El establecimiento de conquistadores, colonizadores y gobernantes en la Nueva España trajo consigo demanda de diversos productos acordes a su estilo de vida peninsular, para ello se adiestró a indígenas en la fabricación de algunos de ellos, otros fueron generados por artesanos migrantes o bien importados de ultramar. Estas condiciones promovieron actividades artesanales e industriales en las que se manifestaba el fundamento de los aspectos de producción, habilidad manual y nivel tecnológico alcanzado. Algunos artículos elaborados localmente con diversos materiales pasaron a formar parte del ajuar doméstico de acaudalados comerciantes, gobernantes y de los principales espacios dedicados al culto religioso, ante los detalles excelsos logrados.
La manufactura de artículos de vidrio se instauró en la ciudad de México ante la necesidad de fabricar vasijas denominadas “cornamuzas” empleadas en la separación de metales, el importarlas implicaba riesgo por su fragilidad y alto costo de inversión, lo que determinó la incorporación de vidrieros a la actividad metalúrgica1. Estos artífices diversificaron su quehacer hacia la elaboración de diferentes recipientes y envases demandados por boticarios y médicos2, así como otros artículos de uso exclusivo de la aristocracia como candiles, lentes para anteojos, espejos y otros más3.
El grupo de vidrieros en de esta ciudad, reducido en comparación con otros conjuntos de artesanos, era de 115 entre los años de 1566 y 1790; hasta este momento no ha sido posible precisar la existencia de su gremio. La zona que habitaban correspondía a la periferia del oriente de la capital, donde se encontraban dos de tres sitios de producción vidriera con capacidad reducida de fabricación y el restante con infraestructura industrial y económica para que fuera continua, sistemática y considerable4. Es de suponerse que estos menestrales pudieron estar vinculados con loceros por la semejanza del material empleado, hornos de producción, proximidad de sus instalaciones y por la existencia del nombramiento de Maestro de Mayor de vidrio y loza fina de un artífice que laboraba en la ciudad de Puebla5, aunque este nombramiento no ha sido reconocido en maestros vidrieros de la ciudad de México. Por otra parte aunque los sitios de manufactura de loza se encontraban al oriente de la ciudad6, los de vidrio estaban retirados de ellos, lo único que compartían loceros y vidrieros era la pobreza, puesto que el salario bajo solo les permitía vivir en condiciones de penuria en la zona referida.
La materia prima empleada por ambos artesanos contenía el elemento químico de silicio que junto con la plata, cobre, plomo, zinc, fierro, níquel, sodio, potasio y otros metales conformaban la arcilla, pedrusco de rocas sedimentaria e ígnea, las primeras localizadas a orillas de ríos y lagos, valles y fondos de barrancas, y las segundas ubicadas debajo de la corteza terrestre. La mayor o menor cantidad de silicio mezclado con otros minerales del material pétreo determinaba el color de la argamasa empleada para la cerámica a configurarse mediante el torno y en frío, para el caso del vidrio, se moldeaba a base de calor y era imprescindible el sodio, potasio y calcio. La materia prima para ambos tipos debió extraerse muy probablemente de diferente sitio lo que determinaba la proporción y tipos de minerales que condicionaba las características físicas de opacidad, transparencia, porosidad, color, resistencia, peso y otras más, según fuera cerámica o vidrio. El proceso de purificación de los componentes químicos y la temperatura necesaria para la fusión de la materia vítrea diferían a los requeridos para la loza, mayólica y porcelana.
Artículos de vidrio eran importados a la ciudad de México de la península ibérica y países centroeuropeos aún de la presencia de vidrieros locales y extranjeros. Existen evidencias de que a partir del segundo periodo del siglo XVIII provenían de la Real Fábrica de Cristales de la Granja de San Ildefonso7 y de la ciudad de Bohemia, ésta importaba sus productos hacia España a partir de la segunda mitad del siglo XVII, todos embarcados en el puerto de Cádiz por comerciantes españoles independientes para distribuirlas en ciudades del nuevo continente8.
Los objetos del material referido fueran de ornato o uso hogareño tenían alto costo económico por lo que formaban parte del ajuar doméstico del estrato social novohispano con capacidad de adquisición, no obstante piezas manufacturadas localmente con diferente calidad, terminado y patrones de forma semejantes a los provenientes del exterior, pasaron a formar parte lentamente de la vida doméstica cotidiana del resto de la sociedad novohispana como puede apreciarse en representaciones pictóricas del siglo XVIII además de piezas integras y fragmentos recuperados de rescates arqueológicos. El reconocimiento de las propiedades físicas y químicas del vidrio favorecieron su uso en otras actividades importantes9.
