1 Introduction
The use of aluminum alloys is of great interest in automotive and industrial applications that depend on the weight-to-strength ratio [1,
2,
3]. Al-Si-Cu systems [4,
5], among them the AA319, can further improve their mechanical properties by standard heat treatments [6,
7], by the Al2Cu (
This research studied the Nickel effect as an additional alloying element in aluminum alloy 319 alloys regarding microstructure and mechanical properties in as-cast, T6 heat treatment, and overheating conditions.
2 Experimental procedure
The raw materials were commercial AA319and Al-20Ni (wt.%) master alloys. The AA319 alloy was melted at 740 in a graphite crucible using a Lindberg Blue electric furnace. Al-20Ni master alloy was added in different proportions to obtain +1, +1.5, and + 2%Ni modified alloys. Synthesized alloys were degassed for 5 minutes using Ar gas and a graphite propeller at 490 rpm, then 0.33 (wt.%) of Al-5Ti-B grain refiner was added. Table I contains elementary quantifications obtained by inductively coupled plasma-atomic emission spectroscopy.
Table I Chemical compositions obtained by ICP-AES: AA319 corresponds to the commercial alloy until modified compositions correspond to +1, +1.5, and +2 (wt.%) Nickel.
Si | Cu | Fe | Zn | Mg | Mn | Ni | Al | |
---|---|---|---|---|---|---|---|---|
Al-319 | 7.94 | 2.51 | 0.7 | 0.39 | 0.33 | 0.25 | 0.04 | bal |
+1%Ni | 7.64 | 2.2 | 0.57 | 0.37 | 0.33 | 0.24 | 1.08 | bal |
+1.5%Ni | 7.47 | 2.11 | 0.59 | 0.37 | 0.33 | 0.24 | 1.59 | bal |
+2%Ni | 7.13 | 2.1 | 0.54 | 0.38 | 0.31 | 0.26 | 2.15 | bal |
Table II Nomenclature corresponds to AA319 and Ni-modified alloys. Tests at ambient temperature correspond to as-cast (AC), solubilized + aging (T6), and over-heating at 250 (OH) conditions. Tensile tests performed at high-temperature conditions over T6 samples correspond to 495 (HT1) and 520 (HT2).
Sample | Test temperature at 25°C | Test temperature at 250 °C | ||
---|---|---|---|---|
Solubilization(5hrs@495°C) | Solubilization(3hrs@520°C) | |||
T6 | OH(45inm@250°C) | HT1(45inm@250°C) | HT2 (45inm@250°C) | |
Al-319 | AT6 | AOH | AHT1 | AHT2 |
+1% Ni | +1%NT6 | +1%NOH | 1%NHT1 | +1%NHT2 |
+1.5% Ni | +1.5%NT6 | +1.5%NOH | +1.5%NHT1 | +1.5%NHT2 |
+2% Ni | +2%NT6 | +2%NOH | +2%NHT1 | +2%NHT2 |
Mechanical properties were measured by tensile and hardness tests using as-cast and heat-treated samples; this last case considered room temperature and 250 conditions. Regarding room temperature tests, the thermal history of samples includes four categories:
As-cast (AC),
T 6-1 consisted of solubilization at 495 for five hours, quenching in the water at 60 and aging at 220 for three hours.
T 6-2 consisted of solubilization at 520 for three hours and the same quenching and aging.
Overheating condition (OH) obtained by T 6-1 samples subject to 250 for 45 minutes, then cool at room temperature.
High temperature of 250 after 45 min for temperature homogenization test in T 6-1 and T 6-2.
A Panalytical X’Pert PRO diffractometer was used for the initial characterization by X-ray diffraction (XRD) technique with Cu radiation at 40 kV and 35 mA. Samples prepared by conventional metallographic techniques and chemically attacked using 20 HCl04 /80 MeOH were analyzed by scanning electron microscopy (SEM), JEOL 5800-LV operated at 20 kV. In the transmission electron microscopy (TEM), we used PHILIPS CM-200, and JEOL JEM2200FS operated at 200 kV. Metallographic preparation was based on electropolishing at -30 using 30 HCl03 /70 MeOH electrolyte solution and 20 V. Samples to tensile tests were manufactured according to the E8-ASTM standard and tested in an Instron-337 universal machine at 0.1 mm/s. Evaluation hardness in a Rockwell-Wilson tester was done and reported on the Rockwell-B scale.
