1. INTRODUCCION
Desde las primeras civilizaciones, los materiales con cierta capacidad de adherencia (material cementante) han sido fundamentales para el desarrollo y evolución de las construcciones. Es así que durante el transcurso de la historia el hombre ha tratado de buscar otros materiales cementantes para obtener mejores propiedades mecánicas y durabilidad. Esta evolución ha llevado a que el cemento portland y el concreto reforzado sean los materiales más utilizados en la industria de la construcción (Gamgbir, 2009).
Por otra parte, la industria del cemento es una de las principales fuentes generadoras de dióxido de carbono (CO2). Se estima que las emisiones de CO2 a la atmósfera alcanzan un valor de 1.0 ton por tonelada de Clinker (Cassgnabere, 2009), que es de donde se obtiene el cemento portland después de la molienda. Ante este inconveniente se han buscado alternativas de aprovechamiento de materiales con capacidad cementante que no sean dañinos para el medio ambiente debido a su procedencia y que además, cuidadosamente empleados, puedan aportar beneficios. Lo anterior ha dado pie a la utilización de sub-productos industriales cuya categorización es amplia y variada (Malhotra, 1996; Day, 2006). Aunque actualmente la cantidad de residuos/sub-productos que se utiliza es poca, comparada con la que se produce, cada día alrededor del mundo se llevan a cabo investigaciones para buscar nuevas aplicaciones de éstos como materiales cementantes en la industria de la construcción con el objetivo de lograr un mayor empleo de ellos y de esta manera disminuir la huella de carbono de la industria de la construcción.
Existen algunos desechos industriales que pueden ser viablemente utilizados como materiales cementantes y que, además, requieren poco o ningún tipo de tratamiento previo para su utilización en la mezcla para concreto y/o mortero. Por otro lado, también existen otros materiales cementantes de origen natural (por ejemplo la ceniza volcánica) que se encuentran disponibles para su uso en la mezcla de concreto (Malhotra, 1996).
Algunos materiales cementantes provenientes de desechos industriales que pueden utilizarse como materiales alternativos son: la ceniza volante, el humo de sílice, la escoria de alto horno, la metacaolinita y el esquisto (Day, 2006), los cuales se pueden emplear como adiciones minerales en la preparación del cemento portland fabricado en planta (Cemento Portland Modificado, CPM); como adición en la molienda; o por la mezcla de dos o más tipos de materiales finos que sustituyen parcialmente al cemento portland (Cemento Hidráulico Adicionado o Cemento con sustituto cementante) empleados en la mezcla de concreto o mortero (Kosmatka, 2004).
La primera propiedad en el concreto que se ha visto afectada por el uso de materiales cementantes de origen natural o industrial es la resistencia a la compresión, asignando para este trabajo la resistencia real (f c ) obtenida de los ensayos por compresión, y por ello existe una gran cantidad de trabajos (Cassgnabere, 2009; Bagheri, 2013; Atis, 2003; Ashtiani, 2013) que bajo diferentes mezclas, condiciones, procedencia o atmósfera permiten utilizar una cierta cantidad de éstos materiales sin afectar en forma notable sus propiedades mecánicas del concreto. Es complicado pensar en un atlas de uso de estos materiales, pero se vislumbra como una necesidad la de conocer si la tendencia a disminuir la f c es constante ó cual es su límite en función de los parámetros de investigación que han sido utilizados en diversas investigaciones. De igual manera, aunque ya existen excelentes combinaciones de materiales cementantes que dan lugar a cementos binarios, ternarios e incluso cuaternarios (Nedi, 2001), la disponibilidad de los materiales en una sola zona o región puede constituir un impedimento económico para su uso generalizado, en especial en países en desarrollo. Por ello el uso de cemento binario producido en planta puede ser de momento la alternativa más práctica en términos económicos y de disponibilidad. El objetivo de este trabajo es re-visitar el estado del arte sobre las tendencias de la resistencia a la compresión de concretos y estructuras que utilizan Escoria de Alto Horno (EAH) como material cementante, así como revisar los niveles de reemplazo de cemento portland que se consideran en las normativas de diferentes países del mundo para la clasificación de los cementos con escoria de alto horno, ya sea mezclado durante la molienda o por la mezcla separada a partir de cada material molido.
2. CARACTERÍSTICAS DE LA ESCORIA DE ALTO HORNO
Un subproducto cementante es el material secundario o incidental que se deriva del proceso de fabricación industrial a través de una reacción química, el cual posee la característica conglomerante después de cierto tratamiento (Malhotra, 1996). Un subproducto industrial considerado como de desecho, puede poseer cierta capacidad puzolánica, y puede ser útil y comercializable al hallarle alguna aplicación en otro sector industrial, por ejemplo como sustituto parcial del cemento portland en las construcción con concreto, o también como agregado pétreo como es el caso de la escoria granulada.
La escoria de alto horno es un subproducto (no metálico) de la manufactura del hierro fundido en alto horno, consistiendo esencialmente de silicatos y aluminosilicatos de calcio y otras fases (Siddique, 2008). Ciertos autores (Malhotra, 1996; Lea, 1971) describen a la escoria de alto horno como un material puzolánico, ya que no presenta propiedades cementosas por sí misma a menos que esté combinada con otros materiales cementantes para su activación química. Pero otros autores señalan que debería ser clasificada como un cemento hidráulico latente, ya que sus componentes son similares a los óxidos del cemento portland (cal, sílice y alúmina) en diferentes proporciones (Lea, 1971).
La escoria generada en la industria siderúrgica es de cuatro tipos según el método empleado para su enfriamiento: la escoria de alto horno enfriada al aire; la escoria expandida o espumada; la escoria paletizada y la escoria de alto horno granulada.
La escoria enfriada al aire no presenta las mismas propiedades hidráulicas que la escoria enfriada por agua, ya que al enfriarse lentamente en el aire, sus compuestos tienen la posibilidad de alcanzar mayor grado de cristalización, lo que generaría un material de poca actividad reactiva. La escoria expandida por su parte es empleada como agregado grueso de peso ligero en la fabricación de concreto con bajo peso específico (Malhotra, 1996). Estos materiales son empleados en la construcción de carreteras y en edificaciones. El tipo de escoria empleada como cementante es el material granulado de alto horno, este subproducto se obtiene por el enfriamiento acelerado de la escoria fundida, a través de la aplicación de agua sobre su superficie con la intención de formar un material vítreo el cual tendrá cierto grado de activación.
