligatoria a los extranjeros o mexicanos con socios extranjeros de solicitar permiso a la Secretaría de Relaciones Exteriores para constituir o modificar sociedades y adquirir empresas, inmuebles, concesiones y acciones; y también se creó una Comisión Mixta intersecretarial reguladora de la inversión extranjera. De esto, en la década de 1960, el gobierno de López Mateos (1958-1964) nacionalizó la electricidad y el de Díaz Ordaz (1964-1970) expidió la legislación minera cuyas normas estimulaban la mexicanización del sector. Es de destacarse que en 1970, durante el gobierno de Díaz Ordaz, se expide el Decreto en el que se limitaba al 49% la participación de capital extranjero en la industria siderúrgica, cemento, vidrio, fertilizantes, celulosa y aluminio, industrias ligadas principalmente a la automotriz (ibidem p.450). La ley de inversión extranjera de 1973 en su artículo 5 primera parte, restringe, entre otras actividades, la inversión de extranjeros hasta el 40% del capital en la fabricación de componentes de vehículos automotores.
Considerando que la Ley de Inversión Extranjera limitaba en alguna medida los intereses de las automotrices, el gobierno con el fin de regular este aspecto y ponerlo en consonancia con la política económica del momento, emitió los siguientes decretos automotrices:
Cuadro 1 Decretos automotrices
Decreto | Principales características |
1962 | Primer decreto automotriz. Se limitaron las importaciones de vehículos y también la importación de motores y transmisiones. Asimismo, se fijó que mínimo 60% de los vehículos fabricados en territorio nacional debían tener contenido nacional. |
1972 | Se redujo el porcentaje de contenido nacional mínimo para vehículos destinados al mercado de exportación. Se obligaba a los fabricantes de la industria terminal a exportar un equivalente de 30% del valor de sus importaciones |
1977 | El descubrimiento de yacimientos petroleros da pie a planes de transformar a México en un país exportador altamente competitivo; para tal propósito, se permitió la inversión extranjera en la industria automotriz. En este decreto se estableció un control estricto sobre la balanza comercial de las armadoras; asimismo, se instituía que al menos 50% del intercambio comercial de las armadoras debía provenir de las exportaciones de autopartes producidas localmente. Como medida de protección al sector autopartista, no se permitía que el capital extranjero tuviera la mayor participación de las inversiones. |
1983 | Decreto para la racionalización de la industria automotriz. Con este decreto se dio una orientación importante hacia el fortalecimiento de las exportaciones, sobre todo las de vehículos. En ese año, el sector automotor absorbía 97% del déficit comercial total de México. Se estableció principalmente que i) los fabricantes de automóviles debían reducir el número de líneas y modelos de autos con el propósito de alentarlos a aprovechar las economías de escala; ii) el contenido local de los vehículos acabados debía aumentar de 50% a 60%. En caso de no poder cumplir con esto, la armadora tendría que incrementar las exportaciones para hacer una compensación, y iii) las armadoras tendrían que equilibrar anualmente las transacciones en moneda extranjera. |
1989 | Decreto para la modernización y promoción de la industria automotriz. Este decreto se modificó en 1990, 1995 y 1998. Por primera vez desde 1962, se autorizaba la importación de vehículos nuevos, siempre que las armadoras tuvieran un saldo positivo en su balanza comercial. De acuerdo con Moreno-Brid (1996), las armadoras recibieron concesiones fiscales por el equivalente a 30% de sus inversiones. Al mismo tiempo, se fortaleció a la industria de autopartes, pues se estableció que, como mínimo, los autos fabricados en territorio nacional debían incluir al menos 36% de sus componentes fabricados localmente. Sin embargo, se permitían excepciones en los vehículos de exportación. |