3 Results
In Fig. 1, XRD patterns show the peaks corresponding to the significant constitutive elements Al, Si, and Cu. Quantification of metallic-Cu was slightly higher in T6 than as-cast. The Ni addition does not change this behavior. Cu clusters suffered significant changes due to heat treatment, where no significant variations were observed compared to the AA319 and AA319 + 2%Ni. The Al2Cu phase was observed in AA319 after T6 heat treatment. An unexpected AA319 + 2%Ni A2lCu phase was obtained in a lower concentration.

Figure 1 X-ray diffraction patterns for as-cast and T6 conditions: a) Al-319, b) +2%Ni. Crystal structures were determined using the Rietveld method.
To AA319 + 2%Ni, additional phases were indexed corresponding to expect AlNi and AlCu. The T6 heat treatment does not modify Ni intermetallic compounds because of thermal stability, which is related to an expected increment in the hardness performance.
SEM micrographs (Fig. 2a)) of the as-cast AA319 show that α-Al precipitates do not present a clear dendritic arrangement morphology, obtaining a similar microstructural arrangement that the observed for as-cast AA319 + 2%Ni (Fig. 2b)).
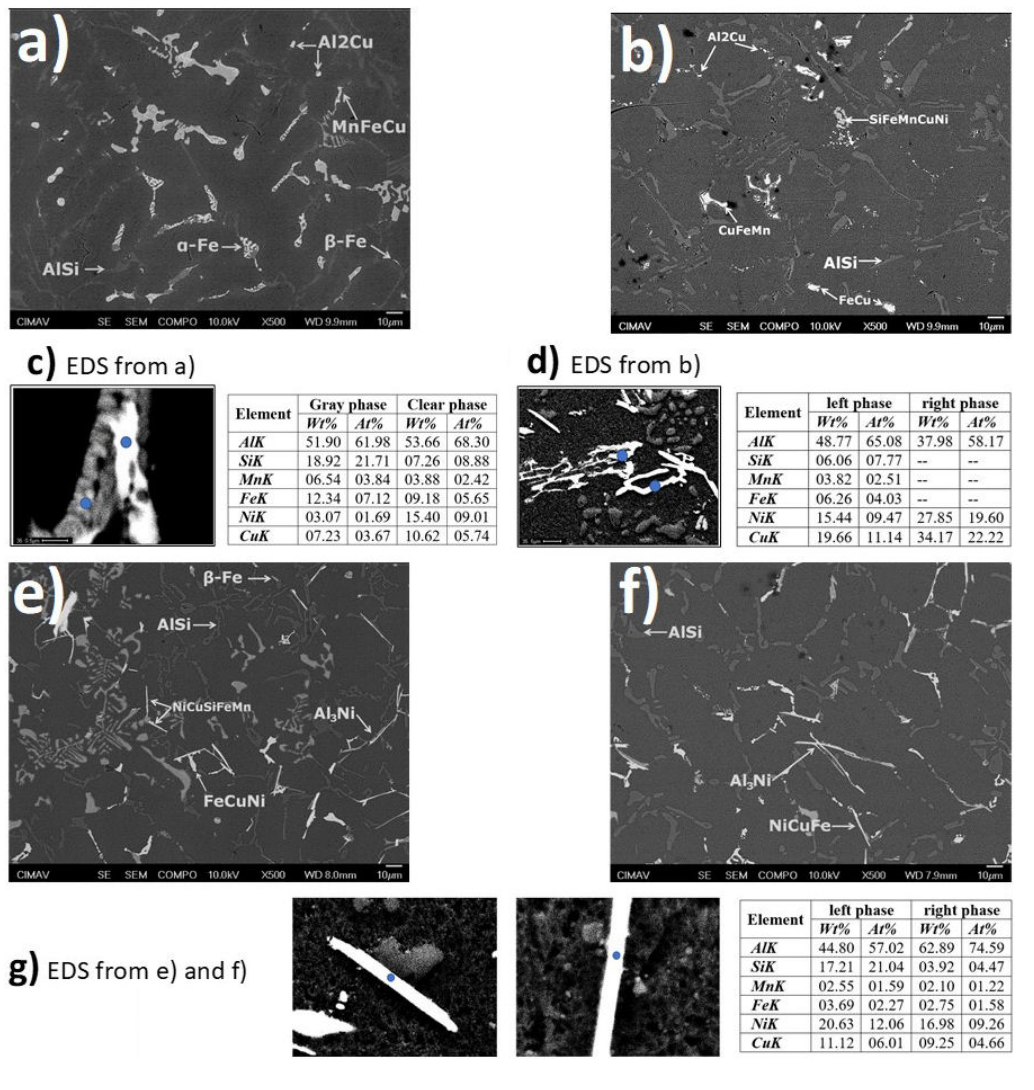