Ante la existencia reducida y dispersa de la información concerniente al proceso de fabricación del vidrio en la ciudad de México durante la época virreinal, el presente documento tiene como propósito presentar un mecanismo explicativo de esta actividad a partir del análisis de las características que debió reunir la materia prima y del proceso implicado para obtener sus cualidades de calidad así como de las instalaciones físicas singulares mediante las que se lograba la integración química de la masa vítrea y además de los utensilios específicos que empleaba el diestro artesano. Asimismo esta reflexión permite comprender las implicaciones económicas que conllevaba la instalación de la actividad productiva y como todo ello influyó para que no se desarrollara como otras labores artesanales en la época referida.
Materia Prima
Los vidrieros consideraban como elementos relevantes a la arena (procedente de lechos de ríos), sal vegetal y diversos minerales presentes en el material pétreo, aunque carecían del pleno conocimiento de la esencia química que determinaba las funciones de cada uno de ellos. Este saber se mantuvo en forma reservada así como las proporciones y pureza de los constituyentes de la materia prima y del proceso requerido para integrarlos, erudición lograda a través del tiempo que condujo a obtener objetos de calidad.
La arcilla (integrante de algunos tipos de arena) era la fuente de sílice y conformaba la mayor parte de la materia vítrea; facilitaba la cohesión del resto de integrantes y otorgaba resistencia mecánica. Los artesanos apreciaban la de coloración blanca por carecer de otros minerales que alteraban la coloración del vidrio, de lo contrario condicionaba mayor requerimiento de temperatura para la fusión, lo que demandaba más leña y generaba deterioro prematuro de los hornos. Para evitar lo anterior se dieron a la tarea de reconocer sitios específicos de obtención en el territorio virreinal o pagaban para que fuera de calidad10.
El proceso al que se sometía la arcilla fue el lavado inicial a fin de reducir impurezas, una de las razones por la que los sitios de producción hasta ahora localizados en la ciudad de México, se ubicaban adjuntos a acequias. A continuación se realizaba la pulverización mediante molino y su cernido para obtener partículas de tamaño reducido lo que facilitaba la reactividad entre los constituyentes de la materia referida por ello se considera que muy probablemente los sitios mineros trituraban y proporcionaban este material.
El componente considerado fundamental fue la “sal” de tipo sódico con función de fundente y que se obtenía del vegetal denominado “barrilla”, término genérico y popular, aunque por sus particularidades se le llamó “barrilla fina”. Se identificaba por su color, sabor y olor una vez obtenida11; variedades de este vegetal diferían en el aporte cuantitativo y cualitativo de los compuestos químicos por lo que en ocasiones se usaban propositivamente, aunque la calidad del vidrio disminuía o bien sustituían a la de tipo fino con el fin de estafar12.
La referencia más antigua de la época colonial que expresa el uso de esta planta para la elaboración de vidrio es la que aparece en el libro de José Corona Núñez de 1579 titulado “Relaciones geográficas de la Diócesis de Michoacán, 1579-1580”, en él se manifiesta que: “se cria gran suma de yerba de que se age el vidrio que los naturales llaman curiraxaqua: vienen los que hagen vidro de la ciudad de Mexico a cojella y la lleban en panes”13. Específicamente el término de barrilla y su uso aparece en la ordenanza de 1596 que resalta su importancia ya que con ella se superaba la calidad de las piezas de vidrio producidas hasta ese momento. Asimismo, indica la penalización por no proporcionarla a los vidrieros o la apropiación de gran volumen para controlar el precio de venta14, práctica monopólica suscitada también en España, por ello el establecimiento de disposiciones para preservar la planta referida15 conocida en diferentes puntos del continente americano16.
Precisar el tipo de barrilla dentro del reino vegetal llevó varios siglos, pues se le daba este término generalizado a toda aquella planta que proporcionaba sal con la que se fabricaba vidrio, jabón, agente blanqueante de textiles y em-pleada para cauterizar heridas17. Los vegetales a partir de los que se pudo obtener componentes sódicos ésta materia prima fueron varias, actualmente se han identificado tan solo 23 géneros de la familia de quenopodiácea, entre ellos el de Halogetum sativus de quien se extraía la mayor cantidad de sodio, por lo que los artesanos se referían a la “barrilla fina”18. El Cuadro núm. 1 muestra los términos comunes de algunas plantas barrilleras que pudieron utilizarse en el siglo XVIII.
