Introducción
La ingeniería de procesos enfocada al desarrollo de productos en la industria automotriz en ocasiones mejora los procesos utilizando métodos alternativos, como es el método por elementos finitos (CAD-CAE), contribuyendo a que las empresas cumplan con los requerimientos de la calidad en la mejora continua. Los resultados determinan un nuevo diseño o alternativa de producción, con un resultado positivo para lograr una mejor competitividad y superando las expectativas del cliente, al mismo tiempo que reducen costos por garantía o reprocesos en la manufactura.
Uno de los sectores estratégicos incorpora nuevos materiales para el desarrollo de productos. En este orden de ideas, indicadores como son la resistencia, el rendimiento, la rigidez y la densidad de los nuevos materiales son desarrollados para lograr excelentes propiedades mecánicas, facilidad de manufactura y productividad. Por ello, los materiales compuestos, como la matriz polímeros (MCMP), son considerados una alternativa viable y real para la fabricación en la industria automotriz.
El sector automotriz es uno de los sectores en que la implementación actual de MCMP ha dejado de ser una opción para convertirse en una realidad, gracias a que esta permite aligerar el peso del vehículo, dando como resultado el menor consumo de combustible vs. los kilómetros a recorrer (autonomía), o la mayor cantidad de carga posible a transportar bajo el mismo consumo.
Lo anterior genera un reto de diseño debido a que, en primera instancia, los materiales poliméricos no se comportan en principio de la misma manera que los materiales metálicos, esencialmente cuando sus condiciones de trabajo están por encima de su temperatura de transición vítrea (Tg).
Además, el desarrollo de la informática para el campo de la ingeniería mecánica ha permitido a la humanidad potenciar el análisis en la ingeniería, procurando ambientes simulados con un ambiente y resultados similares a los esperados en pruebas destructivas o métodos analíticos tradicionales. A esta estrategia se le ha denominado método por elementos finitos (MEF, o mejor conocidos como Computer Aided Design y Computer Aided Engineering CAD-CAE), el cual permiten mejores diseños y procesos de manufactura.
Por un lado, los materiales denominados tradicionales son esencialmente los metales ferrosos y no ferrosos, que son objeto de estudio convencional desde hace varias décadas, especialmente desde la primera revolución industrial. Por otra parte, los polímeros se han tomado como objeto de estudio en las recientes décadas, aproximadamente desde los años 50 y los MCMP desde los años 90, conllevando esto a que el conocimiento generado en cuanto a las formas de falla de los primeros permiten ser confiables para su uso en los procesos de manufactura actuales, es decir las pruebas mecánicas a las que se someten los polímeros confirman que no fallarán en el trabajo ordinario que realizan los diversos productos.
En este caso, una empresa solicitó un estudio de CAD-CAE y su validación con probetas destructivas para confiar en los materiales polímeros que ellos utilizan en diversas partes del proceso de ensamble y manufactura que se caracterizan por la unión de láminas de material de matriz polímero (resina poliéster/fibra de vidrio), por medio de una unión metálica no removible (remache) con concentrador de esfuerzos (orificio).
Antecedentes
El uso de estos materiales compuestos, junto con refuerzos estructurales fabricados en materiales convencionales, mejora significativamente la funcionalidad de los diseños que comúnmente se utilizan (Fiore, Calabrese, Scalici, Bruzzaniti & Valenza, 2018).
El uso de nuevos materiales genera retos en el diseño de piezas, de ensambles y de funciones de servicio debido a que muchas aplicaciones conllevan incertidumbre o derivan en nuevas formas de ruptura, en comparación con los materiales convencionales. En el caso de los materiales compuestos laminados, una de las formas de rotura más habituales es la delaminación1.
Una falla es el colapso final de la una unión debido a la resistencia de los materiales, ya sean convencionales o compuestos. Los compuestos dependen en gran medida de la forma en la que están orientadas las láminas o del promedio de las fibras que los componen, esto aunado a que es común colocar capas en diferentes niveles con orientaciones particulares, generando en principio incertidumbre sobre cómo se desarrolla la transferencia de los esfuerzos al interior del componente, el cual depende del número de capas, la orientación de cada una de ellas y al espesor del laminado.