2003 | Decreto para el apoyo de la competitividad de la industria automotriz terminal y el impulso al desarrollo del mercado interno de automóviles. En este decreto se contempla: i) estimular la llegada de inversiones para construir o ampliar las actividades de ensamblaje y disminuir los costos de las importaciones mediante la reducción arancelaria: ii) autorizar el registro de nuevas compañías productoras en la industria terminal en territorio nacional (siempre que su inversión en activos fijos fuera de al menos 100 millones de dólares) y contemplen la fabricación de 50.000 vehículos anuales como mínimo, con un plazo de cumplimiento de 3 años a partir del inicio de operaciones; iii) beneficiar la importación de ciertos autos con tasa cero, hasta alcanzar volúmenes de hasta el equivalente a 10% de la producción del año anterior; iv) permitir a las empresas importar mayor cantidad de vehículos siempre que se comprometan a incrementar la inversión y su producción, que continúen con programas de capacitación y desarrollo, que desarrollen proveedores locales y transfieran tecnología a proveedores de primer y segundo nivel. Este decreto se modificó en 2010. |
Fuente: Basado en Miranda (2007), Vega-Cánovas (2010) y Moreno-Brid (1996). |
Cada uno de los decretos anteriores obedece a un interés del momento económico y de los actores que presiden la responsabilidad de política económica del país. Así, el Decreto de 1962 es de integración, el de 1972 el que fija las bases para el desarrollo, el de 1977 para el fomento, el de 1983 de la racionalización, el de 1989 para fomento y modernización y el de 2003 es considerado como promotor de exportaciones.
El TLCAN entre muchos otros aspectos, reforma el decreto automotriz de 1989. Entre los aspectos más relevantes que la firma del TLC trajo, se encuentran los siguientes:
Las tarifas arancelarias a las importaciones fueron reducidas a la mitad.
La tarifa de importación de automóviles y camiones ligeros se redujo de 20 a 10%, acordando eliminarse por completo a partir del año 2004.
16% de las fracciones de autopartes sufrieron reducción de las mismas tarifas inmediatamente, 54% en el periodo de los primeros cinco años posteriores, quedando desgravadas en su totalidad al cabo de diez años.
La tasa arancelaria sobre las autopartes pasó de 14% en 1993 a 10% en 1994 y 3% en 1998.
Se redujo de 1.75 a 0.8 el factor de compensación de la balanza comercial, con lo cual las compañías manufactureras instaladas en México pudieron acelerar el ritmo de sus importaciones.
El margen de contenido nacional para vehículos fabricados en México se definió bajo el siguiente esquema: 34-36% en 1993, 29% en 1998 y 0% para el 2004.
Así, cabe preguntarse, ¿Qué dice el gobierno mexicano actualmen-te con respecto de la industria automotriz? De acuerdo con la Secretaría de Economía, la Dirección General de Industria Pesada y Alta Tecnología, (Secretaría de Economía, 2012). Se expone in extenso con la finalidad de mostrar la actitud acrítica y falaz del gobierno mexicano, que parece más bien representante de las empresas armadoras trasnacionales:
A nivel global, la importancia de la industria automotriz en las economías nacionales y su papel como propulsor para el desarrollo de otros sectores de alto valor agregado, han provocado que diversos países tengan como uno de sus principales objetivos el desarrollo y/o fortalecimiento de esta industria.
México no es la excepción, pues la industria automotriz en nuestro país ha representado un sector estratégico para el desarrollo de nuestro país. Su participación en las exportaciones la coloca como la industria más importante, superando incluso al sector petrolero. En 2011, la industria automotriz exportó el 22.5% del valor de las exportaciones totales.
En 2011, cuatro de cada cinco vehículos producidos en México se exportaron, lo que posiciona a nuestro país entre los más importantes a nivel mundial, ocupando el lugar número 8 en manufactura y el 6 entre los principales países exportadores de vehículos automotores.
Adicionalmente, esta industria se ha constituido como precursora de la competitividad en las regiones donde se ha establecido, lo que se ha traducido, entre otros resultados, en empleos más calificados y mejor remunerados, así como en un mayor desarrollo del capital humano. En promedio, las remuneraciones de la industria automotriz terminal en México equivalen a 2.3 veces las del resto de las manufacturas.
