Introducción
La corrosión y su control constituyen temas de gran interés científico y tecnológico, dado el impacto que tiene este fenómeno en la degradación de materiales y sistemas ingenieriles, así como las grandes pérdidas económicas asociadas. La protección anticorrosiva es particularmente importante cuando se trabaja con metales y aleaciones, que son ampliamente usados en función de sus propiedades físicas y mecánicas, pero que pueden ser muy susceptibles a la degradación, especialmente en ambientes agresivos [1].
El control de la corrosión en los metales se puede realizar de varias maneras, siendo una de las más comunes el uso de recubrimientos. Para obtener recubrimientos protectores sobre una superficie metálica se puede emplear una amplia variedad de materiales y técnicas. Las películas derivadas de procesos sol-gel han mostrado resultados prometedores y han sido estudiadas por varios autores. Las ventajas de estos recubrimientos incluyen la relativa sencillez de los procedimientos a seguir para obtenerlos, la homogeneidad de las películas obtenidas, la capacidad de recubrir superficies relativamente grandes y complejas, y la posibilidad de controlar el tamaño y la morfología de las partículas en el recubrimiento [2-6].
Entre los materiales que han recibido mayor atención para formar recubrimientos sol-gel se encuentran los óxidos de silicio, zirconio, aluminio, titanio y cerio (SiO2, ZrO2, Al2O3, TiO2, CeO2), así como varias de sus combinaciones. El ZrO2 presenta propiedades singulares tales como elevada resistencia al desgaste, baja actividad química, resistencia al rayado, alta resistencia eléctrica y térmica. Estas propiedades lo hacen muy útil en una variedad de aplicaciones, incluyendo las películas protectoras [2-6]. Con el fin de mejorar las propiedades mecánicas y eléctricas del ZrO2 a elevadas temperaturas, se requiere estabilizar su estructura en fase cúbica o tetragonal con ayuda de un dopante, asimismo podrá ser utilizado en varias aplicaciones con demandas mecánicas o estructurales [7].
Los sustratos metálicos más empleados en estudios de corrosión incluyen aceros al carbono e inoxidables y las aleaciones de aluminio. Las técnicas para recubrir estos sustratos pueden ser por aspersión y electrodeposición [8]. Sin embargo, las técnicas más usadas en este caso son dip-coating y spin-coating, ya que son técnicas que no requieren de equipos sofisticados, hacen posible la reproducibilidad de los resultados experimentales alcanzados y son suficientemente versátiles para realizar recubrimientos a nivel industrial [2-6].
Los estudios efectuados muestran que los recubrimientos cerámicos derivados de procesos sol-gel mejoran sustancialmente la resistencia a la corrosión de los aceros y las aleaciones de aluminio. Por otro lado, dado que las propiedades mecánicas y físicas de los recubrimientos dependen de la composición, forma, tamaño y distribución de tamaño de las partículas que los conforman, existe especial interés en los recubrimientos de óxidos cerámicos. En estos casos se han evidenciado mejoras en sus propiedades a medida que se controla y reduce el tamaño de las partículas [5,9,10].
Durante las dos últimas décadas, varios autores han estudiado y evaluado las propiedades anticorrosivas de recubrimientos sol-gel de zirconia aplicados sobre sustratos metálicos [3,11]. De acuerdo con [3] la zirconia incrementa la vida útil del acero inoxidable en un factor de 8 en un ambiente muy agresivo ya que forma una barrera física de protección [11]. Además, al someter el recubrimiento a un tratamiento térmico se logra una superficie libre de grietas y con mejores propiedades anticorrosivas. Se ha trabajado especialmente con estructuras cristalinas estabilizadas con itria [6,12-14]. Sin embargo, una de las alternativas para obtener películas con fines de protección anticorrosiva podría ser el uso de zirconia estabilizada con calcia, que resulta en un compuesto (CaZrO3) más estable químicamente y con buena resistencia a la corrosión que hasta el momento parece no haber sido estudiado sobre sustratos de acero inoxidable y aluminio comercial. Al solubilizarse el óxido de calcio en el óxido de zirconio se forma una solución sólida en la fase cúbica, sea este parcial o totalmente estabilizado, dependiendo de la cantidad de óxido dopante y temperatura de calcinación. Además del uso del calcio como estabilizante, actualmente existe interés en estudiar: a) uso de diferentes precursores en el proceso sol-gel, b) obtención de recubrimientos con tamaño y morfología de partículas controlados, c) formulación de procesos que permitan aplicar películas homogéneas, libres de defectos y de mayor espesor (que las obtenidas hasta el momento) y d) empleo de películas nanocompuestas e híbridas.