Figure 2 SEM micrographs of as-cast and T6 heat treatment conditions; a) as-cast AA319, b) AA319T6, c) as-cast AA319 + 2%Ni T6 , d) AA319 + 2%Ni T6 . The EDS results in Figs. c), d), and g) correspond to the representative phases found in more significant quantities in each thermal state and chemical composition.
Al2Cu clusters were identified as coarsening particles in the as-cast stage. Intermetallic particles were identified along Al-matrix containing as main elements: Cu, Fe, Mn, and Ni [15]. In the case of AA319 + 2%Ni (Fig. 2e)), Al3Ni in ribbon-like morphology was the most notable effect after Ni addition [16]. Ni intermetallics precipitated with Fe and Cu elements [17]. Microstructural changes due to T6 heat treatment were observed following the Oswald ripening process, a notable effect of coarsening and rounded
Regarding Cu clusters, there was a similar amount of Cu dissolved in α-Al after Ni addition, which remained without significant changes in both AA319 T6 and AA319 + 2%Ni T6 . Additionally, in both solution temperatures schemes (495 and 520), Cu clusters were maintained in similar amounts and sizes. The morphology of Al9FeNi was modified in Ni samples, differing from undesirable Fe phases with sharp edges.
Figure 3 characterized by TEM the evolution of micro- and nano- precipitates in AA319 and AA319 + 1%Ni at T6 and over-heating thermal stages. T6 heat-treated samples in Figs. 3a) and 3c) show dark phases of irregular morphology, corresponding to high Si content precipitates with a similar composition range. AA319