Igualmente, el sector ha generado una importante derrama de capacidades tecnológicas que encuentran aplicación en otros sectores, como son el eléctrico, electrónico y aeroespacial y que, a su vez, han propiciado la generación de cuadros técnicos especializados.
Como ejemplo, conviene señalar que en el sector aeronáutico se ha observado un fuerte crecimiento en los últimos años. Actualmente, México ocupa el primer lugar en inversiones de manufactura aeronáutica en el mundo, con 33 mil millones de dólares en el período 1990-2009, mostrando un crecimiento promedio anual de sus exportaciones mayor a 20%.
En nuestro país se han desarrollado importantes centros de proveeduría de nivel mundial, muchos de ellos con alta integración a las empresas terminales (Tier 1). Así lo evidencia el hecho de que más del 80% de la producción de autopartes se destina a la exportación.
Por su amplia proveeduría y las ventajas competitivas a nivel mundial que ofrece México en mano de obra calificada y competitiva, posición geográfica y acceso preferencial a otros mercados, la industria automotriz mexicana aún tiene un alto potencial de crecimiento y de generación de empleos de alta calidad.
México puede incrementar su competitividad como productor de vehículos y autopartes y convertirse en un importante centro de diseño e innovación tecnológica, para lo cual el desarrollo del capital humano juega un papel fundamental, ya que un bajo nivel de Capital Humano limita la implementación de procesos de mayor valor.
En el siguiente inciso se aportan datos que refieren las ventajas que obtienen las armadoras extranjeras (en especial, las norteamericanas) y las desventajas para nuestro país, a efecto de ponderar críticamente unas y otras.
Volviendo al tema del TLCAN, es evidente que todos los puntos acordados tienen claros beneficios para las automotrices norteamericanas. La coincidencia de puntos de vista manifestados por las empresas y los representantes del gobierno mexicano, en los que se omiten algunos aspectos que cuestionan el punto de vista de que la inversión de las compañías automotrices sólo tienen ventajas. Los aspectos que se han mencionado son, por ejemplo, que el precio de la mano de obra en México en el sector automotriz, es casi diez veces menor que en EUA, a pesar de que los obreros mexicanos son en algunos casos más productivos que sus pares norteamericanos. En lo general, puede afirmarse que tienen el mismo nivel de productividad tomando como base el Harbour Report de 2007 que informa sobre 70 plantas fabricantes de automotores en Norteamérica: Canadá, EUA y México. Añádase que el hecho de la enorme diferencia salarial ha sido, en muchos casos, un factor que ha coadyuvado a que los salarios de esta industria en EUA haya sido reducida a la mitad, desde antes, durante y después de la crisis del 2008-2009, a pesar de que el TLCAN tiene un capítulo creado con el fin de evitar disminuciones salariales y de puestos de trabajo y de que exista una comisión encargada de tal fin.
En los relatos de las empresas automotrices antes reseñados puede observarse que las barreras legales, de idiosincrasia y de conflictos raciales e históricos, fueron abatidos a lo largo de los sesenta años previos a la firma del TLCAN, y que por lo tanto, no es éste el que abre la puerta a la inversión extranjera y al abuso extremo de los contratos laborales, sino que fueron imponiéndose las medidas que necesitaban los consorcios para operar en las mejores condiciones que les garantizan la maximización de sus ganancias. El TLCAN sólo ratifica, legaliza y profundiza el abuso de las compañías hacia sus trabajadores de ambos lados de la frontera, así como de los beneficios en subsidios de impuestos y en el obsequio de infraestructura para operar en las mejores condiciones. Las plantas instaladas en México por las armadoras y los fabricantes de autopartes, organizados en clúster o no, son de magnitudes enormes que se les han otorgado a precios de ganga y con los servicios urbanos que requieren (energía eléctrica barata, agua, pavimentación, drenaje, etc.). La mayoría de las plantas armadoras y de fabricación de motores se miden en cientos de hectáreas con instalaciones y vías óptimas para transportar sus productos y materiales. Asimismo, los clúster que operan alrededor de las plantas son de grandes magnitudes que contaron en su momento con las mismas ventajas y facilidades que las ensambladoras.