En este trabajo se sintetizó óxido de zirconio estabilizado con calcia por el método de sol-gel, con el propósito de obtener un recubrimiento anticorrosivo sobre sustratos de acero inoxidable 304 y aluminio comercial mediante los métodos de dip-coating y spin-coating. Además, se evaluó la resistencia anticorrosiva de los recubrimientos mediante un ensayo en cámara salina, ya que es una de las técnicas más utilizadas a escala industrial y que representa una alternativa de evaluación de la resistencia a la corrosión frente a técnicas electroquímicas usadas por otros autores [2,3].
Metodología Experimental
Obtención y caracterización del sol-gel de ZrO 2 estabilizado con calcia
Para la obtención del sol-gel de zirconia estabilizada con calcia se utilizó oxicloruro de zirconio octahidratado (como precursor) y acetato de calcio monohidratado (como estabilizador de la estructura cúbica), en una relación molar precursor/estabilizante de 0.84/0.16 y se añadió glicina para regular el pH a 4. Se consideró un tiempo de envejecimiento de 24 h luego del cual se realizó un proceso de evaporación a 80 ± 10 °C hasta conseguir una solución viscosa de color café claro [7,14].
Para evaluar las características del sol-gel obtenido se realizó un análisis termogravimétrico (TGA) usando un analizador Q500 de TA. Durante el análisis se elevó la temperatura a una tasa de 5 °C/min hasta alcanzar los 600 °C. El sol-gel obtenido se calcinó a 550 y 600 °C, durante 30 min, a una tasa de calentamiento y de enfriamiento de 5 °C/min. Al finalizar este proceso se obtuvo un polvo fino de color blanco, correspondiente a nanopartículas de ZrO2 estabilizado con calcia. Estas partículas fueron caracterizadas por difracción de rayos X (DRX) en un difactrómetro Empyrean de Panalytical, dispersión dinámica de luz (DLS) en el analizador de tamaño de partícula Brookhaven 90 Plus, microscopía electrónica de barrido (SEM) en el microscopio Aspex, PSEM eXpresTM y microscopia electrónica de trasmisión (TEM) en el TECNAI, G2 Spirit Twin de FEI [7]. Estos análisis permitieron determinar si se obtienen recubrimientos de naturaleza híbrida o completamente cerámica.
Síntesis y caracterización de las películas de ZrO 2 estabilizado con calcia aplicadas sobre sustratos metálicos
Los recubrimientos sobre los sustratos metálicos fueron obtenidos mediante el depósito sobre los sustratos del sol-gel obtenido durante el proceso de síntesis, por dip-coating y spin-coating. Previo a este proceso, se realizó una limpieza y acondicionamiento de la superficie de los sustratos de acuerdo a la norma ASTM G1. Se utilizaron sustratos de 3 × 5 cm2 de acero inoxidable 304 y de aluminio comercial. Para realizar el recubrimiento mediante dip-coating el sustrato metálico fue sumergido en el sol-gel obtenido durante 1 min y luego fue lavado con agua destilada por 30 s, eliminando así las partículas no adheridas a la superficie. Este proceso se repitió por tres ocasiones. La obtención del recubrimiento por spin-coating consistió en aplicar el sol-gel sobre el sustrato metálico a una velocidad de rotación de 3000 rpm durante 60 s utilizando un spin-coater Holmarc, HO-TH-05 [13].