CUADRO 1 DIVERSAS PLANTAS BARRILLERAS
NOMBRE COMÚN | PAÍS |
borde o espinosa58 | ESPAÑA |
Escobillosa59 | |
Pinchuda60 | |
Salada61 | |
Salicor62 | |
Sisallo63 | |
Tamojo64 | |
Carambillo65 | |
Común66 | |
Alacranera67 | |
Fina o de Alicante68 | |
Algazal o Gazul69 | |
Sayones70 | |
Almarjo71 | |
Maromera72 | MÉXICO |
Romerito73 | |
Saladilla74 | |
Verdolaguilla blanca75 | CUBA |
Criolla o yerba de vidrio76 | |
Yerba del Vidrio77 78 | PERÚ |
Lechuga de mar79 | CENTROAMÉRICA |
Con respecto a su sitio de plantío el documento de Correa Núñez expresa que prosperaba en la laguna de Cuitzeo y la ordenanza comentada declara su labranza en Guyangareo, ambos sitios ubicados en la región agrícola de Michoacán, fundada alrededor de 1541 por Antonio de Mendoza19 20 21 , en ella quizás se cultivó alguna otra variante junto con el trigo, cebada, adormidera, comino y anís como costumbre peninsular22. Otro lugar de cultivo fue Xaltocan, ubicado al norte de la cuenca de México y rodeado de aguas con lechos salinos. En esta zona, según ordenanzas de 1796, los indígenas eran diestros en reconocerla y cosecharla, por ello se les exentó de trabajar en el desagüe en la ciudad de México, con el fin de dedicarse a su cultivo y cubrir la demanda solicitada por la Casa del Apartado en donde se producían cornamusas23.
El procesamiento de la barrilla, estaba a cargo del “barrillero”, actividad registrada en la ciudad de México en 1790 y se iniciaba con el secado de la planta madura con raíz por dos semanas, condición en que se almacenaba hasta por dos años siempre y cuando se preservara de humedad. Una vez realizado lo anterior se procedía a incinerarse en temporada seca, lo que requería de 28 a 40 horas y se realizaba en una excavación circular con promedio de 1.5 a 2 m. de diámetro y uno de profundidad, su interior se cubría con arcilla arenosa a la que se untaba líquido graso. En la superficie se colocaba una rejilla de metal sobre la que se distribuía la yerba, el fuego se ubicaba de tal forma que su combustión fuera completa, rápida y uniforme, el producto derretido caía al fondo, pero debería estar libre de yerba sin quemar o de cenizas; a menor cantidad de estos restos, mayor calidad del material. El producto obtenido se agitaba con palas de madera sin generar burbujas24, una vez terminada esta etapa se aguardaba a que la mezcla solidificara, lo que llevaba 48 horas e inclusive se dejaba hasta dos semanas o más; de 4 quintales de hierba que equivalía a 184 kg., se generaba un quintal de piedra de barrilla de 46 kg.; los barrilleros procuraban obtener de 200 a 300 kg., cada vez que se realizaba el proceso25. Una vez endurecida la pasta se fragmentaba para comercializarse, posteriormente los vidrieros trituraban y cernían el material para diluirlo en agua y someterla al fuego y así obtener la sal que se adicionaría al resto de los componentes; esta última etapa muy probablemente se realizó en el sitio de producción y bajo la supervisión del maestro vidriero.