5. Integración automotriz en América del Norte y competencia global
Cuando en diciembre de 1992 firman el TLCAN los presidentes de EUA (George Bush), de Canadá (Brian Mulroney) y de México (Carlos Salinas), los grupos de negociación llevaban más de dos años trabajando en el texto que se presentó consolidado con corchetes en enero de 1992; representantes de General Motors Corporation, Ford Motor Company y Chrysler, tuvieron personal que participó permanentemente en las negociaciones.
Una primera conclusión por lo señalado hasta aquí es que las armadoras norteamericanas en México han tenido con el TLCAN la culminación del proceso de integración de la industria automotriz instalada en el país bajo las directrices de Ford, GM y Chrysler.
Sin embargo, el propio TLCAN abrió nuevos desafíos a la competencia global en esta industria de gran importancia en el concierto industrial global y transnacional de la producción mundial en nuestros días. Así, con el Tratado se inicia la etapa de consolidación y absorción, sin ninguna restricción, a las Big Three, que solamente se ve confrontada por la lucha de los mercados de las automotrices Volkswagen y Nissan y en menor medida, de Honda y Toyota.
Es elocuente en mostrar (Gráfica 1) que la industria automotriz ha logrado hacer que su crecimiento sea permanente. De los doce millones de vehículos que se hacían en el año de 1965 a los 87 millones del 2013, muestra un crecimiento de 625% en 47 años, con promedio cercano al 5% anual. Esto a pesar de los muchos vaticinios de hace ya varios años de que por ser una industria madura, estaba en fase de decadencia, y a pesar de las muchas crisis económicas que han pasado en este largo periodo. Parece que la estrategia de apertura de nuevos mercados, especialmente de los países que integran los BRICS (Brasil, Rusia, India, China y Sudáfrica) ha logrado mantener un crecimiento que ha permitido sostener una tasa de ganancias ad hoc. Dentro de este esquema global, en los últimos treinta años, las empresas automotrices estadounidenses han perdido mercado y utilidades ante las empresas alemanas, japonesas, coreanas e inclusive indias. Ante este panorama, la industria automotriz instalada en México juega un papel marginal en la estrategia de las corporaciones, pues la decisión que toman las administraciones de las empresas de incrementar o disminuir la producción en el país se dan en un complejo sistema de variables financieras, laborables y políticas en las que México es, en importancia porcentual, menor al 10% de la facturación de cada ensambladora.
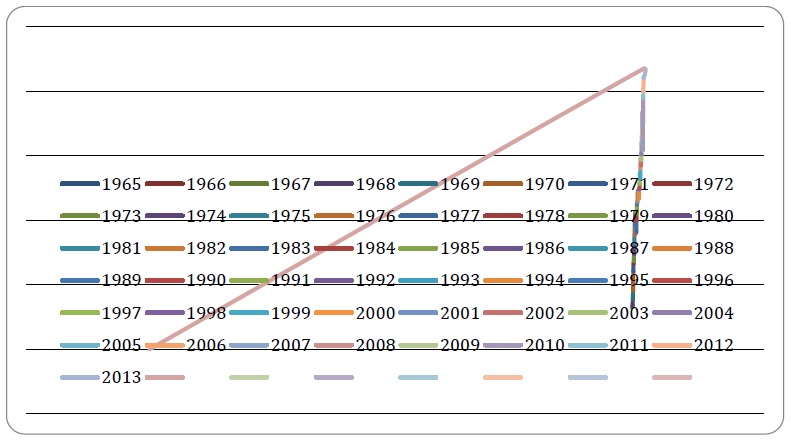
Fuente: Ward´s World Motor Vehicle Data (hasta 2007). OICA (2008-2013)
Gráfica 1 Producción mundial de vehículos 1965-2013
En el Cuadro 2 se aprecia que, excluyendo a China que es la gran fabricante mundial, la producción de vehículos en México ha crecido en los 20 años de TLCAN 189%, un crecimiento de más del doble que el crecimiento mundial, también más que Canadá y mucho más que EUA en donde el incremento es prácticamente nulo. Una buena parte de la explicación de este hecho parece obedecer al castigo que las administraciones de las Big Three están infringiendo al sindicato United Auto Workers (UAW), al que han culpado de los malos resultados financieros de las empresas debido, dicen, a que tienen salarios y prestaciones muy altas. Este argumento es falso, primero porque los fondos de pensión del que tanto mencionan cómo extraordinariamente costosos, son más altos en Alemania, igual que los salarios. Sin embargo, la empresa Volkswagen que cubre dichos costos, goza de inmejorable salud financiera, económica y crecimiento; lo mismo sucede en BMW y Mercedes Benz. La estrategia de GM, Ford y Chrysler ha sido trasladar plantas a países donde los salarios son mucho menores (deslocalización), con facilidades fiscales y de infraestructura y en varios casos, un mercado importante, a la vez que sirve para golpear a la UAW. Esta manera de operar también la han hecho las armadoras alemanas y japonesas -Toyota en menor medida- logrando beneficiarse con un menor costo de mano de obra, misma productividad, y sin sacrificar calidad.