T6
(Fig. 3a)) contains a high density of Al2Cu-
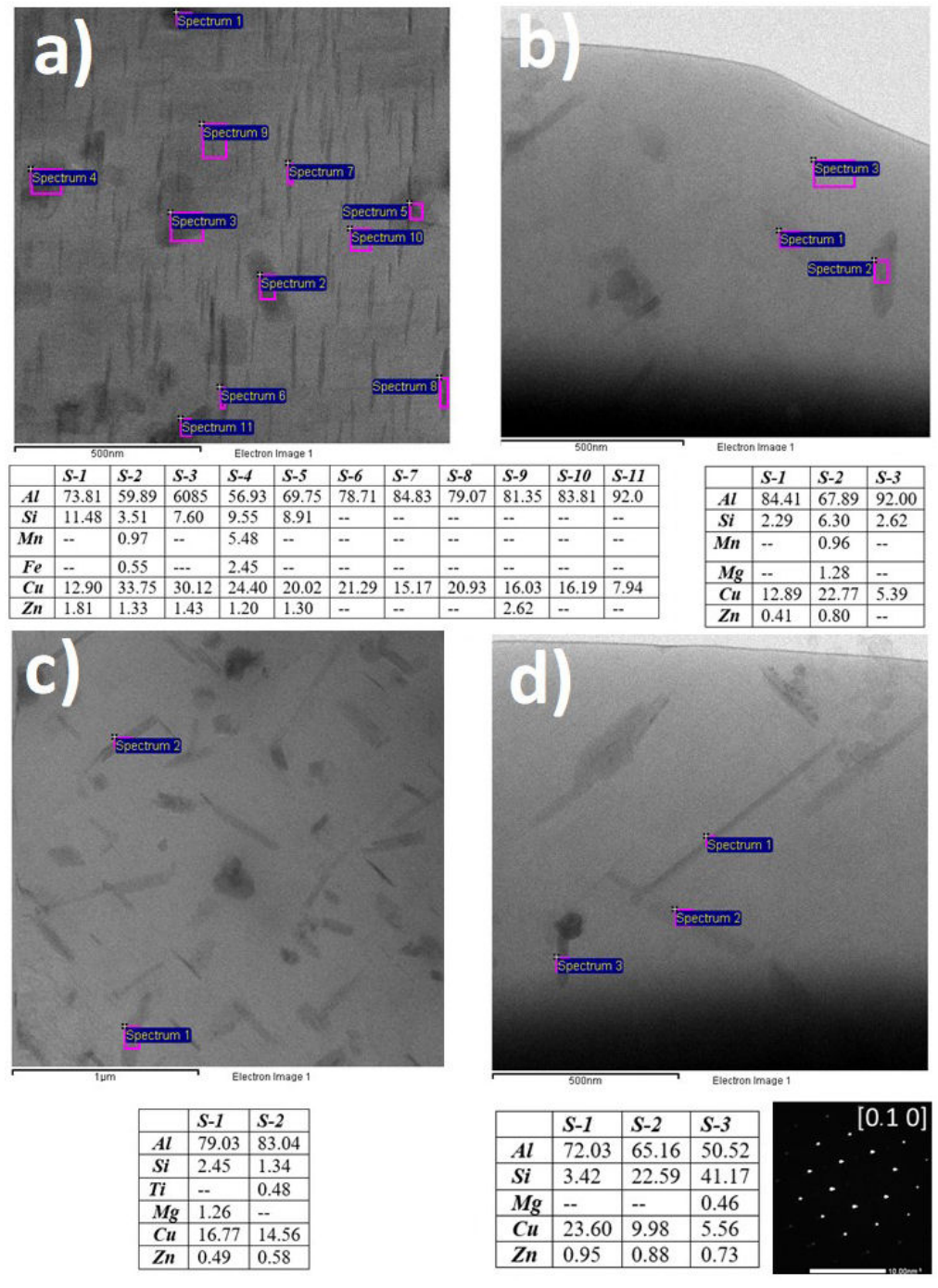
Figure 3 TEM micrographs of a) AA319 T6 , b) AA319 OH1 , c) AA319 + 1%N T6 , d) AA319 + 1%N OH . In all cases, elemental analyses are listed and labeled as Spectrum and the studio number.
The TEM micrograph presented in Fig. 3b) reveals that high temperatures, described in the experimental section, produce thermal degradation of the AA319. AA319
OH
sample shown in Fig. 3b) a representative area where
Figure 4 concentrates hardness and tensile test measures. The presence of hard Ni phases should be enough to increase hardness value regardless of thermal history; thus, this was observed since the as-cast condition, as seen in Fig. 4a). It was observed a gradual increment in hardness with Ni content additions in modified alloys. In the T6 condition, hardness variation is not significant since changes were just a few units. It was observed mechanical degradation by over-heated condition after high-temperature condition, with increment in hardness as a function of Ni content. The hardness of AA319 + 2%N OH increased significantly from its previous thermal condition, T6. AA319 + 1%N OH was enhanced around 10% relative to the reference alloy AA319 OH and 5% compared to the maximum of AA319 T6 .