El enfriamiento rápido con agua de la escoria fundida previene la formación de cristales más grandes, dando como resultando un material granular que comprende casi 95% del compuesto de alumino-silicato de calcio no cristalino. La escoria granulada es procesada por medio de un secado previo y posteriormente sometida a molienda con molino rotatorio de bolas, hasta obtener un polvo muy fino, el cual es conocido como cemento de escoria de alto horno de grano molido (GGBS por sus siglas en inglés). La escoria granular posee tamaños de partícula entre 4 a 15 mm, y después de la molienda menor de 45 μm y área superficial de 400 a 600 m2/kg, la cual puede ser empleada como un cemento hidráulico latente (Lea, 1971). El material molido es un polvo de color más claro que el cemento portland, la coloración que brinda al concreto es más clara y le da un acabado de superficie suave comparado con el concreto con cemento portland. La gravedad específica que presenta es de 3.15.
En la figura 1 se muestra una imagen de MEB (SEM) extraída de la literatura, con la morfología de una pasta hidratada, compuesta por un sistema cementante con 30% de escoria de alto horno y 70% de cemento portland ordinario (Li, 2011). En la figura 1 se observan partículas angulares que corresponden a la escoria y que no han alcanzado a hidratarse después de 7 días. Este comportamiento es normal en los cementos con escoria, ya que la escoria presenta una menor actividad de reacción comparada con el cemento portland ordinario.

Figura 1. Microfotografías de MEB de pastas hidratadas después de 7 días, pasta con 30% de escoria de alto horno y 70% de cemento portland ordinario (BFS escoria de alto horno, C-S-H silicato de calcio hidratado) (Li, 2011).
Las especificaciones para la escoria granulada de alto horno como material cementante se encuentran en la ASTM C 989 (ASTM-C-989, 1999), donde se clasifica la escoria en tres grados de resistencia. Los grados están basados en un índice de actividad de la escoria: grado 80 (con bajo índice de actividad); grado 100 (con índice moderado de actividad) y grado 120 (con alto índice de actividad); también se encuentran otras especificaciones para la escoria en la AASHTO M 302 (ASSTHO-M302, 2000). El número en las designaciones de calidad corresponde a la resistencia a compresión a los 28 días, aproximadamente, realizados en cubos estándares de mortero preparadas con EGAH (mezcla con una cantidad igual en masa de cemento portland). El grado de actividad influye en el comportamiento reactivo en la mezcla fresca de concreto y del fraguado posterior. Por otro lado, la actividad hidráulica de la escoria estará determinada por su composición química, el área superficial y el tamaño de partícula de la escoria molida (Puertas, 1993; Pal, 2003).
La composición química de la escoria de alto horno puede ser muy variada según su origen, pero para ser considerada como un material cementante se requiere que la composición química se encuentre entro los rangos: CaO (30-45%), SiO2 (30-48%), Al2O3 (15-25%), Fe2O3 (0.5-2%), y otros óxidos de menor cantidad (Shetty, 2013). Entre los requerimientos químicos dados por la ASTM 989 (ASTM-C-989), se establece 2.5% y 4.0% como las cantidades máximas de sulfuros (S) y de sulfatos respectivamente, bajo estas cantidades la presencia de escoria en el concreto armado no representa un riesgo de corrosión para el acero de refuerzo (Wang, 2010). La escoria de alto horno pulverizada es ligeramente alcalina y exhibe un pH en solución en un rango de 8 a 10, sin embargo el lixiviado de escoria puede exceder un valor de 11, un nivel que puede ser corrosivo para aluminio o tuberías de acero galvanizado colocadas en contacto directo con la escoria (Wang, 2010).
Las proporciones de los compuestos de óxidos mencionados anteriormente, determinará la basicidad de la escoria y su capacidad hidráulica. Pero para que la escoria pueda desarrollar realmente su potencial hidráulico se necesita que su fase vítrea sea mayoritariamente superior a 70%. Esta característica vítrea condicionará la capacidad de la escoria para recrear la estructura cristalina que le proporcionará al concreto sus cualidades de resistencia y durabilidad.
Como material cementante, la escoria granulada tiene las siguientes características: es un cemento hidráulico latente fuerte cuando es molido, posee bajo contenido de Na2O y K2O, peso ligero, alta permeabilidad al agua, no contiene cloruros y no produce reacciones álcali-agregado.
El reemplazo del cemento por escoria granulada molida (EGAH) generalmente reducirá la cantidad de agua necesaria para obtener un mismo revenimiento como el obtenido en un concreto con CPO. La reducción de la cantidad de agua estará influenciada con el incremento del nivel de reemplazo y la finura de la escoria (Shetty, 2013). La demanda de agua típica de la mezcla de concreto con EGAH es del orden de 3-5% menor que el concreto con cemento Portland (Wang, 2004; Walker, 2011). Esto representa una reducción de 5 a 10 litros de agua por metro cúbico de concreto. Para reemplazos del CPO por EGAH en el orden de 70% y 80%, la reducción en la demanda de agua puede ser menor, debido a la concentración mucho más alta de las partículas más finas EGAH (Siddique, 2012; Oner, 2007). Este comportamiento es debido a que las superficies de las partículas de EGAH son más suaves y de mayor cristalinidad que las de cemento portland, resultando en menor adsorción de agua sobre la superficie de las partículas de EGAH.
Entre las ventajas que puede ofrecer el empleo de escoria granulada molida en el concreto fresco y endurecido se tienen: reducción del calor de hidratación, refinamiento de la estructura de poro, reducción de la permeabilidad de agentes externos, incremento de la resistencia al ataque químico, resistencia al ataque por sulfatos, mejoramiento de la trabajabilidad de la mezcla, y en ciertos casos puede mejorar la resistencia a la corrosión del acero de refuerzo, recordando aquí que esto dependerá de la composición química de la escoria. El concreto con escoria puede alcanzar mayor resistencia de compresión para determinados niveles de reemplazo del cemento portland. Además que se tiene un ahorro de cemento portland común en la mezcla de concreto (Shetty, 2013).