Cuadro 2 Producción de vehículos 1993 y 2013
Producción (miles de unidades) |
% | ||
1993 | 2013 | 2013/1993 | |
Mundo | 46,785 | 87,250 | 86 |
EUA | 10,872 | 11,045 | 2 |
México | 1,055 | 3,052 | 189 |
Canadá | 1,081 | 2,380 | 120 |
Big Three en México | 635 | 1,556 | 145 |
China | 1,297 | 22,117 | 1605 |
Fuente: OICA. |
En el Cuadro 3 se observa que en EUA disminuyeron los empleos 27%, aunque la producción creció 2% en el periodo (Cuadro 2); en México el crecimiento de la producción es de 189% y 50% de empleos, y en Canadá la producción se incrementa 120% y los empleos bajan 12%. El contraste considerando las Big Three en conjunto es aún mayor: la producción aumenta 145% y los empleos disminuyen 41%. Hay varios factores que explican estas grandes diferencias entre los que destacan la mayor robotización y las técnicas administrativas de producción para incrementar la productividad. Sin embargo, existen diferentes estudios que muestran que la intensificación del trabajo en las empresas automotrices en el mundo ha aumentado de manera importante, provocando mayor estrés en los trabajadores (Stewart, Paul, Danford Andy, Mrozowicki Adam & Murphy Kenny, 2013). Lo que resulta incomprensible y lastimoso es ver que los salarios y prestaciones han disminuido de manera importante en el periodo, como se ve más adelante. Por otro lado, se evidencia, en lo que respecta a Norteamérica, el traslado de producción de los EUA a México. Todas las armadoras, incluyendo a las norteamericanas han acelerado el traspaso de su producción a países con las ventajas que ya hemos enunciado (mano de obra barata, sindicatos dóciles, subsidios fiscales, infraestructura para sus plantas y sus proveedores, y nuevos mercados para sus productos).
Cuadro 3 Empleados, industria automotriz 1993 y 2012
Empleados* (miles) |
% | ||
1993 | 2012 | 2012/1993 | |
Mundo | nd | 8400* | |
EUA | 1080 | 790 | -27 |
México | 386 | 580 | 50 |
Canadá | 130 | 115 | -12 |
Big Three México | 51 | 30 | -41 |
China | 1,650 | ||
Fuente: Elaboración propia con base en datos de Bureau of Labor Statistics, OICA, INEGI y Expansión. |
* Incluye trabajadores de armadoras y autopartes
Por lo que respecta a salarios y remuneraciones:
1) Las Big Three tienen, casi permanentemente en los últimos 20 años, el 51% de la producción del país (Carrillo y González, 1999), lo que permite sugerir que los datos presentados son válidos. También es probable que la situación sea peor (Quiroz, 2009 :5).
2) Se concluye (Castellanos 2012): Los salarios de este cuadro son promedios, lo que quiere decir que dentro de las plantas, la gran mayoría de los trabajadores gana un salario significativamente menor del que se presenta y, los menos, (operarios especializados) ganan varias veces más.