El problema de investigación es, por lo tanto, predecir la vida útil de los materiales compuestos. El estudio de los mecanismos de falla y su desarrollo, precisos y universales, deben predecir el máximo de resistencia de los laminados compuestos, particularmente bajo cargas triaxiales, especificado por Borba, Blaga, dos Santos & Amancio-Filho (2018).
Investigadores como Wan, Yang, Ismail & Sheng (2018) se han encaminado en determinar los criterios de falla para estos materiales, de los cuales algunos de ellos han sido implementados en paquetes de software de elementos finitos, como el criterio de falla Hashin (implementado dentro de la programación del software ABAQUS) y el criterio de falla Tsai-Wu (implementado en el software ANSYS).
Un fabricante de autobuses, dentro de sus procesos de mejoramiento continuo, aportó un caso de estudio real (Figura 1) donde se presenta un modelo de montaje en la unión del techo y el frente de un vehículo automotor de pasajeros (ambas a partir de materiales laminados compuestos, resina poliéster/fibra de vidrio). La estructura del vehículo es de acero de bajo carbono, con unión pernada (remache metálico), reforzada con adhesivo (entre las paredes de los laminados) y con cinta en la parte exterior como refuerzo, la cual está sometida a diferentes tipos de esfuerzo a partir de la vida útil y de servicio del vehículo automotor.
En este orden de ideas, el objetivo del estudio es simular el comportamiento de uniones mecánicas en materiales compuestos para un autobús, de manera que se pueda mostrar su comportamiento debido a las cargas externas incidentes sobre la unión, utilizando el análisis por elementos finitos y comparando los resultados contra probetas para ensayos mecánicos a tensión con un error menor al 3%.
Metodología
Este caso de estudio empezó caracterizando mecánicamente a tensión el material laminado sin concentrador de esfuerzos (Figura 2b) y con concentrador de esfuerzos (Figura 2a), según las normas ASTM D3039 y ASTM D5766.

Fuente: Elaboración propia.
Figura 2 Probetas ASTM D5766 (a) y ASTM D3039 (b) en máquina de ensayos a tensión.
La norma ASTM D3039 aclara el método de prueba que determina las propiedades de tracción en el plano de los materiales compuestos de matriz polimérica reforzados por fibras de alto módulo2. Las formas de material compuesto se limitan a fibras continuas o materiales compuestos discontinuos reforzados con fibras en las que el laminado es equilibrado y simétrico con respecto a la dirección de prueba. Este método de prueba está diseñado para producir propiedades de tracción (American Society for Testing and Materials [ASTM], 2017).
La norma ASTM D5766 aclara el método de prueba para determinar la resistencia a la tracción de orificios abiertos de los laminados compuestos de matriz polimérica multidireccional reforzados por fibras de alto módulo. Las formas de material compuesto se limitan a materiales compuestos reforzados con fibras continuas o fibras discontinuas (cinta o tela, o ambas) donde la densidad relativa de los plásticos por desplazamiento cobra importancia (ASTM D883), así como la terminología relativa a los plásticos (ASTM D2584), el método de prueba para la pérdida de ignición de resinas reforzadas curadas (ASTM D2734) y los métodos de prueba para contenido vacío de plásticos reforzados (ASTM D3039/ASTM D3039M) (ASTM, 2011).
Para realizar los ensayos mecánicos se utilizó la maquina universal de ensayos electromecánica del centro de materiales y ensayos del Servicio Nacional de Aprendizaje (Sena), marca BESMAK BMT, referencia E Series Servo, con una capacidad de 2 kN hasta 500 kN y con un control de la velocidad de desplazamiento de 0.001 mm/min-300 mm/min.
La materia prima que se empleó fue la fibra de vidrio extraída del techo de un autobús proporcionado por un fabricante de autobuses, el cual no se ensambló y se cortó en la misma parte del empalme de la unión bajo las condiciones ambientales que se encontraban en la planta. Se utilizó fibra de vidrio cortada matt 180 (laminación manual) con 450 g/m², fabricada con vidrio del tipo E, con un aglutinante soluble en monómero de estireno compatible con resina poliéster.