La incorporación de la escoria de alto horno en la mezcla cementante, modifica la naturaleza y características de los hidratados formados, afectando a la red capilar del concreto, reduciendo el tamaño y el número de poros. Este efecto de la escoria se refleja en el concreto en estado endurecido y su durabilidad. Sin embargo, los efectos benéficos de la escoria en las propiedades mecánicas y durabilidad del concreto estarán en función de diferentes factores, entre los cuales se pueden destacar aquí la calidad de la escoria, el diseño adecuado de la mezcla, la colocación y transporte del concreto fresco y el cuidado en el tiempo y tipo de curado.
Otra característica considerable de las escorias es el proceso de hidratación, que es más lento que el del Clinker debido a que su disolución es más difícil por su carácter vítreo y también por la necesidad de una fuente de activación sulfática (yeso, anhidrita) o alcalina (por presencia de álcalis o portlandita). La activación de la escoria se genera por la presencia de portlandita Ca(OH)2 liberada de la hidratación del Clinker, por los álcalis contenidos en la escoria y por la acción del regulador de fraguado (yeso y/o anhidrita).
Ante esto, se pueden mencionar otras características de los cementos de escoria granulada de alto horno, relacionadas con su proceso de hidratación.
No hay liberación de portlandita Ca(OH)2 y se puede pensar en un consumo de la cantidad liberada por el clinker.
No hay formación de aluminato tricálcico (C3A).
Los álcalis (K2O y Na2O), que participa como catalizadores en la hidratación de las escorias, quedan atrapados en la red cristaliza y no en estado libre.
Por otro lado, como un beneficio medioambiental, la escoria granulada molida es también considerada un material sustentable (Gjørv, 2000), al ser un subproducto de desecho industrial y su uso en el concreto es reconocido por la certificación LEED (Leadership in Energy and Environmental Design) (Council U.S.G.B. 2014; Slag Cement Association). Ante esto, la escoria puede ser utilizada en concreto para superestructuras, y con una debida evaluación, también es empleada en concreto armado expuesto en ambientes con cloruros y sulfatos, con la desventaja de su característica lenta de fraguado, lo que implicaría un mayor tiempo de ejecución de determinado proyecto.
Debido a que la escoria adicionada en la mezcla de concreto tiene menos reactividad en los primeros días, se presenta una considerable disminución en la resistencia a compresión a edades tempranas comparadas con mezclas de concreto con CP. Sin embargo, a edades posteriores se ha detectado lo contrario, es decir, alcanzando en varios casos resistencias mayores que las de un concreto homólogo (Oner, 2007; Berndt, 2009).
3. ESCORIA DE ALTO HORNO COMO MATERIAL CEMENTANTE EN LA NORMATIVA
La EAH puede ser empleada para la misma finalidad que el cemento portland, ya que fragua y endurece por la reacción química con el agua, por lo que es considerada como un cemento hidráulico latente por tener los mismos compuestos que aquel. Sin embargo, en algunos casos se requiere que la escoria sea mezclada también con cal hidratada para ganar funcionalidad (Gambhir, 2009; Lea, 1971).
Las especificaciones para el cemento de escoria se encuentran en las normas ASTM C595 (ASTM-C595, 200) donde se clasifican en tipo IS y S (Cemento portland de escoria de alto horno y Cemento de escoria o siderúrgico) respectivamente.
El cemento tipo IS está constituido básicamente por escoria granulada de alto horno (EGAH), el cual se puede moler conjuntamente con el Clinker del cemento portland o bien con molienda separada para incorporarlo posteriormente a la mezcla cementante. La cantidad de EAH en este tipo de cemento se encuentra entre 25% y 70% de la masa cementante. Se considera que el contenido de escoria de 70% de la masa cementante trae cierto beneficio en la resistencia y la durabilidad pero hasta cierto grado y de acuerdo al ambiente donde se exponga el concreto. Por otro lado, si se pretende emplear dosis más elevadas que la anterior, se deben hacer ensayos del concreto para la verificación de la resistencia, durabilidad y otras especificaciones requeridas para el proyecto.
En la tabla 1 se muestran las cantidades de contenido de escoria en el cemento consideradas en las normas de diferentes países. De acuerdo a las normas presentadas en la tabla 1, la norma europea (UNE-EN-197, 2013) considera un nivel de escoria en la mezcla cementante del 95%, siendo el mayor nivel comparado con las de otros países mostrados en la tabla 1. Mientras que para los países americanos, Colombia es quien tiene considerado en su norma hasta 85% de escoria y México con 80%. Por otro lado, es imprescindible mencionar que el uso de altos niveles de escoria debería quedar sujeto a determinado control de verificación del concreto, debido a la compatibilidad con otras adiciones en la mezcla, o bien por los agregados y las condiciones ambientales.
El empleo de otros materiales cementantes, distintos a los tradicionales, implicarán ciertos efectos y cambios en el concreto fresco y endurecido. Para la mezcla de concreto se necesita determinada cantidad de agua para que se lleve a cabo la reacción de hidratación. La escoria tiene entre sus peculiaridades la capacidad de disminuir la cantidad de agua de mezclado de 1% a 10%, dependiendo de la cantidad de sustitución. Así también, puede tener mayor cantidad de sangrado sin que éste tenga efectos adversos en el concreto, pero también tiende a disminuir el calor de hidratación en comparación con el cemento portland. Sin embargo, el empleo combinado de escoria de alto horno molida y ceniza volante puede disminuir el tiempo de fraguado (Lee, 2013).
Para el concreto endurecido el empleo de escoria puede contribuir al mejoramiento de la resistencia a compresión. Pero también se corre el riesgo de que la resistencia del concreto tienda a sufrir una disminución con la adición cuando no se aplica un adecuado método de curado y el cuidado respectivo para el sistema cementante empleado. Así se tiene que el desarrollo de la resistencia en concreto con EGAH puede ser similar al concreto normal si es curado a temperatura de 23 ºC aproximadamente.