Los vidrieros novohispanos ante dificultades para procesar u obtener la barrilla recurrieron a sustituirla por cenizas de álamo, pino, abedul, olmo y chopo, ya que aportaban compuestos potásicos en lugar de sódicos, aunque con ello se reducía lo diáfano del vidrio; este material fue utilizado en Europa antes de reconocer las ventajas del material sódico incluido en otros recursos naturales. En el siglo XVII se remplazaba a la planta referida por tequesquite26, tal vez por su obtención menos complicada y reconocimiento empírico de sus componentes sódicos y de carbono, puesto que sus características generales fueron reportadas para fines del siglo XVIII27. Al inicio del siguiente siglo se identificaron las variedades denominadas por su manifestación física: polvillo, costrilla y espumilla, así como el sitio exacto de extracción en el lago de México (de Texcoco), cuevas cercanas a Teotihuacán y Otumba, Puebla, Celaya, cerca de Guadalajara, San Luis Potosí, Zacatecas, Durango y Chihuahua28, para entonces se reportaba que la variante polvillo generaba la tenacidad del vidrio. Estudios muy posteriores demostraron la presencia de una variedad adicional presente en el lago de Texcoco, el confitillo; el análisis químico de todas induce a pensar que las más utilizadas fueron esta última y la espumilla, por su gran contenido de sesquicarbonato sódico29. Algunos vidrieros expresaron opiniones adversas de este componente ya que no otorgaba la transparencia al vidrio, sin embargo esto pudo deberse al contenido de materia orgánica y terrosa no eliminada mediante alguna técnica o bien se obtenía de sitio diferente. Esta eflorescencia mineral natural se empleaba también en el procesamiento de textiles, en la metalurgia para sintetizar ácido nítrico o “agua fuerte” con el que se separaban metales, y para producir pólvora30 31. Para esta última aplicación se requería purificarlo, lo que realizaba la Real Fábrica de Pólvora con alto costo económico; el explosivo era de vital importancia para el gobierno ya que se destinaba a los buques de guerra que escoltaban a los que transportaban mercancías, oro y plata hacía la península ibérica, los que en ocasiones eran interceptados por naves de origen inglés interesadas en los metales.
Otro ingrediente utilizado fue el calcio que se obtenía de cenizas de caliza, huesos y rocas sedimentarias de canteras con depósitos de microfósiles y caparazones del plancton, específicamente del tepetate blanco localizado en la cercanía del lago de Texcoco aportaba este elemento químico con función estabilizante de la reacción entre los integrantes. Desde la época prehispánica la cal u óxido de calcio se empleaba como material de construcción y en el proceso de nixtamalización, por lo que su obtención no fue complicada para los vidrieros. Al principio de la Colonia la cal se producía en Zumpango, Citlatépetl, Xaltocan, Tequixquiac y en Hueypoxtla; los españoles de la ciudad de México desde el siglo XVI demandaban de este último sitio su producción y habitantes de Xilotzingo compraban piedra caliza a este poblado para quemarla y comercializarla también, sin embargo posteriormente la cal se adquirió del sureste de Tula, Hidalgo32. Es importante considerar que las laderas de la cadena montañosa que rodeaban al lago de Texcoco contenían gran cantidad de carbonato de calcio dada su constitución de rocas ígneas y tobas volcánicas, sobre las que se encontraba el tepetate blanco.
La roca caliza extraída de canteras se calcinaba en hogueras abiertas y al aire libre llamadas “caleras” o en fosos de dos metros de diámetro y 50 cm. de profundidad; se construían también hornos de piedra o arcilla hasta de ocho metros de diámetro, techados y ubicados bajo el nivel del suelo para reducir el consumo de energía para mantener por mayor tiempo la temperatura a semejanza de los hornos peninsulares de Toledo33. El proceso de calcinación debía realizarse a cierta temperatura de lo contrario se perdía la reactividad química, aquellos fragmentos que no alcanzaban este estado se retiraban y el remanente se cernía varias veces mediante malla fina para obtener fracciones lo más pequeñas posibles. Es probable que los vidrieros se valiesen del mármol para obtener este compuesto como los artesanos muranenses34.
Los metales incorporados en el material pétreo como el cobre, manganeso, hierro, estaño, níquel y otros proporcionaban color al vidrio según la proporción contenida, el conocimiento empírico alcanzado por algunos vidrieros permitía eliminar la acción de los metales o reforzarla al adicionar otros de manera intencionada para lograr cierta variedad de coloración o bien decolorarlo. Este saber condujo a la posibilidad de imitar el color de algunas piedras, por ello tanto en la península ibérica como en la Nueva España se promulgaron ordenanzas que prohibían a estos artífices la colocación de piezas de vidrio engastado en plata, oro u otro metal con el fin de evitar el fraude35; se desconoce hasta el momento sí alguno de origen novohispano contaba con dicha habilidad.