Con el fin de establecer la influencia de la temperatura y tiempo de calcinación del recubrimiento sobre los sustratos se consideró un diseño experimental 22 cuyas variables experimentales fueron la temperatura y tiempo de calcinación. Las temperaturas consideradas fueron 550 y 600 °C y los tiempos fueron 5 y 10 min. Se utilizó una velocidad de calentamiento de 5 °C/min y de enfriamiento de 10 °C/min [15]. A continuación, se determinó el espesor de los recubrimientos utilizando un perfilómetro Bruker, DektakXT. Los espesores fueron medidos en la parte central de la placa, haciendo recorrer el sensor una longitud de 2 cm. Finalmente, para seleccionar las condiciones más adecuadas de densificación del recubrimiento, a los sustratos metálicos recubiertos se les realizó una evaluación mediante la prueba de trama cruzada según la norma ASTM D3359-09 para determinar de manera cualitativa la adhesión del recubrimiento al sustrato según el porcentaje de recubrimiento adherido en la cinta adhesiva. Se realizaron tres mediciones utilizando tres muestras diferentes de cada uno de los recubrimientos en cada sustrato estudiado.
Evaluación de las propiedades anticorrosivas
Una vez caracterizados los recubrimientos, se preparó un nuevo conjunto de sustratos metálicos con recubrimientos utilizando las condiciones de mejor adherencia. A continuación, se evaluó la resistencia a la corrosión durante 500 h en una cámara salina Q-FOG, CCT-600 utilizando una solución de cloruro de sodio al 5% en peso, de acuerdo con la norma ASTM B117-11. A los sustratos metálicos se les colocó cinta adhesiva en su contorno, antes de ser ubicados en la cámara salina, para evitar el contacto del área que no está recubierta con la solución salina para así poder evaluar solo el área recubierta. Al finalizar las 500 h de exposición, los sustratos fueron lavados para eliminar la sal y los residuos de óxido. Luego, se cuantificó el área en cada una de las muestras que presentaba algún tipo de defecto superficial, ligado a procesos de corrosión del sustrato. Para la cuantificación, se utilizó una cuadrícula milimetrada, en donde se pudo evaluar el área total de cada muestra y el área de cada defecto encontrado, y se calculó el porcentaje. Se realizaron tres mediciones utilizando tres muestras diferentes en cada caso estudiado. Finalmente, se obtuvieron fotografías de los sustratos metálicos ensayados usando un microscopio óptico marca Meiji Techno, MZ-13TR, a 50 aumentos, para evaluar las fallas del recubrimiento y la presencia de corrosión en la superficie de los sustratos. Además, se ensayaron los sustratos sin recubrimiento a manera de blanco: a) sometido al mismo tratamiento térmico del recubrimiento y b) sin tratamiento térmico.
Resultados y discusión
Caracterización del sol-gel de ZrO 2 estabilizado con calcia
La Figura 1 muestra el termograma del sol-gel de ZrO2 estabilizado con calcia y se observa que existen dos escalones relacionados con la pérdida de masa de la muestra a medida que se eleva la temperatura. El primer escalón, comprendido entre 25 y 170 °C, corresponde principalmente a la eliminación del solvente y presenta una temperatura de máxima tasa de degradación en 107 °C de acuerdo con la curva derivada. En esta fase se obtiene una pérdida de peso del 18 %. El segundo escalón empieza a partir de 170 °C hasta aproximadamente 300 °C, donde ocurre la combustión de la materia orgánica y corresponde a una pérdida de peso del 3 %. La temperatura de máxima tasa de degradación para la pérdida de la materia orgánica es igual a 175 °C. A partir de los 300 °C, la masa del sol-gel se mantiene constante, en un 79 % del peso inicial, hasta cerca de los 600 °C. Se establece entonces que el recubrimiento densificado a 550 °C y 600 °C aplicados sobre los sustratos es de tipo cerámico ya que todo el material orgánico fue eliminado.
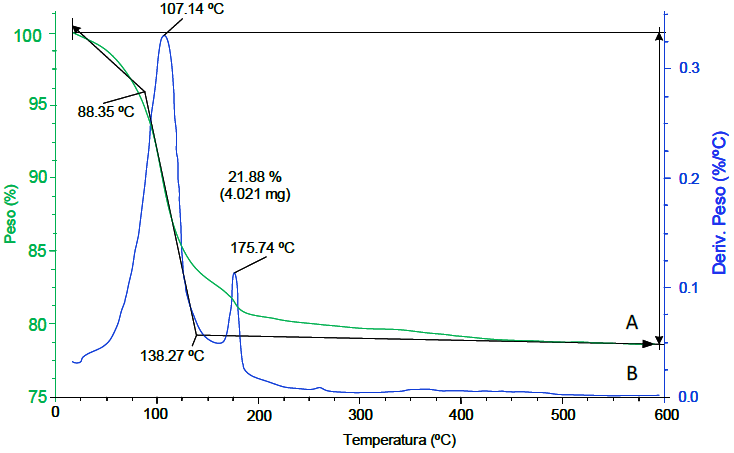
Figura 1 Termograma del sol-gel de ZrO2 estabilizado con calcia a) curva primaria y b) curva derivada.