4. RESULTADOS DEL EFECTO DE LA EAH EN LA RESISTENCIA A COMPRESIÓN
Para esta sección se realizó una recopilación de datos de investigaciones reportadas en la literatura, poniendo atención en los niveles de reemplazo del cemento portland por escoria de alto horno y el efecto causado en la resistencia a compresión real (f c ) del concreto endurecido a las edades de 28 y 90 días. Cabe mencionar que las mezclas de material cementante que se han investigado están compuestas por el sistema: cemento portland y escoria.
Regularmente la cantidad de agua empleada para preparar la mezcla de concreto está especificada de manera implícita en la relación agua/cemento (a/c), Pero para sistemas cementantes la cantidad de agua está especificada por la relación agua/material cementante expresado por a/mc. Sin embargo existen casos particulares donde no se usa únicamente agua para la preparación de la mezcla sino que se requiere de alguna solución activadora de algún subproducto, entonces el término empleado es s/mc que representa la solución acuosa con el agente químico (solución alcalina) y material cementante.
Las técnicas de curado del concreto después de 24 h de colado pueden ser muy variadas, entre éstas están: el curado húmedo o curado en inmersión de agua; curado a temperatura ambiente; curado con temperatura (T) y humedad relativa (HR) controlada. El periodo de curado dependerá del sistema cementante utilizado para la mezcla del concreto con dosis de escoria como reemplazo del cemento.
En la tabla 2, se muestran algunos resultados reportados en la literatura sobre resistencia a compresión real f c del concreto a edades de 28 y 90 días, conteniendo reemplazos del cemento portland ordinario tipo I por el subproducto de EAH. En la tabla se mencionan el nivel de reemplazo, la relación a/mc y la resistencia a compresión a 28 y 90 días.
Tabla 2. Resistencias a compresión (f c) del concreto con sistema cementantes CPO tipo I + EAH con diferentes niveles de reemplazo según diversos autores.

Como se puede observar en la tabla 2, la cantidad de reemplazo del cemento por escoria tiene un máximo del 80% para la investigación reportada en el 2007 (Atis, 2007), estando esta cantidad dentro del rango que se reportan en las normas estándar de los diferentes países como México y Colombia. Así también se puede mencionar que se han investigado concretos con diferentes relaciones de a/mc, comprendiendo dicho rango entre 0.28 a 0.55, mencionando además que en bajas relaciones de a/mc se hace indispensable la utilización de algún aditivo reductor de agua o superplastificante para conferirle las propiedades adecuadas en el estado fresco del concreto.
De acuerdo a la tabla 2, existe una amplia gama de posibilidades para emplear la EAH como sustitución parcial del cemento para fabricar mezclas de concreto, pero en algunos casos el resultado no tiene un buen efecto en lo que concierne a la resistencia mecánica. Por esto es importante proporcionar ciertos detalles en cuanto a la resistencia a compresión del concreto en función de la cantidad de escoria empleada en el sistema cementante CPO + EAH.
En las figuras 2 y 3 se muestran en forma gráfica los datos mostrados en la tabla 2, correspondientes a la resistencia a compresión real del concreto a edades de 28 días (figura 2) y 90 días (figura 3) en función de la cantidad del nivel de reemplazo del cemento. También en las figuras 2 y 3 se muestran las lineas de correlación promedio con la clasificación en tres rangos de la relación a/mc; los valores menores a 0.4, el rango entre 0.4 y 0.6, y los valores mayores a 0.6.
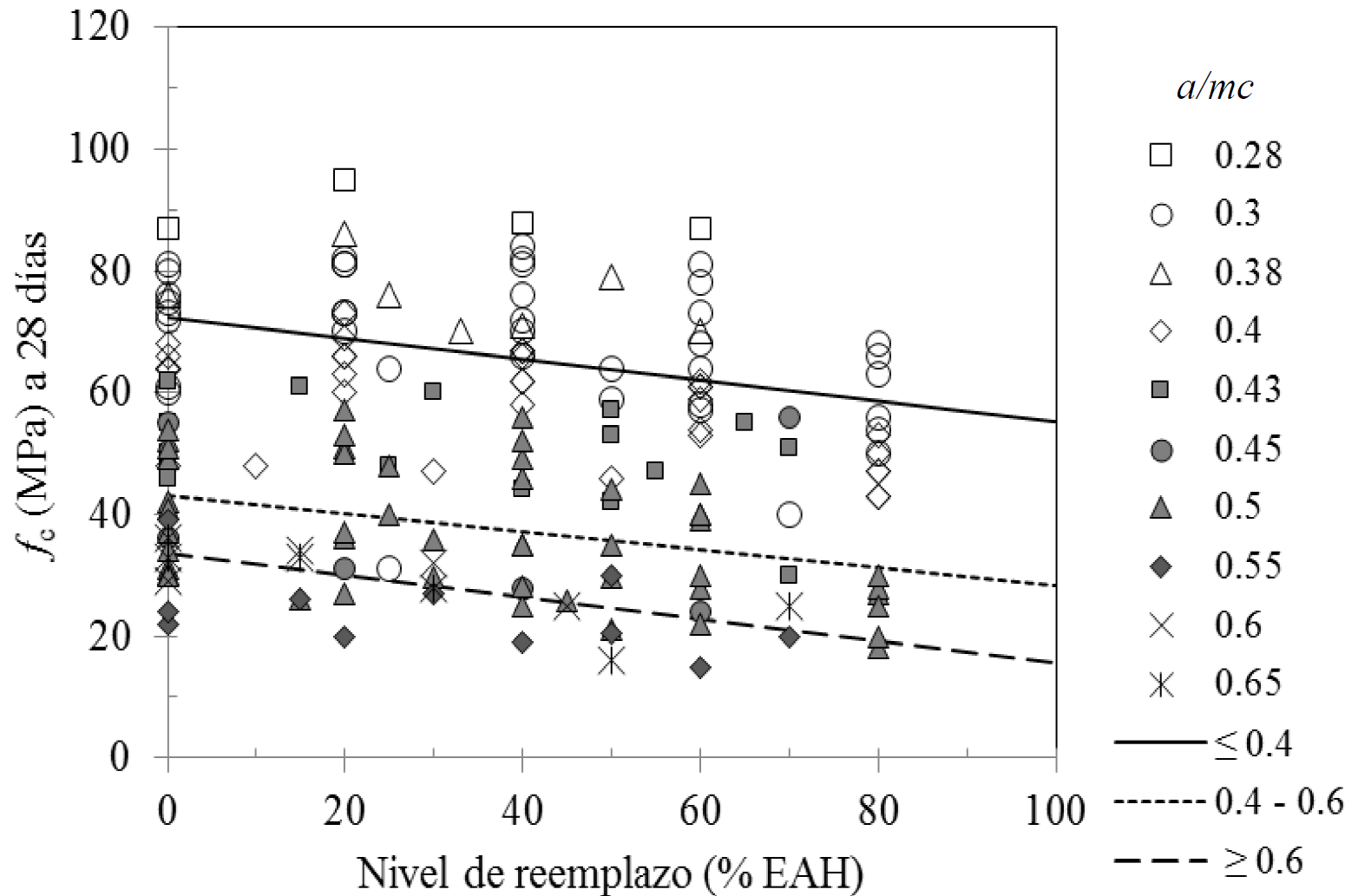
Figura 2. Datos reportados en la literatura (tabla 2) de resistencia a compresión real (f c) de los concretos con escoria y ensayados a 28 días.