Para las probetas de uniones se realizaron dos variaciones del modelo del autobús con los materiales en la planta, realizando así probetas de ensayo destructivo de uniones no permanentes de tres tipos: unión adhesiva, unión remachada y unión mixta, con dimensiones de 250 mm × 25 mm × 2.5 mm. Estas usaron el mismo material de la fibra de vidrio; además, la fábrica aseguró que las uniones se realizaran sobre la línea de montaje de uno de sus autobuses donde el operario extendió el uso del taladro para remaches de aluminio de 4.8 mm y realizó la preparación de la superficie y la aplicación de los adhesivos como sugiere el fabricante, como si se tratara de un autobús de producción.
El remache es sólido de aluminio. El adhesivo para las probetas utilizado es para una resistencia a la cortadura por tracción de 2.0 N/mm2. Se determinaron las propiedades mecánicas a tracción tales como el módulo elástico, esfuerzo y deformación máximos mediante la norma ASTM D3039, en la cual se empleó una velocidad de ensayo de 2 mm/min y probetas de 250 mm × 25 mm × 2.5 mm. Para la norma ASTM D5766 se emplearon probetas de 280 mm × 30 mm × 2.5 mm.
La formulación de las pruebas ASTM D3039 y ASTM D5766 son diferentes pruebas normalizadas para ensayos destructivos en fibras de vidrio. Dichas pruebas son necesarias para la comprobación del error. La importancia no solo es probar que el método de ensamble cumple con la normatividad que se realiza sistemáticamente para cumplir con el sistema de calidad, sino también son importantes los resultados de las pruebas que se desean evaluar por métodos matemáticos de elemento finito y así validar virtualmente para rediseño de ensambles en carrocerías de autobuses. Es decir, la validación de la simulación permitirá la mejora continua del ensamble y reducirá no solo la probabilidad de falla de un ensamble sino también costos y métodos.
En otras palabras, en caso de que el método de elemento finito no arroje los valores esperados con una cercanía a los valores obtenidos por pruebas reales en probetas, no podrá ser una herramienta para la mejora continua en el proceso de ensamble deseado y, por lo tanto, no se reducirán los costos por mejora continua. Por otro lado, en caso de que los resultados de la simulación sean similares a las probetas, en consecuencia, se tendrá confiablidad de mejora continua y se reducirá la cantidad de probetas necesarias para comprobación de resultados simulados. Es así como la veracidad de este estudio se certifica al tomar en cuenta varias probetas sujetas a pruebas normalizadas ASTM.
El objetivo principal de la simulación es encontrar un margen de error controlable y confiable entre la realidad y la simulación. El hecho de que se tengan diferentes pruebas normalizadas no afecta los márgenes de error. Dicho de otro modo, cada prueba normalizada ASTM tiene su propia aproximación simulada por elementos finitos, lo que permite asegurar que los resultados obtenidos por elementos finitos sean viables y confiables.
Tabla 1 Tabla resumen de probetas previas ensayos a tensión.
Espécimen | Espesor [mm] | Anchura [mm] | Probeta | |
PROBETA FIBRA DE VIDRIO NORMA ASTM |
ASTM D3032 | 2.50 | 25.00 | A2; A3 A4; A5 |
ASTM D5766 con agujero |
2.80 | 30.00 | B2; B3 B4; B5 | |
UNIÓN FIBRA DE VIDRIO | REMACHE | 2.70 | 31.00 | C2 |
2.50 | 31.00 | C3 | ||
2.50 | 31.00 | C4 | ||
2.50 | 31.00 | C5 | ||
MIXTA REMACHE Y ADHESIVO |
3.20 | 29.30 | D2 | |
2.80 | 30.00 | D3 | ||
2.80 | 30.00 | D4 | ||
3.20 | 28.20 | D5 | ||
ADHESIVO | 3.50 | 29.00 | E2 | |
3.50 | 31.30 | E3 | ||
3.30 | 24.00 | E4 | ||
3.30 | 30.10 | E5 |
Fuente: Elaboración propia con datos proporcionados por el Sena.