El polvo que se obtuvo del proceso de calcinación del solgel fue caracterizado por DRX. Esta caracterización permitió verificar la obtención del ZrO2 estabilizado con calcia en una estructura cúbica al comparar los picos obtenidos con los de una muestra de óxido de zirconio en fase cúbica dopada con 15 %mol de calcia de la base de datos PCPDFWIN v2.01 [16]. Se observa que existe un ligero desplazamiento del pico en 95 ° y esto se puede deber a que existe una diferencia en la cantidad de calcio presente en las muestras sintetizadas. Además, no se observaron modificaciones significativas en la estructura cristalina al variar la temperatura de calcinación entre 550 y 600 °C como se muestra en la Figura 2.

Figura 2 Difractograma del óxido de zirconio estabilizado con calcia tratado térmicamente a 550 °C y 600 °C.
Mediante el ensayo de dispersión dinámica de luz (DLS), al analizar el tamaño de las nanopartículas de ZrO2 estabilizado con calcia se observa que el tamaño se ve afectado por la variación de la temperatura de calcinación. Así, se obtienen partículas con tamaños menores e iguales a 5.2 nm al utilizar una temperatura de 600 °C mientras que a 550 °C se obtienen tamaños iguales a 7.2 nm. Esta variación en el tamaño de partícula se debe a que al incrementar la temperatura y tiempo de calcinación se producen contracciones y movimientos de los poros entre las partículas [17].
En la Figura 3 se muestran las micrografias obtenidas por microscopía electrónica de barrido (SEM) y de transmisión (TEM) de las muestras de ZrO2 estabilizadas con calcio sintetizadas a 550 y 600 °C por 30 min, respectivamente. Se aprecia en las micrografías SEM, al utilizar un detector de electrones retrodispersados, que las partículas se encuentran formando aglomerados lisos de forma irregular y de composición homogénea ya que existe una sola fase en los compuestos sintetizados. Además, las muestras obtenidas a 550 °C presentan un tamaño de partícula entre 3 y 30 μm aproximadamente y de 1 y 33 μm para las muestras obtenidas a 600 °C. En las micrografías obtenidas por TEM se observa que existen partículas entre 9 y aglomerados de 51 nm aproximadamente y partículas con un tamaño de entre 1 y 17 nm en cada temperatura de síntesis de 550 y 600 °C, respectivamente [18].
Caracterización de las películas de ZrO 2 estabilizado con calcia aplicadas sobre sustratos metálicos
En la Tabla 1 se muestran los resultados del espesor aproximado para los recubrimientos obtenidos por dip-coating y spin-coating sobre sustratos de acero inoxidable 304 y aluminio comercial determinados por perfilometría. Los valores de espesor corresponden a valores promedio, sin tomar en cuenta los picos más altos o más bajos de la superficie del recubrimiento, ya que estos pueden deberse a fallas del sustrato y a que la superficie del sustrato no es totalmente plana. Además, las mediciones de perfilometría permitieron establecer que los espesores son muy regulares a lo largo de los recubrimientos.
Tabla 1 Espesores promedio de los recubrimientos sobre los sustratos metálicos.
Técnica | Espesor del recubrimiento | |
---|---|---|
Acero inoxidable 304 (μm) |
Aluminio comercial (μm) |
|
Dip-coating | 3.0 | 1.6 |
Spin-coating | 2.0 | 1.5 |
Los porcentajes del recubrimiento adherido al sustrato que se muestran en la Tabla 2, fueron determinados siguiendo la norma ASTM D3359-09. Con base en estos resultados, la interacción de las variables tiempo y temperatura de calcinación sobre la adhesión del recubrimiento al sustrato metálico se analizó mediante el programa estadístico Statgraphics Centurion XVI y cuyas gráficas se muestran en la Figura 4.