Cuadro 4 Salarios y productividad en la industria automotriz, 1994-1997
|
Fuente: Carrillo y González 1999: 101. |
Cuadro 5 Salarios e incrementos salariales 2003- 2008 (en pesos mexicanos corrientes)
Concepto | 2003 | 2008 | 2008/2003 |
Salario diario con prestaciones (total) | 258.33 | 306.41 | 18.6 |
Salario diario sin prestaciones (total) | 198.71 | 235.93 | 18.7 |
Salario diario administrativos de armadoras | 828.93 | 900.99 | 8.7 |
Salario diario obreros de armadoras | 299.34 | 325.36 | 8.7 |
Salario diario administrativos autopartes | 432.38 | 514.98 | 19.1 |
Salario diario de obreros autopartes | 143.81 | 171.28 | 19.1 |
Salario por hora del total (Con prestaciones) | 42.63 | 50.69 | 18.9 |
Salario por hora en armadoras | 116.11 | 126.20 | 8.7 |
Salario por hora de autopartes | 36.54 | 43.52 | 19.1 |
Fuente: Elaboración propia con datos de INEGI, La industria automotriz en México, 2010. |
Los salarios de este cuadro son promedios, lo que quiere decir que dentro de las plantas, la gran mayoría de los trabajadores gana un salario significativamente menor del que se presenta y, los menos, (operarios especializados) ganan varias veces más.
Cuadro 6 Salarios y productividad en la industria automotriz, 2003-2008
|
Fuente: Castellanos (2012) |
Con la finalidad de aportar información acerca de que los obreros mexicanos “ganan menos porque hacen menos”, vale la pena comentar que el director del departamento de recursos humanos de la planta de Nissan Aguascalientes afirmó, en la visita a sus instalaciones en septiembre del 2009, que dicha planta es reconocida como la más productiva de Nissan en el nivel mundial. Asimismo, en la encuesta aplicada en 31 plantas de autopartes entre 2008 y 2209, tanto los ingenieros como los obreros de las plantas mexicanas, fueron generalmente calificados como de clase mundial.
Como se aprecia (Cuadro 7), la exportación de vehículos tuvo en el periodo un crecimiento de 853%, que es mayor al 12% de promedio anual. Por su lado, la exportación de autopartes creció 378% en el periodo, más del 7% promedio anual. Aunque el promedio de la importación de autos es muy alto, como su base es pequeña (823 millones de dólares en 1993) el efecto en números absolutos no es tan significativo como para afectar el elevado saldo positivo en la balanza comercial de la industria automotriz.
Cuadro 7 Valor de las exportaciones e importaciones 1993 y 2012 (millones de dólares a precios de 2012)
1993 | 2012 | 2012/1993 | |
Exportaciones vehículos | 5506 | 52485 | 853 |
Exportaciones autopartes | 4173 | 19935 | 378 |
Total de exportaciones | 9679 | 72420 | 648 |
Importaciones de vehículos | 823 | 14320 | 1640 |
Importaciones de ensambles | 9791 | ||
Importaciones de autopartes | 2380 | 20599 | 765 |
Total de importaciones | 12994 | 34915 | 168 |
Saldo de la balanza comercial | -3315 | 37505 | |
Fuente: Datos de 1993 en Juan Carlos Moreno Brid (1996). Datos del 2012 en INEGI (2010), Cuadros 3.3.3 y 3.3.4 |
Una consideración necesaria en el análisis de esta industria es que el tan pontificado crecimiento de las exportaciones que provoca un saldo favorable de la balanza comercial del país, éste, es de las empresas armadoras y fabricantes de autopartes. El dinero está en sus arcas, no en las del gobierno. Lo que se paga a los trabajadores mexicanos ronda cerca del 10% del valor de las exportaciones. Por último, como se observa en el mismo cuadro, el saldo de la balanza en autopartes es deficitario (664 mmd) que, además de su pequeña importancia, es dinero que se maneja intercompañías, sin tener un efecto en las arcas nacionales.