El espécimen 1 de cada grupo se utilizó como referencia para la calibración de la máquina y posterior ensayo de cada uno de los grupos de probetas. A partir de los ensayos mecánicos se realizó un análisis estático estructural de elementos finitos en un software; este modelo virtual posee tres etapas: preprocesamiento, procesamiento y proceso. El preprocesamiento consta de dos partes:
Definición de objetivos de simulación. Acotación de componente de estudio, localizando una zona altamente comprometida o zonas de bajo compromiso, según el interés a evaluar de la resistencia estática o en eliminación o adición de componentes.
Creación del modelo virtual. Para empezar, es necesario cargar una geometría para delimitar las condiciones de frontera, migrándola de software o partiendo desde geometrías en el mismo. Este paso puede intervenir negativamente en los resultados. Para este caso, la creación del modelo virtual se realizó en dos pasos:
Creación de diseño asistido por computadora-ingeniería asistida por computadora (CAD-CAE, por sus siglas en inglés). Se modela la unión entendiendo que lo que se requiere estudiar es la unión del autobús. Se acotó la figura como antes se había descrito para así obtener las condiciones de frontera en el modelo, reduciendo de manera significativa la unión, de tal forma que la unión sea un simple sándwich (Figura 3).
Depuración de geometrías. Para realizar el análisis de elementos finitos migrando la geometría de otro software computacional, es necesario realizar una simplificación del modelo depurando la geometría. En el caso particular de los remaches, la librería del software 3D genera los modelos lo más semejante posible a la realidad. Pero para que el mallado del modelo se realice en condiciones óptimas se simplifican algunas curvaturas, como redondeos, para que los elementos cumplan con la debida ortogonalidad y asimetría u oblicuidad (Figura 4).
Mallado del dominio computacional. Al arrancar el mallado del dominio, es importante tener en cuenta que este influye en la solución de los modelos; de esta manera, el definir la precisión de la aproximación realizada en una malla es el punto de partida, ya que cuanto más refinada se encuentre la malla, se consigue, en general, una solución más exacta. Para esto es importante definir específicamente la malla y los contactos del modelo. Para la definición de la configuración global de malla se procedió estableciendo el dimensionamiento. Se especificaron las funciones de tamaño, curvatura, proximidad, tamaños de malla, tasa de crecimiento, etc., dejando inicialmente la función de curvatura activada y los valores por defecto para que los parámetros sean modificados cuando se realicen los refinamientos.
Análisis de las herramientas de contacto con las conexiones más simples en el modelo usando la herramienta de contactos. Para validar la penetración en los contactos se realizaron las verificaciones iniciales.
Configuración de la simulación. La configuración de la simulación integra datos específicos al modelo, dando pie a una aproximación exacta cuando se tienen en cuenta datos importantes como:
Definir el material y sus propiedades. Se seleccionaron cada uno de los materiales utilizados usando sus propiedades mecánicas obtenidas por las gráficas y las entregadas por los proveedores de cada uno de los materiales y llamando cada una de sus librerías para realizar el respectivo análisis.
Condiciones de frontera según modelo físico. Muchos trabajos de diseño necesitan una representación adecuada del problema, lo cual es usualmente estudiado en forma separada, ya que la complejidad en los diseños de cualquier elemento puede aumentar exponencialmente con relación a parámetros no controlables. La acotación del problema en este punto resulta crucial para el éxito del método de diseño elegido, debido a que gracias a esto se obtienen traslados de cargas o simplificación de modelos para los posteriores análisis.
Configuración de procesos a resolver. Los elementos a resolver con el método de elementos finitos son los contrastes de las propiedades mecánicas a tracción tales como el módulo elástico, esfuerzo máximo y deformación máxima, para así analizarlos con los ensayos destructivos.