Tabla 2 Porcentaje promedio de adhesión de los recubrimientos.
Temperatura (ºC) |
Tiempo (min) |
Acero inoxidable 304 (%) |
Aluminio comercial (%) |
||
---|---|---|---|---|---|
dip- coating |
spin- coating |
dip- coating |
spin- coating |
||
550 | 5 | 94.5±0.5 | 95.5±0.5 | 97.0±1.0 | 97.5±0.5 |
10 | 97.5±0.5 | 98.3±0.3 | 97.5±0.5 | 98.2±0.3 | |
600 | 5 | 92.5±0.5 | 94.0±1.0 | 99.5±0.5 | 99.8±0.3 |
10 | 86.3±1.5 | 91.0±1.0 | 99.2±0.3 | 99.7±0.3 |
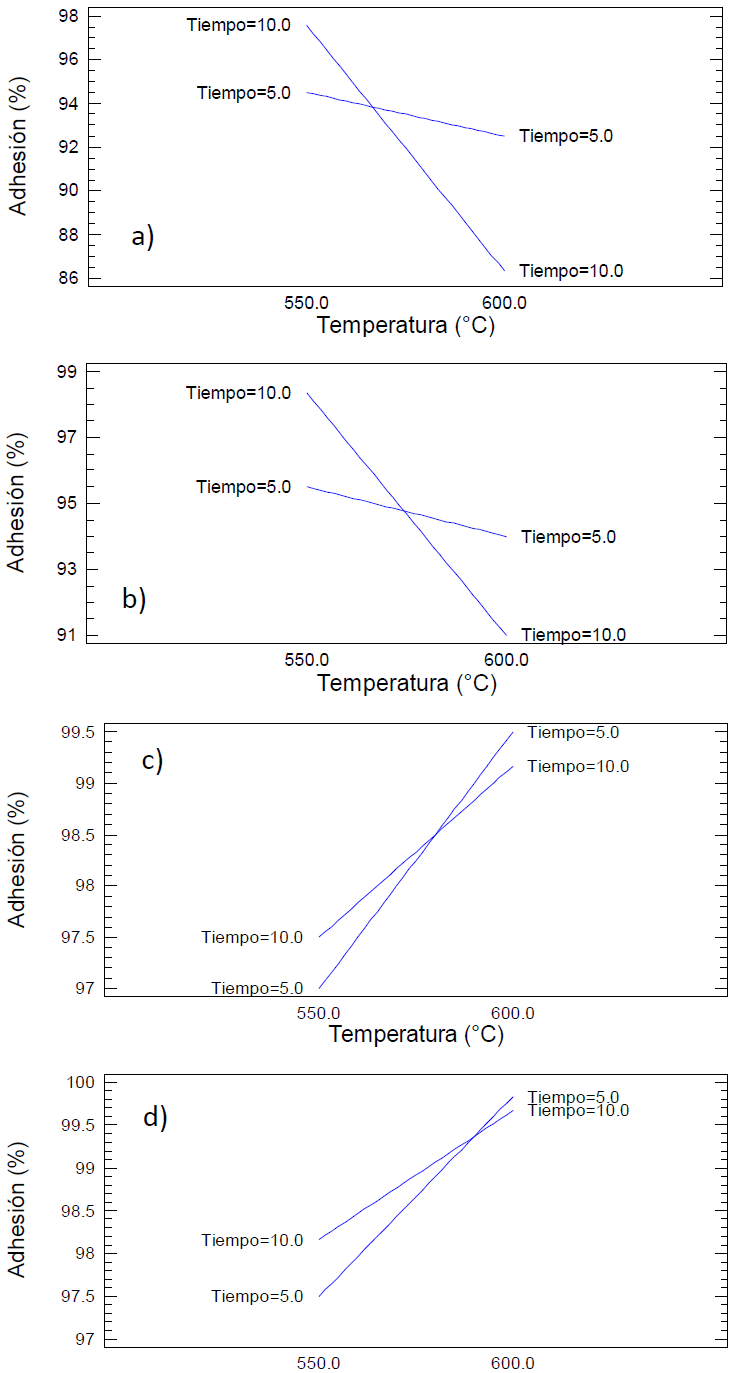
Figura 4 Interacción de la temperatura y el tiempo en la adhesión de los recubrimientos depositados sobre acero inoxidable 304 por a) dip-coating y b) spin-coating, y sobre sustratos de aluminio comercial por c) dip-coating y d) spin-coating.