Figura 3 Datos reportados en la literatura (tabla 2) de resistencia a compresión real (f c) de los concretos con escoria y ensayados a 90 días.
Se puede observar en la figura 2, que hay una ligera tendencia generalizada a la disminución de la resistencia cuando se incrementa la cantidad de escoria en la mezcla cementante, aunque se puede observar que hay un rango donde puede mejorarse la resistencia. El nivel de reemplazo que se ha empleado en las investigaciones alcanza un valor del 80%, pero se puede observar que en el rango de 20% a 60% es donde se observan valores ligeramente mayores de f c comparados con el concreto de referencia, es decir sin escoria. Un comportamiento similar al de la resistencia a los 28 días se puede observar también en la resistencia a los 90 días mostrado en la figura 3. En dicha gráfica se puede apreciar además que para un período más largo de tiempo (mayor edad del concreto), la resistencia f c de los concretos con reemplazos en el rango de 20% a 60% tiende a incrementar con la edad.
Para ambas edades de los concretos (figuras 2 y 3), se observa que con los niveles de reemplazo del cemento mayor a 60% de escoria, la resistencia del concreto es inferior que el concreto sin reemplazo.
Para determinar el efecto generado en la resistencia f c de los concretos para las edades de 28 y 90 días, se determinó un parámetro que llamamos tasa de cambio, este parámetro es un valor unidimensional obtenido de la fracción entre la resistencia f c del concreto con escoria y la f c del concreto de referencia. En las gráficas de la figura 3, se muestra la tasa de cambio (eficiencia) de la resistencia f c del concreto con escoria con respecto al concreto homólogo de referencia y en función de los diferentes niveles de reemplazo. La línea horizontal marca la tasa de f c para el concreto de referencia. Un valor inferior a dicha línea indica que el concreto con escoria no alcanzó el valor de la resistencia de su homólogo sin escoria, mientras que valores por encima de la línea horizontal significan que el concreto superó o mejoró la resistencia del concreto sin escoria.
De manera similar a lo observado en las figuras 2 y 3, se puede observar en la figura 4 que existe una tendencia conocida y esperada a la disminución de la resistencia del concreto f c con el incremento del nivel de reemplazo de cemento por escoria en el sistema cementante siendo congruente con lo reportado en la literatura (Abdelkader, 2010).

Figura 4. Tasa de cambio (eficiencia) de la resistencia a compresión real f c de los concretos con escoria, a 28 días.
De nueva cuenta, el rango donde se aprecia un mejor efecto en la resistencia está entre los niveles de 20% y 60% donde se alcanzan valores similares o ligeramente superiores de f c con respecto al concreto de referencia, este efecto se ve más marcado en la gráfica de la figura 5 para concreto de 90 días de edad. Además, se observa en la gráfica de la figura 4, que reemplazos mayores a 60% tienen disminución en el mejoramiento de la resistencia f c . De la misma manera, este efecto también se puede apreciar a la edad de 90 días, resultando congruente con lo observado en las figuras 2 y 3.