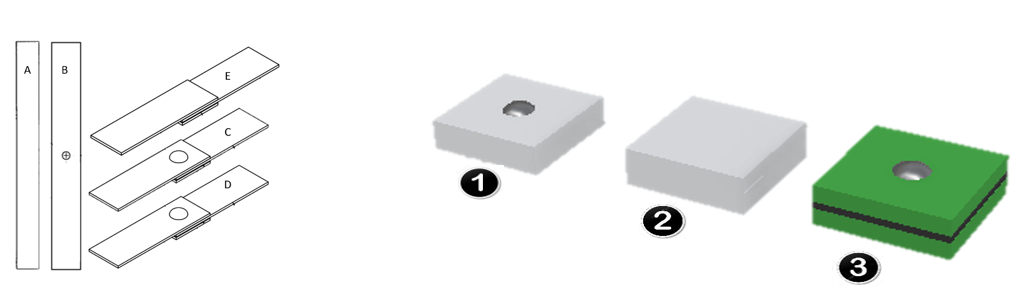
Fuente: Elaboración Propia.
Figura 3 Diferencia de grupos de probetas según tipo, previo ensayo y modelos susceptibles a analizarse con elementos finitos.
En el programa, la convergencia se controla con el cambio de incremento del desplazamiento nodal, el cambio de fuerzas fuera de equilibrio e incluso el cambio de energía interna. El último criterio da una idea de cómo ambos desplazamientos y fuerzas se acercan a sus valores de equilibrio.
Resultados de ensayos de tracción
Los siguientes son los resultados entregados por el Sena, y se muestran los módulos elásticos a tracción de las diferentes pruebas que se realizaron contra su posición.
Se puede observar en la Figura 7 que con las probetas controladas con la norma la gráfica esfuerzo deformación se comporta de manera similar. El comportamiento mecánico del material con un concentrador de esfuerzos para cada ensayo y el efecto del concentrador mostraron que esta probeta (Figura 7) tiene un primer pico que puede ser un efecto deslizante de la unión o que la misma probeta se desfibró, pero está presente en todas las probetas.

Fuente: Elaboración propia.
Figura 5 Mallado inicial generado por ANSYS. Condiciones de frontera aplicando la carga externa para el análisis y la carga en el interior de los agujeros.

Fuente: Elaboración propia.
Figura 7 Ensayos a tensión, fibra de vidrio normas ASTM D3039 y ASTM D5766.
La primera unión en la Figura 8 presenta una disminución importante en los esfuerzos para el ensayo y el efecto del concentrador con el remache.
En este ensayo se observó que esta unión mostrada en la Figura 9 tiene las resistencias más altas, ya que presentó en todas las probetas un aumento del módulo elástico y un esfuerzo máximo conforme se incrementó la unión con el adhesivo y el remache, como se esperaba por la unión mixta.
En cuanto al último ensayo con la unión adhesiva, en la Figura 10 se presentan los esfuerzos más bajos, como era de esperar por esta unión no permanente, pues la unión adhesiva presenta ventajas en otros aspectos, como la elongación previa a la rotura de la falla.
En la Tabla 2 se presentan los valores medios encontrados de deformación para las probetas. Se observa que la mayor deformación fue la alcanzada por la unión adhesiva y se muestran los módulos de elasticidad, la elongación con la fuerza máxima y el esfuerzo último alcanzado por las mismas.
Tabla 2 Comportamiento mecánico de las probetas.