Hornos de Producción
La información de las particularidades arquitectónicas de los hornos de vidrio en la ciudad de México es reducida, parte de ella es posible deducirla de los planos de la Casa del Apartado que datan de 1778, ya que eran al menos activos previamente al último tercio del siglo XVII; este sitio se ubicaba en el límite norte de la primera traza de la ciudad, adjunto a una acequia, en la “Calle de agua que va al monasterio de Santo Domingo” que más tarde se denominó “Calle del Apartado”36. Sumados a él existieron dos sitios más de fabricación registrados en 1748 y 1790, por el momento se desconocen sus características, existencia de restos arqueológicos y fecha precisa en que iniciaron su actividad. Otras referencias, aunque ajenas a nuestro país permiten tener idea de las particularidades de este tipo de instalación, una de ellas es la de Georgius Agricola de 1556 37 y la restante es la descripción arquitectónica de restos arqueológicos de seis hornos de un taller de vidrio de finales del siglo XIII ubicado la región de Murcia, España38
Del documento de 1556 se infiere que el número de hornos en el taller de producción dependía de la solvencia económica del vidriero para establecer la factoría y mantener el volumen de objetos elaborados. Agricola expresa que eran necesarios tres de ellos para realizar el proceso, sin embargo al disponer de uno solo era posible lograrlo, aunque implicaba mayor tiempo en la ejecución de la tarea, menor número de trabajadores y por tanto volumen reducido de piezas generadas. El primer horno servía para la fusión de los integrantes de la materia prima; era de forma circular con techo abovedado, en su base y al centro se ubicaba la fosa para el fogón y se accedía a él por un corredor en pendiente, que iniciaba en una de las caras de la pared externa. Por arriba de este acceso y lateralmente se encontraba una oquedad para introducir el crisol que contendría “pasteladura vítrea”39. El material para la construcción de hornos era arcilla particular, las fuentes de información solo refieren el empleo de barro negro y blanco provenientes de diversos lechos fluviales, con ellos se fabricaban bloques de hasta 70 cm. de grosor y se unían entre sí con el mismo tipo de material, una vez construido con estos bloques se recubría con ladrillo; los crisoles empleados también se fabricaban con este material40.
El segundo horno de diámetro aproximado de cuatro m. techado con bóveda y de dos m. de altura, contaba con fogón central y acceso a este. En sus paredes se encontraban varias oquedades de forma cuadrangular separadas entre sí a distancia similar, a través de las que se introducía el crisol para vaciar su contenido a los colocados en su interior e introducir la “caña”, herramienta necesaria para tomar la materia vítrea a modelar, por lo que se le denominaba de trabajo (Fig. 1).

Fig. 1 Grabado que muestra el “horno de trabajo” con oquedades de forma cuadrangular por las que introducían la “caña”. El volumen de producción estaba supeditado al número de artesanos que trabajaban y dimensiones del horno. Fuente: Suárez y Núñez, 1780.
Adjunto al descrito se encontraba un tercero que sería de templado, de forma rectangular con oquedades por las que se introducía las piezas ya modeladas y se colocaban sobre la plataforma horizontal que separaría al fogón (Fig. 2); la temperatura en él era menor con el fin de evitar el cambio brusco de ésta lo que generaba fragmentación de las piezas, después de cierto tiempo se extraían de él para almacenarse41.

Fig. 2 Representación del horno de trabajo y de templado, este último de forma rectangular en que se colocaban las piezas ya modeladas previamente a su almacenamiento en bodegas. Fuente: Agricola, 1556.
Los detalles mencionados al conjuntarse con la información de los cuatro hornos de vidrio que revelan los planos de la Casa del Apartado permiten concebir la imagen de esta zona de producción (Fig. 3). En dos espacios denominados la “Oficina de hornos de vidrios”, con dimensiones de 27 varas de ancho por 17 de largo que equivaldría aproximadamente a la superficie de 383 m2 y techados con tejamanil, se encontraban cuatro hornos separados por un muro pero con acceso entre sí. En una de ellas existían dos de forma circular de diámetro menor con tres aberturas y recámara lateral de forma rectangular, una adjunta y otra separada, con acceso propio e independiente; en la “oficina” restante se reconoce un horno de diámetro mayor con una abertura y sin recámara y otro de menor tamaño con tres aberturas y recámara agregada42. El primero presenta la abertura que pareciera ser el umbral que conduce hacia el fogón o bien el espacio para introducir o extraer el crisol. Los tres hornos restantes de diámetro menor.