Como se puede observar en la Tabla 2 y la Figura 4, existe una interacción entre la temperatura y tiempo de calcinación de los recubrimientos respecto al porcentaje de adhesión. Por tanto, se podría establecer que existe mayor porcentaje de adhesión a mayor densificación de los recubrimientos sobre los sustratos metálicos. Para los tiempos y temperaturas evaluados en la Figura 4, se observa que el porcentaje de adhesión aumenta con el tiempo de densificación cuando la temperatura es de 550 °C, mientras que disminuye en función del tiempo cuando la temperatura es de 600 °C para ambos tipos de sustratos. Es decir que, a mayor temperatura se requiere menos tiempo de calcinación, y viceversa. Sin embargo, se establece que la mayor adherencia para el recubrimiento sobre los sustratos de acero inoxidable 304 se obtuvo a 550 °C calcinado durante 10 min, mientras que, para los sustratos de aluminio comercial, es a la temperatura de 600°C y 5 min de calcinación. Usando estas condiciones se obtuvo un nuevo conjunto de sustratos metálicos recubiertos para evaluar las propiedades anticorrosivas en ambiente salino.
Evaluación de las propiedades anticorrosivas
En la Tabla 3 se presenta la cuantificación del área afectada después del ensayo en cámara salina, para los diferentes sustratos y recubrimientos. En este análisis se tuvo en cuenta defectos de la muestra ligados a procesos corrosivos. Adicionalmente, se evaluó cada muestra después del ensayo de cámara salina, mediante microscopía óptica, para verificar si las fallas presentadas se deben a la corrosión del sustrato y descartar cualquier defecto de la superficie del sustrato o defectos debidos a la aplicación del recubrimiento.
Tabla 3 Porcentaje promedio de área corroída en las muestras de acero inoxidable 304 y aluminio comercial después de 500 horas de ensayo en cámara salina.
Muestra | Recubrimiento | Tratamiento térmico |
Area corroída (%) |
---|---|---|---|
Acero inoxidable 304 |
No | Si | 98.7 ± 1.2 |
No | No | 1.7 ± 0.6 | |
Dip-coating | Si | 2.3 ± 1.5 | |
Spin-coating | Si | 5.3 ± 1.5 | |
Aluminio comercial |
No | Si | 92.0 ± 3.5 |
No | No | 84.7 ± 5.0 | |
Dip-coating | Si | ≤ 1 | |
Spin-coating | Si | ≤ 1 |
Se puede apreciar que después de 500 horas de ensayo en un ambiente de cámara salina, los recubrimientos se comportan de manera que previenen la corrosión en el sustrato. Si se comparan los resultados obtenidos de las muestras con recubrimiento y el sustrato sin recubrimiento, se verifica que el revestimiento obtenido brinda protección contra la corrosión, independiente del método de aplicación, con excepción del acero inoxidable 304 sin tratamiento térmico, donde se evidencian resultados similares al material revestido. Sin embargo, el metal base se ve comprometido en su estructura por fallas tipo picadura como se evidencia en la Figura 5, no así los materiales revestidos.

Figura 5 Micrografias ópticas a 50X, de los sustratos de acero inoxidable 304 (a-d) y aluminio comercial (e-h) finalizado el ensayo en la cámara salina: (a y e) sustrato sin recubrimiento con tratamiento térmico, (b y f) sustrato sin recubrimiento ni tratamiento térmico, (c y g) sustrato con recubrimiento aplicados por dip-coating y (d y h) sustrato con recubrimiento aplicados por spin-coating.
En la Figura 5(a-d) se presentan las micrografías ópticas de los sustratos de acero inoxidable 304 sin recubrimiento y con recubrimientos aplicados por dip-coating y spin-coating, una vez finalizado el ensayo en la cámara salina durante 500 h. Como se puede observar, los sustratos sin recubrimiento se ven afectados por la corrosión, especialmente aquel sometido a tratamiento térmico. En este caso se observa la formación de una capa de material corroído y la presencia de picaduras en la superficie del metal. En el sustrato que no fue sometido a procesos térmicos se observa un inicio de corrosión por picadura, que a largo plazo puede conducir a una degradación del metal.