Probeta | Ensayo Tensión FUERZA [N] |
Esfuerzo [MPa] |
Elongación [mm] FUERZA MAX |
LONGITUD INICIAL 250 mm Deformación Unitaria [mm/mm] |
Módulo Young [MPa] |
A2 | 5593.10 | 89.49 | 3 941 132.00 | 1.58% | 5676.64 |
A3 | 6255.40 | 100.09 | 4 436 275.00 | 1.77% | 5640.23 |
A4 | 7362.30 | 117.80 | 5 078 927.00 | 2.03% | 5798.31 |
A5 | 8900.70 | 142.41 | 6 203 927.00 | 2.48% | 5738.75 |
B2 | 6721.20 | 80.01 | 4 128 463.00 | 1.65% | 4845.28 |
B3 | 4356.70 | 51.87 | 2 955 659.00 | 1.18% | 4386.96 |
B4 | 6647.00 | 79.13 | 3 781 461.00 | 1.51% | 5231.51 |
B5 | 4794.00 | 57.07 | 3 295 946.00 | 1.32% | 4328.91 |
C2 | 1446.10 | 17.28 | 2 938 640.00 | 1.18% | 1469.83 |
C3 | 1184.60 | 15.29 | 2 465 963.00 | 0.99% | 1549.61 |
C4 | 1340.20 | 17.29 | 2 719 975.00 | 1.09% | 1589.44 |
C5 | 1646.40 | 21.24 | 2 492 145.00 | 1.00% | 2131.08 |
D2 | 2653.70 | 28.30 | 1 941 976.00 | 0.78% | 3643.60 |
D3 | 2970.20 | 35.36 | 3 847 128.00 | 1.54% | 2297.79 |
D4 | 2869.20 | 34.16 | 2 486 149.00 | 0.99% | 3434.74 |
D5 | 2523.30 | 27.96 | 2 151 351.00 | 0.86% | 3249.37 |
E2 | 1229.10 | 12.11 | 9 129 054.00 | 3.65% | 331.62 |
E3 | 1440.50 | 13.15 | 8 801 225.00 | 3.52% | 373.51 |
E4 | 1114.20 | 14.07 | 6 493 581.00 | 2.60% | 541.62 |
E5 | 1176.00 | 11.84 | 6 329 265.00 | 2.53% | 467.64 |
Fuente: Elaboración propia con base en los datos analizados de resultados de ensayos.
Resultados de post-procesamiento CAD-CAE
En el caso del análisis CAD-CAE se muestran los resultados de post-procesamiento, los cuales implican el refinamiento de mallado del dominio computacional, el análisis de las herramientas de contacto con las conexiones y la convergencia de la independencia de la malla.
1. Refinamiento de mallado del dominio computacional. Determinación de tipos de elementos y calidad de la malla, ortogonalidad y oblicuidad de los elementos.
Se comienza a analizar la calidad de una malla por dos criterios grandes y simples para cualquier estudio. El primer criterio que se revisó fue el de ortogonalidad, que nos dice que una malla ortogonal es una generalización de la noción geométrica de perpendicularidad, haciendo que los esfuerzos se transmitan de una buena manera para este criterio. Se dice que una ortogonalidad es buena si se encuentra entre el rango de 0.69 a 1. El segundo criterio que se revisó fue el de la asimetría u oblicuidad, que es una propiedad de determinados cuerpos en los que surge una discordia cuando no somos capaces de reconocer qué parte es la original de la asimetría y, por ende, no son iguales en todos sus lados. Para este criterio, una asimetría aceptable se encuentra entre los valores de 0 a 0.25 al añadir controles de malla.
2. Análisis de las herramientas de contacto con las conexiones más reales. Este análisis se lleva a cabo haciendo uso de la herramienta de contacto cuyo objetivo es ver el estado inicial y los estados posteriores al refinamiento de la malla, pues el procesamiento inicial puede no contemplar los contactos reales. De esta manera, comprender los tipos de contacto en el ensamble es primordial para un eficiente análisis, observando a detalle para realizar un diagnóstico adecuado cuando surjan problemas de convergencia con los mismos.
3. Convergencia de la independencia de la malla. Este proceso está parcialmente automatizado para modelos basados en CAD, con generación automática de mallas y solo para el tipo de análisis de tensión estática con modelos de material lineal, pero no es el mejor.
Para iniciar, se utiliza la primera malla generada con el menor número de elementos que sea razonable y se analiza el modelo. Se vuelve a crear la malla con una distribución de elementos más densa y se vuelve a analizar el modelo comparando los resultados con los de la malla anterior. Se continúa incrementando la densidad de la malla y nuevamente se analiza el modelo hasta que los resultados converjan satisfactoriamente. Este tipo de estudio de convergencia de malla permite obtener una solución precisa con una malla que sea lo suficientemente densa, pero que no demande una cantidad excesiva de recursos de procesamiento.
Para modificar la densidad de una malla de elementos finitos se pueden utilizar distintas características, pero para esta malla generada a mano se recurrió a la geometría de estructura alámbrica sin malla y se modificó el número de divisiones, también recurriendo a una mejora de la malla superficial. Al comparar una versión del modelo con otra, se consultan los valores resultantes en la misma ubicación para cada variante (por ejemplo, el punto medio de un arco o una arista o, bien, el centro de una superficie), en este caso el esfuerzo Von Mises.