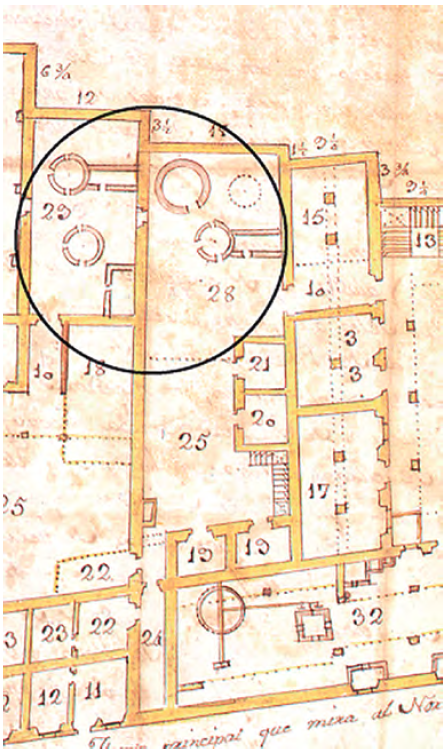
Fig. 3 Fracción del plano de la Casa del Apartado, el círculo negro delimita la “Oficina de hornos de vidrio” (28 y 29); las cifras que aparecen en la parte superior indican la longitud en varas castellanas. Cada espacio muestra la representación de los hornos de trabajo con tres accesos para depositar el material fundido o tomarlo de los crisoles; el de mayor diámetro era el destinado a la fusión. Adjunto a ellos se aprecia un espacio rectangular que sería el horno de enfriamiento; los números 15, 19 y 20 refieren bodegas de cornanuzas, vidrio y barrilla respectivamente. Fuente: AGN. Casa de Moneda, Vol. 388, exp. 5, f. 60.
Serían los de trabajo, sus aberturas probablemente estuvieron colocadas a una altura del nivel del piso que permitiría al artesano tomar fácilmente el material vítreo mediante la “caña”, lo que condicionaría que el espacio destinado al fogón se ubicara por debajo del nivel del piso para mantener por mayor tiempo el calor necesario. Adicionalmente los espacios laterales permitían liberar el vapor generado en la cámara, aunque esto propiciaba que los artesanos estuvieran más expuestos a la alta temperatura propagada43. En relación a los de forma rectangular adjuntos a los de trabajo corresponderían al de templado (Fig. 3).
Un aspecto que llama la atención respecto a la descripción de las características de los hornos y que no se constata en los planos, es la existencia de espacio específico para al fuelle o bien que la orientación del horno fuera tal que permitiera la entrada de corriente de aire que “avivara” el fuego e intensificara la combustión; se excluye ésta última condición puesto que se encontraban en espacios cerrados. Se desconoce el material con el que se construyeron estos hornos de la ciudad de México, únicamente se tiene referencia que los crisoles se fabricaban de roca porfídica muy refractaria, extraída de una cantera cercana a la ciudad de Pachuca, los que eran necesario remplazar por continuo deterioro44; la fuente energética empleada era leña seca de árboles belloteros y roble que proporcionaba mayor aporte térmico45, su transportación pudo ser por vía fluvial para reducir costos.
Al compararse la representación de los hornos de menor diámetro de la Casa del Apartado de 1778 (Fig. 3) con el de Murcia46 (Fig. 4A), se percibe similitud de su base y de los accesos laterales (Fig. 4B) y a su vez con las de Agricola del siglo XVI (Fig. 2). De lo anterior se deduce que los hornos de vidrio del siglo XVIII de la ciudad de México mantenían el diseño de los empleados en el siglo XVI y a su vez con los de tres siglos atrás en Europa, aunque muy probablemente variarían los materiales con los que se construían.

Fig. 4 Representación arquitectónica de un horno de producción localizado en Murcia. A. Vista de la planta del horno en ella se aprecia una banqueta en forma de “U” donde se encontraban restos de crisoles (c) con material vítreo; en posición central se ubicaba el fogón (f). B. Corte transversal en que la línea curva punteada muestra hipotéticamente la bóveda, en sus extremos se marca el acceso (ACC) al interior del horno y la ubicación de los crisoles (c) Fuente: Jiménez, 1998
Aunque el propósito de esta sección del documento no es realizar el análisis de los hornos empleados en diferentes actividades, es conveniente expresar que en la producción de cerámica también se empleó este recurso, sin embargo existió una variedad de ellos47 debido entre otros factores a la temperatura necesaria para lograr la cocción de la argamasa empleada, diferente a la requerida para la fusión de la materia vítrea. Una variante de ellos presenta características similares específicamente en el que se realizaba la fusión, ya que ambos eran bicamerales de base circular, con domo y parrilla, este elemento separaba ambas espacios48, el inferior destinado a concentrar el calor de la hoguera y el superior en la que se colocaba el crisol para fundir la masa vítrea, asimismo comparten el mismo diseño arquitectónico que el de los hornos árabes49, pero muy probablemente se diferenciaban es su material de construcción, aunque ambos se recubrían de ladrillo.