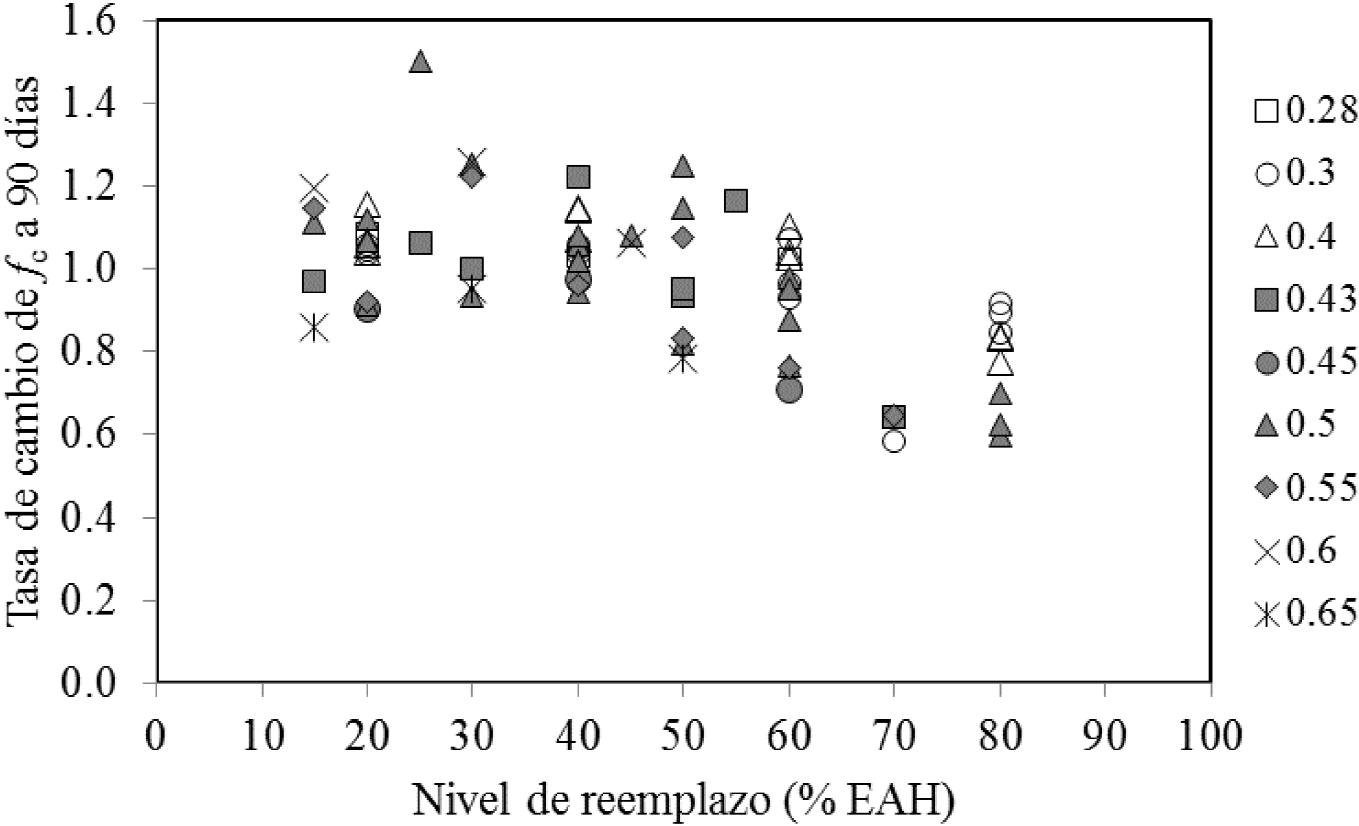
Figura 5. Tasa de cambio (eficiencia) de la resistencia a compresión real f c de los concretos con escoria, a 90 días.
De acuerdo a los resultados reportados por Ahmend Hadjasadok et al. (Hadjasadok, 2012), se observa que para la misma relación de a/mc se reduce la resistencia f c cuando se incrementa el nivel de reemplazo del CPO, pero para una misma cantidad de escoria la resistencia f c se incrementa al reducir la relación a/mc.
Por otra parte, en la figura 5 se puede observar que a edades de 90 días el concreto adquiere una mayor resistencia comparada con la edad de 28 días (figura 4). Esta observación también fue realizada en los trabajos realizados por Ilker Bekir Topcu y Raif Boga (Topç, 2010) donde además concluyen que con reemplazos de 25% de EGAH al sistema cementante, resulta en una mayor resistencia compresión del concreto con curado bajo agua y durante 28 días, asi como a 90 días. Debe mencionarse también que el concreto con 90 días de edad alcanzó 10.5% más de resistencia que a los 28 días. Sin embargo, para un reemplazo de 50% la resistencia disminuye en tiempos similares de curado, dicho efecto con el nivel de reemplazo similar fue observado por Bougara (Abdelkader, 2010). Por su parte Chidiac y Panesar (Chidiac, 2008), concluyen que la resistencia f c del concreto con escoria es disminuida con el incremento del nivel de reemplazo de cemento.
El comportamiento que se observa en la tardanza del mejoramiento de la resistencia mecánica en los concretos con escoria se infiere que es debido a que el subproducto cementante siderúrgico tiene un proceso de activación más tardado que el del cemento convencional.
Estas características también han sido mencionadas en otras investigaciones realizadas en pastas (Sanchez, 2011), otras en mortero (Hwang, 1991) y también en concreto (Lee, 2013), teniendo un resultado similar en la disminución de la resistencia a edades tempranas por una consecuencia del retraso del tiempo de hidratación del material cementante suplementario. Este comportamiento genera una disminución de la tasa de precipitación de los productos de reacción más estables, los cuales contribuyen en la resistencia mecánica.
Debido que la resistencia estará relacionada con las fases formadas en las pastas, se menciona uno de los resultados de las investigaciones realizadas por Chao-Lung Hwang y Der-Hsien Shen (Hwang, 1991) en pastas con sistemas de CPO - EAH con reemplazos de 10% a 40% y tres relaciones agua-material cementante 0.35, 0.47 y 0.59, concluyendo que para una determinada relación a/mc, un contenido alto de EAH requerirá mayor tiempo de fraguado de la pasta.
Sin embargo, según la investigación realizada por Martínez Aguilar et al, (Aguilar, 2010) reportan que la f c en pastas con EAH podría ser mejorada con la activación de la escoria mediante un tipo de sulfato alcalino (Na2SO4 o K2SO4 mezclado con Al2SO4), o bien por medio de alguna fuente sulfática como el fluoryeso (Fy, CaSO4) que también es otro subproducto industrial, aunque también mencionan que la f c a los 90 días en algunos casos fue menor que a los 28 días. Los autores relacionan dicho efecto, con la formación de fases poco estables (etringita y yeso) en la estructura interna de la pasta cementante y que por lo tanto resulta en una inestabilidad (expansión) a edades posteriores.
De acuerdo a lo anterior se puede decir que para un contenido constante de escoria, el tiempo de fraguado cambiará proporcionalmente con la relación a/mc. Esto conllevará a obtener un mejor resultado de la resistencia a compresión a edades posteriores que para un concreto convencional, por lo que se tendría una mayor tasa de hidratación de los compuestos químicos del material cementante.