4. Determinación por elementos finitos de propiedades de probetas. Para determinar laspropiedades de las probetas se usó la fuerza máxima de cada uno de los ensayos, realizando el refinamiento de malla para reducir el error y la convergencia de malla con el esfuerzo equivalente en cada uno de los ensayos, hasta que el error cayera por debajo del 3%, extrayendo así cada uno de los ensayos como se muestra a continuación.
En la Figura 11 se evidencia la aplicación de condiciones de frontera, donde la carga máxima del ensayo mecánico de la probeta del grupo A (norma ASTM D3039) se aplica sobre el área B de 7027.9 N. Como se muestra en la figura, además se insertó un soporte fijo como condición de frontera sobre el área A para poder analizar el modelo.

Fuente: Elaboración propia.
Figura 11 Aplicación de cargas, esfuerzo y deformación de probeta (ASTM D3039).
La Figura 11 muestra el esfuerzo equivalente sobre la probeta. La escala de colores evidencia el esfuerzo máximo que se produce cerca del borde del soporte pero con una zona crítica de la zona central, con un valor máximo de 114.84 Mpa y un mínimo de 88.429 Mpa. La Figura 11 tiene la escala de colores del último resultado de este primer grupo. La deformación máxima alcanza alrededor de 5 mm, esta se produce a lo largo de la probeta.
Sobre el modelo de la probeta del ensayo del grupo B (norma ASTM D5766) se aplica en el área B, como lo muestra el modelo en la Figura 12, donde la carga máxima correspondiente es de 5629.7 N en el área A.

Fuente: Elaboración propia.
Figura 12 Aplicación de cargas, esfuerzo y deformación probeta (ASTM D5766).
La Figura 12 muestra el esfuerzo equivalente sobre la probeta. Este se encuentra en el concentrador de esfuerzos, pero con una zona crítica en el agujero, con un valor máximo de alrededor de 66 Mpa y un mínimo de 11 Mpa. La última de este grupo fue la deformación total y, como lo muestra la Figura 12, este modelo alcanzó un valor máximo de 3.52 mm.
Para comenzar, con el grupo de uniones se realizaron dos análisis. El primero de estos se realizó aplicando las cargas sobre el agujero del remache. El más aproximado de este análisis fue en el que se consideró que las cargas fueran aplicadas en las áreas laterales de la probeta de 1404.3 N sobre el área B en la Figura 13 y el soporte en el área A en la misma.

Fuente: Elaboración propia.
Figura 13 Aplicación de cargas, esfuerzo equivalente y deformación de probeta, grupo C.
En la Figura 13 se observa el esfuerzo equivalente del modelo de la unión. La escala de colores evidencia que el esfuerzo máximo se produce no como el aplastamiento en la zona externa de la probeta sino en el agujero del remache. El esfuerzo crítico en la zona interna tiene un valor máximo de alrededor de 25 Mpa. La deformación del modelo de la unión alcanza un valor máximo cercano a los 3 mm (Figura 13).
Al aplicar las cargas en el grupo de probetas D, se tuvo en cuenta la misma consideración del grupo C, aplicando las cargas externamente y usando la fuerza del ensayo mecánico de 2754.1 N, como se muestra en el área B de la Figura 14, aplicando además el soporte fijo en el área A en la misma figura de azul.
La Tabla 3 muestra los datos conglomerados, resultado del análisis de elementos finitos de los modelos virtuales de cada una de las probetas analizadas en cada grupo.
Tabla 3 Datos de las probetas por el método de elementos finitos.
Elementos Finitos | |||
Grupo | Ensayo Tensión FUERZA [N] |
Esfuerzo [MPa] |
Elongación [mm] FUERZA MAX |
A | 7027.88 | 114.84 | 4 996 000 |
B | 5629.73 | 65.93 | 3 525 100 |
C | 1404.33 | 18.31 | 2 734 800 |
D | 2754.10 | 32.29 | 2 629 900 |
E | 1239.95 | 12.60 | 7 519 400 |
Fuente: Elaboración propia con datos analizados de resultados elementos finitos.