Herramientas
Con respecto a estos utensilios los registros novohispanos son inexistentes hasta el momento, no obstante la reducida información de origen europeo auxilia a la comprensión de la última etapa de fabricación de artículos de vidrio.
Las herramientas requeridas por los vidrieros eran diversas, algunas de uso básico y otras de diseño singular de acuerdo a la especialidad del artesano que debieron ser forjadas por herreros, sin embargo ya que varias de ellas estarían expuestas a temperaturas de consideración debieron de tener porciones de madera para poderlas manejar.
Una vez colocada la materia prima en el crisol, se introducía al horno para lograr la integración de los ingredientes entre el rango de 500 a 1,500° C durante cinco horas, lapso en que algunos elementos químicos requerían menor o mayor temperatura para unirse entre sí. Durante este momento era necesario agitar la mezcla mediante palas de hierro de mango largo50 y retirar burbujas con ayuda de la pala llamada “espumadera” también de metal aunque con varias perforaciones51, sus largas empuñaduras de madera se apoyaban en el soporte denominado “cabra”52 que las mantenía en posición horizontal, con el fin de evitar fatiga y larga exposición del vidriero al calor intenso. Una vez que la materia vítrea alcanzaba su mayor fluidez, según la experiencia del artesano, se procedía a trasladar el crisol al horno de trabajo53 para vaciar el contenido a otros crisoles. A continuación un vidriero diferente introducía por las aberturas laterales una varilla de metal hueca de 120 a 180 cm. de longitud denominada “caña”, cuya tercera parte de este utensilio era de madera y en su extremo tenía una boquilla. Una vez que lograba retener un volumen determinado de la masa con el extremo de metal, extraía la caña para insuflar aire con la boca y formar una ampolla o vejiga, la que modelaría de acuerdo a la forma y grosor del objeto deseado. Este último ya modelado se separaba de la caña para fijarse al “puntil” (caña maciza), una vez adherida se colocaban aplicaciones adicionales de materia vítrea para confeccionar asas y diferentes realces con el fin de decorar la pieza. Para lograr esto último, se empleaba una variedad de pinzas y herramientas (Fig.5) e inclusive el artesano se acomodaba en un banco con descansa brazos que le permitía, una vez sentado, apoyar y mantener en forma horizontal el “puntil” y a la vez girarlo con el fin de colocar en la periferia del objeto aplicaciones que lo aderezaban o bien generar el cuello de un frasco o partes angostas en el envase o bien delinearlo con pinzas especiales e inclusive modificar la superficie.

Fig. 5 Herramientas empleadas por vidrieros: tijeras (A), pincetas de punta (B), de concha (C), de flor (D), de asas moldeadas (E), planas (F), asas cuadradas lisas (G), hoja de oliva (H) y para generar perforaciones (I). Su empleo dependía de la pieza a modelar. Reproducción esquemática de Adrián R. Peralta Chacón, tomado de Suárez, 1780.
Las placas de vidrio plano se obtenían a partir de una vejiga vítrea a la que se le daba forma de cilindro mediante movimiento oscilatorio de la caña y simultáneamente por lo viscoso de la vejiga incrementaba su longitud. El extremo opuesto a la boquilla se recortaba con el empleo de tijeras o una herramienta de forma semejante a un sable, a continuación con estas mismas se cortaba el cilindro a lo largo por una de sus caras, lo que generaba que la estructura tendiera a tomar forma cóncava con tendencia a aplanarse a causa del peso de sus borde. Mediante pinzas colocadas en sus vértices se ubicaba sobre una plancha de piedra o madera, cubierta de una capa de arena o polvo muy fino para evitar su adherencia a la superficie54 y completar su aplanamiento; debido a que los cilindros de vidrio eran cortos y de diámetro reducido, las placas de vidrio empleadas como ventanas o espejos eran de dimensiones reducidas. También se elaboraba vidrio plano de forma circular a partir del aplanamiento de la vejiga55 al presionarla sobre la plancha mencionada.