Cuadro 8 Datos Generales sobre la industria automotriz instalada en México
El número que aparece entre paréntesis junto al nombre de la empresa es el lugar que les corresponde en las 500 empresas más importantes de México. Como se ve, la venta de cada una de las firmas es enorme. Sin embargo, en ningún caso alcanza el 10% de la venta total de la compañía a la que corresponde. Los resultados estimados se determinaron con un promedio de las utilidades que tienen las empresas en el nivel mundial (8%). El resultado muestra que las inversiones que realizan GM, Ford y Chrysler, son sólo una parte de las utilidades que obtienen en México.
Cuadro 9 Utilidades de las armadoras de vehículos en México 2012
Empresa | Ventas (millones de pesos) |
Ventas (millones de dólares) 1=12.76 |
Utilidad (millones de dólares) |
GM (8) | 181,656 | 14,236 | 1139 |
VW (10) | 161,401 | 12,649 | 1012 |
Ford (15) | 132,790 | 10,407 | 833 |
Nissan (16) | 132,176 | 10,359 | 829 |
Chrysler (17) | 123,900 | 9,710 | 777 |
Fuente: Expansión (2013). |
Esta consideración debería ser tomada en cuenta por las autoridades gubernamentales para negociar mayores beneficios para el país, como mejor remuneración salarial, menos exenciones en impuestos y exigir una verdadera promoción de fabricantes mexicanos tanto de autopartes como de vehículos.
Los voceros gubernamentales y diversos analistas de esta industria creen que la instalación de fábricas de vehículos y autopartes en nuestro país transfieren tecnología benéfica al mismo. Es difícil asegurar que es nula, pero sí parece ser insignificante. Primera-mente, Los ingenieros y operarios que trabajan en esas empresas extranjeras, no pueden posteriormente laborar en alguna empresa mexicana en la que aplique los conocimientos adquiridos. No sólo porque no hay más que empresas extranjeras, sino porque al contratar personal, los trabajadores firman un acuerdo de confiabilidad en que no pueden aplicar lo conocido en otra empresa. Segundo, las pocas empresas mexicanas que hacen autopartes, o son de coinversión, de la que es casi imposible salirse y aprovecharla, o son pequeñas empresas por los requerimientos de grandes cantidades de recursos que se requieren para montar una planta adecuada (las conocidas barreras de entrada).
Conclusiones
El TLCAN fue la culminación de un largo proceso de negociaciones de las empresas norteamericanas, desde la década de 1940, para tener enormes facilidades y ventajas en el establecimiento de fábricas en México. A partir del TLCAN las armadoras dictan la política industrial de la industria automotriz en el país.
Las principales ventajas que obtuvieron las Big Three fueron la obtención de enormes terrenos a precios simbólicos, con todas las facilidades de urbanización (agua, electricidad, drenaje, vías cercanas hacia los puertos y hacia el Norte), mano de obra calificada, disciplinada responsable y muy barata, así como sindicatos sometidos a los designios de la administración de los consorcios. También, cercanía al mercado que eligieron las empresas.
El establecimiento de las fábricas de vehículos y autopartes en México ha ayudado a las Big Three a desmantelar las prestaciones y reducir salarios de los trabajadores de esas empresas en EUA, afiliados a la UAW.
La creación de empleos en México en la industria automotriz asciende a 600 mil trabajadores directos, los mejor pagados en la industria del país, ha sido a costa de los trabajadores de EUA, cuyos salarios son diez veces mayores que los de los trabajadores mexicanos.
Las cuantiosas inversiones que han hecho históricamente las Big Three son sólo una parte de las utilidades que han obtenido en el país.
Las enormes exportaciones de esta industria, que aporta un gran superávit a nuestra balanza comercial, son realmente exportaciones de las armadoras norteamericanas y los recursos los utilizan según sus intereses.
La transferencia tecnológica por la instalación de las Big Three en México tiene repercusiones insignificantes para el país y sus habitantes.