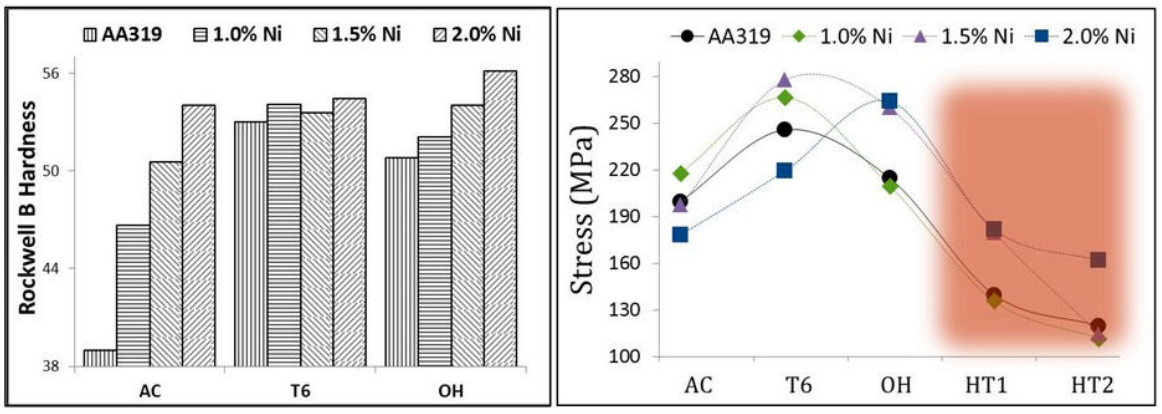
Figure 4 Rockwell B Hardness and UTS values for all chemical compositions; AA319, AA319 + 1%Ni, AA319 + 1.5%Ni, and AA319 + 2%Ni. Used thermal stages were; as-cast, T6, over-aging, and high temperature for two different solubilization temperatures HT1 (495) and HT2 (520).
In Fig. 4b, tensile tests are shown: in the as-cast condition, AA319 + 1%Ni sample obtained the highest UTS values of 218 MPa, followed by AA319, +1.5%Ni, and +2%Ni (178 MPa). After T6 thermal treatment, AA319 + 1.5%Ni T6 and AA319 + 1%Ni T6 samples present the highest UTS values of 278 and 267 MPa, respectively. In comparison, the AA319 value was 246 MPa; over-heating conditions, the deteriorating effect in AA319 OH and AA319 + 1%N OH samples were evident. For the AA319 + 1.5%N OH and AA319 + 2%N OH samples, UTS values were 260 and 264 MPa, respectively, evidencing the effect of the addition of Ni. UTS reaches maximum values at the T6 stage for AA319 T6 , AA319 + 1%%N T6 , and AA319 + 1.5%N T6 ; however, a pronounced drop of every maximum peak was observed in the over-heating condition. The maximum UTS was obtained at over-heating for AA319 + 2%N OH . UTS values until high-temperature conditions were maintained in the range of 136 MPa (AA319 + 1%N HT1 ) to 182 MPa (AA319 + 2%Ni HT1 ). Regarding the higher solubilized temperature, HT2, the range was 112 (AA319 + 1%N HT2 ) to 162 MPa (AA319 + 2%N HT2 ).
4 Discussion
Commercial aluminum alloy 319 (AA319) after T6 heat treatment reduced the amount and size of Cu clusters due to the solubilization process activated by high temperature [?]. In Ni-modified samples, a significant reduction in the size and quantity of mentioned Cu-clusters was presented. Regarding indexed crystal phases, XRD showed a quantity decrease in
On the other hand, the retaining of
The mechanism, such as Ni interacting with Cu to reduce the size of the needles, was not clear after using TEM micrographs at solubilized samples after 1 to 4 hrs. However, it was supposed a reduction of kinetics transformation from GP to
Al-Ni precipitates are hard and brittle particles, which can decrease UTS in the way that occurred in AA319 + 2%N
AC
. However, the increase of Al2Cu phases positively counterbalanced the presence of Ni phases in a significant way. UTS value increased by Ni addition due to the higher density of Al2Cu with a smaller dimension. The observed drop in UTS values at high temperatures and long times is due to the coarsening of Al-Cu and Al-Si precipitates, which quickly screen the improvements done by Ni precipitates. It is a known fact that the coarsening of Al2Cu phases is presented as a function of the temperature. However, the detrimental effect of transformation kinetics of the
5 Conclusion
Commercial aluminum alloy 319 and a series of alloys modified with +1.0%, +1.5%, and +2.0% Nickel were used to investigate their micro and nanostructural evolution. The synthesized conditions were as-cast, T6, overheating, and high temperature. By TEM micrographs, it was concluded that the modified alloys reduce