Los candiles o arañas se conformaban de piezas pequeñas de diversas formas, las que se perforaban con pinzas de extremos puntiagudos para generar orificios pequeños e introducir cordón de metal para unirlas entre sí, en algunas de ellas se generaban realces en la superficie al presionarlas con pinzas de relieve en las caras internas o bien eran labradas a mano.
Las bases planas de vasijas y recipientes se generaban con el uso de placas de mármol o metal denominadas “mabre” o “plancha”, al asentar la vejiga de vidrio; de requerirse algún detalle de dimensión en una porción del objeto, el artífice se auxiliaba del “bufador” (Fig. 6)56, herramienta con la que se insuflaba aire en una porción de la pieza fija al “puntil”, generalmente eran recipientes de forma particular solicitados por boticarios y médicos. Los objetos ya modelados se separaban de este para introducirlos al horno de enfriamiento o templador mediante el uso de palas largas a manera de charolas; para desplazarlas en el interior se empleaba el “rable”, varilla de madera y hierro en forma de “T”, la porción más larga servía de mango.

Fig. 6 La ilustración izquierda corresponde a la herramienta denominada “bufador”, utilizada para soplar dentro de la pieza modelada parcialmente y así dar forma a porrones bufados, ilustración de la derecha. Fuentes: Cabañete, 1958, Suárez y Núñez, 1780.
De todo lo anterior se deduce que el espacio físico destinado a la fabricación de vidrio era de dimensión extensa ya que aunado al asignado a los hornos se requería de sitios adicionales para molienda de la materia prima, sí el material no se adquiría con cierto grado de trituración, lugar para el resguardo de herramientas, accesorios y el destinado a almacenar materia prima, leña y piezas producidas. Era costumbre que el sitio de fabricación se ubicara adjunto a la morada del maestro vidriero, por lo que todo induce a pensar que aún de que el taller de producción fuera pequeño dispusiera recursos mínimos para laborar. Existe registro de que se asignó a uno de los primeros vidrieros novohispanos dos “solares”, terreno con superficie total de 5000 varas cuadradas equivalente a 3,512 m2, en donde podría construir su vivienda y taller, asimismo de que a otro vidriero se le concedió un solar en el barrio de Moyotla, localizado al sur-poniente de la ciudad57. La ubicación de los sitios de fabricación de vidrio en la ciudad de México era contigua a las acequias por la necesidad imperiosa de agua en el proceso y asimismo como vía de acceso para la entrega de materia prima y leña proveniente de bosques circunvecinos; su localización alejada de la ciudad prevenía incendios y otras molestias, sin embargo el apresurado asentamiento de la población condujo a su inclusión en la parte urbana, lo que sucedió con la Casa del Apartado.
La labor de producción vidriera era compleja y detallada, la instalación de la planta productiva implicaba recursos económicos de consideración aún de ser modesta. En forma específica la Casa del Apartado, a cargo de particulares, pudo hacer frente a la inversión ante los altos ingresos obtenidos por la separación del oro y plata, que el gobierno pagaba por ello. Este sitio de producción absorbía la “barrilla” y el tequesquite de la más alta calidad para producir cornamuzas y agua fuerte, destinados a la separación de los metales referidos; ante la experiencia alcanzada y el aprovechamiento de la infraestructura instalada se dedicó a producir envases y otros aditamentos de vidrio para boticarios y médicos, lo que redundaba económicamente. Para los vidrieros independientes que atendían la demanda de algunos miembros de la sociedad de boticarios y flebotomianos, la instalación del sitio de producción fue más ardua, muy probablemente tuvieron que recurrir ocasionalmente a la Casa referida para adquirir barrilla o bien a la Real Fábrica de Pólvora para procurarse tequesquite, puesto que esta última supervisaba el uso de la variante refinada.
A pesar de lo anterior el proceso de producción de vidrio en la ciudad de México, que tuvo como fundamento la experiencia peninsular, se enfocó a la fabricación de artículos suntuarios de uso cotidiano y hacia la elaboración de recipientes empleados en la metalurgia y iatroquímica, (etapa de transición entre la alquimia y química farmacéutica), el uso de envases contenedores de remedios para la salud muy probablemente fueron incorporándose a la vida cotidiana para ser de uso ordinario en aquellos ámbitos sociales carentes de capacidad económica para encargarlos al artesano.