Para lograr apreciar el efecto causado por la escoria en el concreto endurecido al transcurrir el tiempo, se determinó la frecuencia del cambio en la resistencia del concreto de acuerdo con tres rangos de la tasa de cambio: aquellos concretos con EAH que presentaban un cambio < 1 con respecto al concreto de referencia; los que no presentaban ningun cambio o tasa de cambio, que fueron considerados igual a 1; y aquellos que presentaban cambios > 1, realizando ésto para ambas edades de los concretos. Lo anterior se muestra en la figura 6 a través de una gráfica de frecuencias de una muestra representativa de los datos de resistencia de los concretos con escoria analizados en este trabajo y que logran tasas de cambio de f c menores, iguales y mayores a 1. En dicha figura 6 se observa claramente que para la tasa de cambio <1 hay una disminución en la frecuencia de la tasa de cambio para los concretos con EAH al pasar de 28 a 90 días de edad, mientras que para la tasa de cambio >1 hay un incremento de la frecuencia. Esto quiere decir que la incidencia en la tasa de cambio con valores <1 para el concreto con EAH a los 28 días, es mayor que para el concreto de referencia. Mientras que los valores de tasa de cambio >1, que representan los concretos con EAH y superan la resistencia del concreto de referencia, tienen mayor incidencia en la tasa de cambio aquellos concretos con 90 días de edad. Esto tiene relación con lo dicho anteriormente, ya que la escoria tiene un proceso de hidratación más lento que el CPO, por lo que requiere de un mayor tiempo para alcanzar una óptima hidratación y de esta forma desarrollar compuestos y fases químicamente más estables que interfieren en una mejoría de la resistencia a compresión del concreto. Ante ésto, se cree que éstas características de hidratación son un factor condicionante para el desarrollo de la resistencia y la que interfiera en la disminución de la resistencia, además del tipo de actividad de la escoria y de la implementación del curado del concreto.
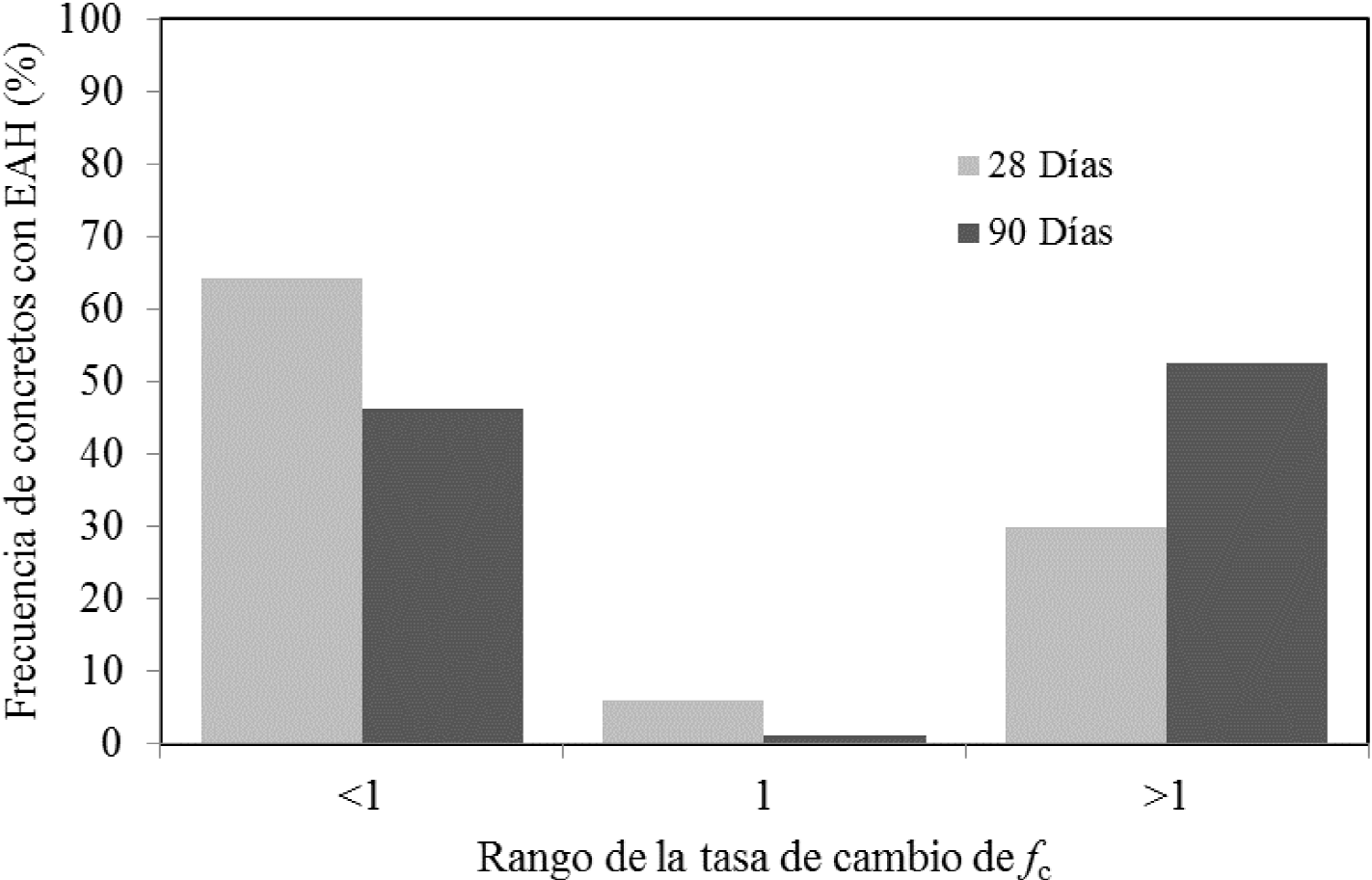
Figura 6. Frecuencias de la número de muestras de concreto con EAH relacionadas con la tasa de cambio (eficiencia) de f c con respecto al concreto de referencia.