La Tabla 4 muestra la lista de error en los resultados de las probetas de ensayo mecánico contra los modelos virtuales. Para el cálculo de este error experimental porcentual se utilizó la siguiente fórmula:
Discusión
En los ensayos, llama la atención el aumento significativo de esfuerzo en las uniones mixtas, pues se duplica el esfuerzo con respecto a las otras uniones. En ausencia de un tipo de unión con el otro prevalece su característica más fuerte, como es el caso de la deformación en el adhesivo. Al respecto, se destacan dos hechos que sin duda impactan en la derivación del aumento de los esfuerzos con otros métodos de unión no permanente. El primero es la debida preparación de superficie, que en la gran mayoría de los casos concluyó en la forma satisfactoria de adhesión de los elementos constituyentes. En segundo lugar, el uso del remache es importante que no reduzca la geometría del cordón de adhesivo recomendada para obtener una buena adhesión (Arenas, Guillamón, González & Sebastián, 2002). En los casos en que el adhesivo se mostró significativamente reducido, este redujo su esfuerzo. Según ello, es posible que exista un aumento real en los casos en que el adhesivo se combina con los remaches, aunque si el adhesivo cumple con los parámetros de esfuerzo, este presentaría una ventaja significativa con respecto a la unión simplemente remachada o adherida
Las propiedades mecánicas presentadas por el método de elementos finitos permiten variar las formas de análisis y comprobar la mejor forma de una unión, pues se compararon con las propiedades de los ensayos mecánicos. La unión mixta de material compuesto presentó excelentes propiedades, incluso por encima de las exhibidas por las otras uniones. Así, el comparar la unión mixta con otro modelo de uniones o con otro tipo de configuración de unión hace de este un punto de partida para diferentes estudios y conceptos en la unión de compuestos, pues estos alcanzaron una resistencia a la tracción importante. Cabe señalar la desviación estándar de los ensayos, pues estos fueron la comprobación de los modelos que constituyen una reducción de las fallas y costos de las uniones.
Conclusiones
Los modelos por elementos finitos se validaron de una manera correcta con los ensayos, comprobando que el error entre los dos métodos es inferior al 3% en los resultados; además, los ensayos se comportaron dentro de lo que se esperaba.
La caracterización mecánica mostró que las probetas demostraron efectos similares en las propiedades mecánicas del material, con incrementos del módulo elástico, resistencia y deformación unitaria al cambiar el tipo de unión, como era de esperarse, y su forma de rotura.
Para el caso de las uniones, en cuanto al módulo elástico, la mejor formulación de unión fue la configuración mixta. Esta logró combinar características deseables en la unión no permanente, tales como las buenas propiedades mecánicas y las más bajas deformaciones unitarias.
En la configuración de la unión adhesiva, el módulo elástico y esfuerzo máximo a la tracción fueron los más bajos. Con respecto a la deformación unitaria en ambos ensayos, el incremento de la deformación fue notable, haciendo de esta la unión no permanente con mayor deformación.
Con relación a la falla de las probetas, estas sucedieron según lo esperado. La unión no permanente falló por el remache o la unión adhesiva, según fue el caso; además, también se evidenció que las probetas que fueron realizadas según la norma y que fallaron de una manera esperada arrojaron valores que facilitaron el análisis de rotura por el concentrador de esfuerzos en el caso de la probeta de la norma ASTM D5766.
El postproceso de los elementos finitos reveló la aproximación al conglomerado de resultados. Sin embargo, al compararlo con el ensayo mecánico, el proceso de refinamiento y convergencia requirió de un análisis a profundidad del ensayo. Adicionalmente, se aumentó el recurso computacional para el análisis, por lo cual es recomendable utilizar el ensayo mecánico, pero la economía del modelo de elementos finitos lo hace un modelo viable.
Sería recomendable profundizar el estudio de este tipo de uniones no permanentes con compuestos, realizando ensayos de resistencia al desgaste. Además, se podrían analizar los ensayos considerando los diferentes tipos de falla, como el claro ejemplo de laminación en los materiales compuestos, aunque este no sea el caso para las uniones no permanentes.