Adicionalmente se observa que, la superficie del recubrimiento aplicado por dip-coating es más homogénea y tiene una mayor resistencia a la corrosión con respecto al recubrimiento obtenido por el método de spin-coating. Después de las 500 h de exposición en cámara salina los sustratos recubiertos por dip-coating no presentan fallas en su superficie. Por otro lado, los recubrimientos obtenidos por spin-coating presentan defectos en su superficie debidos a la no homogeneidad en el recubrimiento, como se observa en la Figura 5d).
En la Figura 5(e-h) se presentan las micrografías ópticas de los sustratos de aluminio comercial sin recubrimiento y con recubrimiento aplicados por dip-coating y spin-coating una vez finalizado el ensayo en la cámara salina durante 500 h. En las micrografías e) y f) se puede observar el deterioro del sustrato de aluminio sin recubrimiento debido a la corrosión producida por el ambiente salino independientemente de que el sustrato haya sido sometido o no a tratamiento térmico. En la micrografía g) se observa que la superficie del recubrimiento obtenido por dip-coating es más homogénea que la del recubrimiento obtenido por spin-coating, que se muestra en la micrografía h). En general, y de acuerdo a las micrografías g) y h), el recubrimiento permanece en perfecto estado sin evidenciar degradación. De esta manera brinda protección al sustrato de aluminio, contra la corrosión provocada por la solución salina.
En el caso de los sustratos de aluminio comercial, después de las 500 h de exposición en cámara salina no se evidenciaron fallas en su superficie, independientemente del método usado para su aplicación. Esto se diferencia claramente de lo sucedido en el caso los sustratos de acero con recubrimientos obtenidos por spin-coating, en los cuales sí se evidenciaron corrosión. Se muestra entonces que, en medios corrosivos salinos, los recubrimientos de óxido de zirconio estabilizado con calcia aplicados sobre sustratos de aluminio comercial brindan una elevada protección anticorrosiva.
En este trabajo se consiguieron mejores resultados de protección anticorrosiva de los sustratos de acero inoxidable 304 y aluminio comercial recubiertos con partículas de óxido de circonio estabilizado con calcia respecto a otros trabajos similares. Así, por ejemplo, en el trabajo realizado por Yañez [19] se obtuvieron recubrimientos con nanopartículas de óxido de zirconio dopado con itrio sobre sustratos de acero al carbono AISI-1012. Las propiedades protectoras de estos recubrimientos fallaron al cabo de unas horas de exponerlos a medios corrosivos de cloruro de sodio al 5 % en peso [19].
Conclusiones
La síntesis de óxido de zirconio estabilizado con calcia mediante el método de sol-gel permitió obtener una solución viscosa y homogénea que posibilitó la obtención de películas entre 1.5 y 3 μm sobre sustratos de acero inoxidable 304 y aluminio comercial. Los recubrimientos cerámicos obtenidos sobre acero inoxidable 304 tienen espesores de entre 2 y 3 μm mientras que los obtenidos sobre sustratos de aluminio comercial tienen espesores de entre 1.5 y 1.6 μm en función de la técnica de aplicación del recubrimiento. En ambos casos, la aplicación mediante spin-coating resultó en recubrimientos de menor espesor, comparados con los obtenidos mediante dip-coating.
La evaluación de las propiedades anticorrosivas del recubrimiento mostró que la película de partículas de zirconia cúbica estabilizada con calcia proporciona una barrera física y química anticorrosiva a los sustratos de acero y aluminio expuestos a un ambiente corrosivo generado por una cámara salina. La protección del recubrimiento ante la corrosión en ambiente salino fue mayor en el caso de los sustratos de aluminio comercial, en comparación con los sustratos de acero inoxidable 304, pese a tener un espesor del revestimiento menor. Además, en los dos sustratos metálicos los recubrimientos aplicados por dip-coating mostraron una mejor resistencia a la corrosión en comparación a los obtenidos por spin-coating.