Como se ha mencionado en párrafos anteriores, para el sistema cementante CPO + Escoria aplicados al concreto endurecido, éste puede producir un efecto en la resistencia que supera la del diseño a la edad de 28 días de curado de acuerdo a lo reportado en la literatura (Topç, 2010; Yeau, 2005). Previo a dicha edad, los concretos con EGAH presentaron f c más bajas comparadas con las del concreto de referencia, pero que puede ser superado a edades posteriores, siendo este mismo comportamiento para todos los niveles de reemplazo. Este resultado se debe a las reacciones químicas secundarias y de la reacción hidráulica lenta de la escoria que contribuyen a densificar la microestructura del concreto. Los resultados presentados por Chidiac y Panesar (Chidiac, 2008) confirman lo anterior, y además que la tasa de hidratación inicial es más lenta en concreto con EGAH que con CPO. Por lo que en el transcurso del tiempo, de 7 a 28 días, el concreto con EGAH (60%) comienza a ganar resistencia, logrando ser superior o similar que el concreto con CPO.
Ante estos resultados, se puede decir ahora que las posibilidades de utilizar un subproducto van a estar determinadas por los requerimientos de calidad del concreto, entendiéndose como las propiedades de resistencias mecánicas y de durabilidad. Cabe señalar aquí que la resistencia a compresión no es un parámetro absoluto para la elección de un determinado concreto en determinada construcción. Entonces, de lo anterior se puede prever que con el incremento en la dosificación de la EAH en el sistema cementante se pueden lograr obtener resistencias a compresión similares a un concreto con CP convencional pero con la noción de que será a edades posteriores como un concreto normal.
Se ha visto anteriormente que la incorporación y el incremento del nivel de escoria en la mezcla de concreto puede tener un carácter benéfico en la propiedades mecánicas del concreto endurecido, pero condicionado a cierto grado de reemplazo y a un determinada edad. Como contrapartida se puede decir que el concreto elaborado con un porcentaje elevado de escoria es muy sensible a las condiciones de curado, generando un secado prematuro en la superficie del concreto lo que conduciría a un aumento de la permeabilidad, además que la hidratación del material cementante se reduce con lo cual generará una disminución de las propiedades mecánicas de resistencia del concreto endurecido.
De manera similar como para un concreto convencional, el curado durante las primeras horas posteriores al endurecimiento de los concreto con un sistema cementante de CPO+EAH, es sumamente esencial, ya que con esta práctica se influye para el desarrollo de la resistencia a compresión, disminución de la porosidad y alta resistencia a la penetración de cloruros. Bajo esta primicia Ramezanianpour y Malhotra (Ramezanianpour, 1995), proporcionan los resultados de sus investigaciones en concreto con los niveles de reemplazo mostrados en la tabla 2 y con curado estándar de humedad continua, corroborando que los concretos que no recibieron un curado, mostraron pobre rendimiento del desarrollo de la resistencia mecánica, así como mayor porosidad y una débil resistencia a la penetración de iones cloruro. Cabe señalar que aún cuando los concretos fueron curados durante 2 días, se vio una mejoría significativa en su resistencia comparadas con el concreto sin ningún tratamiento de curado. Por lo tanto, se reafirma la importancia del curado del concreto con el sistema cementante CPO + EAH, ya que como se ha dicho la reacción de hidratación de la escoria es más lenta que la del cemento.
Un parámetro importante en la predicción de la resistencia del concreto con escoria a través del modelo de Feret (Feret, 1982) es el coeficiente de eficiencia de la escoria. En el tiempo de hidratación de la mezcla cementante, la escoria tiende a mejorar su coeficiente hasta alcanzar un valor optimo comparado con el cemento portland, pero posteriormente también se ha visto que puede disminuir (Abdelkader, 2010) Por ello la eficiencia va a depender del nivel de reemplazo, ya que se ha observado que con 15% de escoria, la activación es completa y se tiene 67% más de eficiencia que con un cemento común. Mientras que para altos niveles de reemplazo (50%) la eficiencia de la escoria disminuye o bien en el mejor de los casos alcanza a ser similar al cemento (Abdelkader, 2010).
En estudios realizados en elementos estructurales con mezclas cementantes de 30%, 50% y 70% de escoria, se han logrado buenos resultados de las resistencias a compresión real f c y expuestos en un ambiente de agresividad leve y cuyos resultados se muestran en la tabla 2, en la investigación de Osborne (Osborne, 1999). Por otro lado, el autor señala que la velocidad de carbonatación y la permeabilidad de especies gaseosas son similares como el concreto con un cemento común, sin embargo considera altamente susceptible el concreto con alto nivel de escoria y expuesto al aire libre, siendo sumamente agresivo en lugares con un ambiente seco. Sin embargo, puntualiza que dar atención en el recubrimiento para el acero de refuerzo, y acotando las cantidades de escoria para situaciones medioambientales de riesgo excesivo de carbonatación puede disminuir tal efecto, siendo así que el nivel de reemplazo de escoria debe quedar limitado hasta un 50%. Para ambientes considerablemente húmedos y en presencia de cloruros puede emplearse hasta un nivel del 70% (Osborne, 1999).
Ante lo dicho anteriormente se puede decir que el debido curado de los concretos con escoria de alto horno debe ser considerado un factor imprescindible para la hidratación y de esa manera poder garantizar un buen desempeño en la resistencias mecánicas y de durabilidad.
Por lo consiguiente, se puede decir que el uso y el nivel de reemplazo de la escoria de alto horno en los sistemas cementantes para concreto, quedará definido de acuerdo a las características de diseño de la mezcla de concreto, tanto fresco como endurecido, y del medio en donde serán expuestos los elementos estructurales.
5. CONCLUSIONES
Después de re-visitar el estado del arte sobre la fc en concretos con escoria de alto horno se pudo confirmar, a través de la experiencia de diversos autores que evaluaron diversas condiciones y tipos de escoria, que el nivel de reemplazo puede ser significativamente alto, pero al rebasar el 50% será necesario un esquema estricto de control de calidad en la preparación y la combinación de otros aditivos que coadyuven al mejoramiento de la resistencia mecánica, ya que de lo contrario se provocarán efectos adversos a los deseados.
El nivel de reemplazo máximo recomendado por varios autores y de acuerdo a los resultados obtenidos por otros es de 70 % para escoria en ambientes de poca agresividad de carbonatación, de lo contrario se debe limitar hasta 50%.
El concreto donde se sustituya parcialmente el cemento por EAH requerirá de un mayor tiempo de hidratación para garantizar la fc deseada, siendo de crucial importancia el curado del concreto.